10 Top Role of Warehouse Management System in 2025
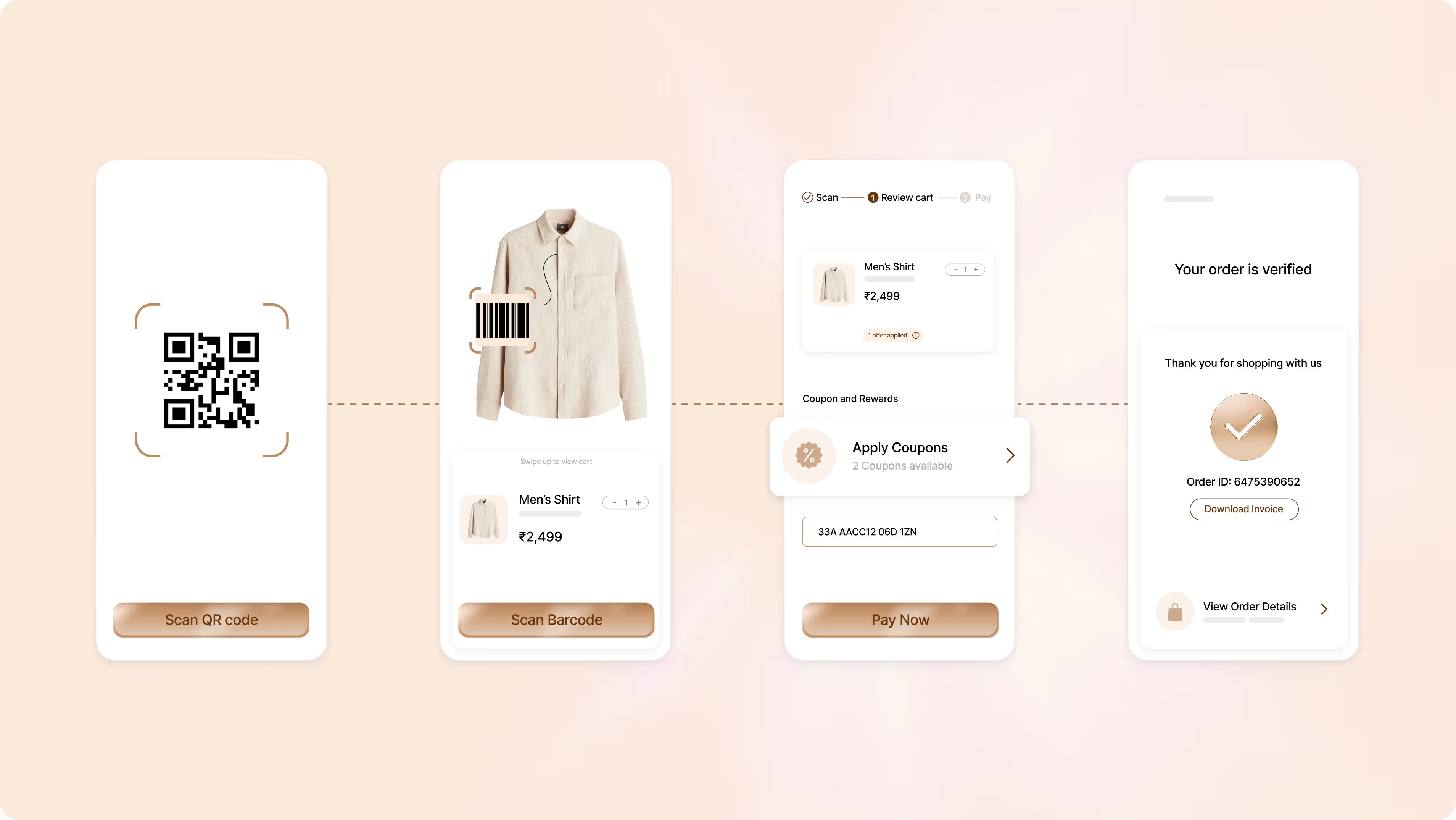
Warehouse management systems (WMS) play a pivotal role in streamlining warehouse operations, ensuring efficient inventory control, order fulfillment, and improved customer satisfaction. By automating key processes, businesses can enhance productivity, reduce errors, and cut operational costs. For example, companies implementing WMS can experience up to a 25% reduction in inventory errors and a 30% increase in productivity.
