Warehouse vs inventory management: systems, automation & future trends
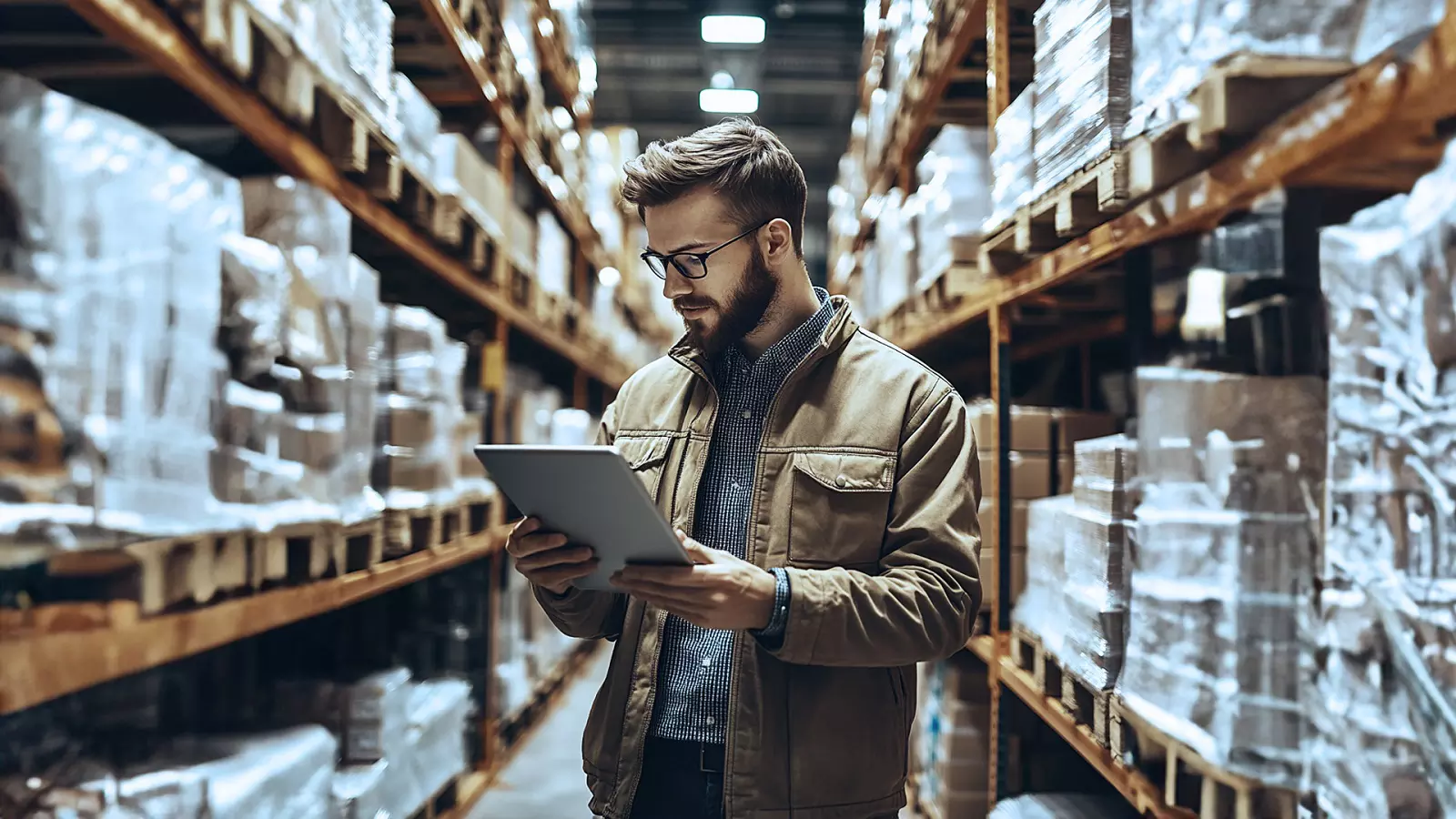
Every time a customer has their delivery fulfilled smoothly, a system must have been at work to organize, track, and move the products. The system relies heavily on two functions: warehousing and inventory management. Although warehousing and inventory management may seem interchangeable terms in conversation, they serve different functions that require distinct strategies in practice.
