12 Best Warehouse Management System Examples in 2025
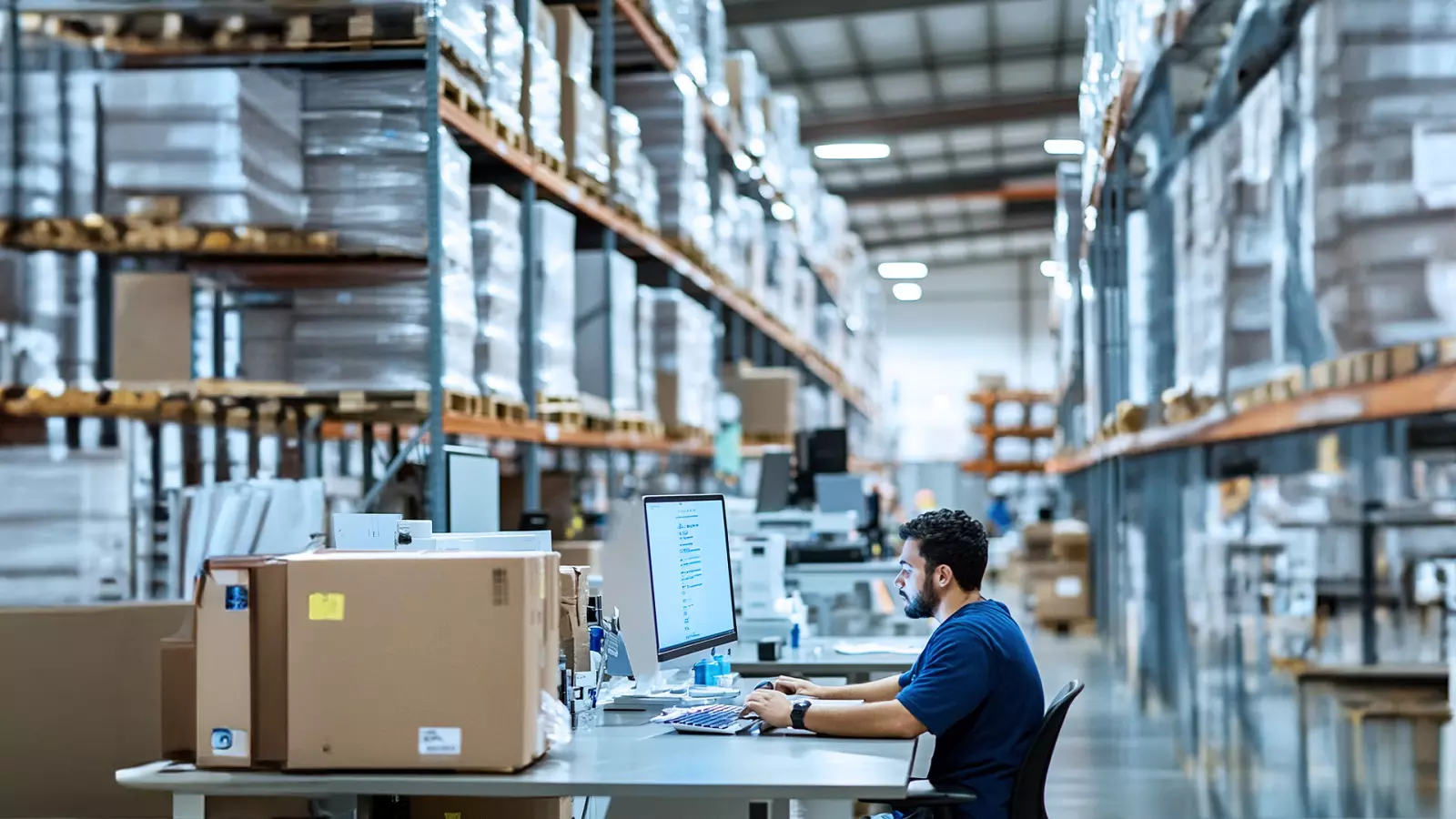
Warehouse operations are no longer what they once were. As customer expectations rise, delivery windows shrink, and e-commerce grows rapidly, companies re-evaluate how their warehouses operate and turn to technology to keep up.
That trend has created a boom in the warehouse management systems (WMS) market. Recent research has found that over 90% of supply chain leaders intend to invest in technologies such as WMS to improve efficiency and resilience. It is likely a coincidence that new WMS providers emerge quarterly, and this is because each claims to have better features, faster integration, and better outcomes.
{{demo_wms="/styles/components"}}
But greater choice does not always mean an easier choice. With scores of choices now, from the thin cloud guys to the deep enterprise-level ones, selection can be overwhelming. Choosing incorrectly can result in a costly delay, a poor user adoption, and a system that just doesn’t do what you need.