The primary benefits of a WMS include real-time inventory tracking, which provides full visibility of stock levels across multiple locations. This reduces costly stockouts and overstocking, helping to balance demand with supply. Additionally, a WMS can optimize space utilization by up to 40%, resulting in cost savings and more efficient warehouse layouts. As cloud-based WMS solutions continue to rise, they offer scalability and flexibility, allowing businesses to manage operations remotely.
Fynd’s Warehouse Management System offers all these benefits with a user-friendly interface, seamless ERP integration, and robust analytics tools to ensure you optimize every aspect of your warehouse operations. By adopting a WMS, businesses can overcome the challenges of manual inventory management and improve operational efficiency. If you're looking to enhance the role of the warehouse management system within your business, Fynd provides a perfect solution to help you achieve these goals.
10 Roles of a Warehouse Management System (WMS) in 2025 Inventory Control and Tracking
A Warehouse Management System (WMS) plays a crucial role in streamlining operations by providing real-time inventory tracking, optimizing order fulfillment, and improving space utilization. It automates workflows, forecasts demand, and manages labor efficiently, reducing costs and enhancing productivity.
Additionally, WMS systems offer data analytics, ensure compliance, and handle returns smoothly. By integrating with ERP and CRM systems, they foster scalability and flexibility, enabling businesses to meet evolving market needs. Ultimately, a WMS improves customer satisfaction through accurate order deliveries and faster service, helping businesses maintain a competitive edge in the fast-paced retail environment. Check out the 10 Key Roles of a WMS in 2025 below.
{{demo_wms="/styles/components"}}
1. Inventory Control and Tracking
A WMS ensures accurate, real-time inventory tracking across multiple locations, minimizing stockouts and overstocking. This enables businesses to optimize inventory turnover, reduce holding costs, and respond swiftly to demand changes. With instant updates, WMS empowers decision-makers with data-driven insights to improve warehouse efficiency, streamline order fulfillment, and maintain a competitive edge in the ever-changing market landscape.
2. Order Fulfillment Optimization
By automating order picking, packing, and shipping processes, WMS accelerates order fulfillment cycles, reducing errors and delays. It optimizes pick paths, enhances accuracy, and ensures faster delivery times. This level of efficiency not only improves customer satisfaction but also boosts operational productivity, helping businesses meet growing consumer demands with precision and agility in competitive supply chain environments.
3. Improved Space Utilization
A WMS utilizes advanced algorithms to maximize warehouse space by optimizing storage layouts and placement strategies. By efficiently organizing inventory and reducing search times, it enhances storage capacity and minimizes wasted space. This role not only lowers operational costs but also ensures smooth workflows and faster order processing, helping businesses manage resources more effectively and improve overall warehouse efficiency.
4. Labor Management and Productivity
WMS enhances labor productivity by automating task assignments and providing optimized workflows. It reduces idle time, eliminates redundant manual processes, and boosts worker efficiency through tools like real-time tracking and performance analytics. This results in a streamlined workforce, improved throughput, and lower labor costs, helping businesses achieve higher productivity levels and maintain consistent performance standards.
5. Returns and Reverse Logistics Management
WMS simplifies the handling of returns, ensuring efficient processing of returned goods, accurate restocking, and minimal disruptions. It provides clear insights into reasons for returns, enabling businesses to address customer concerns effectively. By managing reverse logistics efficiently, WMS helps maintain customer satisfaction while minimizing losses and waste, ensuring smooth operations in an often-overlooked area of warehouse management.
