Types of Warehouse Management Systems & What is Warehouse Management Systems 2025
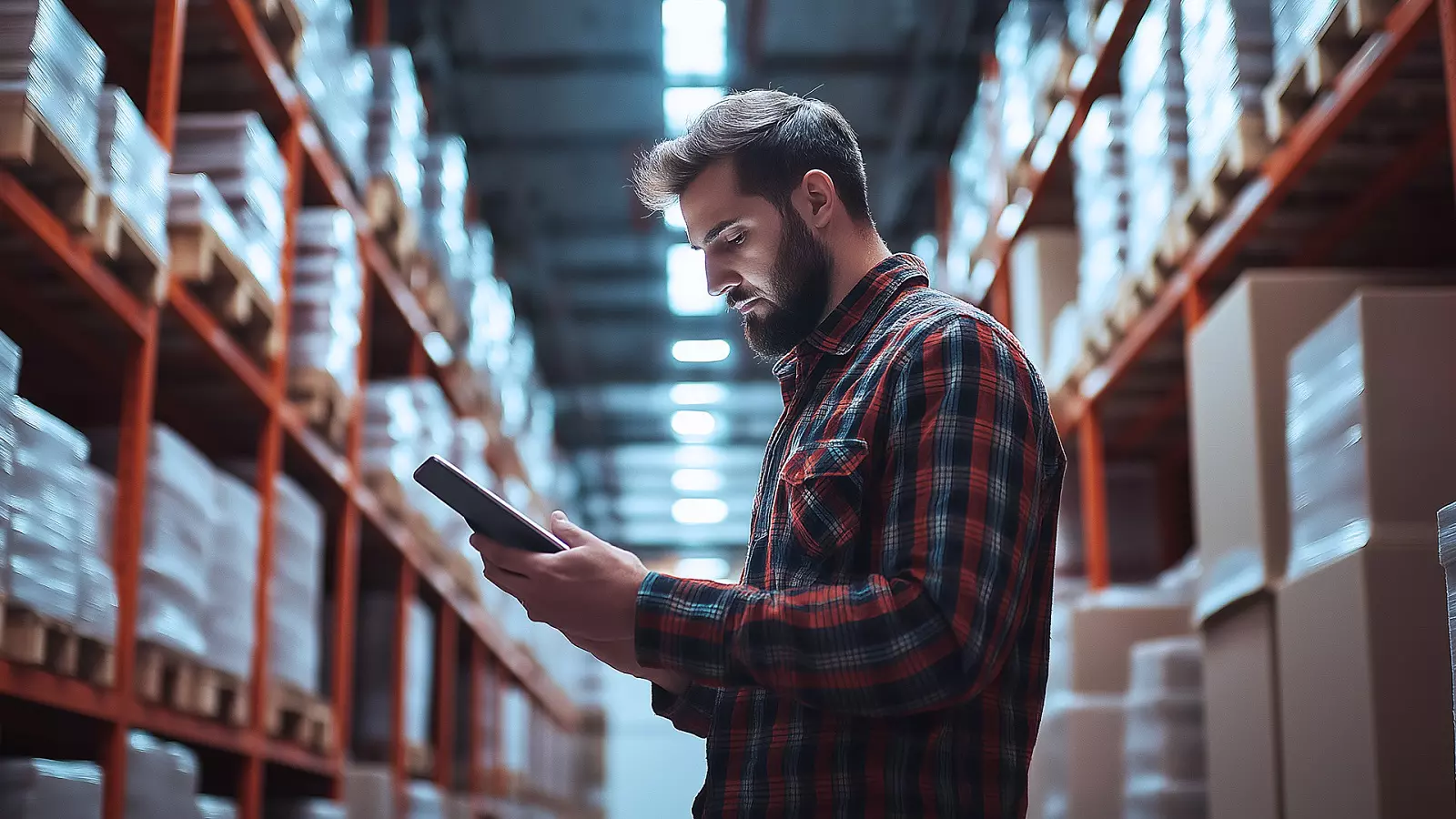
A Warehouse Management System (WMS) is essential software designed to streamline and manage daily warehouse tasks, from receiving goods to shipping them out. By automating key processes like inventory tracking, order fulfillment, and resource allocation, WMS helps improve efficiency and accuracy. It serves as a central hub that connects all warehouse activities, offering real-time visibility and control over inventory in multiple locations. This enhanced control leads to better decision-making and quicker responses to operational needs.