That is why it is more important than ever to slow down, cut down the noise, and select a WMS that aligns with your operational needs. In this blog, we’ll guide you through this process, starting with the explosion of the WMS market and what actually counts when choosing from the available solutions.
What is a warehouse management system (WMS)?
A Warehouse Management System (WMS) is the digital architecture of today’s warehousing. It’s a software program for controlling and optimizing all aspects of operation in the warehouse, including the receiving and storage of goods, picking, packing, and the shipment of goods. Imagine it is the invisible hand directing inventory flow, worker efficiency, and accuracy of orders.
But here’s the kicker: In today's instant delivery-widening omnichannel world, a returns center no longer offers a competitive advantage—it’s vital. It provides businesses with real-time inventory visibility, minimizes costly mistakes, quickens fulfillment, and opens agility across the supply chain.
Whether you have a small warehouse or a global fulfillment network, a WMS will ensure that your operations run smoother, faster, and smarter.
Warehouse management system examples
1. Fynd WMS
The world of retail is moving fast, and efficacy, accuracy, and flexibility are highly important. Fynd WMS has been developed to serve these demands, providing a complete set of solutions that regulate warehouse activities and improve overall productivity.
Why choose Fynd WMS?
Seamless inbound operations
- Gain complete visibility on incoming shipments and co-sign all documents right in the app.
- Employ intelligent zoning to simplify the receiving process to unload and store effectively.
- Perform quality checks and allocate an appropriate number of unloading docks without waste of time and mistakes.
Optimized putaway processes
- Be smart with route mapping to increase storage space and workforce efficiency.
- Intelligently pair products to uniquely categorized bins based on categories, values, and purchase history.
- Create rules for the assignment specifically to meet the particular business's needs.
Efficient order fulfillment
- Use intelligent batch creation and picking algorithms to increase the accuracy of orders.
- Use mobile picking and sorting devices to track orders in real time and thereby reduce fulfillment time.
Real-time inventory management
- Guard inventory stock in several locations through real-time tracking.
- Increase the likelihood of neither overstocking nor stockouts by maintaining one trusted inventory picture.
Scalability and flexibility
- Onboard new customers with easy access and operate multiple facilities using the same platform.
- It is sensitive to changing business needs and is highly appropriate for 3PLs and growing companies.
Enhanced customer satisfaction
- Specifically, ensure the timely and correct deliveries and consequently improve the levels of customer trust and loyalty.
- Give real-time updates and transparency with the order fulfillment process.
Seamless integration
- Seamlessly integrate with TMS software, ERP system, and e-commerce platforms, including Shopify and WooCommerce.
- Simplify the bidirectional exchange of information, reduce human errors, and increase forecasting power.
Fynd WMS is an attractive, intelligent, user-centric, and scalable solution uniquely tailored to ensure it always keeps up with the changing demands of modern warehouse activities. Enterprises advance to a peak of stunning efficiency, accuracy, and customer satisfaction with its buy-all and get-all.
2. Oracle warehouse management cloud
Customers today demand more than ever before: fast delivery, accurate orders, and full visibility into inventory. Warehouse operations must be efficient but also smart, responsive, and scalable to compete.
That's where Oracle Warehouse Management Cloud (WMS) comes in. Built for the digital supply chain, this cloud-based application enables you to streamline fulfillment, automate warehouse operations, and see in real-time across your network. Whether you're operating a distribution center, a store, or providing 3PL services, Oracle WMS provides the power and freedom to reduce costs, increase accuracy, and adapt quickly to change.
Why choose oracle WMS?
- Fulfillment from anywhere: Transform any site location like a warehouse, retail store, or kiosk into a smart and linked fulfillment hub.
- Seamless omnichannel support: The integration of retailing, electronic commerce, and wholesale order fulfillment as an optimized process. Offer faster and better service in all the avenues utilized.
- Complete inventory visibility: Track inventory in real time, from the factory floor to the shelf. With one trusted view, prevent overstocking and stockouts.
- B2B and D2C fulfillment: Effortlessly integrate business and consumer orders with easy wave planning, intelligent task clustering, and route optimization.
- Ready to automate: Easily integrate with warehouse automation solutions, such as pick-to-light, sorters, and conveyors, to speed up operations and minimize manual handling. Easily automate tasks and streamline processes.
- Rapidly deploy, easily scale: Ideal for 3PLs and expanding businesses. Onboard new customers in a matter of hours, and manage multiple facilities from one platform.
With Oracle WMS, you can leap years ahead with an optimized operations system that eliminates cost, increases speed, and achieves remarkable customer satisfaction.
3. SAP extended warehouse management (EWM)
The core of the problem lies in the fact that when supply chains are lengthy and the demand for products is close to saturation, storage capacity alone is insufficient. Companies require smarter operations capable of growth, automation, and compatibility with the surrounding logistics and production environment. That is precisely where SAP Extended Warehouse Management (EWM) is meant to operate.