Warehousing is specifically concerned with the space, including how products are stored, handled, and moved around a facility. Inventory management is more about visibility, such as keeping track of what is in stock, specifically where it is located, when it needs to be reordered, etc.
While the difference can seem minor, the effects are not. Poor coordination between the two functions can result in overstocked products, missed orders, backorders, or late shipments, which ultimately compromise customer satisfaction.
However, when warehousing and inventory systems are integrated, they can reduce costs, increase turnaround time, and increase accuracy. In this blog, we explore more about where inventory and warehousing management work together, where they differ, and how businesses can take advantage of both.
Understanding inventory vs. warehouse management
Inventory and warehouse management are often discussed together, and for good reason. They are connected, often overlap, and both play an important role in a company’s supply chain performance. However, while they work hand in hand, they have two different objectives.
The primary difference revolves around focus: inventory management focuses on visibility and control of stock, whilst warehouse management focuses on efficiency in physically handling that stock. When they're both clearly defined and aligned, inventory and warehouse management can set the stage for accurate, reactive, responsive, and scalable operations.
In this section, we'll describe each system, starting with inventory management.
What is inventory management?
{{demo_wms="/styles/components"}}
Inventory management refers to the process of keeping track of, controlling, and optimizing goods within the supply chain. Inventory management makes sure that goods are available at the right time, place, and quantity while maintaining minimal capital or risk of running out of stock. Because inventory often serves as a representation of working capital for businesses, inventory management goes beyond back-office operations; it impacts customer experience, operational costs, and revenue.
At its core, inventory management answers a few critical questions:
- How much stock do we have?
- Where is it located?
- When should we reorder?
- How much should we order?
The answers to these questions can assist a business to find a healthy balance between supply and demand. Poor inventory management results in excess inventory, which can incur storage costs or the waste of lost inventory. Conversely, low levels of inventory can lead to slowdowns in business and ineffective sales, which decrease customer satisfaction.
Inventory management is applicable in almost every industry, from retailers monitoring seasonal inventory to manufacturers managing raw material shortages to e-commerce brands running similar inventory with a number of fulfillment centers. There are differences in complexity, but the essence is the same: managing inventory with visibility and control in order to achieve business objectives.
While quarterly or semiannual counts are still required in many businesses, modern inventory management extends far beyond spreadsheets and infrequent audits. Using cloud based software with automation and smart tracking not only reduces costs but gives the businesses the ability to monitor how much inventory they have across different sites and ahead of the demand as well as have the reorder point and also integrate their own chain with those of the suppliers and their sales channels to respond quicker and have fewer human errors.
It is fair to say that inventory is a strategic and operational decision. If an organization is successful with inventory, it can move quicker, respond faster to changing consumer behavior, and give consumers a better shopping experience with less wasted inventory and risk.
Advanced inventory management techniques
Although it is good to monitor inventory on a basic scale, advanced techniques can assist companies to adequately optimize stocks, use carrying costs, and be demand responsive throughout the entire supply chain. They result in a competitive advantage in bringing about the reactive position of inventory management into a proactive position. Below are four key techniques widely used across industries:
1. ABC analysis
ABC analysis separates inventory into three subsections and is generally based on usage of sales volume/value.
- A-items are easy to identify; they are the high-price, low-quantity items that make up the highest part of revenue but require tighter controls.
- B-items fall in between.
- C-items are low-price, high-quantity items that need the least control.
Using an approach like this allows businesses to prioritize resources, minimize excess stock in low-impact areas, and direct attention to high-focus areas.
2. Economic order quantity (EOQ)
EOQ is a formula that provides the optimal order quantity for a business to order, in order to minimize total inventory costs, especially the ordering costs and holding costs associated with keeping inventory. It is also assumed to be fixed costs and steady demand, so it is strictly applicable to businesses with predictable inventory needs.
The basic formula is:
EOQ = √(2ds / h)
Where:
- d = demand rate.
- s = ordering cost per order.
- h = holding cost per unit per year.
By determining the economically ordered size of orders, businesses can reduce unnecessary ordering, overstocking, and generally improve cash flow.
