Complete Guide to Warehouse Barcode Systems
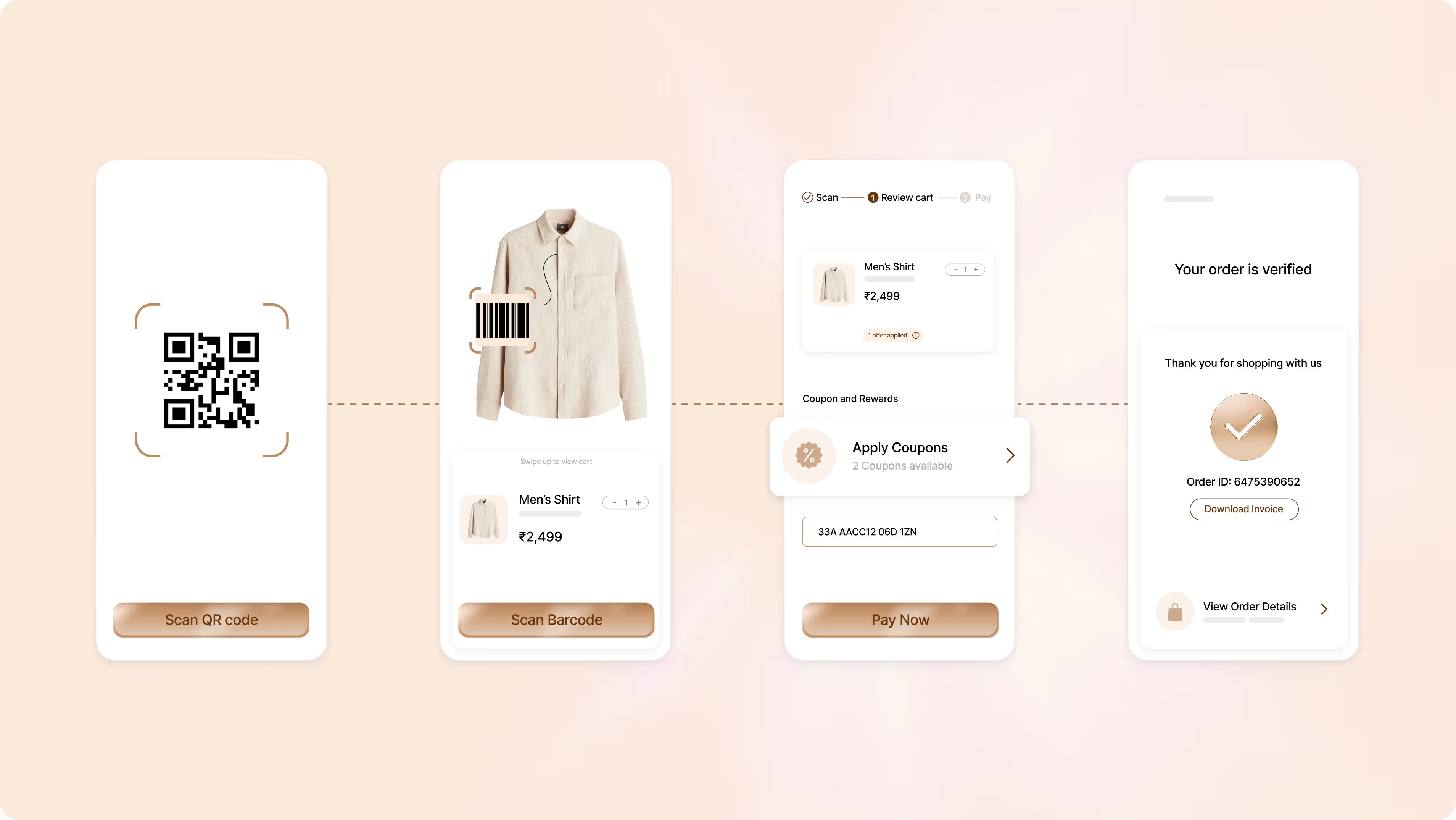
Implementing a barcode system in your warehouse can significantly enhance operational efficiency and accuracy. To begin, assess your current inventory management processes and identify areas where barcoding can streamline operations. When choosing the appropriate barcode technology, consider factors such as the type of products you handle, the size of your warehouse, and your budget. For instance, 1D barcodes are suitable for simple product identification, while 2D barcodes can store more information, making them ideal for complex inventory systems. Invest in barcode scanners and software that integrate seamlessly with your existing Warehouse Management System (WMS) to ensure smooth data flow and real-time tracking.
