The complete guide to smart warehousing: automation, tools and strategies
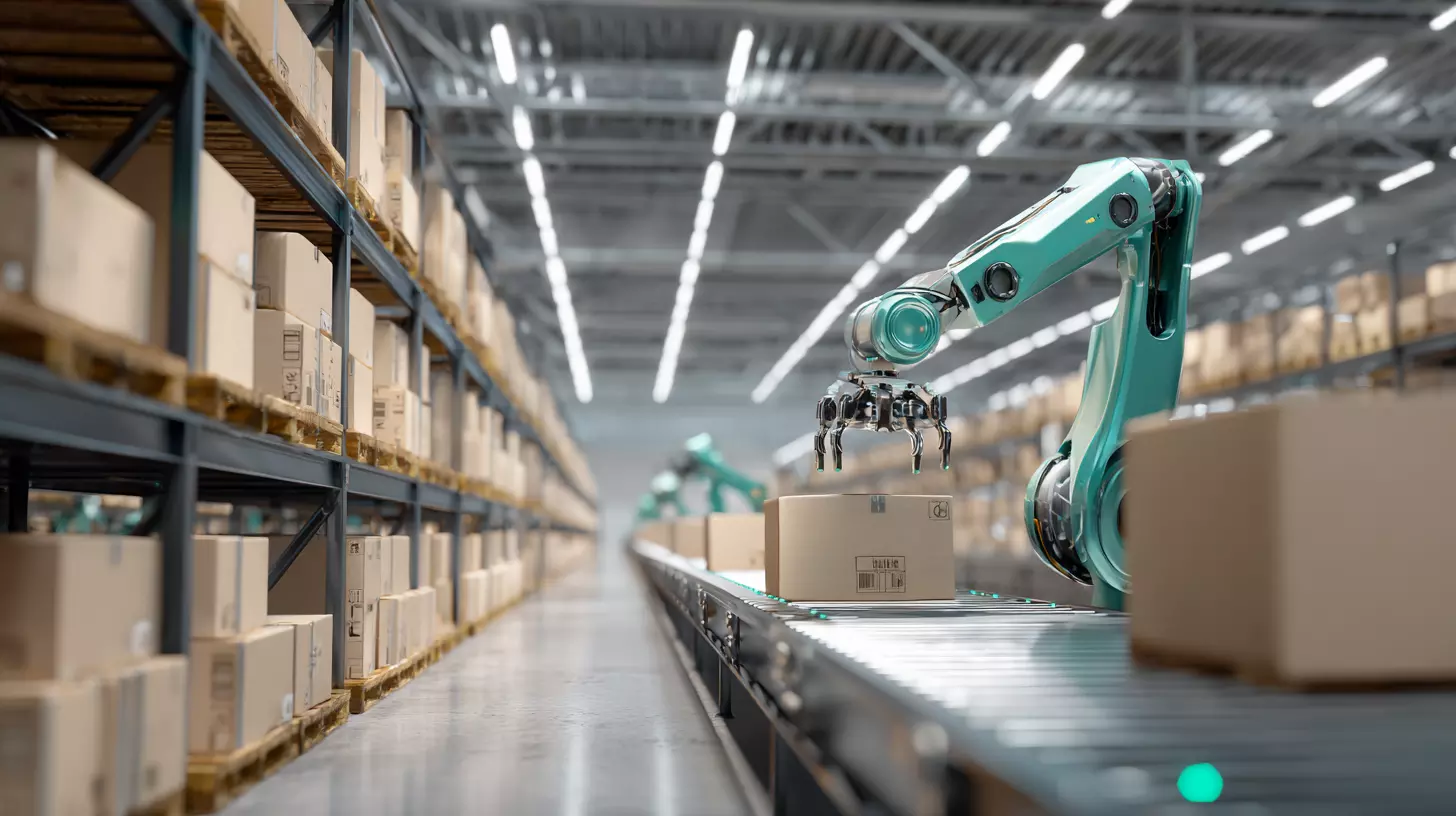
Warehousing nowadays is not as it used to be. Warehouses are under more pressure than before due to the growth of online shopping and the escalating expectations of customers. Quicker delivery, increased inventory, and fewer workers make it difficult to maintain operations as before.
Smart warehouse technology is where the solution lies. Imagine you provided your warehouse with a brain: it automates repetitive tasks, enables real-time integration of systems, facilitates real-time data sharing, and empowers teams to make better decisions using data. Smart warehouses are using robots, sensors, and other software that share information to ensure that they do not rely on clipboards and manual checks.