3. Just-in-time (JIT)
Just in time inventory management or JIT, focuses on stockpiling the least amount of inventory possible and buying in replenishes only when absolutely necessary for production or sale to the customer. JIT management reduces carrying and waste costs, but it hinges on supplier reliability and if the business is tightly coordinated.
JIT is common in industries like automotive and electronics manufacturing, but it carries the risk of stockouts. Effective JIT inventory management depends heavily on close supplier coordination and reliable lead times. Businesses who wish to use JIT business practice must invest in planning tools and stronger supplier partnerships.
4. Safety stock
Safety stock is the extra inventory kept on hand to protect against uncertainty in demand or supply. Safety stock is intended to buffer against stockouts as a result of delays from suppliers, demand spikes, or variance from forecasting.
The amount of safety stock kept must be based on lead times, variability of demand, and desired service level. Too much safety stock increases holding costs, and too little safety stock can lead to lost sales. Demand forecasting and lead time will help set safety stock targets.
By bringing such techniques to practice independently or in combination with each other, companies will be able to advance inventories more efficiently. The combinations and techniques used will be industry and business model specific, as well as risk tolerance, but if a business can become proficient in even one, meaningful increases in performance and profitability can be achieved.
What is warehouse management?
Warehouse management is the management, control, and optimization of the physical processes in a warehouse and/or distribution center. Warehouse management encompasses every process from how goods are received, stored, and picked to how they are packed, shipped, and replenished. As the objective of warehouse management is to move goods through the warehouse or distribution center as effectively, efficiently, accurately, and cost-effectively as possible, warehouse management typically has ground-level visibility into actual inventory locations and so operates with physical spaces.
Warehouse management is distinct from inventory management since inventory management tracks items in terms of levels and availability at various locations, whereas warehouse management is concerned with how inventory is physically moving or being moved in a given space.
Managing how inventory is moved about in a warehouse or distribution center includes managing the people and equipment in the warehouse or distribution center, the storage configurations of inventory, as well as the work processes to minimize bottlenecks and maximize throughput.
Core functions of warehouse management include:
- Receiving and inspection of incoming goods.
- Putaway (assigning storage locations).
- Order picking and packing.
- Cycle counting and stock verification.
- Shipping and dispatch.
- Returns and reverse logistics.
- Performance tracking (e.g., order accuracy, picking speed).
An effective warehouse management strategy means not only shipping the right products to the right customer, but also maintaining control over your operating costs/expenses in doing so. For example, by optimizing your pick paths, you will spend less time travelling, and proper slotting of your high turnover items will help put your order together faster.
Modern warehouse management is influenced heavily by technology. Most businesses use a Warehouse Management System (WMS) to manage everyday operations and provide real-time direction to employees, while taking into consideration available labor, replenishment triggers, barcoding, and labor assignment rules. These features increase visibility, minimize human error, and ultimately help businesses scale as demand increases.
Warehouse management is no longer simply storing items - it is integral to the customer experience. Efficient, rapid, and flexible warehouse operations can give your company a distinct competitive edge.
What do inventory management and warehouse management have in common?
Inventory management and warehouse management focus on different areas of the supply chain, but they are inherently linked. Typically, in most organizations, the systems and teams responsible for inventory management and warehouse management should work closely with one another to maintain inventory accuracy, reduce inefficiencies, and ensure the movement of the product is smooth from storage to shipment.
In general, both inventory management and warehouse management align and work toward better visibility, better operating practices, and better decision making. The two functions share a number of shared objectives and performance measures, especially true in high-volume and fast-paced businesses, such as retail, manufacturing, and e-commerce.
Shared goals
- Improve order accuracy.
- Reduce carrying and handling costs.
- Increase product availability.
- Minimize delays and disruptions.
- Maintain real-time visibility into stock and movements.
Shared key performance indicators (KPIs)
- Inventory turnover: A metric that shows how frequently inventory is sold or used within a specific time frame (typically monthly or annually). It is calculated as sales (or cost of goods sold) divided by average inventory. A high turnover often indicates efficient inventory management and strong sales performance.
- Order accuracy rate: the percentage of orders without errors. This is a measure of the accuracy of inventory and the execution of warehouse operations.