Next, train your staff on how to use the barcode system effectively. Proper training is crucial for minimizing errors and ensuring that employees understand the benefits of using barcodes for inventory management. Develop standard operating procedures (SOPs) for scanning items during receiving, picking, packing, and shipping processes. This will help maintain consistency and accuracy throughout your operations.
Finally, continuously monitor and evaluate the performance of your barcode system. Regular audits will help identify any discrepancies in inventory levels and allow for timely adjustments. Additionally, gather feedback from employees to improve processes and address any challenges they may encounter. By following these steps, you can successfully implement a barcode system that enhances efficiency, reduces errors, and ultimately improves customer satisfaction in your warehouse operations.
Why Use Barcodes in a Warehouse?
Using barcodes in a warehouse improves inventory management and efficiency. With real-time tracking, businesses can monitor stock levels accurately and make smart restocking decisions. This helps avoid stockouts or overstock situations by identifying trends in product movement and adjusting inventory accordingly.
Barcodes also reduce errors from manual data entry, cutting mistakes by up to 85%. Automating inventory processes leads to more accurate counts, streamlining operations, and boosting productivity. Employees can focus on important tasks while maintaining reliable and up-to-date inventory records, easing their workload and improving overall efficiency.
{{demo_wms="/styles/components"}}
Understanding the Essentials of Warehouse Barcode Systems
Understanding the essentials of a warehouse barcode system is vital for optimizing inventory management and enhancing operational efficiency. Barcodes streamline various processes, including receiving, storing, picking, packing, and shipping products. By automating data entry and tracking, these systems significantly reduce human error while providing real-time visibility into inventory levels.
As supply chains become increasingly complex, implementing a barcode system can lead to improved accuracy, faster processing times, and heightened customer satisfaction. This technology not only simplifies inventory management but also supports better decision-making and resource allocation. A warehouse barcode system begins with assigning unique barcode labels to each item or storage location.
Benefits of Warehouse Barcoding
Warehouse barcoding provides a range of significant advantages compared to traditional inventory management methods. One of the primary benefits is the ability to track products in real-time, which empowers businesses to monitor stock levels with precision and make informed restocking decisions based on current inventory data.
Furthermore, barcode scanning minimizes the risk of human error associated with manual data entry, a common source of inaccuracies in inventory counts. By automating this process, businesses can ensure more reliable data, which helps prevent stockouts and overstock situations. Ultimately, these improvements lead to enhanced operational efficiency, enabling organizations to respond more effectively to customer demands and optimize their supply chain management.
1. Improved Inventory Visibility
Warehouse barcoding significantly enhances inventory visibility by providing real-time data on product quantities and locations. This transparency allows businesses to monitor stock levels and quickly identify discrepancies, giving you a sense of control and empowerment. With accurate, up-to-date information at their fingertips, managers can make better decisions regarding restocking and inventory turnover, leading to a more organized warehouse environment and reduced likelihood of stockouts or overstock situations.
2. Streamlined Operations
Implementing a barcoding system streamlines warehouse operations by automating key processes such as receiving, picking, and shipping. With barcode scanning, employees can quickly and accurately process inventory movements without the need for extensive manual data entry. This efficiency reduces the time spent on each task, enabling warehouses to handle higher order volumes while maintaining accuracy and improving overall productivity.
3. Enhanced Accuracy
Barcode systems greatly enhance inventory accuracy by reducing human errors associated with manual data entry. When products are scanned rather than manually recorded, the likelihood of mistakes decreases significantly. This increased accuracy ensures that inventory counts are correct, leading to better decision-making regarding stock levels and preventing issues such as stockouts or excess inventory, which can disrupt operations.
