What is TMS and WMS: Integration and Benefits
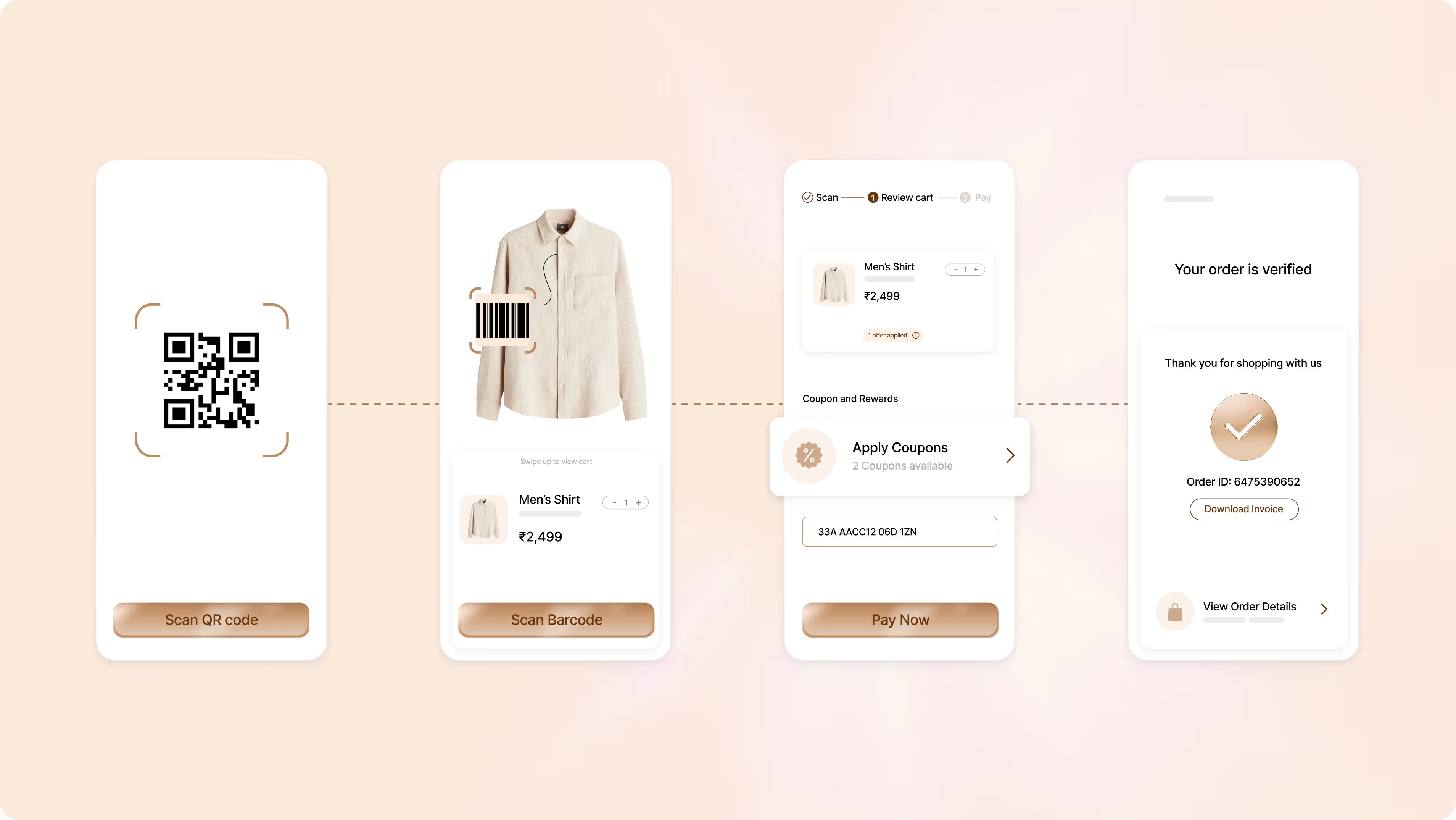
Warehouse and Transportation Management Systems (WMS and TMS) are vital for businesses aiming to streamline operations. A Warehouse Management System (WMS) focuses on optimizing inventory storage, order fulfillment, and stock accuracy. In contrast, a Transportation Management System (TMS) manages the planning, execution, and optimization of product transportation. Integrating both systems allows seamless coordination between warehousing and logistics, reducing delays and improving accuracy.