The SAP EWM system implements the service dedicated to automated and fast-moving warehouses, offers a wide variety of stock control and tracking, and is fully integrated with other SAP modules such as production planning, transportation management, and quality control. It becomes particularly important for industries requiring accuracy, versatility, and synchronization in material and information flow across the supply chain.
Why choose SAP EWM?
- High-volume fulfillment: Friendly integrated resource and task management to help effectively deal with complex processes and large stocks.
- Full operational transparency: They should mainly be able to monitor stocks on a real-time basis, the flow of work, and identify potential problem areas.
- Integrated with production & quality: Connect different types of work orders of the warehouse directly to the production flow and quality control.
- Smarter space utilization: Techniques such as advanced slotting to help reduce the space and help in minimizing the picking time and the associated labor costs.
- Automation-ready platform: Automate the conveyors, sorters, and robotics systems for resolving issues entailing greater operational speed.
- Cloud-based agility: Succeed workloads on the cloud to provide antifragility, elasticity, and continuous improvement in dynamic markets.
SAP EWM integrates your warehouse into the bigger picture of your overall supply chain, enabling an efficient and optimal utilisation of your warehouse.
4. Manhattan active® warehouse management
When everything is connected and at this pace, the speed of fulfillment and flexibility hold the key. Manhattan Active® Warehouse Management is a modern WMS provided as a fully connected cloud service, ensuring that you always have the most up-to-date WMS capabilities to drive increased warehouse visibility and efficiency.
Designed for speed, Manhattan’s WMS consolidates supply chain processes such as labor management, slotting, and automation. It is created with Machine learning, Real-time orchestration, and an easy-to-use interface, and it is flexibly scalable to match your operation as you go through the retail, wholesale, or even direct-to-consumer shipping model.
Why choose manhattan active WMS?
- Unified operations: By providing fulfillment, labor, automation, and slotting all in the app that has close integration with your entire distribution network.
- Smart fulfillment, smarter planning: It continuously adjusts to changes in workers’ availability, equipment non-availability, and order volumes via integrated order streaming and execution-based planning.
- Automation-first design: Seamless incorporation of robotics and automation, ranging from conveyance to more complex equipment like robotic arms and the like, to act in parallel to humans.
- Digital twins & real-time views: They apply a twin vision to every warehouse movement and every task, asset, and worker to make quick and empowered decisions.
- Flexible picking & slotting: Select the proper type of picking method—batch, individual order, wave, or wave-less, and select slotting in the course of daily operation.
- Engaged user experience: Access clean design, clear interfaces, streamlined new user onboarding, and ease-of-use across both web and Android/desktop environments.
Manhattan Active WMS reimagines the warehouse as a connected ecosystem for supply chain operations that flexes to your business’s needs and evolves as the market does.
5. Blue yonder warehouse management
In the ever-evolving supply chain environment, businesses are pressured with growing demands for speed, accuracy, and adaptability. Blue Yonder’s Warehouse Management System (WMS) is solving these problems with a range of AI-based solutions that foster increased efficiency while making the warehouse operations transparent and under the tight control of all involved.
Why choose blue yonder WMS?
- Holistic warehouse optimization: Blue Yonder WMS supports a digital environment with maximum optimization of every operational step, accuracy, efficiency, compliance, and desired levels of customer service.
- Unified yard and warehouse performance: By combining yard and warehouse operations, businesses can improve accuracy, visibility, and insights, which result in more efficient facility operations, lower detention fees, and accelerated throughput.
- AI-driven task management: The system uses AI to dynamically calculate the most critical work to be carried out, which increases the overall productivity of the warehouse while ensuring that important key operations are done at the appropriate time.
- Rapid robotics integration: Blue Yonder’s Robotics Hub enables any robotics vendor or warehouse automation solution to easily interact on a single platform, thus speeding up the ROI process and minimizing implementation costs with no vendor lock-in.
- Enhanced labor productivity and engagement: The Labor Management System offers an in-depth understanding to strengthen employee engagement and employee performance by offering a systematic definition of best practices and identification of opportunities to improve the same.
- Real-time inventory visibility: Blue Yonder WMS provides end-to-end visibility through effective inventory management from the supplier to the user, traceability of products at all times without the use of paper and manual processes.
- Seamless omnichannel support:The system allows for multiple pick methods to minimize time taken travelling and increase efficiency in the system with much improved integration with other systems like TMS, Labor Management System, e-commerce platforms, and others.
- Scalable and configurable user experience: Blue Yonder WMS makes both the user experience and the configuration of the system intuitive rather than convoluted; thereby increasing the flexibility and responsiveness in real-time, prescriptive, and mobile workflows to handle complex warehouse operations.