4. Cost Savings
The adoption of warehouse barcoding can lead to substantial cost savings for businesses. By minimizing errors, streamlining operations, and enhancing inventory accuracy, companies can reduce labor costs associated with manual inventory management. Additionally, improved accuracy helps prevent costly stockouts or overstocking situations, ultimately leading to more efficient resource allocation and higher profitability in the long run.
5. Better Customer Service
Warehouse barcoding contributes to improved customer service by enabling faster and more accurate order fulfillment. With real-time inventory data and streamlined picking processes, businesses can quickly respond to customer orders, ensuring timely delivery. This reliability not only enhances customer satisfaction but also builds trust and loyalty, ultimately leading to increased sales and long-term business success in a competitive market.
5. Types of Barcodes
In warehouses, 1D barcodes (e.g., UPCs) are used for simple item identification and quick scanning, while 2D barcodes (e.g., QR codes) store more data, including batch numbers, expiration dates, and location info. Choosing the right barcode type is key to improving inventory accuracy and streamlining operations, ensuring efficient management in a fast-paced environment.
6. Implementing a Barcode System
To successfully implement a barcode system in your warehouse, begin by assessing your current processes and identifying areas for improvement. Choose appropriate barcode technology and scanners that integrate with your existing Warehouse Management System (WMS). Training staff on proper scanning techniques and developing standard operating procedures (SOPs) will ensure smooth adoption. Continuous monitoring and adjustments will further enhance the effectiveness of the system.
7. Integrating with Warehouse Management Systems
Integrating barcoding with your Warehouse Management System (WMS) can significantly streamline operations. This integration allows for seamless data transfer between systems, minimizing manual entry errors and improving overall productivity. By ensuring that inventory levels are updated in real-time, businesses can make informed decisions regarding stock management and order fulfillment. This cohesive approach enhances operational efficiency and reduces labor costs.
8. Best Practices for Maintenance
Maintaining a warehouse barcode system requires regular audits and updates to ensure optimal performance. Establishing best practices, such as routine checks on barcode scanners and software updates, will help prevent potential issues. Additionally, providing ongoing training for staff will keep them informed about any changes in procedures or technology. By prioritizing maintenance, businesses can sustain the benefits of their barcode systems long-term while adapting to evolving inventory needs.
Benefits of Warehouse Barcode Systems
Implementing a warehouse barcode system provides a multitude of benefits that greatly enhance inventory management and operational efficiency. By automating data entry and tracking, barcodes facilitate various processes, including receiving, storing, picking, packing, and shipping products.
This technology significantly reduces human error, leading to improved accuracy in inventory records and minimizing discrepancies. Furthermore, barcodes offer real-time visibility into inventory levels, allowing businesses to respond quickly to changing demands. As supply chains become increasingly complex, adopting a barcode system is essential for organizations seeking to streamline their operations, reduce costs, and ultimately enhance customer satisfaction through timely and accurate order fulfillment.
- Real-Time Tracking: Real-time tracking allows businesses to monitor inventory levels continuously, enabling informed decisions about restocking.
- Reduced Errors: Barcode scanning minimizes human error by eliminating manual data entry.
- Improved Efficiency: Employees can quickly locate and scan items, significantly speeding up warehouse processes.
- Enhanced Inventory Accuracy: Implementing a barcode system boosts inventory accuracy by ensuring precise tracking of items throughout the warehouse.
- Increased Customer Satisfaction: By streamlining order fulfillment processes, a barcode system ensures timely and accurate deliveries.
Step By Step Guide On How to Implement Barcodes in Your Warehouse
Implementing a barcode system in your warehouse can significantly improve inventory management and operational efficiency. This step-by-step guide outlines the essential phases of integrating barcodes into your warehouse processes. By automating data entry and tracking, barcodes streamline various operations, such as receiving, storing, picking, packing, and shipping products.
This not only reduces human error but also enhances accuracy and provides real-time visibility into inventory levels. As supply chains become increasingly complex, adopting a barcode system is crucial for businesses aiming to optimize their operations and improve customer satisfaction. Follow these steps to ensure a smooth implementation process that maximizes the benefits of barcoding in your warehouse.
