What are WMS Modules | Understanding Benefits for Efficient Warehouse Operations
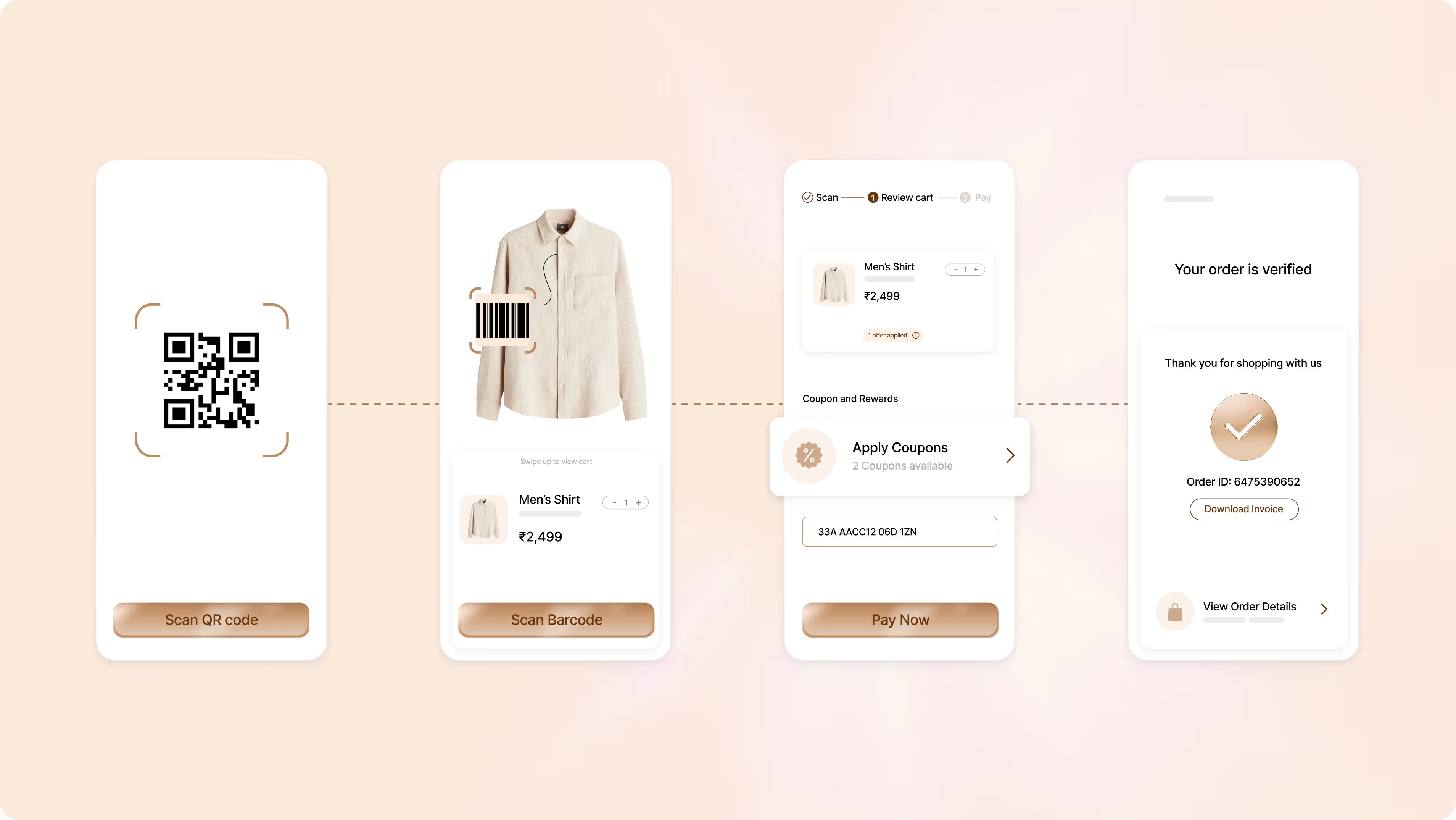
Warehouse Management System (WMS) modules are specialized components that streamline warehouse operations by improving efficiency, visibility, and resource utilization. Each module targets specific tasks, such as inventory management, order processing, labor management, and shipping coordination, which are critical for modern warehouses to manage high-demand supply chains. With the global WMS market projected to grow from $2.94 billion in 2020 to $5.72 billion by 2026, more businesses are investing in these modular systems to enhance productivity and cut costs.