Blue Yonder WMS enables businesses to change their warehouse procedures to satisfy the dynamics of the supply chain and become efficient, adaptable, and customer-pleasing.
6. Infios warehouse management system
In the continuously changing environment that is the world of supply chain management, adaptability, efficiency, and real-time visibility matter very much. Previously called Körber Supply Chain Software, Infios provides a full complement of Warehouse Management System (WMS) that would meet these requirements.
Leveraging its position as a Leader in the 2025 Gartner® Magic Quadrant™ for Warehouse Management Systems for the seventh year in a row, Infios WMS enables businesses to optimize processes, increase productivity, and future-proof their supply chains with a variety of applications.
Why choose infios WMS?
- Adaptable and scalable solution: Infios WMS is a flexible, mobile-supported solution for the operational management of all processes, inventories, and resources in the warehouse or distribution center. Its flexibility enables businesses to bend the system to their individual business needs, making it scalable as they grow.
- Comprehensive process automation: The system will automate the warehouse processes by sharing near real-time data across yards management, goods received, stock control, material handling, and order fulfillment functions. This automation makes it more efficient, minimizes errors, and speeds up operations.
- Integrated supply chain solutions: Other than warehouse management, we have plenty of integrated solutions: transportation management, order management, and warehouse control systems. From such a holistically based standpoint, the whole supply chain can be operated easily, with better visibility and responsiveness.
- Advanced analytics and AI capabilities: Infios relies on predictive analytics, as well as AI-powered insights for real-time visibility and decision support. On the basis of these capabilities, businesses are able to predict challenges, handle the procedures, and make quick decisions.
- Robust feature set: The WMS covers a broad range of features from barcoding to cross-docking inventory management to kitting up to order-to-pay management to real-time tracking and reporting and analytics to returns management to shipping to yard management. Such functionalities guarantee all-around monitoring of warehouse operations.
- Proven track record: With over 5,000 customers distributed in 70 countries, Infios has proved that it can turn out flexible and innovative technology solutions into a business model that can be adapted to satisfy changing business needs. It is its commitment to turning innovation meaningful and useful to companies that ensures that supply chains become sources of competitive advantage.
Infios WMS is the robust, flexible, and intelligent answer for business owners who wish to improve their warehouse operations and overall supply chain performance. Its wide range of capabilities, its ability to integrate, and its inclusion in the industry’s standards provide compelling reasons why it is a good strategy for organizations to follow trends in a constantly changing marketplace.
7. NetSuite warehouse management system (WMS)
In the high-tempo world of supply chain and logistics, it is vital for warehouses to operate efficiently in order to be able to meet the customers' expectations and maintain a profitable level.
NetSuite’s Warehouse Management System (WMS) provides a complete solution that will help streamline warehouse activities, give better visibility into the stock, and increase order fulfillment accuracy. Owing to the use of industry best practices and mobile technology, NetSuite WMS enables businesses to maximize their warehouse operations and help achieve growth.
Why choose NetSuite WMS?
- Seamless integration with NetSuite ERP: NetSuite WMS is natively integrated with the NetSuite ERP platform, so data synchronizations between different systems are not necessary. This integration offers real-time visibility across the entire workflow of managing inventory and completing orders, as well as the entire manufacturing process, and enables every team to work using the right information, updated.
- Mobile warehouse management: The NetSuite WMS mobile application allows human resources who operate in warehouses to perform daily activities such as receiving, put away, picking, and packing, using mobile devices. The mobility increases efficiency, reduces errors by man, and it as well updates the inventory in real-time to increase overall warehouse productivity.
- Advanced inbound logistics: The receiving processes are made easier by WMS NetSuite through mobile-enabled tools and pre-defined away strategies. Such attributes ensure that when data on receipt is captured, it is captured with efficiency and that items are warehoused in an optimal manner, hence maximizing warehouse space use.
- Optimized order fulfillment: NetSuite WMS allows high volume fulfillment via wave releases by the means of intelligent pick and pack strategies. The system can operate single or multi-order picking, therefore allowing for a faster order to effectively serve the customer.
- Robust bin management: NetSuite WMS provides full bin management capabilities that enable an organization to establish stock locations and have them matched to particular items. This feature enables effective tracking and location of the inventory even without the customary bin setup in a location.
- Smart cycle counting: The Smart Count feature will make automation of inventory cycle counting without the need for a transaction freeze in the warehouse. It tracks inventory levels in real time and notifies users of any variation during the counting process, which will make inventory bookkeeping correct and avoid disruptions to operations.
- Enhanced inventory visibility: Equipped with this real-time ability to track inventory in and out of the warehouse, NetSuite WMS provides full visibility on stock quantity and locations. Such visibility enables the elimination of stockouts or overstocks and makes room for decisions based on knowledge.
