What is a Work Order Management System?
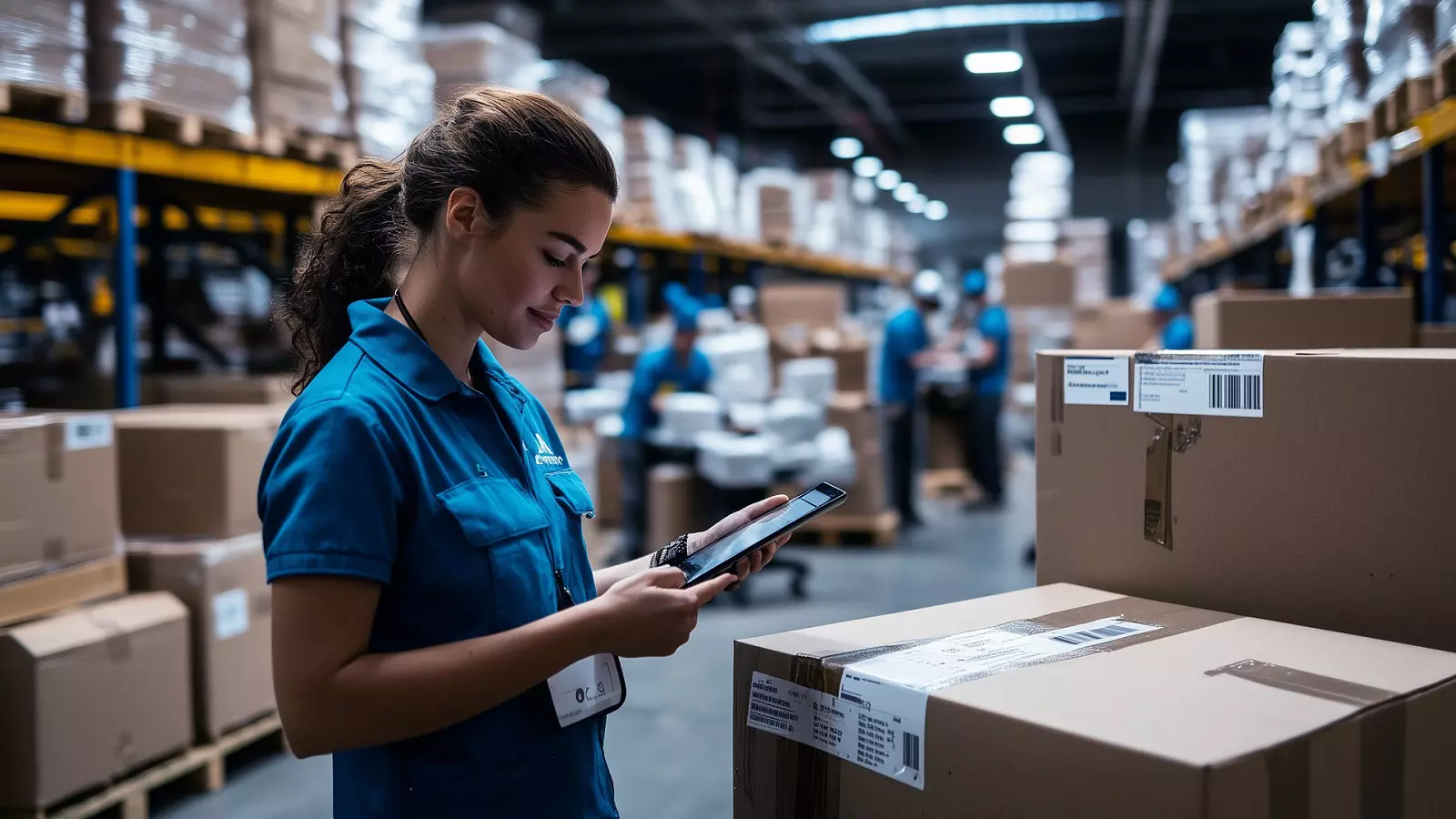
Managing work orders effectively is essential for any organization, regardless of its size or industry. Many users face challenges in tracking and completing tasks, which can lead to inefficiencies, confusion, and wasted resources. Understanding how a Work Order Management (WOM) system functions can significantly improve these processes, ensuring that tasks are completed efficiently and on time.
This blog post will explore the different facets of work order management systems, including their types, processes, benefits, and common challenges. By shedding light on these topics, readers will gain a better understanding of how WOM systems can help streamline operations and improve overall Performance. Knowing the specific types of work orders, for instance, can aid in prioritizing tasks and managing resources more effectively.
In addition to addressing the core concepts, this guide will provide practical insights and best practices for implementing an effective WOM system. Readers will learn how to overcome challenges like communication gaps and manual tracking issues. With this knowledge, you can make informed decisions that not only enhance your workflow but also lead to better decision-making and cost reduction. Ultimately, this blog aims to equip you with the tools and understanding needed to optimize your work order management and drive your organization toward success.