6. Integration with Supply Chain Systems
Seamless integration with systems like ERP, TMS, and CRM allows WMS to connect warehouse operations with broader supply chain processes. This integration improves data flow, enhances visibility, and enables better decision-making across departments. By creating a unified system, businesses can optimize workflows, reduce errors, and increase overall efficiency in managing supply chain complexities.
7. Real-Time Data and Advanced Analytics
WMS delivers actionable insights through real-time data collection and comprehensive analytics. It tracks key performance indicators, identifies bottlenecks, highlights trends, and provides accurate forecasts to optimize operations. Advanced reporting tools empower businesses to make informed, strategic decisions, enhance overall warehouse efficiency, and improve customer satisfaction by ensuring timely and highly accurate deliveries, fostering trust and reliability in increasingly competitive supply chain environments.
8. Scalability and Flexibility
A cloud-based WMS offers scalability to adapt to business growth, seasonal demands, and market changes. With features like remote accessibility and modular upgrades, it supports operations in multiple warehouses and locations. This flexibility ensures that businesses can expand or pivot strategies without disruptions, maintaining efficiency while keeping costs under control.
9. Regulatory Compliance and Traceability
WMS ensures compliance with industry standards and regulatory requirements by maintaining accurate records and facilitating traceability. It streamlines processes for labeling, documentation, and auditing, reducing the risk of penalties or delays. By supporting transparency in operations, WMS helps businesses maintain credibility and meet the growing demands for accountability in modern supply chains.
10. Enhanced Customer Satisfaction
WMS ensures timely and accurate order deliveries, leading to improved customer trust and loyalty. Features like real-time tracking, error reduction, and faster processing times contribute to a better overall experience. By consistently meeting or exceeding customer expectations, businesses can build long-term relationships and maintain a competitive edge in the market.
Key Benefits of WMS
A Warehouse Management System (WMS) plays a vital role in streamlining warehouse operations, enhancing accuracy, and optimizing resources. By automating key tasks and providing real-time insights, a WMS helps businesses improve efficiency, reduce costs, and deliver better customer experiences. Below are key features that make WMS indispensable for modern warehousing:
- Improved Inventory Accuracy: Real-time tracking minimizes errors, prevents stock issues, and ensures accurate data for better decisions.
- Faster Order Fulfillment: Automated picking, packing, and shipping streamline processes, speeding up deliveries and boosting accuracy.
- Cost Reduction: Optimizes inventory, labor, and space usage, cutting storage and operational costs.
- Enhanced Efficiency: Automates routine tasks, coordinates activities, and reduces delays to improve productivity.
- Better Space Utilization: Maximizes storage with smart placement strategies, reducing wasted space.
- Real-Time Data & Reporting: Provides instant updates and insights for quick decision-making and improved responsiveness.
- Improved Customer Satisfaction: Ensures timely, accurate deliveries, fostering trust and loyalty.
- Scalability: Adapts to business growth and demand fluctuations while maintaining efficiency.
- Supply Chain Integration: Seamlessly connects with ERP and TMS systems, enhancing coordination and visibility.
- Increased Labor Productivity: Automates task assignment and reduces manual work, boosting throughput and accuracy.
Key Features of WMS
A Warehouse Management System (WMS) optimizes operations by automating tasks like inventory tracking, order fulfillment, and shipping. It uses real-time data and system integration to streamline workflows, reduce errors, and improve space utilization. This leads to better inventory control, faster order processing, and higher customer satisfaction, making it essential for boosting efficiency and scalability.
- Inventory Tracking: Real-time stock updates reduce stockouts, optimize turnover, and improve order accuracy.
- Order Management: Automates picking, packing, and shipping to enhance speed and accuracy, boosting customer satisfaction.
- Barcode Scanning: Improves accuracy and workflow speed by tracking products during receiving, picking, and shipping.
- Automated Replenishment: Monitors stock levels and triggers purchase orders to maintain optimal inventory.