{{demo_wms="/styles/components"}}
The companies that switch are not merely keeping pace but going ahead. The global smart warehouse market is growing at a high rate, and it is not surprising. It enables effective time management, reduces mistakes, prevents operational collapse, and helps prevent your team from burning out.
This blog will delve into what a smart warehouse truly is, the best technologies you require, the advantages you can anticipate, practical situations, potential issues to be aware of, and what the future holds.
What is a smart warehouse?
A smart warehouse is a smarter warehouse with a technology-powered approach that uses automation, information, and connectivity to facilitate the easy running of such a warehouse. It goes beyond manual work and creates an atmosphere in the warehouse where machines and systems can communicate with one another, decide, and be flexible to changes on a real-time basis.
Picking and tracing of inventories and restocking are rather people and paper-intensive in a traditional warehouse. This can lead to time and human error wastage and inefficiency. A smart ware, however, integrates the power of automation, sensors, robotics, A.I., and software platforms to enable the warehouse to be more responsive and efficient.
A warehouse can be considered smart with three main parts:
1. Automation
This includes conveyor belts, robotic arms, autonomous mobile robots (AMR), as well as automated storage and retrieval systems (AS/RS). Automation helps reduce human effort, enabling the more speedy and precise execution of order picking and packing activities daily.
2. Connectivity
Smart warehouses are built on a network of interconnected devices and systems that work in real-time. This consists of IoT sensors, RF tags, barcode scanners, and a connected machine. When these devices are combined, they provide a real-time, transparent view of the warehouse. For example, when a product is misplaced, the system will immediately recognize it and instruct a robot to retrieve it.
3. Data integration
The main benefit of a smart warehouse is that it collects, analyzes, and acts upon data. Because of modern systems (warehouse management systems (WMS), enterprise resource planning (ERP) systems, and artificial intelligence dashboards), warehouses are making faster decisions in a shorter amount of time. They can track order trends, determine the optimal quantity of items to order, and even identify the most efficient path for pickers or robots to follow.
As these elements operate in combination, they can transform a warehouse into a living system that constantly learns and evolves. The outcome is increased speed in operations, reduced cases of error, reduced costs, and improved experience of both employees and clients.
With the rise of demand for faster and more reliable deliveries, smart warehouses have become a necessity rather than a luxury. The smart warehousing market is projected to reach USD 46.42 billion by 2030, with a CAGR of 8.3%. The growth is a clear sign of the pace at which companies have embraced digitalization and automation into their supply chains.
Top 7 must-have smart warehouse technologies
A smart warehouse employs a variety of technologies to operate at maximum efficiency. These technologies are capable of working in conjunction to ensure that repetitive tasks can be automated, tasks are performed accurately, and operations are conducted at a high level of efficiency. These are seven of the most important technologies that you will encounter in a smart warehouse, and their value.
1. Automated picking tools
Automated picking technologies, including pick-to-light, voice picking, and robotic picking arms, speed fulfillment time and reduce the likelihood of human errors. For instance, in a pick-to-light system, workers have lights indicating the location of storage, which makes the picking process significantly faster, easier, and more accurate. All of automated picking represents a fantastic solution for e-commerce warehouses, which tend to have thousands of different SKUs and short turnaround times.
There are also companies using AI-powered robotic arms that pick individual items, which design the picking arm to adapt to the shape and weight of items, and then automatically sort them as well. Automating this process can reduce the dependency on manual labor and also allow warehouses to operate longer shifts without the fatigue and mistakes associated with human labor.
2. Autonomous mobile robots (AMRs) and automated guided vehicles (AGVs)
AMRs and AGVs are revolutionizing warehouse mobility. Unlike AGVs, which rely on fixed paths for transporting materials, AMRs can adjust their destination or planned path based on current dynamic conditions using sensors and mapping software.
Amazon (and others) currently use over 750,000 mobile robots to move inventory inside their facilities. These machines don't replace people, but instead assist them by carrying out repetitive and time-intensive tasks, providing workers with more time to apply their skill set in a more fulfilling way.
3. Automated inventory control platforms
Manually tracking inventory is inefficient and can lead to mistakes. Automated inventory management solutions can use sensors, barcode scanners, and real-time tracking to keep an accurate count of stock at all times.