What is a Work Order Management System (WOM)?
A Work Order Management (WOM) system is a software solution that helps organizations create, track, and manage work orders efficiently. It serves as a central hub where users can request maintenance or service tasks, ensuring that all work is documented and assigned appropriately. By following defined procedures, a WOM system helps streamline operations and maintain accountability among team members.
These systems are essential for various industries, including manufacturing, facilities management, and service organizations. By automating work order processes, they reduce manual errors and enhance communication between departments. Overall, a WOM system plays a critical role in improving operational efficiency and ensuring timely task completion.
{{demo_oms="/styles/components"}}
Importance of WOM
The importance of a Work Order Management (WOM) system lies in its ability to streamline workflows and enhance operational efficiency. By providing a structured approach to managing tasks, a WOM system ensures that work orders are prioritized, tracked, and completed in a timely manner. This leads to reduced downtime, which is crucial for maintaining productivity in any organization.
Additionally, a WOM system fosters better communication among team members and departments. It creates a clear record of all requests and actions taken, making it easier to identify issues and implement improvements. Ultimately, investing in a WOM system can significantly boost an organization's overall performance and service quality.
Types of Work Orders
Work orders can be classified into several categories, each serving distinct purposes within an organization. Understanding these types is crucial for effective management and prioritization of tasks. By recognizing the differences between reactive, preventive, predictive, and new business/installations work orders, teams can streamline their processes and allocate resources more efficiently.
This not only enhances productivity but also ensures the timely completion of maintenance and service tasks. A clear grasp of these work order types helps organizations reduce downtime, optimize resource allocation, and maintain operational efficiency.
1. Reactive Work Orders
Reactive work orders are generated in response to unexpected issues or breakdowns. When equipment fails, or a service request arises, these work orders are created to address the problem quickly. While reactive work orders are necessary, relying too heavily on them can lead to increased downtime and maintenance costs, highlighting the need for a balanced approach that includes preventive measures.
2. Preventive Work Orders
Preventive work orders are planned tasks aimed at preventing equipment failure or service disruptions. These work orders are scheduled regularly, allowing organizations to perform maintenance before issues arise. By focusing on routine inspections, part replacements, and system checks, preventive work orders help extend the lifespan of assets, improve reliability, and reduce overall operational costs.
3. Predictive Work Orders
Predictive work orders utilize data analysis and monitoring tools to anticipate when maintenance will be needed. By assessing factors like usage patterns and equipment performance, organizations can proactively address potential issues before they lead to failures. This approach minimizes downtime and reduces maintenance costs while maximizing asset performance, making it a valuable strategy for effective work order management.
4. New Business/Installations
New business/installation work orders are created for the setup and commissioning of new equipment or systems. These work orders involve various tasks, such as installation, testing, and training. Proper management of these work orders ensures that new assets are integrated smoothly into existing operations. This type of work order is essential for expanding business capabilities and enhancing service offerings.
Work Order Management Process
The work order management process is essential for ensuring that tasks are completed efficiently and on time. It involves a series of steps that guide organizations in handling work orders from initiation to closure. By following a structured approach, teams can improve communication, prioritize tasks, and streamline operations. Understanding this process is crucial for organizations looking to enhance their workflow and achieve better results.
Each step in the work order management process plays a vital role in the overall efficiency of operations. From requesting work to analyzing outcomes, these steps ensure that every aspect of work order management is addressed systematically, leading to improved service delivery and operational effectiveness.
1. Work Request Approval
The first step involves obtaining approval for a work request. Employees submit requests when they notice maintenance needs or service issues. This step is crucial for evaluating all requests based on urgency and potential impact. Once approved, these requests move forward, ensuring that critical tasks are prioritized. A clear approval process helps allocate resources effectively and minimizes delays in addressing pressing issues.
2. Work Order Creation
Once a work request is approved, the next step is to create a work order. This document outlines the task's specifics, such as the description, location, and necessary resources. Work order creation formalizes the initiation of the task, providing a clear roadmap for execution. Accurate documentation at this stage ensures that all team members understand what needs to be done, facilitating better coordination and accountability.
3. Prioritization
Prioritization is crucial to ensure that tasks are handled in the correct order. During this step, work orders are ranked based on urgency, importance, and potential operational impact. Effective prioritization allows organizations to focus on high-impact tasks that prevent equipment failures or service disruptions. By addressing the most critical issues first, teams can maximize resource utilization and improve overall operational efficiency.
4. Scheduling
Scheduling involves assigning specific dates and times for when the work will be performed. Proper scheduling ensures that resources, such as personnel and equipment, are available when needed. This step helps avoid conflicts and ensures that tasks are completed within the expected timeframe. A well-structured schedule allows for better planning and coordination among team members, enhancing the overall efficiency of the work order process.
