What is Vehicle Fleet Management?
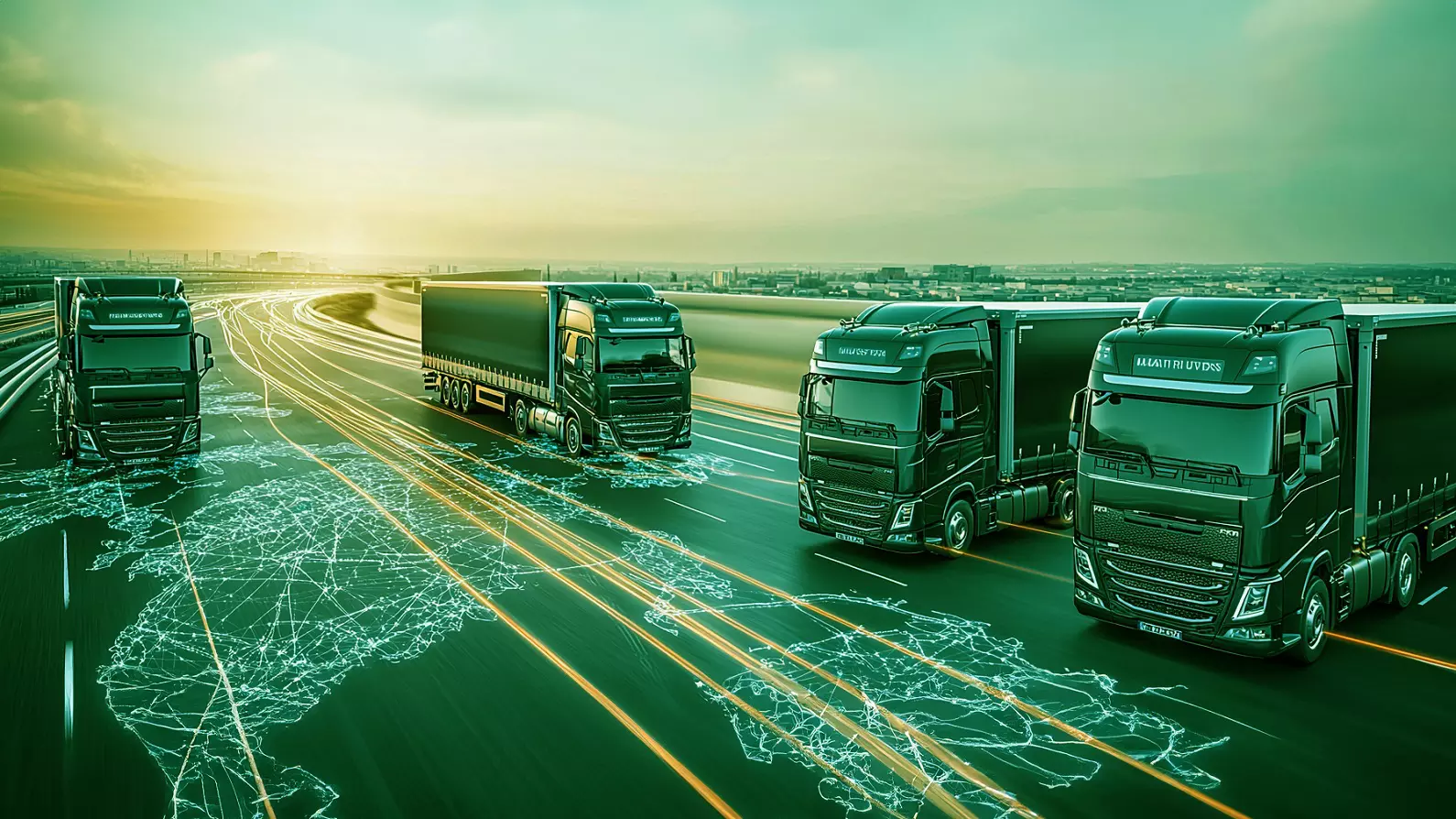
Fleet management in the U.S. is expected to hit $52.5 billion by 2030. That says a lot about how important it’s become for companies to keep their vehicles reliable, safe, and cost-effective. So, what does managing a fleet actually mean? And what does a fleet manager really do?
In short, they’re the ones making sure vehicles are where they need to be, drivers stay safe, fuel bills don’t get out of hand, and everything keeps moving. It’s part long-term planning, part daily problem-solving. This guide breaks down what fleet management really looks like from what it covers to how it’s done and what makes it work well in the real world.