For example, IoT-based shelves that notify teams when stocks are low or when items are put in the wrong location. Coupled with RFID tags, this will significantly enhance inventory visibility, resulting in reduced shrinkage and overstocking. Companies that use RFID technology have reported inventory accuracy up to 95%.
4. Warehouse management systems (WMS)
A WMS is the brain of a smart warehouse. It does everything needed, including inventory tracking and order management, labor distribution, and shipping. An effective WMS system integrates well with other systems, such as ERP software and transportation systems, to provide a comprehensive view of the entire chain.
New WMS systems that run in the cloud, leveraging AI and machine learning, are performing demand forecasting, recommending layout tuning, and taking it a step further by assigning appropriate tasks to robots and employees based on current workloads. This coordination eliminates potential errors by businesses, lowers operational costs, and aligns customer expectations with delivery.
5. Implementation of the Internet of Things (IoT)
The Internet of Things (IoT) connects devices, systems, and sensors throughout the warehouse. They can monitor a wide array of functions in real-time, including temperature in storage areas, and determine the location of a forklift. If a machine starts overheating or if a cold storage unit fails, they can send an immediate alert, reducing the chance of product loss.
Very large corporations such as Amazon, Walmart, and DHL are already implementing IoT into their warehouse processes. These companies use sensors, RFID tags, and real-time analytics to improve inventory accuracy, minimize downtime, and gain visibility across their supply chains. What we see in these examples is that IoT is not just the future but will define the future of global logistics and set the pace for its scalability and responsiveness.
6. Collaborative robots (cobots)
Unlike traditional robots that operate in an isolated environment, cobots are designed to work alongside workers. Cobots can assist with repetitive tasks such as lifting, sorting, or scanning, while improving efficiency and reducing physical fatigue.
Cobots are most evident in warehouses where space is limited or workflow is dynamic. Cobots are safer, provide ease of programming, and are more flexible than industrial robots. Most companies that use cobots find that their return on investment is quick, due to the ease of use, improved productivity, and a reduction in workplace injuries.
7. Automated Storage and Retrieval Systems (AS/RS)
AS/RS systems automate the retrieval and storage of inventory in compact, high-density racking systems. AS/RS systems use equipment like conveyors, cranes, or shuttles to deliver inventory to the requested location in a highly efficient and accurate manner. Generally, AS/RS systems deliver inventory to storage or retrieve inventory from staging. AS/RS systems are very efficient for warehousing in small spaces, especially for high-throughput warehouses.
For example, AutoStore is a cube-based AS/RS system that allows companies to stack bins vertically, potentially storing up to four times more inventory in the same floor space, depending on layout and use case. AS/RS systems increase picking efficiency, reduce human error, and reduce total labor cost.
Top 10 smart warehouse benefits
Implementing smart warehouse technology is not just a way to follow a trend; it can also change the way your operations run. Whether you have high order volumes, complex SKUs, or you're trying to lower your operational costs, a smart warehouse can improve your business. Here are the top 10 benefits smart warehouses provide:
1. Improved operational efficiencies.
Smart warehouses overcome time delays in transferring products from storage to shipping by automating mundane operations such as picking, sorting, and restocking. Smart warehouses utilize automation, real-time data, and optimized workflows to ensure that resources are utilized efficiently at all times.
2. Lower labor costs
Automation doesn’t take the place of your team; it frees them up to do more valuable work. Cobots, AMRs, and AS/RS systems perform all of the laborious and time-consuming tasks, which means you can do more work with fewer employees. This can be especially helpful during peak seasons or when labor markets are tight.
3. Better order accuracy
Smart technology can eliminate human error. For example, automated picking tools and WMS platforms ensure the right products get picked, packed, and shipped. An automated warehouse means fewer returns, happier customers, and reliability and dependability in reputation.
4. Real-time visibility and information
IoT sensors, WMS platforms, and inventory trackers all allow you to monitor your operations in real-time; you will know the location of your products, the amount of stock you have, and where your operations underperform, allowing you to make informed decisions quicker.
5. Quicker order processing and shipping
With warehouse automation and intelligent operating systems, orders can move quickly. Robots do not get tired, and WMS systems can determine the best way to optimize each aspect of the order lifecycle from receiving the product to dispatching it. This way, you have a better chance of meeting the high demand for same-day and next-day delivery.
6. Improved space utilization
Smart storage solutions, such as AS/RS systems and cube-based solutions, optimize every square inch of the warehouse. That means there’s less need for you to expand physically and lower storage costs in the long run.