As e-commerce grows, the need for efficient warehouse management has become more critical. Customers expect fast and accurate order deliveries, making WMS a vital tool for businesses. Beyond just managing inventory, a WMS plays a key role in the overall supply chain, ensuring that operations are smooth and responsive to market demands. Companies that invest in WMS can better meet these expectations while reducing costs and errors, giving them a competitive edge in the market.
A WMS also integrates with other systems, like Enterprise Resource Planning (ERP) and Transportation Management Systems (TMS), to synchronize all aspects of warehouse operations. In today’s competitive environment, having a robust WMS is no longer optional; it’s a necessity. With labor shortages and increasing customer demands, a WMS helps businesses adapt, meet challenges, and succeed in the ever-changing marketplace. Implementing a WMS can significantly enhance productivity, allowing companies to scale operations as they grow.
What is a Warehouse Management System (WMS)?
A warehouse management system (WMS) is a software solution designed to optimize and control daily warehouse operations from the moment goods arrive at a facility until they are shipped out. By automating processes such as inventory tracking, order fulfillment, and resource allocation, a WMS enhances operational efficiency and accuracy.
This system serves as a central hub that integrates various warehouse activities, enabling real-time visibility and management of inventory across multiple locations. As e-commerce continues to grow, the demand for efficient warehouse management has intensified, making WMS an essential tool for businesses aiming to meet customer expectations for speed and accuracy in order delivery.
{{demo_wms="/styles/components"}}
Types of Warehouse Management Systems
A Warehouse Management System (WMS) is a comprehensive software solution designed to streamline and optimize various warehouse operations, such as inventory management, order fulfillment, picking, packing, and shipping processes. By automating these tasks, WMS significantly improves efficiency, accuracy, and real-time visibility within the warehouse environment.
This enables businesses to manage their resources more effectively while minimizing errors and delays. As e-commerce and global trade continue to expand, robust WMS solutions have become essential for organizations looking to enhance their supply chain performance and meet growing customer expectations.
1. Standalone Warehouse Management Systems
Standalone Warehouse Management Systems are independent software applications focused solely on managing warehouse operations. These systems are ideal for small to medium-sized businesses that require specific functionalities without needing broader enterprise integration. Standalone WMS often includes essential features such as inventory tracking, order management, and labor management tailored to optimize warehouse efficiency.
Advantages:
- Cost-Effective: Standalone WMS typically has lower upfront costs compared to integrated systems, making it accessible for smaller businesses.
- Specialized Features: These systems offer advanced functionalities specifically designed for warehouse operations, enhancing efficiency and accuracy.
- Ease of Implementation: With fewer complexities involved, standalone WMS can be set up quickly, allowing businesses to improve their operations promptly.
- Flexibility: Users can customize features based on their specific needs without the constraints of a larger integrated system.
Disadvantages:
- Limited Integration: Standalone systems may struggle to integrate with other business software, leading to data silos and inefficiencies.
- Scalability Issues: As a business grows, standalone WMS may not accommodate increased complexity or volume without significant upgrades.
- Narrow Focus: These systems primarily concentrate on warehouse functions and may lack broader supply chain capabilities found in integrated solutions.
2. ERP Integrated Warehouse Management Systems
ERP Integrated Warehouse Management Systems combine warehouse management functionalities with broader Enterprise Resource Planning (ERP) systems. This integration allows for seamless communication between various business processes, such as inventory management, order processing, and financial tracking. By utilizing an ERP-integrated WMS, businesses can achieve a holistic view of their operations, enabling better decision-making and improved efficiency across departments.
Advantages:
- Unified Data Management: Provides a single source of truth for all business processes, reducing data silos and improving accuracy.
- Enhanced Efficiency: Streamlines workflows by automating data exchange between the WMS and other ERP modules, leading to faster order fulfillment.
- Improved Inventory Control: Real-time visibility into inventory levels helps prevent overstocking and stockouts, optimizing inventory management.