5. Assignment
In the assignment phase, the appropriate personnel are designated to carry out the work order. This involves matching the right skills and expertise to the specific task. Clear communication about assignments is essential, as it ensures that team members understand their responsibilities and deadlines. Assigning the right individuals not only improves efficiency but also enhances the quality of the work performed.
6. Distribution
Once assignments are made, work orders need to be distributed to the relevant team members. This can be done through various channels, such as email, mobile apps, or management software. Effective distribution ensures that everyone involved has access to the necessary information to perform their tasks. By providing clear and timely communication, organizations can reduce confusion and enhance accountability among team members.
7. Execution
Execution is the phase where the actual work is carried out according to the work order details. Technicians or team members follow established procedures to complete the task efficiently and correctly. This step is crucial for ensuring that all work is performed to the required standards. Proper documentation during execution allows for tracking progress and any issues encountered, which aids in future planning.
8. Documentation
Documentation is a critical part of the work order management process. After the task is completed, all relevant details, such as time taken, resources used, and any challenges faced, must be recorded. This information provides valuable insights for future work and helps organizations assess their Performance. Accurate documentation also aids in compliance, reporting, and continuous improvement initiatives within the organization.
9. Closure
After successful execution and documentation, the work order is officially closed. This step involves reviewing the completed task to ensure that all requirements are met and that the work order is fully resolved. Closure is essential for finalizing the work order process and provides an opportunity for feedback. Closing work orders also help maintain accurate records for tracking and performance analysis, ensuring that lessons learned are applied in future projects.
10. Analysis
The final step in the work order management process is analysis. Organizations review completed work orders to identify trends, areas for improvement, and potential issues that may arise in the future. This analysis provides insights into the efficiency of the work order process and helps inform better decision-making for operations. Continuous improvement in work order management leads to optimized resource allocation, enhanced service quality, and overall operational success.
Benefits of Work Order Management
Implementing a work order management system can significantly enhance operational efficiency and streamline maintenance workflows. By organizing tasks and automating processes, organizations can reduce delays and ensure that essential work is prioritized. Understanding the benefits of effective work order management helps teams recognize its value and motivates them to adopt best practices.
This section outlines key advantages that come with a robust work order management system. From cost reduction to improved decision-making, these benefits highlight how effective work order management can lead to overall organizational success.
1. Simplifies Maintenance Workflows
Work order management simplifies maintenance workflows by providing a clear framework for handling tasks. This system allows teams to track work orders easily, ensuring that no tasks are overlooked. By standardizing processes, organizations can reduce confusion and improve coordination among team members. A streamlined workflow enhances productivity, enabling teams to focus on completing tasks efficiently and effectively.
2. Reduces Costs
One of the primary benefits of work order management is cost reduction. By organizing tasks and optimizing resource allocation, organizations can minimize waste and avoid unnecessary expenses. For example, scheduled maintenance prevents costly breakdowns, and better planning leads to more efficient use of time and materials. Over time, these savings contribute to improved profitability and more effective budget management.
3. Detailed Documentation
Effective work order management ensures comprehensive documentation of all maintenance activities. This documentation includes details about completed tasks, resources used, and issues encountered. Detailed records provide valuable insights into operational Performance and help identify trends over time. Additionally, proper documentation is essential for compliance and auditing purposes, safeguarding the organization against potential liabilities.
4. Better-Driven Decision Making
With a robust work order management system, organizations can access accurate data and analytics to inform decision-making. By analyzing work order trends and performance metrics, teams can identify areas for improvement and make informed choices about resource allocation. This data-driven approach enhances strategic planning and ensures that decisions align with organizational goals, ultimately leading to more effective operations.
Common Challenges of Work Order Management
While work order management systems provide numerous benefits, organizations often encounter challenges that can hinder their effectiveness. Recognizing these obstacles is crucial for teams to develop strategies to overcome them. By addressing these challenges, organizations can improve their work order processes and enhance overall productivity.
This section explores the common challenges faced in work order management. Understanding these issues helps organizations proactively address them, leading to smoother operations and better outcomes. For now, let's see what are the common challenges of WOM, which are as follows:
1. Communication Gaps
Communication gaps can significantly disrupt the work order management process. When team members do not effectively share information, it can lead to misunderstandings about task requirements and priorities. Clear communication may prevent delays in work execution and result in mistakes. To mitigate this challenge, organizations should implement effective communication tools and foster a culture of collaboration among team members.
2. Prioritization Confusion
Prioritization occurs when teams need help determining which tasks should be addressed first. Without a clear system for ranking work orders, critical issues may be overlooked, leading to service delays and decreased efficiency. Establishing a prioritization framework helps teams focus on high-impact tasks, ensuring that urgent work is completed promptly. Reviewing and updating priorities can also help alleviate confusion.