A WMS can increase inventory accuracy by up to 99% and reduce warehouse labor costs by 30%. Meanwhile, a TMS can lower transportation costs by 8%–12%. Together, these systems enhance supply chain visibility, enabling real-time tracking and better decision-making. This integration ensures that warehouses are aligned with transportation schedules, improving on-time deliveries and reducing inventory holding costs.
For businesses looking to scale, integrating WMS and TMS offers significant efficiency and cost savings. Fynd WMS supports this integration, helping companies achieve faster delivery times and better warehouse organization. This blog will solve the problem of inefficient logistics and inventory management by offering insights into how WMS and TMS can work together to boost productivity. Implementing these solutions can lead to improved customer satisfaction, reduced operational costs, and higher overall profitability.
What is a Transportation Management System (TMS)?
A Transportation Management System (TMS) is a software solution designed to help businesses manage, plan, and optimize the transportation of goods. It streamlines the entire shipping process, from selecting carriers to tracking deliveries, ensuring efficient and cost-effective transportation operations.
A TMS also integrates with other supply chain systems, providing real-time data and improved visibility across all shipping activities. This tool is essential for businesses looking to reduce transportation costs, improve delivery times, ensure compliance with regulations, and enhance overall customer satisfaction.
- Route Optimization: Find the most efficient delivery routes.
- Carrier Selection: Pick the best shipping providers for each order.
- Tracking and Visibility: Monitors shipments in real time.
- Cost Control: Reduces shipping costs with automation.
- Compliance Management: Ensures all transport regulations are followed.
{{demo_wms="/styles/components"}}
What is a Warehouse Management System (WMS)?
A Warehouse Management System (WMS) is software that helps businesses efficiently manage and control their daily warehouse operations. It streamlines the entire process, from receiving and storing goods to picking, packing, and shipping orders.
By optimizing the flow of products within the warehouse, a WMS improves accuracy and efficiency, allowing companies to better manage their inventory, reduce operational costs, and minimize errors in order fulfillment. This system is crucial for businesses aiming to enhance productivity, improve customer satisfaction, and scale their operations effectively.
- Inventory Control: Tracks stock levels and locations in real time.
- Order Fulfillment: Streamlines the picking, packing, and shipping process.
- Space Optimization: Utilizes warehouse space efficiently to maximize storage.
- Labor Management: Assigns tasks to workers for improved productivity.
- Reporting and Analytics: Provides data to improve decision-making and warehouse performance.
Core Features Of A Transportation Management System (TMS)
A Transportation Management System (TMS) is an essential tool for businesses aiming to streamline their logistics and transportation operations. This software automates the processes involved in managing, planning, and optimizing shipments while providing valuable insights into cost, performance, and efficiency.
With features like real-time visibility, route optimization, and carrier selection, a TMS not only helps improve delivery times and reduce transportation costs but also ensures compliance with industry regulations. By enhancing overall operational efficiency, it empowers businesses to make data-driven decisions that boost customer satisfaction and profitability.
1. Route Optimization
Route optimization helps businesses determine the most efficient delivery paths, significantly reducing fuel consumption and delivery times. This feature takes into account various factors, including traffic patterns, weather conditions, and distances, to identify the fastest and most cost-effective routes. By streamlining transportation logistics, route optimization leads to substantial savings and enhanced delivery performance, ultimately improving customer satisfaction and operational efficiency.
2. Carrier Selection
Carrier selection in a TMS allows businesses to evaluate and compare various shipping providers based on cost, speed, and reliability. This feature provides access to a range of carrier rates and services, enabling companies to make informed decisions that enhance their transportation network's efficiency. By selecting the most suitable carrier, businesses can significantly reduce overall shipping costs while ensuring timely deliveries and maintaining high service standards.