For instance, inventory management modules enable precise tracking, reducing errors by up to 30% and maintaining optimal stock levels. The labor management module enhances productivity through real-time tracking of employee tasks, which can increase workforce efficiency by up to 40%. In addition, features like the picking and packing module improve order accuracy and speed, supporting faster delivery, a key demand in the e-commerce sector. These benefits help businesses operate efficiently and improve customer satisfaction.
Fynd’s WMS platform provides businesses with robust WMS modules tailored to their operational needs, making it a reliable choice for companies looking to improve warehousing. This page helps users understand how WMS modules can solve challenges like inventory mismanagement and fulfillment delays, ensuring efficient warehouse operations.
What is a WMS Modules?
WMS modules are individual components within a Warehouse Management System (WMS) that manage specific functions of warehouse operations, such as inventory tracking, order fulfillment, and labor management. Each module focuses on a key part of the workflow to streamline processes and improve accuracy, from receiving goods to organizing storage and coordinating shipments.
By breaking down tasks into specialized modules, a WMS provides flexibility, allowing businesses to choose and scale functions based on their needs. These modules enhance efficiency by automating manual tasks and providing real-time data, helping businesses reduce errors, lower costs, and optimize warehouse space. Together, WMS modules make operations more efficient and responsive to customer demand.
{{demo_wms="/styles/components"}}
1. Inventory Management Module
The Inventory Management Module is a critical component of a Warehouse Management System (WMS) that focuses on tracking and managing stock levels within a warehouse. This module provides real-time visibility into inventory, allowing businesses to know exactly what they have on hand at any given time.
By automating inventory processes, this module helps reduce errors, minimize stockouts, and improve overall efficiency. Effective inventory management ensures that warehouses can respond quickly to customer demands and maintain optimal stock levels, ultimately enhancing operational performance.
Key Features of the Inventory Management Module
The Inventory Management Module enhances efficiency by providing real-time tracking of stock levels, automating reorder processes, and optimizing warehouse organization. It ensures data accuracy with cycle counting and supports better decision-making through detailed reporting and analytics. These features enable businesses to reduce costs, prevent stockouts, and improve service levels.
- Real-Time Tracking: Monitors inventory levels in real time, providing accurate data on stock availability.
- Automated Reordering: Automatically triggers reorders when the stock reaches a predefined level, preventing stockouts and overstocking.
- Location Management: Organizes inventory by location within the warehouse, improving picking efficiency and space utilization.
- Cycle Counting: Facilitates regular inventory counts to verify stock accuracy and maintain data integrity.
- Reporting and Analytics: Generate reports on inventory turnover, stock levels, and trends, helping businesses make informed decisions.
These features help businesses streamline their inventory processes, reducing costs and improving service levels.
2. Order Management Module
The Order Management Module is an essential part of a Warehouse Management System (WMS) that focuses on managing customer orders throughout their lifecycle. This module helps streamline the entire order fulfillment process, from order placement to delivery.
By automating various tasks, such as order processing and tracking, businesses can enhance order accuracy, reduce lead times, and improve customer satisfaction. An efficient order management system allows warehouses to handle high volumes of orders while maintaining transparency and control over the fulfillment process.
Key Features of the Order Management Module
The Order Management Module streamlines order fulfillment by automating processing, providing real-time tracking, and enabling prioritization based on urgency. Integration with inventory ensures stock availability, while robust reporting and analytics deliver valuable insights into order performance. These features help businesses enhance efficiency, meet delivery deadlines, and improve customer satisfaction.
3. Receiving and Putaway Module
The Receiving and Putaway Module is a vital component of a Warehouse Management System (WMS) that oversees the intake and storage of incoming goods. This module streamlines the receiving process by automating essential tasks such as checking product quantities, verifying shipments against purchase orders, and assigning optimal storage locations.
Optimizing putaway processes ensures that items are stored efficiently and remain easily accessible for future orders. Effective receiving and putaway practices significantly reduce errors, improve inventory accuracy, and enhance overall warehouse productivity, ultimately leading to better fulfillment rates and customer satisfaction. By leveraging this module, warehouses can maintain seamless operations and adapt to fluctuating demand.
Key Features of the Receiving and Putaway Module
The Order Management Module streamlines order fulfillment by automating processing, providing real-time tracking, and enabling prioritization based on urgency. Integration with inventory ensures stock availability, while robust reporting and analytics deliver valuable insights into order performance. These features help businesses enhance efficiency, meet delivery deadlines, and improve customer satisfaction.