- Improved labor productivity: NetSuiteWMS increases labor productivity by directing warehouse staff through activities with the use of mobile devices. The system’s ability to manage tasks makes sure that employees concentrate on high-priority activities and thus minimizing idle time and increasing operational stamina.
NetSuite WMS has stood out as a strong and scalable solution for businesses that want to maximize their warehouse operations. The integration of the application with NetSuite ERP, the potential for usage on mobile devices, and the overall feature set make it attractive to organizations that want to improve the efficiency, accuracy, and customer satisfaction in their supply chains.
8. Infor warehouse management system (WMS)
Infor's Warehouse Management System (WMS) is a cloud-based, AI empowered system purposed at improving the efficiency, accuracy, and scalability of the warehouse operations. Infor WMS utilizes emerging technologies and a user-focused design to allow organizations the capacity to be able to optimize supply chain performance.
Why choose infor WMS?
- AI-Driven operational intelligence: Infor WMS provides artificial intelligence (AI) (like generative AI (GenAI) and machine learning (ML)) to automate routine tasks; reduce error rate; and provide predictive insights. These are decision-making, streamlined operations, and overall warehouse improvement in efficiency.
- 3D Visualization and real-time monitoring: The system provides state-of-the-art 3D visualization tools to get a broad view of warehouse operations. This feature enables the real-time monitoring of inventory, equipment, and labor activities, hence providing proactive operation management and quick reaction to operational problems.
- Integrated labor management: Labor management capabilities within WMS are in-built functionalities that help reduce worker time wastage. Features like voice processing and task automation direct employees through their task flow efficiently, hence increasing engagement and time saving on training.
- Advanced inventory and order management: The ability of the system to support complex plans of inventory control is also there, such as multi-owner, multi-facility inventory control plans, real-time tracking, and rotation rules with configuration. The system also has enhanced order management capabilities, including wave and dynamic replenishment functionalities, which will aid the timely and accurate completion of order fulfillment.
- Seamless automation integration: Infor WMS is a pre-eminent integration technology that seamlessly integrates with various warehouse automation technologies such as robotics, conveyors, and sorters. This integration enhances the effectiveness of the operation, eradicates manual mistakes, and introduces scalability to changes in business needs, respectively.
- Scalable cloud-based architecture: Infor WMS is offered in a cloud –native platform, making it scalable and flexible to change the needs of businesses. High availability and security, as well as the performance of the system architecture, ensure that the organizations can expand without huge infrastructure costs.
Infor WMS is presented as a full solution to companies that want to improve their warehouse procedures. Its capability to provide AI-branded insights with improved visualizations and easy automation integration puts organizations in a good position to address the current problem and future needs.
9. Fishbowl warehouse management system (WMS)
Fishbowl’s WMS provides a suite of integrated solutions designed to consolidate warehouse processes and facilitate improved visibility of inventory while customising its integration with accounting, such as QuickBooks and Xero. Developed specifically for small and medium-sized businesses, Fishbowl WMS offers on-premises and cloud-based solutions to meet various requirements of businesses.
Why choose fishbowl WMS?
- Real-time inventory tracking: Fishbowl WMS offers real-time visibility and control of inventory in all locations. This function will remove manual data entry, it will guarantee accurate inventory keeping, and will help to avoid shortage and overstocked situations
- Multi-location management: Proper tracing and tracking of inventory from multiple warehouses or store locations is easy. Fishbowl’s multi-location management helps businesses keep an eye on stocks, transfers, and fulfillment for orders from several locations, thus increasing operational efficiency.
- Advanced Order Fulfillment: Optimize the process of order processing with the help of pick, pack, and ship processes. Fishbowl WMS helps in streamlining an effective order fulfillment process, such as sales order, transfer order, credit returns, and RMAs, thus delivering goods exactly on time with accuracy.
- Integration with quick books and xero: Fishbowl WMS is 100% compatible with accounting software, including QuickBooks and Xero. Such integration ensures that the update of inventory movement is recorded in the accounting record, and this will provide a proper financial view and will reduce manual data entry.
- Automated purchasing and vendor management: Automate the purchase process through establishing reorder points, fine-tuning the approval process, and overseeing vendor information such as price, lead times, and part numbers. These features guarantee the best inventory balance and consumer consumer-friendly procurement process.
- Robust reporting and analytics: Get a hang of warehousing operations, customizable reports, and analytics. Fishbowl WMS is able to give opportunities for monitoring indicators that define the performance of the warehouse, watching inventory trends, and making well-chosen operational decisions that should lead to increased efficiency of the warehouse.
- Flexible deployment options: Select Fishbowl Advanced (on-premises but with hosted capabilities) or Fishbowl Drive (a cloud-hosted application that can be accessed from anywhere). Such flexibility enables firms to choose the most suitable model of deployment for their convenience.