Step 1: Assess Current Processes
Begin by evaluating your existing inventory management processes to identify areas that could benefit from barcoding. Analyze workflows, pinpoint inefficiencies, and determine which tasks would be improved through automation. Engaging with staff can provide insights into the daily challenges they face. This assessment will help you establish clear objectives for the barcode system, ensuring it aligns with your warehouse's specific needs.
Step 2: Choose Barcode Technology
Select the appropriate barcode technology based on your warehouse requirements. Consider factors such as the types of products you handle, the environment (e.g., temperature or humidity), and scanning distance. Options include 1D barcodes for simple item identification or 2D barcodes for storing more information. Ensure that the chosen technology integrates well with your existing Warehouse Management System (WMS) for seamless data flow.
Step 3: Train Your Staff
Effective training is crucial for successful implementation. Organize training sessions to familiarize staff with the new barcode system, including how to use scanners and interpret data. Develop standard operating procedures (SOPs) that outline best practices for scanning items during receiving, picking, packing, and shipping processes. Continuous support and refresher training will help maintain proficiency and confidence among employees.
Step 4: Implement Barcode Labels
Once the staff is trained, begin labeling items with unique barcodes. Ensure each product or storage location has a printed barcode label that adheres securely to the item. Use a consistent labeling format to facilitate easy scanning and recognition. This step is essential for establishing an organized inventory system that allows for efficient tracking and management of products throughout the warehouse.
Step 5: Monitor and Evaluate
After implementation, continuously monitor the performance of your barcode system. Conduct regular audits to ensure inventory accuracy and identify any discrepancies in stock levels. Gather feedback from employees regarding their experiences with the new system to identify areas for improvement. Regular evaluations will help you adapt and optimize the barcode system over time, maximizing its effectiveness in enhancing warehouse operations.
Challenges to Implement Barcodes in Your Warehouse
Implementing a barcode system in your warehouse can greatly enhance operational efficiency, but it also comes with its own set of challenges. Understanding these challenges is crucial for successful implementation and long-term effectiveness.
Common issues include the need for proper training, potential integration difficulties with existing systems, and environmental factors that can affect barcode readability. Additionally, managing barcode quality and ensuring consistent labeling practices are essential to avoid operational disruptions. By recognizing these challenges upfront, businesses can develop strategies to mitigate them, ensuring a smoother transition to a more efficient inventory management system.
- Training Requirements: Employees may require extensive training to effectively use the new barcode system. Inadequate training can lead to errors and inefficiencies during implementation.
- Integration Issues: Integrating barcode systems with existing Warehouse Management Systems (WMS) can be complex.
- Environmental Factors: Harsh warehouse environments can degrade barcode labels due to moisture, heat, or abrasion.
- Barcode Quality Control: Maintaining high-quality barcodes is essential for accurate scanning. Resistance to Change: Employees may resist adopting new technology due to comfort with existing processes.
Conclusion
Using a barcode system in your warehouse can greatly improve how you manage inventory and make operations more efficient. However, it's important to deal with challenges like training staff, making sure the system works well with existing technology, and managing barcode quality. You might also face resistance from employees who are not used to the new system. By planning and addressing these issues, you can make the transition smoother. In the end, a barcode system will help reduce mistakes, improve accuracy, and increase customer satisfaction, helping your warehouse succeed in the long run.
Frequently asked questions
A warehouse barcode system uses barcode technology to automate inventory management, enabling efficient tracking of products throughout the warehouse, reducing errors, and improving operational efficiency.
What types of barcodes are commonly used?
Barcodes enhance inventory accuracy by automating data entry, minimizing human errors associated with manual tracking, and providing real-time visibility into stock levels and locations within the warehouse.
. What equipment is needed for a barcode system?
Commonly used barcodes include 1D barcodes (like UPCs) for simple item identification and 2D barcodes (such as QR codes) for storing more complex information about products.
Essential equipment for a barcode system includes barcode scanners, printers for creating labels, and software that integrates with your Warehouse Management System (WMS) for effective inventory management.
Successful implementation involves assessing current processes, selecting appropriate technology, training staff effectively, maintaining high-quality labels, and continuously monitoring performance to make necessary adjustments.
Challenges include training requirements for staff, integration issues with existing systems, environmental factors affecting barcode readability, maintaining label quality, and potential resistance to change among employees.