- Space utilization: a measure of how storage is being used in the warehouse. Poor space utilization can lead to congestion or increased storage costs.
- Cycle time: the time it takes to pick, pack, and ship an order. Cycle time will depend on the physical layout of the warehouse as well as the accessibility of inventory.
- Stockout rate: how often items cannot be found when ordered. These stockouts are caused by bad stocking processes or back-orders due to delayed finishing of orders.
Combining inventory management and warehouse management functions can greatly enhance efficiency for many companies, either through integrated software or aligned processes. Companies are able to minimize double handling and discrepancies to mitigate the risk of holding stock when they do not really need to, and reacting quicker to changes in demand and supply is possible when both systems are working together.
Difference Between Inventory Management and Warehouse Management
Inventory management and warehouse management often complement each other, but serve different functions in the supply chain. It can be helpful to know the difference when researching software, engaged in a process, or thinking about scaling. While both inventory management and warehouse management are concerned with goods and inventory, they are different not only in function, but also in focus, meaning, execution, and systems.
Key differences at a glance:
IMS vs. WMS: features and differences
Inventory management systems (IMS) and warehouse management systems (WMS) are specialized tools that both serve a unique purpose in the supply chain. IMS focuses on what stock you have, where it is stored, and how close it is to requiring replenishment. WMS focuses on the physical handling of that stock while it is being stored, and what happens to it when it is moved throughout the warehouse.
Together, an IMS and a WMS provide a solid foundation for a more efficient flow of operations, from when the purchase is planned to when the customer receives it.
What is an inventory management system (IMS)?
An inventory management system (IMS) is a solution that helps a business track the amount of inventory they have, manage inventory levels across multiple locations, and automate tasks such as re-ordering and demand forecasting. An IMS is especially useful in an omnichannel environment where the stock is spread out across warehouses, retail stores, and fulfilment partners.
What is a warehouse management system (WMS)?
A WMS is made to help manage and optimize the daily activities of a warehouse. A WMS provides real-time visibility into every aspect of warehouse workflows, directing the activities of workers, assigning storage, once a storage location is chosen, managing how the picks/packages are handled, as well as connecting with devices (scanners, mobile terminals, etc.) used in warehouse operations.
IMS vs. WMS: side-by-side comparison
Both systems add value individually, but together they provide significant value, while adding efficiency, particularly within intricate or high-volume supply chains.
Cost considerations and roi analysis
When deciding between an IMS and WMS, you're not only faced with a technology decision, you're also faced with a financial decision. Each system has a different cost structure and long-term value based on your particular business complexity, transaction volume, and rated growth.
- The cost of implementation is cheaper in inventory management systems than it is in warehouse management systems, since they can also be implemented at a SaaS subscription level. Inventory management systems are usually simple and easy to install, and ROI is usually justified via cash tied up in inventory, stockouts, or better forecasting.
- Warehouse management system often needs more investment, particularly when investment in hardware, customization of systems, and training of teams is involved. The returns, though, when scaled at large and in their busy environment, are big: utilization of space, reduction of errors in the process of filling orders, and labor efficiencies can be very high.
Businesses often see the most ROI from using both WMS and IMS, though this may not be practical for all, especially smaller firms with limited resources. When IMS and WMS operate together, inventory planning and warehouse execution align, improving efficiency, customer satisfaction, and drastically reducing costly errors.
Integrating inventory management and warehouse management systems for operational success
Although an Inventory Management System (IMS) and a Warehouse Management System (WMS) exist to accomplish different tasks, their true potential is realized when they become integrated. This will allow a closed feedback loop of inventory planning and warehouse execution to provide real-time control, visibility, and agility.
Integrating IMS with WMS allows:
- Real-time inventory visibility across all inventory locations and channels.
- Synchronized order fulfillment that looks to the correct available inventory.
- Ability to respond faster to any customer demand and supply chain disruptions, returns, etc.
- Timely reporting and KPIs, as the expense of manual data transfer is eliminated.
How integration operates:
IMS (inventory management system) and WMS (warehouse management system) usually integrate via APIs or middleware solutions that allow data to flow automatically between systems. Certain enterprise solutions deliver both as part of a combined suite, while others utilize best-of-breed solutions in which integration is performed through custom or third-party solutions.