- Cost Savings: Reduces operational costs through better resource allocation and demand forecasting.
Disadvantages:
- Complex implementation: Integrating WMS with existing ERP systems can be challenging and time-consuming, requiring significant planning and resources.
- Higher Initial Costs: The upfront investment for an ERP-integrated WMS may be higher compared to standalone systems.
- Limited Flexibility: Businesses may face constraints in customizing the WMS features compared to standalone solutions that offer more specialized functionalities.
3. Cloud-Based Warehouse Management Systems
Cloud-Based Warehouse Management Systems leverage cloud technology to provide scalable and flexible warehouse management solutions. These systems allow users to access their warehouse data from anywhere with an internet connection, facilitating real-time tracking and management of inventory and operations. Cloud-based WMS is particularly beneficial for businesses looking to reduce IT infrastructure costs while enhancing accessibility.
Advantages:
- Scalability: Easily scales with business growth, allowing companies to adjust their usage based on changing needs without significant investment in hardware.
- Lower IT Costs: Reduces the need for extensive on-premise infrastructure, lowering overall IT maintenance costs.
- Accessibility: Enables remote access to warehouse data, facilitating better collaboration among teams and improved decision-making.
- Automatic Updates: Cloud providers typically offer regular updates and maintenance, ensuring users have access to the latest features without additional effort.
Disadvantages:
- Data Security Concerns: Storing sensitive information in the cloud may raise security concerns for some businesses.
- Internet Dependency: Requires a reliable internet connection; any downtime can disrupt access to critical warehouse data.
- Potential Integration Challenges: Integrating cloud-based WMS with existing on-premise systems may pose compatibility issues.
4. Supply Chain Module Warehouse Management Systems
Supply Chain Module Warehouse Management Systems are designed as part of a broader supply chain management (SCM) system. These solutions emphasize the entire supply chain process, from procurement to distribution, ensuring that warehouse activities align with overall supply chain objectives. This integration helps businesses manage inventory more effectively while improving coordination with suppliers and customers.
Advantages:
- Holistic View of Operations: Provides insights into the entire supply chain, enabling better forecasting and planning.
- Enhanced Collaboration: Facilitates communication between different stakeholders in the supply chain, improving responsiveness to market changes.
- Optimized Inventory Management: Helps prevent stockouts by integrating demand forecasting with inventory levels across the supply chain.
- Streamlined Processes: Automates various supply chain functions, reducing manual intervention and improving efficiency.
Disadvantages:
- Complex Setup: Implementing a supply chain module WMS can be complex due to the need for extensive integration with other systems.
- Higher Costs: Typically more expensive than standalone WMS due to the breadth of functionalities offered.
- Training Requirements: Employees may require significant training to effectively utilize the comprehensive features of a supply chain module WMS.
5. Industry-Specific Warehouse Management Systems
Industry-specific Warehouse Management Systems are tailored solutions designed to meet the unique needs of particular sectors such as pharmaceuticals, food and beverage, or retail. These systems incorporate specialized features that address regulatory requirements, industry standards, and operational challenges specific to each sector.
Advantages:
- Customization for Compliance: Designed to meet industry regulations and standards, ensuring compliance with legal requirements.
- Specialized Features: Offers functionalities that cater specifically to industry needs, enhancing operational efficiency.
- Improved Efficiency: Streamlines processes unique to the industry, such as batch tracking in pharmaceuticals or perishable goods management in food logistics.
- Enhanced Reporting Capabilities: Provides industry-specific analytics and reporting tools that help businesses make informed decisions.
Disadvantages:
- Limited Flexibility: May not easily adapt to changes in business operations or new industry trends outside its original design scope.
- Higher Costs for Customization: Custom features may come at a premium price compared to more generic systems.
- Vendor Lock-In Risks: Businesses may become reliant on specific vendors for updates and support, limiting future options for change or upgrades.
Improve Inventory Accuracy And Reduce Stockouts With Wms
Implementing a Warehouse Management System (WMS) can significantly improve inventory accuracy and reduce stockouts, ensuring that businesses maintain optimal stock levels and meet customer demands. A WMS provides real-time visibility into inventory levels, automates tracking processes, and enhances order management.