3. Real-Time Tracking
Real-time tracking empowers businesses to monitor shipment statuses throughout the entire delivery process. This feature offers complete visibility, allowing companies to provide customers with accurate updates on their orders and quickly identify any potential delays. By enhancing transparency, real-time tracking helps improve customer satisfaction and fosters proactive problem-solving, ensuring that businesses can address issues before they escalate and maintain a smooth logistics operation.
4. Freight Auditing
Freight auditing automates the verification of shipping charges, ensuring they align with pre-established rates and services. This feature reviews invoices for discrepancies, preventing overcharges and inaccuracies in billing. By streamlining the auditing process, businesses can reduce errors, save time, and ensure accurate shipping costs. Ultimately, freight auditing leads to better financial management and improved operational efficiency within the logistics process.
5. Compliance Management
Compliance management within a TMS helps businesses adhere to industry regulations by automating necessary documentation for customs, taxes, and safety standards. This feature simplifies the complexities associated with regulatory compliance, minimizing the risk of fines, delays, or legal issues. By ensuring that all shipments meet the required guidelines, businesses can maintain smooth operations and build trust with customers and partners alike.
6. Load Optimization
Load optimization maximizes the efficiency of cargo space during transportation by determining the best way to pack shipments. This feature calculates how to consolidate orders into fewer vehicles or containers, minimizing the number of trips required. By optimizing loads, businesses can significantly reduce transportation costs, lower emissions, and improve overall delivery efficiency, all while maximizing their resource utilization.
7. Performance Analytics
Performance analytics provides businesses with insights into their transportation operations by tracking key performance indicators (KPIs) such as delivery times, costs, and carrier performance. This feature allows companies to analyze historical data, identify trends, and pinpoint areas for improvement. By leveraging these insights, businesses can make data-driven decisions to enhance efficiency, reduce costs, and improve service levels across their logistics network.
8. Freight Management
Freight management simplifies the complexities of managing shipments from origin to destination. This feature allows businesses to handle all aspects of freight, including pricing, carrier selection, and scheduling. By automating these processes, companies can reduce manual errors, ensure timely deliveries, and enhance their overall logistics performance. A well-managed freight system contributes to smoother operations and improved customer satisfaction.
9. Integration Capabilities
A robust TMS offers integration capabilities with other supply chain systems, such as Warehouse Management Systems (WMS) and Enterprise Resource Planning (ERP) software. This feature enables seamless data exchange, providing a comprehensive view of the entire logistics process. By integrating systems, businesses can enhance operational efficiency, improve communication, and ensure that all departments work collaboratively toward common goals.
10. Customer Portal
A customer portal feature allows clients to access shipment information, track deliveries, and manage orders online. This self-service capability improves customer engagement by providing real-time updates and transparency in the shipping process. By empowering customers with easy access to information, businesses can enhance satisfaction, build trust, and reduce the volume of inquiries to customer service, leading to more efficient operations.
Core Features of a Warehouse Management System
A Warehouse Management System (WMS) is essential for businesses seeking to optimize their warehouse operations and improve inventory management. This software solution enables companies to manage and control the movement of goods efficiently, from receiving to storage and shipping.
By automating processes, improving accuracy, and enhancing visibility throughout the supply chain, a WMS helps organizations reduce operational costs, minimize errors, and increase overall productivity. With its robust features, a WMS is vital for achieving effective warehouse management and delivering exceptional customer service.
1. Inventory Management
Inventory management is a core feature of WMS that allows businesses to track stock levels, locations, and movements in real-time. This functionality ensures accurate inventory counts, reduces the risk of stockouts or overstock situations, and enables effective replenishment strategies. By maintaining optimal inventory levels, companies can enhance order fulfillment efficiency and improve customer satisfaction.