{{demo_tms="/styles/components"}}
What is vehicle fleet management?
It’s how companies keep track of their work vehicles. Not just where they are, but how they’re running, how much fuel they’re using, if drivers are being safe, and if everything’s legal.
It’s used in delivery, construction, public works any job that needs vehicles out in the field.
Different people handle different pieces:
- Someone checks where the trucks are and when they’ll arrive.
- Someone else makes sure repairs happen before things break.
- Another person looks at fuel costs to catch waste.
- Safety folks watch for speeding or hard braking.
- Dispatchers figure out who goes where and when.
- And someone tracks all the paperwork insurance, inspections, deadlines.
That’s it. Just make sure the vehicles do their job and don’t cause problems.
How to manage a fleet of vehicles?
Here’s a simple step-by-step to help you build and manage your fleet from the ground up—without the guesswork.
1. Define the fleet’s role and requirements
If you’re building a fleet from scratch, the first thing to figure out is what you actually need the vehicles to do. Not every business has the same demands—a plumbing company might need a few reliable service vans, while a logistics company will be looking at long-haul trucks built for the long run.
Start by asking yourself some basics:
- What kind of work will these vehicles handle deliveries, service calls, or something else?
- How often will each one be on the road?
- Are they mostly driving through cities, covering rural routes, or crossing state lines?
- Are there any legal or environmental rules you need to keep in mind like low-emission zones or weight restrictions.
Answering these early on will help you make smarter decisions.
You won’t waste money on vehicles that aren’t suited to the job, and you won’t come up short on capacity later. A helpful approach is something called “fleet profiling,” where you match each role in your business to the right type of vehicle—based on things like size, fuel type, and how much it needs to haul.
2. Plan how you’ll get and rotate your vehicles
Once you know what kind of vehicles you need, the next step is figuring out how you’ll bring them into the fleet—and how you’ll keep them running for the long haul. Some businesses prefer to buy their vehicles outright, while others go the leasing route to stay current with newer models and avoid big maintenance costs.
Rotating vehicles is just as important. It’s a simple way to stretch the life of your fleet. For example, you can move older vehicles to lighter-duty routes and save the newer ones for the heavy lifting.
Here are a few good questions to guide your planning:
- Does it make more sense to lease or buy based on your budget and goals?
- How long should a vehicle stay in service three years, five, or until it hits a certain mileage?
- Can you move vehicles between teams or locations to even out the wear and tear?
It also helps to have clear replacement rules.
Something like: “Replace delivery vans every 120,000 miles or five years—whichever comes first.” That kind of structure keeps your costs predictable and your vehicles off the repair line.
3. Install a central fleet tracking system
If you’ve got more than a handful of vehicles on the road, it helps to know exactly where they are and what they’re doing. That’s where a fleet tracking system comes in. With tools like GPS and telematics, you can check vehicle locations, spot idling, monitor speed, and catch maintenance needs before they turn into problems. And the best part? It’s all in one place—whether you’re managing a few vans or a huge fleet.
Ask questions like:
- How will you track vehicle locations and usage?
- What insights do you need fuel usage, driving habits, maintenance schedules?
- Do you need alerts for things like off-route driving or long idle times?
Fynd’s delivery fleet management system is built to do exactly that.
It offers live trip status updates, lets you assign drivers based on availability and proximity, and gives you a zoomed-in view of what’s happening on the road. As soon as a trip starts, the system updates every detail—from trip distance to driver status—all on one interactive dashboard.
Key features include:
- Real-time trip visibility with exact delivery status and driver location
- Instant status switching (offline to online) for task-based assignments
- Route views that update with each new pickup, drop, or stop
- Clear visibility into how many drivers are online and in progress
- A single screen that shows movement, progress, and pending actions
This kind of live data flow removes communication gaps between drivers and dispatchers. It helps you stay on top of things without getting in the way. Just smoother, more controlled operations.
4. Build a preventive maintenance program
Preventive maintenance isn’t just about doing oil changes on time, it’s about keeping your vehicles in good shape and avoiding surprise breakdowns. Think of it as a routine that keeps everything running smoothly.
Every vehicle should have a simple log where you track what’s been done and what’s coming up, like regular checkups, tire rotations, inspections, or anything under warranty.