- Real-Time Reporting: Provides insights into performance metrics for data-driven decision-making and agility.
- Labor Management: Assigns tasks efficiently, reducing idle time and boosting workforce productivity.
- Warehouse Layout Optimization: Maximizes storage space and reduces search times through efficient layout planning.
- Multi-Channel Integration: Seamlessly connects with ERP, TMS, and other platforms for unified operations.
- Pick and Pack Automation: Guides workers with optimized routes, reducing errors and speeding up fulfillment.
- Shipping Management: Chooses carriers, generates labels, and tracks shipments for cost-effective, timely deliveries.
How Does a Warehouse Management System Work
A Warehouse Management System (WMS) helps businesses track inventory, manage stock, and streamline warehouse operations. By using real-time data, a WMS ensures goods are efficiently moved within the warehouse, improving overall efficiency. It supports accurate order fulfillment, faster processing times, and optimized resource management.
WMS automates manual tasks like inventory tracking and order picking, helping businesses reduce errors and meet customer demands quickly. This system not only improves accuracy but also boosts cost savings by minimizing stockouts, reducing excess inventory, and maximizing warehouse space. Here's how a WMS works:
Step 1- Inventory Tracking
A Warehouse Management System (WMS) continuously monitors inventory levels and tracks stock locations within the warehouse. By providing real-time visibility of stock, it ensures the right items are available for picking and shipping, reducing the risk of stockouts or overstock situations. This capability helps optimize inventory turnover and improves overall warehouse efficiency, enabling businesses to respond more quickly to demand changes and reducing storage costs.
Step 2- Order Fulfillment
When an order is received, a WMS generates picking lists, directing warehouse staff to the correct locations for picking. By optimizing pick paths and providing real-time updates, it accelerates the order fulfillment process. This leads to faster order processing, improved picking accuracy, and a more efficient workflow. The result is an enhanced customer experience with fewer errors and quicker deliveries, helping meet high expectations in the fast-paced supply chain environment.
Step 3- Shipping & Receiving
A WMS effectively tracks both incoming shipments and outgoing orders, ensuring products are accurately received and stored in the correct locations. It also provides real-time data on order packing and shipping, ensuring each item is correctly packed and dispatched without error. This system not only increases the accuracy of shipping but also ensures products are delivered on time, leading to improved customer satisfaction and operational efficiency.
Step 4- Integration with Other Systems
A Warehouse Management System integrates seamlessly with other critical business systems such as Enterprise Resource Planning (ERP) and Customer Relationship Management (CRM) software. This integration provides a complete, real-time view of the supply chain, from procurement to customer delivery. By connecting data across multiple systems, a WMS enhances operational visibility and enables better decision-making, ultimately streamlining processes, reducing costs, and improving efficiency.
Types of Warehouse Management Systems
Warehouse Management Systems (WMS) come in several types, each designed to meet specific business needs and enhance operational efficiency. These systems optimize various warehouse functions such as inventory management, order fulfillment, and shipping, contributing to cost reduction and improved accuracy.
By selecting the appropriate WMS, businesses can increase overall efficiency, reduce errors, and enhance customer satisfaction. The choice of system often depends on the size of the company, its operations, and its technological infrastructure. Below is an overview of the different types of WMS, each suited to specific requirements and business scales.
1. Standalone WMS
A standalone WMS operates independently of other business systems like ERP or CRM, focusing exclusively on warehouse functions such as inventory tracking, order picking, and shipping. This system is ideal for businesses that need to streamline warehouse operations without integrating complex solutions. While it may lack certain advanced features, it is a cost-effective choice for smaller businesses or companies that don’t require real-time data sharing with other departments.
2. Integrated WMS
An integrated WMS works seamlessly with other business systems, such as ERP and CRM, allowing for real-time data sharing across various departments. This integration provides a comprehensive view of inventory, customer orders, and the supply chain, facilitating better decision-making. It’s an ideal choice for businesses that require a more holistic and connected approach to warehouse management, improving accuracy and operational efficiency across the entire enterprise.