2. Order Fulfillment
Order fulfillment streamlines the process of picking, packing, and shipping orders. A WMS automates tasks such as order prioritization and picking routes, allowing workers to complete orders more quickly and accurately. By optimizing order fulfillment, businesses can reduce lead times, enhance productivity, and ensure timely deliveries, ultimately leading to higher customer satisfaction.
3. Real-Time Tracking
Real-time tracking provides visibility into the movement of goods throughout the warehouse. This feature allows businesses to monitor inventory levels, order statuses, and shipment progress at any time. With real-time data, companies can make informed decisions, address potential issues proactively, and keep customers updated on their orders, fostering transparency and trust.
4. Barcode Scanning
Barcode scanning enhances inventory accuracy and efficiency by automating data entry processes. Workers can use handheld devices or mobile scanners to quickly capture information related to stock movements, shipments, and orders. By minimizing manual data entry errors and speeding up operations, barcode scanning contributes to better inventory control and streamlined warehouse processes.
5. Space Utilization
Space utilization features are crucial for helping businesses maximize their warehouse layout and optimize storage capacity. By analyzing storage patterns and recommending optimal placements for products, a Warehouse Management System (WMS) ensures that all available space is utilized effectively. This capability leads to improved organization, allowing for easier access to items and reducing retrieval times.
6. Labor Management
Labor management tools within a WMS allow businesses to monitor workforce productivity and optimize labor allocation. By tracking employee performance and analyzing workload distribution, companies can ensure that resources are deployed effectively. This feature helps improve labor efficiency, reduce overtime costs, and create a more balanced workload for warehouse staff.
7. Reporting and Analytics
Reporting and analytics features provide valuable insights into warehouse performance and inventory trends, enabling businesses to monitor their operations effectively. A WMS generates comprehensive reports on key performance indicators (KPIs), such as order accuracy, inventory turnover, and labor productivity. By analyzing this data, companies can identify areas for improvement, make informed, data-driven decisions, and enhance overall warehouse efficiency, leading to optimized operations and increased profitability.
8. Automated Replenishment
Automated replenishment ensures that stock levels are maintained optimally by triggering reordering based on predefined thresholds. This feature helps prevent stockouts and excess inventory by analyzing sales patterns and forecasting demand. By automating the replenishment process, businesses can maintain inventory balance and enhance order fulfillment efficiency, ultimately improving customer satisfaction.
9. Integrated Shipping Management
Integrated shipping management within a WMS streamlines the process of preparing and dispatching shipments. This feature automates carrier selection, rate comparison, and shipping label generation, ensuring that orders are shipped efficiently and cost-effectively. By simplifying shipping logistics, businesses can enhance delivery performance and reduce shipping costs while improving overall customer service.
10. Quality Control
Quality control features in a WMS help businesses maintain high standards for their products. This functionality enables companies to implement inspection protocols during receiving, storage, and shipping processes. By identifying defects and ensuring that only compliant goods are delivered, businesses can minimize returns, enhance customer satisfaction, and protect their brand reputation through consistent product quality.
How to Do a TMS and WMS System Work
Transportation Management Systems (TMS) and Warehouse Management Systems (WMS) play critical roles in the supply chain, working together to optimize logistics and improve operational efficiency. While TMS focuses on planning, executing, and tracking the movement of goods, WMS manages the storage and inventory within a warehouse.
By integrating these systems, businesses can enhance visibility, streamline operations, and ensure timely deliveries, ultimately leading to improved customer satisfaction. Understanding how TMS and WMS function and collaborate can help organizations maximize their logistics capabilities.
Working of Transportation Management Systems (TMS)
A TMS automates and optimizes transportation logistics by managing the movement of goods from one location to another. It begins with planning routes and selecting carriers based on cost, speed, and service levels. The system then monitors shipments in real-time, providing visibility into delivery statuses. By analyzing performance data, TMS helps businesses make informed decisions, improve delivery times, and reduce transportation costs, ultimately enhancing the efficiency of logistics operations.