7. Scalability and Flexibility
Smart warehouses scale with you. Need to process a larger number of orders? Add robots as needed. Need to manage more SKUs? Add software modules. Smart systems are designed to scale without overwhelming your staff and causing delays.
8. Reduced rates of error
The quality is checked at all levels, and errors are eliminated through automated system checks at an early stage. Digital identification of inventory, RFID tracking, and barcode scanning translate to fewer lost goods, mis-picks, or shipping errors.
9. Energy efficiency
A high number of warehouse technologies have been advanced, keeping in mind sustainability. The use of smart lighting systems, automatic equipment that powers down when idle, and controlled climate control systems is useful to reduce the expenditure on energy bills.
10. Enhanced customer satisfaction
When orders arrive faster, more accurately, and with fewer exceptions, customers take notice. Customers consistently notice the improved shipping times and are pleased. Happy customers lead to better reviews, more repeat purchases, and stronger long-term relationships. Customer experience is a key area of competitive differentiation in today’s economy, and smart warehouses help you on your journey to delivery.
To summarize, smart warehouse technologies benefit you both now and in the future. The extensive benefits of setting you up for success, from lowering costs to customer satisfaction, touch every leg of the supply chain.
Smart warehouse example: Puma’s transformation with Autostore
Puma, a worldwide sports brand, was experiencing a significant uptick in demand for their e-commerce capabilities and required faster and more accurate order fulfillment capabilities. To improve their order fulfillment capabilities, Puma secured an agreement with Autostore and systems integrator Bastian Solutions to deploy cube-based goods-to-person systems across multiple sites in North America and Europe.
Below are the impacts of this smart warehouse transformation on Puma's operations:
- They set up a grid with 305,000 bin locations in Indianapolis, making it one of the largest Autostore installations in North America.
- Storage capacity increased by 10 times, and it allowed Puma to co-locate multiple distribution Centers into one high-density facility.
- Order accuracy improved to 99 percent as a result of automated picking and automated verification systems.
- The shipping capacity was improved to 150,000 units per day. Lead times for fulfillment were reduced from as high as two weeks to same-day or next-day fulfillment.
- Energy usage was reduced by as much as 85 percent due to the efficiency of Autostore's robots and its grid-based design.
In addition to gains in operation, the new system also enhanced the working environment. Robots handle heavy loads and streamline repetitive, labor-intensive tasks, allowing employees to focus on less physical and more value-added work.
The experience of Puma on the path of smart warehouse development demonstrates the possibility to develop integrated automation, robotization, and warehouse management software to transform the processes at supply chain levels and make operations quick and scalable with regard to sustainability.
Challenges of smart warehousing and how to solve them
The transition to a smart warehouse is worth long-term results, but it does not go without short-term difficulties. Numerous businesses encounter challenges in the process of introducing automation, digitization, and data-based systems, more so when the company is moving out of the conventional warehouse design. The good news? The majority of these difficulties are obvious to solve.
The following are the most frequent obstacles that businesses encounter and how to overcome them.
1. Labor shortages
The challenge: warehouses around the world are having a hard time finding and keeping qualified staff. Warehouse work can be physically tough, turnover is high, and we are already facing an aging workforce.
The solution: Smart warehouse technology can cut down on manual labor. Automated picking technology, cobots (collaborative robots), and other guided systems can lift some of the repetitive, strenuous tasks from the employees so they can focus on more value-added work. Employers can also let employees move into a training program, which opens up the workforce for supervisory or technical roles that can help retain employees while filling some of the skill gaps.
2. Higher order volumes and SKU complexities
The problem: E-commerce development has resulted in warehouses managing more products at a higher volume and at a faster speed. Inventory accuracy, speed of picking, and storage footprint can be impacted.
The solution: Installing an advanced warehouse management system (WMS) along with automated inventory management enables businesses to track, organize, and process thousands of SKUs accurately. For warehouses moving high volumes, robotic picking and automated storage and retrieval systems (AS/RS) can dramatically enhance the retrieval and processing speed while maintaining accuracy.
3. The expectations of customers in terms of delivery time frames.
The problem: Same-day or next-day delivery is becoming the norm among customers. Either slow or wrong delivery may damage brand loyalty and have a negative effect on subsequent purchases.
Solution to it: Smart warehouses make fulfillment smoother by operating integrative models where inventory may be controlled, highest priority orders can be identified, and picking and packing can be quickly facilitated. Predictive analytics also enables companies to deal with peak demand in advance, thus minimizing delays and sidestepping last-minute repairs.