It also helps to ask questions like:
- What service schedule does the manufacturer recommend?
- Are some vehicles on the road more and need extra attention?
- Can we set up software to remind us when it’s time for maintenance?
Fynd TMS makes it easier to stay ahead of maintenance without making it a big chore.
You get a clear picture of how each vehicle is being used, what condition it’s in, and when it might need a check. Everyone—from the person behind the wheel to the dispatcher—can spot issues early. If something’s not right, it gets flagged before the day even starts. Plus, since all your trip and task info is in one system, maintenance just fits right into the daily workflow. Nothing gets lost or forgotten.
5. Track driver behavior and vehicle performance
Telematics shows you how drivers are handling the vehicles. Things like hard braking, quick takeoffs, sharp turns, and sitting idle too long all burn more fuel and put extra strain on the vehicle. That info’s useful for coaching drivers and keeping things safer on the road.
Ask questions like:
- Are drivers following safe, fuel-efficient driving habits?
- Which vehicles are using more fuel than expected?
- Do certain routes cause more wear and tear?
Create a scoring system or driver report card.
Let’s say one of your drivers rarely slams the brakes and keeps idle time to a minimum. That kind of performance might earn them a green rating. On the other hand, a driver who keeps tripping alerts? They might need a little extra coaching.
Some companies go a step further and offer rewards for good driving—things like bonuses or gift cards. It’s not just about saving fuel. You’re also cutting down the chance of accidents and keeping vehicles in better shape for longer.
Best practices for managing your fleet
Keeping a fleet in good shape isn’t just about fixing things when they break. The real trick is stopping issues before they happen. Here are a few habits every fleet manager should keep in mind:
1. Make preventive maintenance part of the routine
Breakdowns slow everything down, cost money, and can put drivers at risk. Maintenance shouldn’t wait until something goes wrong. Set up a schedule for each vehicle—based on mileage, engine hours, or whatever the manufacturer recommends.
That means regular oil changes, checking fluids, brakes, tires, and batteries, and swapping out parts before they wear out completely. It’s not about adding more work—it’s just doing the right work at the right time.
One way to stay on top of it: group vehicles by type and set service intervals accordingly. A delivery van doing short daily routes might get checked every 5,000 miles. A heavy-duty truck doing long hauls might need a tighter schedule.
Keep a written log for every vehicle, noting the last service date, type of service, and upcoming tasks. A well-maintained vehicle runs longer, consumes less fuel, and faces fewer compliance issues. It also avoids disruptions like missed deliveries or downtime from preventable issues like tire failures or overheating.
2. Keep an Eye on Fuel Use
Fuel is one of the biggest costs in fleet management, so tracking it isn’t optional. The key is consistency—log every fill-up with the date, amount, and odometer reading. Once you’ve got that down, you can start seeing what each mile is really costing you.
Keep an eye out for things like:
- One vehicle using more fuel than others in the same group
- Sudden jumps in fuel use tied to certain drivers or routes
- Long idle times that waste fuel for no reason
Catch this stuff early, and you can adjust routes, check for engine problems, or just talk to the driver. Small changes here can make a big difference over time.
3. Train and monitor drivers for safe and efficient behavior
Drivers are directly responsible for the vehicle’s safety, fuel use, and overall condition. That makes training and accountability critical. Every driver should be trained not just in basic road rules but in fleet-specific standards: how to handle long hours, how to reduce wear on brakes and tires, and how to handle emergency breakdowns or inspections.
Safe driving behavior includes smooth acceleration, maintaining safe distances, avoiding harsh braking, and minimizing idle time. Set behavioral benchmarks—for instance, no more than two harsh braking events per 100 miles. Monitor against those standards through regular reporting, check-ins, or ride-alongs.
Drivers who meet or exceed standards should be acknowledged. Those who fall below should receive follow-up training. This builds a culture of ownership and accountability, reducing both incident rates and long-term maintenance costs.
4. Smarter routes save more than just fuel
Let’s be honest—poorly planned routes are a pain. They waste fuel, chew up driver hours, and can throw off your whole schedule. Planning routes isn’t just about picking the shortest line between two points. You’ve got to think about real-world stuff—like traffic at 4 pm, tight delivery windows, road closures, and making sure the workload evenly spreads out.
A good place to start? Take a look at the routes you've already been using. Where were the slowdowns? Which drivers had to reroute or sit in bumper-to-bumper traffic? That’s the kind of insight that helps you build better routes next time.