A good system integration method allows:
- Sales orders generated in IMS will automatically generate pick tasks inside WMS.
- Inventory being captured in the warehouse will reflect instantly on all its channels.
- Returns, cycle counts, and recommendations are universally referenced and updated across systems.
Advantages of having a unified system:
- Greater accuracy – It reduces shipping errors when the inventory data is accurate and consistent across the board.
- Improved fulfillment speed – Integrated systems work in real time to allow for tasks to be assigned and to choose the best paths to pick items for the sales order that is being filled.
- Improved forecasting and planning – With the two systems feeding you accurate data, planning and forecasting have never been easier.
- More scalable – Unified systems can accommodate a greater volume of orders and sales without issue.
Warehouse automation and emerging technologies
Warehouses are more than static storage spaces. They are becoming intelligent ecosystems, powered not just by automation, but also by integration and real-time data visibility, to help retailers scale, reduce costs, and serve complex customer demands. But for automation to have a meaningful impact, the warehouse must be underpinned by a connected IMS-WMS infrastructure.
What is warehouse automation?
Warehouse automation is the use of technology to perform repetitive, time-consuming, or high-risk tasks. This can mean everything from moving inventory within a warehouse to providing up-to-the-minute data on product conditions.
Advantages of automation include:
- Quicker and more reliable picking and packing.
- Lower labor dependency and costs.
- Safer working environments.
- Better accuracy and traceability of inventory.
So, now let's dive into the technologies that are leading this charge.
1. Robotics
Autonomous robots aren't just science fiction anymore; they're becoming critical to today's warehouses. Two key classes are present:
- Autonomous mobile robots (AMRs) - these smart robots operate on the warehouse floor autonomously. They can deliver bins to human pickers and also collaborate in a goods-to-person system.
- Automated guided vehicles (AGVs) - these vehicles drive products along established paths, moving either pallets or carts between warehouse points.
Robots can improve order picking speed, reduce walking time and errors, and help companies handle high volumes more efficiently. However, they still require human oversight, and the cost savings may not always scale linearly with volume.
2. Internet of Things
The Internet of Things refers to a network of devices that can collect data and share it in real-time. In warehousing, these devices include:
- RFID Tags and readers - help track the movement of product throughout the facility.
- temperature and humidity sensors - monitor the conditions for sensitive goods.
- Smart shelving systems automatically sense stock levels.
These devices can send constant updates to IMS and WMS platforms, providing visibility that manual systems cannot achieve. For example, if an RFID tag shows that a pallet has entered the wrong zone, the WMS can automatically create a correction task.
3. Artificial intelligence (AI)
AI can help make sense of the vast amount of supply chain data. In warehouses, AI enables:
- Predictive analytics - Predict demand patterns so you can adjust inventory levels ahead of time.
- Task optimization - Assign workers and equipment based on workflows, not on set schedules.
- Anomaly detection - Identify unusual trends, such as mis-picks or slowdowns, in real-time.
AI is not just a potential benefit; it is providing real benefits now. Research from McKinsey indicates that companies that adopt AI in their supply chain practices have reduced logistics costs up to 15%, decreased inventory levels as much as 35%, and increased service levels by 65% compared to slower adopters.
In a competitive marketplace, this is much more than a technology opportunity; this is a strategic advantage.
4. Automated storage and retrieval systems (AS/RS)
Automated Storage and Retrieval Systems (AS/RS) employ robots and control systems to automatically place and retrieve inventory in designated storage locations. AS/RS systems may include the following components, depending on use case:
- Shuttle systems for fast-moving items.
- Crane-based units for high-density vertical storage.
- Carousels for small-item picking.
AS/RS improves space efficiencies and reduces picking errors. AS/RS provides solutions for environments where limited space and picking accuracy are a primary concern.
Regardless of the automation technology, these systems must rely heavily on real-time data and tightly integrated systems. A robot is worthless without knowledge of the accurate location of an item. An AI model is of no value unless it has been trained on reliable and repeatable data streams from across inventory and warehouse activities.
This is why you cannot underestimate the importance of the integration between an IMS and a WMS - it is an accountability and single source of truth that automation requires to deliver on its promises.