4. Order Picking Errors
The problem: Human error is part of manual picking, and the pressures of a highly timed operation can heighten it. Picking the wrong item can cause customer disappointment and dissatisfaction, resulting in increased returns and shipping costs.
The solution: Automation can significantly increase picking accuracy. Picking solutions such as pick-to-light, voice-picking, and barcode verification all decrease mistakes at the source. Real-time data integration from your WMS will confirm that every item is verified before being packed and shipped; you can maintain accuracy levels over 99%.
5. Lack of visibility into inventory
The problem: Some warehouses are running their stock with antiquated systems or spreadsheets, giving them inventory blind spots that create overstock, stockouts, and lost space and labor.
The solution: Smart warehouses use IoT sensors, RFID tags, and real-time tracking to give teams a real-time overview of the inventory in their entire facility. This gives better visibility, in turn, better forecasting, fewer errors, and lower holding costs.
6. Increased competition and pressures of scaling
The problem: fast-moving competitors, particularly digital natives, have created higher expectations for customers to have things delivered fast, and warehouses without flexible systems struggle to scale effectively.
The solution: Cloud-based smart warehouse platforms allow companies to top up their capacity without worrying about investing in large-scale infrastructure. Modular automation, such as AMRs, either as a fleet or shuttle systems, makes it easier to scale your operations without committing to major infrastructural investments. Having a lean operation in fast-moving industries is key, and smart warehousing allows for agile operations and flexibility.
Smart warehousing has many potential advantages, but only if businesses are aware of the pitfalls and are prepared to confront them. Companies with the proper technology and intelligent strategies can leverage some of the challenges into benefits.
Data protection in smart warehouses
The level of connectivity and the presence of data in smart warehouses make data security an aspect that should not be underestimated. Barcode scanners, inventory sensors, and any other device are included in a digital ecosystem. The volume of sensitive data produced, transferred, and stored in that ecosystem is beyond most people’s imaginations: inventory stocks, consumer data, business performance, etc.
Without any protection, this data is one of the targets.
Why data security matters
Cases of data security breaches may have severe implications such as revenue loss, downtimes, regulatory fines, and reputational losses. Cyberattacks such as ransomware or even phishing can block the system of the warehouse, pause the process, and disclose personal information about customers or suppliers. Some vulnerabilities allow the whole system to be compromised after a single weakness in a sensor or even a 3rd party integration.
Common risks in smart warehouse
- Unsecured IoT devices and sensors.
- outdated software or firmware.
- Lack of encryption during data transfer.
- weak access controls or poor password hygiene.
- insufficient employee training on cybersecurity best practices.
-
What are the methods of securing warehouse information?
1. Secure and encrypted use systems
Choose warehouse management systems with end-to-end encryption at rest and in transit. This makes data impossible to read or steal, even if it is intercepted.
2. Install access control mechanisms.
Not all people have to have access to everything. Restrict viewing of and editing data using role-based access. The multi-factor authentication (MFA) serves as an additional security measure for key systems.
3. Update systems
It is recommended that all devices (more so, IoT devices) be patched and updated on a regular basis. A number of cyberattacks exploit the vulnerabilities that can be recognized and ironed out within months.
4. Educate your employees
The security of a smart warehouse depends on its operators. Implement the basic cybersecurity training of all staff so that they learn how to recognize any form of phishing, remain safe using passwords, and observe safety rules.
5. Audit and monitor activity
Monitor and identify suspicious activity in real time using automated monitoring. Periodic auditing of the systems assists in fixing the weaknesses before they are used by the attacker.
Bonus: Contract with reputable suppliers.
Ensure your technology partners have a high regard for security, are updated regularly, and help with compliance needs such as the GDPR or ISO 27001. A safe vendor is a safe prolongation of your own operation.
With the increased intelligence of the warehouses comes the threats. One thing you cannot avoid doing is making cybersecurity part of your smart warehouse plan.
Emerging trends in smart warehousing (2025 and beyond)
With the further development of technology, smart warehouses not only become automated but are also defined as smarter, greener, and more responsive. These will be the major trends to influence the future of smart warehousing:
1. Warehouse optimization by AI
Artificial intelligence is even taking over the functions of the brain in warehousing. The demand patterns have been predicted using AI algorithms, the picking routes optimized, workloads evened, and even the possible bottlenecks identified before they take place. The more data the systems hold, the smarter they are and the more accurate they are with the management of labor, space, and the inventory of the enterprise.