Also, little tweaks can make a big difference. Things like avoiding left turns in busy areas or grouping deliveries in the same neighborhood. For example, instead of sending a driver all over town, keep their stops close together. Less driving, more doing. And here’s the thing: route planning isn’t one-and-done. Stuff changes—traffic, customer needs, weather, whatever. Your routes should change with it.
5. Stay on top of the rules
There’s a lot of red tape when it comes to running a fleet. Things like inspections, insurance, emissions checks, making sure your drivers have the right licenses, keeping log books up to date—it’s a lot. And yeah, if you miss something? You’re looking at fines, delays, or worse—vehicles parked until it’s sorted out.
Keep a compliance calendar for every requirement tied to each vehicle and driver. This includes:
- Registration and insurance renewal dates
- Inspection cycles (monthly, quarterly, annual)
- Certification expiry dates for drivers (CDL, medical exams, etc.)
- Regional or state-specific rules for commercial vehicles
Each of these should have a clearly assigned owner—whether the fleet manager, HR, or the driver.
Documentation should be physically stored in the vehicle and backed up in your internal records. In high-compliance sectors (e.g., hazardous material transport), routine internal audits should be conducted to catch issues early.
Vehicle fleet management tasks
When it comes to managing a fleet it involves multiple tasks that ensure effective vehicle operation and regulation compliance. If you’re doing vehicle fleet management, your key responsibilities will include:
1. Vehicle procurement and disposal: You have to select vehicles that fit your operational needs and budget. You may have to decide between purchasing or leasing, talking to suppliers and more.
2. Maintenance scheduling: Another role is to schedule when the maintenance routine for the vehicles must be done. This will help prevent any breakdowns and extend the life of your vehicle.
3. Driver management: You’ve got to hire solid drivers, train them right, and keep an eye on how they’re doing out there. It’s not just about getting from point A to B it’s about safety, responsibility, and making sure they’re representing the company the right way.
4. Route planning: It’s not as simple as it sounds. You’re juggling traffic, delivery windows, and making sure drivers aren’t wasting fuel zig-zagging across town. A good route saves money and time—and keeps the drivers a little saner.
5. Fuel stuff: Fuel’s expensive. So tracking how much each vehicle uses isn’t just a nice-to-have—it’s a must. You can catch weird spikes, figure out who’s idling too long, and start making small changes that save a lot over time.
6. Paperwork and compliance: Yeah, it’s the boring part, but it matters. Licenses, insurance, inspections—all that stuff needs to be up to date. One slip-up and suddenly a vehicle’s off the road, or you’re hit with a fine.
7. Watching the budget: Fleet costs can get out of hand fast if you’re not paying attention. You’ve got to know where the money’s going, spot what’s worth spending on, and where you can cut back without hurting the operation.
8. Safety: Accidents happen but the fewer, the better. Regular training, the right safety gear, and keeping vehicles in good shape all help lower the risk (and the headaches that come with it).
9. Using the data: If you’re not looking at the numbers, you’re flying blind. Telematics, GPS, maintenance logs they’re full of info you can use to make smarter decisions. It’s not about overthinking—it’s about being one step ahead.
What you should actually be tracking in fleet management
If you want to know how your fleet’s really doing, you’ve got to track more than just miles or fuel. Here are a few key things to keep an eye on—nothing fancy, just what actually matters day to day.
1. Budget adherence
Basically, are you spending more than you planned? This covers everything—fuel, maintenance, insurance, you name it. If you’re constantly going over budget, either the plan’s off or something in the process needs fixing.
2. Vehicle utilization
How often are your vehicles actually out there doing their job? If something’s sitting around too much, that’s wasted money. On the flip side, if it’s constantly in use, you might be pushing it too hard or not have enough vehicles in rotation.
3. Replacement timing
Every vehicle has a shelf life. If you're holding onto them too long, you’re probably bleeding money on repairs and breakdowns. Track mileage, age, and how often it’s in the shop—that’ll tell you when it’s time to move on.
4. Total cost of ownership (TCO)
It’s easy to focus on the price tag when buying a vehicle, but that’s just part of the story. What about everything else fuel, repairs, insurance, how much it’s worth when you sell it? When you add all that up, some “cheap” vehicles end up costing way more in the long run. So yeah, looking at the full picture helps you avoid buying a money pit.