3. Real-Time Tracking Issues
Real-time tracking is essential for effective work order management, but many organizations struggle to implement this feature. Without real-time visibility, teams may miss crucial updates on task status or resource availability. This lack of tracking can result in delays and miscommunication. To improve real-time tracking, organizations should invest in modern work order management software that offers dashboards and alerts to keep teams informed.
4. Manual Work Order Management
Relying on manual processes for work order management can lead to inefficiencies and errors. Paper-based systems are often prone to lost documents, miscommunication, and delays in task execution. Transitioning to a digital work order management system can streamline operations by automating workflows, improving data accuracy, and enabling better tracking of tasks. Embracing technology is essential for overcoming the limitations of manual management.
Best Practices for Work Order Management
To maximize the effectiveness of a work order management system, organizations should adopt best practices that promote efficiency and reliability. Implementing these strategies helps streamline workflows, improve communication, and enhance overall productivity. By following established best practices, teams can ensure that their work order processes are effective and tailored to meet their specific needs.
This section highlights key best practices for work order management. Understanding and applying these practices can lead to smoother operations and better outcomes for organizations, ultimately driving success.
1. Prioritize and Categorize Work Orders
Effectively prioritizing and categorizing work orders is essential for efficient operations. By distinguishing between urgent and routine tasks, teams can focus on what matters most. Categorizing work orders based on factors like type or department also helps in assigning them to the appropriate team members. This structured approach ensures that critical tasks receive the attention they need, preventing delays and enhancing productivity.
2. Implement Standard Operating Procedures (SOPs)
Standard Operating Procedures (SOPs) provide clear guidelines for managing work orders consistently. Establishing SOPs ensures that all team members follow the same processes, reducing confusion and errors. These procedures also help in training new employees, ensuring they understand their roles and responsibilities. Regularly reviewing and updating SOPs can keep them relevant and effective, contributing to continuous improvement in operations.
3. Monitor and Evaluate Performance
Regularly monitoring and evaluating Performance is crucial for identifying areas of improvement within the work order management process. By analyzing metrics such as completion times and resource utilization, organizations can gain insights into their efficiency. This data-driven approach allows teams to adjust processes and implement changes that enhance productivity. Conducting periodic reviews fosters a culture of accountability and continuous improvement.
4. Use Work Order Software
Investing in work order management software can significantly improve operational efficiency. These digital tools streamline workflows by automating tasks, enabling real-time tracking, and enhancing communication among team members. Software solutions can also provide valuable analytics, helping organizations make informed decisions. Choosing the right software tailored to specific needs can transform the work order management process, leading to better outcomes.
Improve Work Order Management with Fynd OMS
Fynd Order Management System (OMS) offers comprehensive solutions to enhance work order management, addressing common challenges faced by organizations. With its user-friendly interface and robust features, Fynd OMS simplifies the entire work order process, enabling teams to manage tasks efficiently. The system ensures that all work orders are tracked in real-time, providing insights into progress and resource allocation.
By leveraging Fynd OMS, organizations can streamline workflows and improve communication among team members. The software allows for the prioritization of tasks based on urgency, ensuring critical work is completed on time. Additionally, Fynd OMS integrates seamlessly with existing systems, making it easier for teams to adapt and improve their operations.
Conclusion
An effective work order management system is essential for organizations aiming to enhance operational efficiency and productivity. By understanding the types, processes, benefits, and challenges associated with work order management, teams can make informed decisions to improve their workflows. Adopting best practices, such as prioritizing tasks and utilizing work order software, can lead to significant improvements in Performance and cost reduction.
By implementing solutions like Fynd OMS, organizations can overcome common challenges and streamline their work order processes. With the right tools and strategies in place, teams can ensure that they meet their goals effectively and continue to deliver high-quality service to their customers.
Frequently asked questions
A work order management system (WOM) is a software solution that helps organizations create, track, and manage work orders efficiently. It streamlines maintenance processes and enhances communication among team members.
The main types of work orders include reactive, preventive, predictive, and new business or installation work orders. Each type serves a different purpose in maintenance and operations.
Work order management can reduce costs by optimizing resource allocation, preventing equipment breakdowns through preventive maintenance, and improving overall operational efficiency.
Common challenges include communication gaps, prioritization confusion, real-time tracking issues, and reliance on manual processes, which can hinder efficiency.
Best practices include prioritizing and categorizing work orders, implementing standard operating procedures (SOPs), monitoring Performance, and using dedicated work order management software.
Fynd OMS enhances work order management by providing real-time tracking, facilitating better communication, and automating workflows, which helps organizations streamline their processes and improve efficiency.