By leveraging features such as barcode scanning and RFID integration, businesses can minimize human errors and streamline inventory management. Additionally, advanced analytics capabilities allow for better forecasting of customer demands, helping to prevent both overstocking and stockouts. Key Strategies to Improve Inventory Accuracy and Reduce Stockouts:
- Real-Time Inventory Tracking: WMS continuously monitors inventory levels, providing up-to-date information that helps prevent stock discrepancies.
- Automated Replenishment: The system can automatically trigger replenishment orders based on predefined thresholds, ensuring that stock levels are maintained without manual intervention.
- Barcode Scanning and RFID: Integrating these technologies enhances accuracy in inventory counts and reduces errors during receiving and shipping processes.
- Advanced Analytics: WMS provides insights into inventory trends and customer demand patterns, enabling better forecasting and planning to avoid stockouts.
Integrated Suite Warehouse Inventory Accuracy And Reduced Stockouts With WMS
Implementing a Warehouse Management System (WMS) is crucial for improving inventory accuracy and reducing stockouts. A WMS provides real-time visibility into inventory levels, enabling businesses to track stock movements accurately and respond swiftly to demand fluctuations.
By automating inventory processes, such as receiving, picking, and shipping, a WMS minimizes human errors and enhances overall operational efficiency. This leads to better inventory management practices, ensuring that products are available when needed and reducing the likelihood of stockouts that can negatively impact customer satisfaction.
Key Strategies to Improve Inventory Accuracy and Reduce Stockouts:
- Real-Time Inventory Tracking: Continuous monitoring of stock levels ensures accurate data is always available, preventing discrepancies and enabling timely replenishment.
- Automated Replenishment: WMS can automatically generate purchase orders when the stock reaches predefined thresholds, ensuring optimal inventory levels without manual oversight.
- Barcode Scanning and RFID Integration: These technologies facilitate precise tracking of inventory movements, reducing errors during receiving and shipping processes.
- Advanced Analytics: Utilizing historical data and trends allows businesses to forecast demand accurately, helping to avoid both overstocking and stockouts.
1. Integrating a Warehouse Management System with Other Systems
Integrating a Warehouse Management System (WMS) with other business systems, such as Enterprise Resource Planning (ERP) and Transportation Management Systems (TMS), is crucial for optimizing supply chain operations. By establishing seamless communication between these systems, businesses can achieve real-time visibility, improved efficiency, and enhanced decision-making.
WMS integration enables the exchange of critical data, such as inventory levels, order information, and shipping details, ensuring that all stakeholders have access to accurate and up-to-date information. This integration streamlines workflows, reduces manual errors, and enhances overall supply chain performance.
2. ERP Integration
Integrating a WMS with an ERP system creates a unified platform that combines warehouse management with broader business processes. This integration allows for the exchange of data between the two systems, ensuring that inventory levels, order information, and financial data are synchronized. By leveraging the capabilities of both systems, businesses can make more informed decisions, optimize resource allocation, and improve overall efficiency.
- Improved inventory management: Real-time inventory data enables better forecasting and reduces the risk of stockouts or overstocking.
- Enhanced order processing: Automated data exchange between the WMS and ERP ensures accurate order fulfillment and reduces manual errors.
- Better financial management: Integrating financial data from the ERP system with the WMS provides a comprehensive view of warehouse costs and profitability.
3. TMS Integration
Integrating a WMS with a Transportation Management System (TMS) streamlines the shipping and logistics processes. By sharing data on order details, carrier information, and delivery schedules, the WMS and TMS work together to optimize transportation planning and execution. This integration enables businesses to reduce shipping costs, improve delivery times, and enhance customer satisfaction.
- Optimized transportation planning: Real-time data on order volumes and delivery requirements allows for better route planning and load optimization.
- Improved carrier management: Integrating carrier information and tracking data ensures efficient communication with shipping providers and accurate delivery updates.
- Enhanced visibility: Tracking shipments across the WMS and TMS provides end-to-end visibility into the supply chain, enabling better decision-making and proactive issue resolution.