Working in Warehouse Management Systems (WMS)
A WMS manages warehouse operations by controlling the flow of goods within a facility. It starts with receiving inventory and assigning storage locations based on predefined rules. The system tracks inventory levels in real-time, enabling efficient picking, packing, and shipping processes. WMS also automates tasks such as replenishment and quality checks, ensuring accurate order fulfillment.
Integration of WMS and TMS
Integrating Warehouse Management Systems (WMS) and Transportation Management Systems (TMS) is crucial for businesses aiming to enhance their supply chain efficiency and streamline logistics operations. When these two systems work together, they create a unified platform that enables seamless data exchange and improved visibility throughout the entire supply chain.
This integration facilitates better decision-making, reduces operational costs, and enhances customer satisfaction by ensuring timely and accurate deliveries. Understanding how WMS and TMS integration functions can significantly benefit organizations looking to optimize their logistics processes.
1. Data Synchronization
Data synchronization between WMS and TMS allows for the real-time sharing of critical information, such as inventory levels, shipment statuses, and order details. This ensures that both systems are working with the most current data, reducing discrepancies and enhancing accuracy. By maintaining up-to-date information, businesses can make more informed decisions, improve order fulfillment, and minimize delays.
2. Improved Visibility
The integration of WMS and TMS enhances visibility across the supply chain by providing a comprehensive view of inventory and transportation activities. Businesses can monitor stock levels, track shipments, and receive alerts about potential issues. Improved visibility allows for proactive problem-solving, enabling organizations to respond quickly to changes in demand or disruptions, thereby maintaining service quality and customer satisfaction.
3. Streamlined Operations
By combining the capabilities of WMS and TMS, organizations can streamline their logistics operations. The integration automates key processes, such as order processing, inventory replenishment, and shipment tracking, resulting in reduced manual work and errors. This streamlined approach improves overall efficiency, allowing businesses to allocate resources more effectively and enhance productivity in both warehouse and transportation functions.
4. Enhanced Customer Service
Integrating WMS and TMS ultimately leads to enhanced customer service by ensuring timely and accurate order fulfillment. With better visibility and real-time data sharing, businesses can provide customers with up-to-date information about their orders, such as estimated delivery times and shipment statuses. This transparency fosters trust and satisfaction, resulting in stronger customer relationships and repeat business.
5. Data Synchronization
Incorporating advanced data synchronization between WMS and TMS enhances the accuracy of inventory management and shipping processes. This feature ensures that inventory counts are consistently updated, reflecting real-time stock levels and reducing the likelihood of stockouts or overstock situations. By aligning data across both systems, businesses can optimize order fulfillment rates and minimize disruptions in the supply chain, leading to improved operational efficiency.
6. Improved Visibility
The integration fosters enhanced visibility not only for internal teams but also for customers and stakeholders. With shared access to shipment tracking and inventory levels, all parties involved can monitor progress and address any potential issues collaboratively. This holistic view encourages transparency, enabling companies to respond to customer inquiries quickly and efficiently. As a result, businesses can boost customer loyalty through superior service.
7. Streamlined Operations
Integrating WMS and TMS facilitates a more cohesive workflow by linking warehouse activities with transportation management. This connection allows for automated order routing, enabling shipments to be processed more quickly and efficiently. By reducing the time spent on manual interventions, organizations can enhance overall throughput. Moreover, streamlined operations enable businesses to adapt to fluctuating demand, ensuring they can maintain high service levels during peak times.
8. Enhanced Customer Service
The integration of WMS and TMS significantly boosts customer service by improving response times to order inquiries and delivery updates. With real-time data available, businesses can proactively inform customers about changes in their orders, such as delays or expected arrival times. This proactive communication builds trust and reliability, enhancing the customer experience. Ultimately, it leads to increased customer retention and positive word-of-mouth referrals.
9. Cost Reduction
Integrating WMS and TMS can lead to significant cost reductions across the supply chain. By automating processes and improving efficiencies, businesses can lower transportation costs through better route planning and reduced freight spend. Additionally, accurate inventory management helps minimize holding costs and reduce waste. The result is a more cost-effective logistics operation, allowing companies to allocate resources more effectively and improve profit margins.