4. Picking and Packing Module
The Picking and Packing Module is an essential part of a Warehouse Management System (WMS) that focuses on fulfilling customer orders efficiently and accurately. This module streamlines the picking process by guiding warehouse staff in selecting the right items from inventory based on customer orders. It also manages the packing process to ensure that items are securely packaged for shipment.
By integrating these two functions, the module helps minimize errors, reduce fulfillment times, and improve overall productivity. Additionally, it enhances the customer experience by ensuring that orders are processed quickly and accurately, leading to higher satisfaction and repeat business.
5. Shipping and Outbound Module
The Shipping and Outbound Module is a crucial component of a Warehouse Management System (WMS) that efficiently manages the final stages of order fulfillment. This module is dedicated to preparing orders for shipment, coordinating with shipping carriers, and ensuring timely delivery to customers.
Automating essential tasks such as label generation, tracking shipments, and managing documentation significantly reduces errors and enhances operational efficiency. The Shipping and Outbound Module also ensures that all items are packed correctly and dispatched on time, which not only boosts customer satisfaction but also helps maintain a reliable and effective supply chain. With improved visibility and control over outbound logistics, businesses can respond quickly to customer demands and optimize their shipping processes.
6. Labor Management Module
The Labor Management Module is a key component of a Warehouse Management System (WMS) that focuses on optimizing workforce efficiency and productivity within a warehouse environment. This module provides tools to track employee performance, manage schedules, and allocate labor resources effectively.
By analyzing labor data, businesses can identify trends, assess workload distribution, and improve operational workflows. The Labor Management Module helps ensure that the right number of employees are assigned to tasks at the right times, ultimately leading to better productivity, reduced labor costs, and enhanced employee satisfaction.
7. Reporting and Analytics Module
The Reporting and Analytics Module is a critical component of a Warehouse Management System (WMS) that empowers organizations to collect and analyze data from various aspects of warehouse operations. By providing insightful reports on performance metrics, inventory levels, and labor efficiency, this module enables managers to make data-driven decisions that enhance operational efficiency.
With features such as real-time dashboards and customizable reports, businesses can identify trends, pinpoint inefficiencies, and track key performance indicators (KPIs). The ability to visualize complex data simplifies analysis, allowing organizations to adapt strategies quickly and optimize resource allocation. Ultimately, the Reporting and Analytics Module serves as a foundation for continuous improvement and strategic planning in the fast-paced environment of warehouse management.
Benefits of WMS Modules
Warehouse Management System (WMS) modules are designed to streamline and enhance various aspects of warehouse operations. By integrating different functions such as inventory management, order fulfillment, and labor management into a cohesive system, WMS modules offer numerous benefits that can significantly improve operational efficiency.
Companies that utilize these modules can expect improved accuracy, reduced costs, and better customer service. With the increasing complexity of supply chains, adopting WMS modules is no longer just an option but a necessity for businesses looking to stay competitive in the market.
1. Improved Inventory Accuracy
One of the primary benefits of WMS modules is enhanced inventory accuracy. By automating inventory management processes, these systems minimize human errors that can lead to discrepancies in stock levels. Real-time tracking and updates ensure that businesses always have accurate data on product availability. This accuracy helps prevent stockouts and overstock situations, allowing companies to maintain optimal inventory levels. Improved inventory accuracy reduces carrying costs and enhances customer satisfaction.
2. Increased Operational Efficiency
WMS modules streamline various warehouse processes, leading to increased operational efficiency. By automating tasks such as order picking, packing, and shipping, these systems reduce the time and labor required for manual operations. For example, automated picking systems guide workers to the most efficient picking routes, significantly speeding up the order fulfillment process. Businesses can handle a higher volume of orders with the same resources, leading to better overall productivity.
3. Cost Reduction
Implementing WMS modules can lead to significant cost savings for businesses. By optimizing labor management and inventory control, companies can reduce unnecessary expenses associated with overstocking and inefficient labor allocation. For instance, better tracking of employee performance enables managers to assign tasks more effectively, reducing overtime and improving productivity. Fewer errors in order fulfillment mean lower costs related to returns and refunds, contributing to an overall reduction in operational costs.
4. Enhanced Customer Satisfaction
With the ability to fulfill orders more accurately and quickly, WMS modules greatly enhance customer satisfaction. Fast and reliable order processing ensures that customers receive their products on time, leading to higher retention rates. Additionally, real-time inventory visibility allows businesses to provide accurate information to customers regarding product availability. This transparency builds trust and strengthens customer relationships, which are crucial for long-term success in today’s competitive market.