How to manage warehouse inventory and inventory management challenges
Controlling inventory within a warehouse may sound easy, but it is a multifaceted challenge. Companies need to strike a balance between having enough inventory to meet demand and excess inventory that could cost them unnecessarily and take up space. To do this across channels, locations, and seasons requires strategy and technology.
Common challenges of warehouse inventory management:
1. Inaccurate Inventory Records
A simple human error while manually entering information, missing a scan, or using a system that is years outdated, can create a disparity between the stock level of record and the physical stock on hand. As a result, businesses will see more stock-outs, unwanted overstock, and poor customer experience.
2. Absence of real-time visibility
If a company does not have real-time updates, it is difficult to manage stock in a timely manner. This is especially challenging in an omnichannel environment where inventory passes quickly through digital and physical channels.
3. Poor picking and storage efficiency
When inventory storage is not organized or is not set up logically, your pickers will spend more time walking the aisles than they will completing a pick. If your layout design is poor, it will impact speed and accuracy.
4. Demand variability
Some tend to overlook variabilities like seasonal spikes, unexpected changes in consumer demands, or changes/disruptions in the supply chain. Without good inventory forecasting, companies can find themselves reactive instead of proactive.
5. Safety and compliance risks
Warehouses must comply with safety regulations (e.g., OSHA) as well as health regulations if the inventory includes hazardous materials. Lack of visible or accurate labeling, walking paths that are cluttered, or having outdated safety practices can result in a company being fined or, worse, injury.
Best practices for better warehouse inventory management
1. Invest in strong IMS and WMS systems
Technology is the core of everything. A well-functioning inventory management and warehouse management system will pull data, ensure accuracy, and support short-term decision making.
2. Do cycle counts regularly
Instead of closing the entire facility for full physical counts, do rolling cycle counts. This will limit disruption and will maintain accuracy across the facility.
3. Improve warehouse layout
Fast-moving items should be grouped closest to the shipping zones, categories should be grouped in an order that makes sense spatially, and pathways should be designed to limit backtracking. More efficient layout = faster picks.
4. Use demand forecasting models.
Using forecasting tools that use sales trends, seasonality, and external factors will allow you to make changes in quantities stocked before they happen and prevent over-ordering or stockouts.
5. Set clear safety protocols.
Train people, make signs, and conduct regular audits of safety priorities. Only safe practices keep things compliant and safe. Every on-site incident is preventable and costly.
Tools to mitigate issues
- RFID systems and barcoding for tracking movement precisely.
- Mobile warehouse apps can perform a real-time inventory check and task management.
- Artificial intelligence-based predictive models to foresee demand.
- Slotting software to constantly optimize where the inventories shall go.
Warehouse layout and design: one of several key drivers of warehouse performance
Layout isn't only about space; it is about flow. A good layout reduces travel time, avoids congestion, and allows pickers to systematically flow through the operation. Here is some layout advice:
- Use A-B-C slotting to position high-volume stock closer to the packing stations.
- Separate your receiving and shipping zones to eliminate cross-traffic.
- Incorporate sufficient lighting and signage to allow quick navigational decisions.
- Construct wide one-way aisles to improve safety and efficiency.
Safety, compliance, and risk management
Compliance is often an afterthought, but it shouldn't be. Unsafe warehouses create risk for employees and can stop operations completely.
Key areas to monitor
- OSHA compliance: proper labeling, signage, PPE, and training.
- Fire safety: clearly marked exits, functional extinguishers, compliant storage of flammables.
- Loss prevention: CCTV, audit controls, and access controls can reduce the risk of theft or shrinkage.
- Incident reporting systems: promote, timely, and open reporting.
A safe warehouse is a productive warehouse.
Future trends in the functions of inventory management and warehousing
As consumer expectations continue to rise and supply chains span the globe, inventory and warehouse management are changing rapidly. The way businesses evolve today in response to future trends will create tomorrow’s success. The future will involve a combination of technology, people, data, and strategy–think sustainable, intelligent automation.
1. Sustainability and green warehousing
Environmental responsibility is not merely a trend anymore; it has become a necessity in business. Warehousing activities have been left with the responsibility to produce less carbon and institute greener work.