Fishbowl WMS is a high-capacity, workable alternative to consider if a business aims to increase its warehouse functions. It has an extensive array of functionalities that can easily be integrated with ease and easily deployed thus making it a desirable alternative for organizations with supply chain processes that it should be run by efficiency, accuracy, and scalability.
10. Softeon warehouse management system (WMS)
In the contemporary world, as logistics is being changed at breakneck speed, warehouses have become the nerve centers of supply chains. The emergence of an ever-increasing level of automation, robots, kitting value-added services, and labor volatility makes a sophisticated but pragmatic warehouse management system (WMS) an absolute necessity.
Softeon is a leading Tier 1 WMS provider that exclusively focuses on the optimization of warehouse operations and provides tailored solutions that enhance the efficiency, inventory management levels, and fulfillment of a business.
Why choose softeon WMS?
- Tailored precision with micro-tuning: Softeon’s WMS provides “micro-tuning” and enables clients to design personalized workflows tailored precisely to business needs. This customization guarantees that operations are maximized for optimal efficiency instead of confining businesses into a “one size fits all solution”.
- Integrated warehouse execution system (WES): The integrated WES serves as the warehouse’s central nervous system in that it pinpoints bottlenecks and maximises production everywhere in the warehouse. Its rules-based engine makes for effective order routing and responsiveness to changing demand patterns on the fly.
- Comprehensive labor and yard management: Softeon’s Labor Management tools make the workforce a well-organized team by tracking, measuring, and optimizing labor productivity. Furthermore, the Yard Management solution also offers full visibility into trailers and containers in the shipping yard and, thus, effective planning for the schedules and check-in/out processes.
- Advanced parcel management: Realizing that each parcel is a representation of a customer’s experience, Softeon’s embedded and flexible parcel engine arms businesses with tools to delight their customers.
- Seamless integration capabilities: Softeon’s WMS is designed to be implemented in a relatively short time with enterprise software applications, robotics, and material handling equipment. Its intuitive and powerful APIs make it easy to integrate in real-time, meaning that companies spend less time managing integrations and more time making productivity improvements.
- Enhanced user interface and onboarding: Changes made during the Spring 2024 release included a simpler user interface that allows users to get to know the app’s setup more easily, quicker client onboarding processes, and some pre-configured solutions for common warehouse roles.
Softeon’s WMS is unique as a comprehensive, customizable solution useful in optimizing warehouse operations of businesses. Its targeted precision, integration systems, and integration capabilities make it a valuable partner in the modern warehousing complexity maze.
11. Zoho inventory management system
Today, customer expectations are for faster delivery, unimpaired stock updates, and impeccable order accuracy across channels. This can be a great difficulty for a business that grows. Zoho Inventory is developed in a bid to make it easier. It puts smart automation and deep integrations into a lean platform that people will use for its ease of use, which helps businesses punch above their weight. It doesn’t matter if you’re selling from Shopify, Amazon, or your site – Zoho lets you scale without chaos.
Why choose zoho inventory?
- Omnichannel inventory control: Aggregate orders from various platforms such as Shopify, Amazon, eBay, etc. Zoho synchronizes the inventory in all of them in real time so that you never oversell and never miss an opportunity.
- End-to-end order management: Automate order taking from purchase to delivery. Zoho handles backorders, dropshipping, and even serial/batch tracking for proper accuracy and traceability.
- Smart automation with simplicity: Set reorder points, automate workflows, and trigger emails or stock transfer without pressing a button. Zoho makes complexity simple.
- Shipping simplified: Sign up with big carriers including FedEx, UPS, and DHL. Print the labels, track the packages, and keep customers posted, as it is all in one place.
- Great for growing teams: User-friendly, comes on board quickly, and is effective. With Zoho’s easy-to-use interface, if you are solo or on the upswing of creating a team, the learning curve is reduced.
- Integrated with zoho ecosystem: For a smooth business suite, use Zoho Books, Zoho CRM, and so forth. All your operations, your sales, and your finance speak the same language.
Using Zoho Inventory, you aren’t just shelving products, you’re creating a smart, scalable system that expands with a business.
12. Odoo inventory management system (WMS)
Modern warehouses need agility and real-time intelligence. Odoo Inventory provides you with both, but without the need for a patchwork of plugins/third-party tools. It’s an all-encompassing, seamless solution to managing your warehouse that will grow with your business. Whether you are a manufacturer, a retailer, or one of the multi-warehouse distributors, Odoo makes you lean, accurate, and fast.
Why choose odoo inventory?
- Real-time stock visibility: Track all the products at different warehouses and locations. Trace exactly everything available, everything moving, and everything idle, all in real time.
- Smart automation & replenishment: Automate procurement using min-max rules or demand forecasts. Set triggers so that you reorder before you ever run out.