10. Scalability
The integration supports scalability, enabling businesses to adapt to changing market demands or expand into new regions seamlessly. As companies grow, their logistics needs become more complex. A well-integrated WMS and TMS solution can easily accommodate increased order volumes and more sophisticated shipping requirements. This adaptability allows organizations to maintain efficient operations during periods of growth without compromising service quality or customer satisfaction.
Businesses That Use TMS and WMS
Many types of businesses benefit significantly from using Transportation Management Systems (TMS) and Warehouse Management Systems (WMS) to enhance their logistics and supply chain operations. These advanced systems help companies manage their inventory more effectively, streamline shipping processes, and ensure timely deliveries.
From retail to manufacturing, organizations across various industries can improve efficiency, reduce operational costs, and boost customer satisfaction by implementing these solutions. Understanding which businesses use TMS and WMS can provide valuable insights into their growing importance in today's competitive market landscape.
- Retailers: Retailers use TMS and WMS to manage inventory levels and ensure products are delivered on time to stores and customers.
- E-commerce Companies: E-commerce businesses rely on TMS and WMS to enable efficient order processing and real-time tracking of shipments.
- Manufacturers: Manufacturers use TMS and WMS to manage raw materials and finished goods effectively. This ensures a smooth production process.
- Food and Beverage Industry: Companies in this sector utilize TMS and WMS to track perishable items and maintain quality control.
- Third-Party Logistics (3PL) Providers: 3PL companies use these systems to manage logistics for various clients. They help optimize warehousing and transportation.
- Healthcare Providers: Healthcare organizations rely on TMS and WMS to ensure timely deliveries to hospitals and clinics, supporting patient care.
- Automotive Industry: Automotive companies use TMS and WMS to manage parts and components efficiently.
- Pharmaceutical Companies: Pharmaceutical businesses benefit from TMS and WMS by ensuring that medicines are stored and transported correctly.
- Construction Firms: Construction companies use TMS and WMS to manage materials and equipment.
-
By leveraging TMS and WMS, these businesses can streamline their operations, reduce costs, and enhance customer satisfaction.
Conclusion
Integration of Transportation Management Systems (TMS) and Warehouse Management Systems (WMS) is crucial for businesses aiming to optimize their logistics and supply chain operations. By leveraging these systems, companies can enhance data synchronization, improve visibility, streamline operations, and ultimately deliver superior customer service.
As businesses continue to face evolving market demands, embracing these technologies will be essential for driving efficiency, reducing costs, and ensuring long-term success in today's fast-paced environment. With Fynd's innovative solutions, companies can seamlessly integrate TMS and WMS to maximize their operational potential and achieve their business goals.
Frequently asked questions
A TMS is designed to help businesses manage, plan, and optimize their transportation operations. It streamlines processes such as route planning, carrier selection, and real-time tracking to improve efficiency and reduce shipping costs.
A WMS enhances inventory management by providing real-time visibility of stock levels, tracking product movement, and automating order fulfillment processes. This leads to reduced errors, better organization, and improved order accuracy.
Yes, TMS and WMS systems can be integrated to create a cohesive logistics operation. This integration allows for better data synchronization, improved visibility across the supply chain, and enhanced operational efficiency.
Industries such as retail, e-commerce, manufacturing, healthcare, and logistics are among the primary beneficiaries of TMS and WMS. These systems help streamline their supply chain processes, enhance customer service, and reduce operational costs.
By providing accurate tracking information, timely deliveries, and efficient order fulfillment, TMS and WMS enhance the overall customer experience. This leads to increased customer loyalty and positive word-of-mouth referrals.
Fynd offers innovative TMS and WMS solutions designed to help businesses optimize their logistics operations. With Fynd's expertise, companies can seamlessly integrate these systems, improving efficiency and driving growth in their supply chain management.