2. Simulation and planning digital twins
A Digital twin is a virtual replica of a warehouse. The technology also enables businesses to test an overhaul, whereas they can simulate the introduction of new automation or reengineering of workflows before implementing the changes in reality. This eliminates risk, enhances planning, and enables informed decisions based on accurate data.
3. Quicker connection with the 5G networks
The 5G networks provide low-latency, ultra-high speeds, and as a result, it is much quicker to interlink thousands of sensors, robots, and systems through a warehouse. This results in easier coordination of devices and is more easily used in real-time decision making, which is vital in large-scale automation and robotics.
4. Sustainable automation
Warehouse design is tending towards environmental sustainability. The newer systems are constructed to consume less energy, use environmentally friendly materials, and produce less waste. Industry players are investing in green logistics by investing in energy-efficient robots and solar-powered facilities as a long-term strategy.
5. Greater personalization in fulfillment
Smart warehouses are emerging to support hyper-customized fulfillments due to the increasing consumer demand. This involves customized wrapping, package bundling, and other shipping arrangements depending on the immediate information about clients. This level of customization can be achieved in smarter systems without compromising speed or accuracy.
6. Augmented reality (AR) integration
Smart glasses are AR tools that are aiding warehouse employees in picking and packing. AR overlays can provide staff with instructions in real-time, thus minimizing errors and training processes. The trend aids in efficiency and the safety of the workers.
Such trends indicate that it is no longer sufficient to simply automate workplaces but rather establish new, cleverly linked environments that can sustain and adapt to changes at very fast rates and become more sustainable. Highly efficient smart warehouses in the not-so-distant future will not only boost productivity, but they will also be wiser, greener, and more human-centric.
The modern supply chain operations are beginning to be based on smart warehouses. Supercharged by automation, real-time data, and smart systems, they allow companies to be much more accurate, fast, and resilient. Conventional warehouses do not perform exceptionally well in providing fast, error-free fulfillment that is required today, and intelligent technology is designed to achieve that.
The advantages are obvious. Smart warehousing can be valued in terms of how it reduces dependency on labor, lowers operational expenses, enhances and optimizes picking of orders and customer satisfaction, with the final outcome of generating more profits. Although there are threats such as complexity of implementation and cybersecurity, other threats are manageable through a proactive, well-considered plan and can create long-term value.
With the supply chain slowing, customer expectations rising, and demands growing, smart warehousing is no longer an option for companies that aim to be competitive, agile, and future-oriented. It's a necessity.
Frequently asked questions
A smart warehouse utilizes technology, such as robotics, automation, and data analytics, to maximize efficiencies in tasks related to warehouse operations. In a traditional warehouse, manual processes are still used, which can add time to any given workflow and also have the potential for more mistakes. Smart warehouses operate faster, more accurately, and with scalability.
The core technologies consist of warehouse management systems (WMS), automated guided vehicles (AGVs), automated storage and retrieval systems (AS/RS), collaborative robots (cobots), internet of things (IoT) sensors, and Artificial Intelligence for predictive aspects.
Implementation costs vary significantly based on a warehouse's size, existing infrastructure, and the automation required. A small upgrade could cost tens of thousands of dollars, while changes in a large warehouse could result in costs of one million dollars or more. Regardless of size, however, most businesses see a strong return on investment and reduced labor costs, improvements in productivity, and accuracy..
Yes. Smart warehouse technologies allow companies to automate laborious, repetitive, and physically demanding tasks, which will reduce reliance on manual labor. This also allows current employees to focus their time on more value-added work. Utilizing smart warehouse technology will also reduce worker fatigue and productivity concerns, thereby potentially increasing job satisfaction.
Smart warehouses can be secure if the correct measures are in place. This means having encrypted platforms, secure access controls, and consistent updates to the system. Providing training on cybersecurity measures for staff and partnering with vendors you trust will further lessen the risk.
Identify your current operational challenges: delayed shipments, inventory inaccuracies, staffing issues, etc., and develop realistic objectives around them, and look at options of technology you can use to assist with these challenges. You will find it easier to begin the transition if you look into using open-ended or scale solutions, for example, starting with a cloud-based WMS or automated picking solutions, and develop from there. Working with experienced partners can make the transition more seamless and improve your chances for long-term success.