- Barcode & RFID ready: Speed operations up with barcode scanning for receipts, picking, and the audit of inventory. The mobile-friendly interface makes it very easy for the floor staff to access.
- Multi-warehouse, multi-location: Fill global warehouses or local bins on time. Transfers, movements, and fulfillment are managed with accuracy.
- Integrated with Everything: Odoo Inventory syncs directly with Odoo Sales, Purchase, Accounting, and Manufacturing. No data silos—just seamless operations.
- Flexible routing and fulfillment logic: Choose FIFO, LIFO, drop-shipping, cross-docking, or custom routes. It’s up to you to make products move—Odoo ensures this happens.
- Powerful analytics, simple dashboards: See KPIs, such as turnover, lead time, and stock aging. Make data-led decisions without having to go through spreadsheets.
Odoo makes warehousing a strategic advantage—speedier, more accurate than ever before, and set for the future.
Categorized warehouse management systems (WMS)
Not all WMS are the same – and that’s a good thing. If you’re a scrappy startup with an expanding garage operation or a giant that ships millions of SKUs around the world, the right system is a powerful accelerant to your supply chain. This is the way to figure out the landscape:
1. By business size
- Small businesses: You’re dealing with tight margins, small teams, and fast order turnarounds. You need automation that doesn’t overwhelm your operations.
- Zoho inventory: Easy to deploy, portable, with minimal system dependencies, and easy to integrate with eCommerce platforms. For small businesses growing from spreadsheets to smart systems.
- Fishbowl: Brings manufacturing and inventory under a single roof. Excellent for small makers or distributors searching for barcoding, part tracking, and QuickBooks integration.
- Mid-sized businesses: You’re operating across multiple channels, warehouse space, and supplier coordination – now it’s time to level up.
- NetSuite WMS: Ideal for companies that use NetSuite ERP. Offers real-time tracking, mobile picking, and inventory optimization.
- Epicor WMS: Tailored for manufacturers. Production-linked warehousing and compliance are strong.
- Fynd platform: Retailers love its all-in-one model. Connect inventory, POS, and online marketplaces without complications.
- Enterprise level: multiple warehouses: Millions of SKUs. Dozens of carriers. You need intelligence, automation, and you need to see the world.
- SAP extended warehouse management (EWM): Depth of ERP integration, robotics support, real-time visibility. Designed for highly regulated industries.
- Blue yonder WMS: AI-led forecasts and influential control tower views. Trusted by Walmart.
- Oracle WMS cloud: The player is modular, scalable, and packed with analytics — all enterprise-class control from anywhere.
2. By industry use case
Retail
NetSuite, Fynd, zara’s in-house WMS
Retail thrives on agility. These systems ensure demand-based replenishment and store-pick with integration and analytics to ensure that one is never overstocked while always touching on trend.
E-Commerce
ShipHero, Logiwa
Built for high-velocity, direct-to-consumer models. You can expect batch picking, Shopify integration, and lightning-fast fulfillment.
Manufacturing
Epicor, infor WMS
The coordinates of factory floors require synchronized inventory and production workflow. These systems keep track of raw materials, automate component picking, and feed real-time data to the ERP.
Third-party logistics (3PL)
Körber, Softeon
Juggling multiple clients and SKUs? These are made for you. Expect billing automation, temperature control, and a customer portal.
Real-world case studies
1. Amazon – warehouse precision with robotics
Amazon's warehouses are the gold standard for warehouse innovation. With more than 750,000 mobile robots assisting human workers, Amazon makes use of its own proprietary WMS coupled with robotic picking technology, route optimization based on artificial intelligence, and real-time tracking of inventory.
Its system computes the shortest picking routes automatically, allocates work to employees according to proximity, and even foresees delays before they occur.
The outcome? Many orders are processed and ready for shipping within 30 minutes, and shipping windows have shortened from days to hours. In addition to diminishing labor dependency, this automation also increased Amazon's ability to store millions of SKUs in worldwide warehouses.
2. Walmart – inventory intelligence at scale
Walmart employs a tightly integrated WMS with its RFID tracking system that provides real-time visibility into inventory across thousands of stores and warehouses.
This program, during rush seasons, distributes inventory automatically in high-demand areas. Walmart also employs predictive analytics to plan for stockouts and signal restocking, sometimes before there's even anything left on a shelf.
Its WMS connectivity with ERP, as well as to supplier portals, resulted in a 30% better inventory accuracy while helping reduce shrinkage losses by tens of millions annually. The smooth integration between store and warehouse makes it possible for customers to order online and pick up in-store in hours.
3. Zara (Inditex) – smart warehousing for speed to shelf.
Through a WMS with support for inventory liquidity, fashion retailer Zara keeps its competitive advantage. New designs in under three weeks move from concept to shelf. Their warehouses use a centralized system that follows each item from supplier to shelf with few overstocks.