5. ETA (Estimated Time of Arrival)
Are things getting where they need to be when you said they would? If not, that’s a problem. It could be the routes, could be the drivers, or maybe something else. Either way, if ETAs are off, customers notice and that’s not a great look.
Challenges & solutions in vehicle fleet management
When it comes to managing a fleet, there is some uncertainty involved. And with uncertainty comes a mix of unpredictable issues. We’ve picked out some of the most common challenges and given you their solutions.
1. Managing high costs
Fleet management isn’t cheap. Fuel, repairs, downtime–all these costs stack up quickly. When you’re not tracking and forecasting these costs, your budget will fall short.
Solution: Break down all costs by category and vehicle. Monitor cost per mile, compare fuel use, and flag high-maintenance units.
- Set a monthly operating cost cap per vehicle
- Track fuel and maintenance costs separately
- Review aging vehicles for replacement or lighter use
Small adjustments, like replacing one inefficient route or phasing out a fuel-heavy vehicle, can save thousands over a quarter.
2. Supply chain disruptions
Delays in getting vehicle parts, fuel, or inventory can stall the entire operation. These issues are hard to control but can be prepared for.
Solution: Build contingency plans. Maintain relationships with multiple vendors. Keep a limited stock of high-failure parts in-house.
- Identify suppliers with a backup options
- Track which vehicles are waiting on delayed parts
- Reschedule routes to use healthier vehicles during shortages
Planning for supply hiccups prevents full stops when things go off course.
3. Fuel management
Fuel usage can vary wildly depending on vehicle condition, route planning, and driving behavior. Left untracked, it’s one of the most wasteful cost centers.
Solution: Measure fuel use by trip and vehicle. Identify trends, compare similar routes, and coach drivers on reducing idle time.
- Monitor idle hours and fuel per delivery
- Flag unusual fuel spend across shifts
- Use mileage-based reports to highlight top and bottom performers
Fuel control starts with visibility, then comes habit change.
4. Route optimization
In order to save costs, route optimization is a must. But it's not that easy. Selecting the most efficient route that leads to less fuel burn and frustrated drivers is necessary but cannot be done with static planning, or outdated maps often don’t reflect real-time traffic or road conditions.
Solution: Use recent delivery data to design smarter, more consistent routes. Assign trips based on location, vehicle status, and delivery clusters.
- Reduce backtracking by clustering sto.ps
- Avoid known delay zones or construction-heavy areas
- Match route lengths to vehicle condition or load
Better routes reduce pressure on drivers and wear on vehicles.
5. Health and safety issues
Driver fatigue, distracted driving, and mechanical issues put both employees and the public at risk. These aren’t just safety concerns—they're liability risks.
Solution: Set limits on shift hours. Monitor driving behavior. Schedule vehicle checks tied to trip frequency and not just dates.
- Limit shift durations based on route type
- Flag harsh driving events (braking, turning, speeding)
- Require safety checks after a certain number of trips
Protecting drivers protects the entire operation.
6. Compliance requirements
Missed inspections, expired licenses, or outdated paperwork can shut down a vehicle or the whole fleet. The real issue most of the time? Disorganization.
Here’s how to fix it: Keep all compliance info in one place no scattered spreadsheets
- Set up alerts before deadlines hit so nothing gets missed
- Keep both physical and digital copies of the important documents
- Assign someone to handle renewals for each vehicle or region
- Do a quick monthly check to catch anything slipping through the cracks
Fleet management isn’t just about planning routes or booking service appointments.
It’s about building a system that holds up when things get busy. That’s where Fynd comes in giving you a clear view of what’s happening, better control at the moment, and tools that actually make the day-to-day easier to manage.
Frequently asked questions
Vehicle acquisition, maintenance planning, driver supervision, fuel and route tracking, and compliance management.
It’s the process of running and maintaining a group of vehicles used for business—keeping them safe, efficient, and ready for daily use.
It helps reduce costs, avoid downtime, and make sure vehicles and drivers stay safe and compliant.
Fuel usage, vehicle downtime, cost per mile, maintenance frequency, and driver behavior scores.
Tools like GPS tracking, telematics, and fleet management software help you monitor vehicles in real time, stay on top of maintenance, and make data-driven decisions that save time and money.
It depends on mileage, age, and repair history—but generally, if maintenance costs keep rising or reliability drops, it’s probably time to retire the vehicle and bring in a new one.