4. CRM Integration
Integrating a Warehouse Management System (WMS) with Customer Relationship Management (CRM) tools enhances the ability to track customer interactions and order histories. This integration allows businesses to connect sales data with warehouse operations, ensuring that customer orders are fulfilled accurately and efficiently. By sharing information between the WMS and CRM, companies can improve customer service, streamline order processing, and gain insights into customer preferences.
- Enhanced Customer Insights: Access to real-time order status and inventory levels helps sales teams provide better service and manage customer expectations.
- Streamlined Order Processing: Automating the flow of information between sales and warehousing reduces manual entry errors and speeds up fulfillment times.
- Improved Communication: Facilitates better collaboration between sales and warehouse teams, ensuring alignment on order priorities and inventory availability.
5. CMS Integration
Integrating a WMS with Customs Management Systems (CMS) is particularly beneficial for businesses involved in international trade. This integration streamlines compliance processes by automating customs declarations and documentation. By connecting the WMS with a CMS, companies can ensure that all necessary paperwork is completed accurately and efficiently, reducing the risk of delays or penalties.
- Regulatory Compliance: Automates compliance checks and documentation, ensuring adherence to customs regulations.
- Faster Processing Times: Streamlines the submission of customs declarations, reducing delays in shipment processing.
- Enhanced Visibility: Provides real-time updates on customs status, allowing businesses to manage potential issues before they arise proactively.
Factors Influencing WMS Selection
Selecting the right Warehouse Management System (WMS) is influenced by several critical factors that align with a business's operational needs and strategic goals. These factors help organizations identify the most suitable WMS that can enhance efficiency, improve inventory accuracy, and streamline processes. Understanding these factors ensures that businesses make informed decisions, ultimately leading to better performance and customer satisfaction. Key Factors Influencing WMS Selection:
Business Requirements: Clearly defining the specific needs of the warehouse operation, including inventory management, order fulfillment, and integration capabilities, helps in selecting a WMS that aligns with operational goals.
- Scalability: The chosen WMS should be able to grow with the business, accommodating increased inventory levels and additional functionalities as the organization expands.
- Integration Capabilities: Assessing how well the WMS integrates with existing systems such as ERP or TMS is crucial for ensuring seamless data flow and process efficiency across the organization.
- Cost Considerations: Evaluating both initial investment and ongoing operational costs is essential. Businesses should consider licensing fees, implementation costs, and potential savings from improved efficiency when selecting a WMS.
- User-Friendliness: A user-friendly interface reduces training time and enhances employee productivity. The system should be intuitive to ensure that staff can quickly adapt to new processes.
- Vendor Support and Reputation: Researching the vendor’s track record, customer support options, and user reviews can provide insights into their reliability and commitment to customer satisfaction.
- Customization Options: The ability to customize the WMS to suit specific operational needs can significantly enhance its effectiveness. Businesses should look for systems that allow for tailored features and functionalities.
Conclusion
Choosing the right Warehouse Management System (WMS) is crucial for streamlining warehouse operations and boosting supply chain efficiency. To make an informed decision, businesses should evaluate factors like specific operational needs, scalability, integration with existing systems, and ease of use. A well-suited WMS can enhance inventory accuracy, reduce stockouts, and improve overall productivity. By carefully selecting a WMS that aligns with their goals, companies can not only optimize their warehousing processes but also significantly contribute to long-term business success and customer satisfaction.
Frequently asked questions
A WMS is software that optimizes warehouse operations like inventory tracking, order fulfillment, and shipping. It automates tasks to improve efficiency and accuracy, providing real-time visibility into inventory for better supply chain decisions.
A WMS automates inventory tracking with tools like barcode scanning and RFID, reducing human errors. It ensures inventory levels match demand, preventing discrepancies and improving overall inventory management.
Integrating a WMS with ERP or TMS systems improves operational efficiency by streamlining data, reducing errors, and enhancing decision-making with real-time inventory and order insights.
Consider operational needs, scalability, integration capabilities, user-friendliness, cost, vendor support, and customization when choosing a WMS to ensure it aligns with business goals.
Yes, by automating replenishment and providing real-time inventory data, a WMS prevents stockouts, ensuring products are available and minimizing overstock risks.
Yes, training helps staff use a WMS effectively, reducing errors and improving productivity.