Their WMS is linked with data from store POS, hence reacting instantly to changing fashion trends. This arrangement allows Zara to ship its newly made garments to 2,000 + outlets around the world, normally within 48 hours, making staple inventory fresh and lessening markdowns.
Integration capabilities of modern WMS
Modern Warehouse Management Systems are designed to be easy to integrate with various platforms to enhance production.
- ERP systems: It integrates seamlessly with ERP platforms like SAP & NetSuite, therefore, providing unified data and easy steps for doing business.
- Transportation management systems (TMS): Connecting with TMS will lead to optimum routes, real-time tracking, and good freight management.
- E-commerce platforms: Ability to integrate and synchronize with Shopify and WooCommerce, automating order management, with synchronized inventory and a better customer experience.
Benefits:
- Unified data: When the information housed in systems is centralized, then discrepancies are mitigated and decision-making is improved.
- Reduced manual errors: Automation reduces human errors in the process of data entry and order processing.
- Better forecasting: Real-time information makes it possible to accurately forecast demand and plan one’s inventory.
How should one choose the best WMS? A step-by-step guide
Step 1: Assess your business needs
Start by examining your current warehouse operations. List out places of pain, from inventory inaccuracies to order lateness. Know your industry's specific demands and customer expectations. This valuation will steer you towards a WMS that will cater to your particular issues.
Step 2: Define budget and ROI expectations
It is important to have a defined budget for your Investment in WMS. Do not forget the long-term costs of maintenance and training for installation. Decide on the return on the investment based on the projected increase in efficiency, accuracy, and customer satisfaction.
Step 3: Evaluate scalability and flexibility
Choose a WMS that will grow with more business. Ensure that it can support future increases in transaction volumes, warehouses, and operational complexities. Degrees of flexibility in customization and integration with other systems are critical for long-term adaptability.
Step 4: Consider integration capabilities
Make sure that the WMS can interconnect with your current ERP, TMS, and e-commerce software. This integration supports real-time data sharing, reduced manual data warehousing, and improved operational efficiency.
Step 5: Prioritize user experience and support
Choose a WMS that has an intuitive user interface to minimize time for the same and reduce errors. Also, evaluate the vendor’s customer support services, including availability, responsiveness, as well as the quality of support offered.
Why is the correct WMS important?
The proper choice of the Warehouse Management System is crucial for optimizing warehouse functioning, reducing costs, and improving customer satisfaction.
A properly implemented WMS increases inventory accuracy, speeds the processing of orders, and generates vital analytics. On the other hand, an ill-fitted system results in inefficiencies, more mistakes, and can limit growth.
Trends of the future warehouse management system
- Artificial intelligence and machine learning: Applying AI for predictive analysis enables better demand forecasting and stock optimization.
- Robotics and automation: The robotic integration into picking and packing processes automates them, making them simpler, more efficient, and cheaper.
- Internet of things (IoT): IoT devices offer real-time tracking of assets and the environment, which improves visibility and control.
- Cloud-based deployments: Scalable, accessible online, and low IT infrastructural solutions are offered in cloud-first WMS solutions.
- Micro-fulfillment centers: A switch to distributed warehouses closer to the urban centers in the process of delivery reduces the time it takes for them to get the shipments, and the change initiates changes in the consumers’ expectations as they get accustomed to prompt delivery.
Selecting the right Warehousing Management System is a strategic move whose effect on the efficiency of your supply chain and customer satisfaction is high. With knowledge of what your business needs, identification of integration capabilities, and knowledge of what is to come, you can select a WMS that will fulfill your current needs and position your business for success.
Frequently asked questions
Proper WMS reliance upon business size, industry, and operational characteristics. Solutions such as Zoho Inventory might help small businesses, while EWM systems like SAP may become necessary for big enterprise companies.
There are four kinds of WMS – standalone systems, which are not integrated into other business systems; ERP modules, able to integrate with other business applications and systems; cloud-based systems, store data off site and can also be used anywhere in the world; supply chain modules, the most complex, having information about various business departments.
The standard warehouse software includes WMS solutions such as NetSuite WMS, Fynd WMS, and Fishbowl Inventory that take care of the inventory, order processing, and logistics.
Where SCM covers the end-to-end supply chain process, starting from procurement, production, to distribution, WMS is focused only on Warehouse operations and inventory management.
Popular WMS solutions differ depending on the industry and the size of the business. However, industry and business-size preferred solutions are SAP EWM, Oracle WMS, and NetSuite WMS, as they both offer a wide range of features and scalability.
It is best to use a WMS to optimize warehouse operations, as these will improve inventory accuracy, automate order fulfillment, and decrease operational costs while improving overall supply chain efficiency.