The major sustainability trends are:
- Lighting and HVAC systems that are energy efficient to reduce power requirements.
- Warehouses powered by the sun to balance grid power.
- Package materials that can be renewed to reduce landfill.
- WMS systems are connected to carbon-tracking tools.
Aligning logistics with environmental goals helps a brand meet regulatory requirements and social expectations. Deloitte conducted a survey on sustainability in the consumer business. The survey showed that when consumers were aware that sustainable products would likely cost more, 67% said they were willing to pay as much as 41% more, with a stronger inclination in younger age groups.
2. Unified commerce and real-time inventory synchronization
The barrier between ecommerce and physical retail is becoming indistinct. Companies need to offer omnichannel visibility in real-time across all channels. This future is unified commerce, where inventory is centrally controlled and made available through all channels.
This means:
- Real-time syncing of inventory across all online and offline sales channels.
- Integrated, returns, and reverse logistics.
- Intelligently routed orders based on location, available stock, and cost efficiencies.
When implemented effectively, unified commerce can drive efficiencies and improve customer satisfaction by accurately displaying in-stock items and enabling faster fulfillment options.
3. Robotics-as-a-Service (RaaS)
This model (Robotics-as-a-Service) is gaining popularity with the expansion of warehouse robotics: Instead of spending on and maintaining expensive robotics, companies can outsource services of robotics companies and have the flexibility of deployment.
The advantages involve:-
- Lower direct cost.
- Enables scaling up more easily during the peak seasons.
- The upgrades on software and hardware are up to date.
Since warehousing needs are occasionally subject to fluctuations, the Raas enables the companies to remain dynamic without long-term commitments in infrastructure.
4. Blockchain for inventory traceability
Blockchain remains an emerging solution with limited adoption, but it holds promise for enhancing traceability and transparency in supply chains. This may enhance trust and traceability in complex and multi-party supply chains.
Some possible use cases include:
- Verifying product authenticity (particularly for pharma or luxury goods).
- Automate audit trails and compliance reporting.
- Fostering supplier accountability.
While blockchain has been explored for improving supply chain transparency, widespread adoption in inventory and warehouse systems remains limited due to scalability and adoption challenges.
Inventory and warehouse management are no longer back-office functions. They are now the key to fulfilling customer satisfaction, ensuring operational efficiencies that come from better informed decision making, and keeping pace with market changes.
As technology continues to evolve and customer expectations continue to increase, you will be better positioned to adapt and survive as a business if you make an investment in a modern inventory management system (IMS), warehouse management systems (WMS), or an integrated inventory, warehouse, and supply chain approach.
The future of supply chain excellence lies not in choosing between inventory and warehouse management but in understanding how they intersect, mutually support, and elevate each other. If you work on them to be aligned and effective, then they become an integrated engine of growth, effectiveness, and long-term value.
Frequently asked questions
A WMS manages the physical movement, storage, and tracking of items within a warehouse or distribution center. An IMS monitors quantities, locations, and movements of products throughout all locations where inventory is held, including warehouses, stores, and fulfillment centers.
A WMS can enhance warehouse operations by organizing and optimizing how tasks like picking, packing, receiving, and storage are completed. A WMS also reduces mistakes, increases the speed of workflows, and allows for a better use of space, all of which lowers costs and increases accuracy.
Inventory management measures to monitor include: Inventory turnover ratio, carrying cost of inventory, accuracy of orders, cycle time, stockout rate, and demand forecast accuracy. These measures allow businesses to manage the stock they have and help react to demand changes early.
Inquire about price and feasibility of adding and removing features as needed, functionality for real-time tracking, barcodes or RFID, forward and reverse order management, demand forecast, analytics, and the ability to easily integrate with your existing erp or ecommerce platforms. Also, check on scalability and if they have a user-friendly dashboard.
Common problems are wrong inventory counts, bad layout design, lack of real-time visibility, ineffective picking techniques, and compliance issues. To address these challenges, you need both effective practices and the right technology.
Through integrations, you can share data seamlessly between the IMS and WMS platforms, which provides you with access to real-time visibility, as well as truly coordinated processes across operations, reduced redundancy, and improved decision-making capabilities, as well as increased opportunities for automation and end-to-end supply chain optimization.