5. Better Data Analytics and Reporting
WMS modules offer advanced reporting and analytics capabilities that provide valuable insights into warehouse performance. Businesses can access real-time data on key performance indicators (KPIs), such as order fulfillment rates, inventory turnover, and labor efficiency. This data enables management to make informed decisions, identify trends, and pinpoint areas for improvement. By leveraging data analytics, companies can adapt their strategies to changing market conditions and optimize their operations for better outcomes.
6. Scalability and Flexibility
Another significant advantage of WMS modules is their scalability and flexibility. As businesses grow or experience fluctuations in demand, WMS systems can easily adapt to changing needs. Whether it’s integrating new technology, accommodating additional inventory, or expanding to new locations, these systems provide the necessary support. This flexibility ensures that companies can scale their operations without compromising efficiency, allowing for sustained growth and competitiveness in the market.
7. Improved Labor Management
WMS modules enhance labor management by providing tools for tracking employee performance and optimizing workforce allocation. By analyzing labor data, managers can identify trends, assess productivity, and allocate tasks based on employee strengths. This targeted approach not only improves operational efficiency but also boosts employee morale by ensuring that staff members are engaged in tasks suited to their skills. Effective labor management ultimately leads to a more motivated workforce.
8. Streamlined Compliance and Safety
Compliance with industry regulations and safety standards is critical in warehouse operations. WMS modules help businesses maintain compliance by automating processes that require adherence to specific regulations. For instance, tracking the storage of hazardous materials or ensuring proper labeling of products can be managed more efficiently with a WMS. These systems can implement safety protocols and monitor employee adherence, creating a safer working environment and reducing the risk of accidents.
9. Seamless Integration with Other Systems
WMS modules can seamlessly integrate with other business systems, such as Enterprise Resource Planning and Customer Relationship Management software. This integration allows for the smooth flow of information across different departments, enhancing collaboration and decision-making. For example, sales data from the CRM can inform inventory management decisions, ensuring that stock levels align with customer demand. By breaking down silos between departments, businesses can achieve greater efficiency and improved communication.
10. Enhanced Visibility and Traceability
WMS modules provide improved visibility and traceability of products throughout the warehouse. With real-time tracking capabilities, businesses can monitor the movement of inventory from receiving to shipping. This transparency allows managers to quickly identify the location of items and assess stock levels, reducing the risk of loss or misplacement. Enhanced traceability also aids in compliance with regulatory requirements, ensuring that companies can provide accurate documentation when needed.
11. Optimized Space Utilization
Efficient use of warehouse space is crucial for operational effectiveness. WMS modules analyze storage patterns and suggest optimal layouts, allowing businesses to maximize their available space. By utilizing advanced algorithms, these systems can determine the best locations for items based on their turnover rates and dimensions. This optimization not only increases storage capacity but also reduces travel time for warehouse staff, enhancing overall productivity and reducing operational costs.
12. Reduced Order Cycle Times
WMS modules significantly reduce order cycle times by streamlining processes such as picking, packing, and shipping. Automation features enable quicker order processing, allowing businesses to fulfill customer requests more rapidly. For instance, optimized picking routes minimize the distance workers need to travel, leading to faster order completion. Shorter order cycle times improve customer satisfaction, as clients receive their products more quickly, which is essential in today’s fast-paced market environment.
Conclusion
WMS modules offer a multitude of benefits that significantly enhance warehouse operations, including improved inventory accuracy, optimized space utilization, and reduced order cycle times. By implementing these advanced systems, businesses can achieve greater operational efficiency, better customer satisfaction, and substantial cost savings.
For organizations looking to streamline their warehouse processes and gain a competitive edge in the market, Fynd provides robust WMS solutions tailored to meet your specific needs. Explore how Fynd can transform your warehouse management and drive your business forward with innovative technology and unmatched expertise.
Frequently asked questions
WMS modules are components of a Warehouse Management System designed to streamline and optimize various warehouse operations, such as inventory management and order processing.
By automating tasks and providing real-time data, WMS modules reduce manual errors and optimize workflows, leading to faster order fulfillment and better resource management.
The Inventory Management Module tracks stock levels, locations, and movements, helping businesses maintain accuracy, reduce excess inventory, and prevent stockouts.
Yes, WMS modules can seamlessly integrate with ERP, CRM, and transportation management systems, enabling data sharing and improved operational coordination.
This module optimizes workforce productivity by tracking performance and scheduling, helping businesses manage labor costs and make informed resource allocation decisions.
Fynd offers tailored WMS solutions that enhance operational efficiency and customer satisfaction, supported by advanced technology and expertise in warehouse management.