3. Cloud-Based WMS
A cloud-based WMS operates on cloud infrastructure, offering scalability, flexibility, and remote access. This type of system reduces the need for expensive on-premises hardware, lowering IT costs, and is easily adaptable to a business’s growth. It allows warehouse managers to monitor and manage operations from any location, making it particularly useful for businesses with multiple warehouses or those expanding into new markets.
4. Subscription-Based WMS
A subscription-based WMS follows a pay-as-you-go model, where businesses pay a monthly or annual fee for the software. This model provides flexibility, making it ideal for smaller businesses or companies with fluctuating needs. It typically includes cloud-based access, regular software updates, and customer support, making it an attractive and cost-efficient solution for growing businesses that need an affordable and scalable system.
How to Implement a Warehouse Management System?
Implementing a Warehouse Management System (WMS) requires thorough planning, clear communication, and efficient execution to optimize warehouse operations. A WMS is crucial for streamlining functions such as inventory tracking, order picking, shipping, and overall warehouse workflow management.
A successful implementation helps to reduce errors, boost efficiency, and integrate seamlessly with existing business processes. Following a structured approach ensures that the system delivers maximum value. The steps outlined below will guide you in successfully implementing a WMS to improve operational efficiency, reduce costs, and enhance customer satisfaction.
- Assess Your Needs: Evaluate your current warehouse processes to understand the gaps and requirements. This will help in choosing the right WMS for your business.
- Choose the Right WMS: Based on your needs, select a WMS that fits your business scale and integrates with your existing ERP, CRM, or other systems.
- Plan Your Workflow: Define your warehouse operations clearly and map out workflows for receiving, storing, picking, packing, and shipping.
- Prepare for Data Migration: Cleanse and migrate existing data into the new system, ensuring inventory counts and other records are accurate for a smooth transition.
- Train Staff: Properly train warehouse staff on how to use the new WMS, including how to manage inventory, process orders, and troubleshoot issues.
- Test the System: Run a pilot test with a small batch of orders to identify any system glitches or inefficiencies before full-scale implementation.
- Monitor and Optimize: After the WMS is live, continuously monitor performance, collect feedback, and make necessary adjustments to improve efficiency and accuracy.
- Provide Ongoing Support: Ensure you have a support plan in place to resolve any technical issues quickly and keep the system running smoothly.
Conclusion
A Warehouse Management System (WMS) revolutionizes warehouse operations by enhancing efficiency, accuracy, and productivity. With key features such as real-time inventory tracking, automated stock replenishment, and optimized picking and packing, a WMS reduces errors, accelerates order fulfillment, and improves customer satisfaction.
By integrating seamlessly with other systems, WMS provides businesses with greater insights and enables data-driven decision-making. For businesses looking for an efficient, scalable warehouse solution, Fynd WMS offers a powerful platform to streamline warehouse operations and optimize supply chain management, helping companies stay competitive and responsive in today’s fast-paced market.
Frequently asked questions
A Warehouse Management System (WMS) is software designed to optimize warehouse operations by automating tasks like inventory management, order fulfillment, and shipping. It ensures efficiency, accuracy, and faster delivery times.
WMS tracks inventory in real time, providing accurate stock levels and reducing errors. It helps businesses minimize overstocking, reduce stockouts, and manage products efficiently, improving inventory turnover and order fulfillment.
Yes, WMS can integrate with ERP, TMS, and other business systems, ensuring seamless data flow across the supply chain. This integration helps businesses streamline operations and enhance decision-making processes.
Automated stock replenishment ensures that businesses maintain optimal inventory levels by triggering purchase orders when the stock reaches predefined thresholds. This reduces stockouts, overstocking, and manual intervention.
WMS automates order picking and packing using real-time data and barcode scanning. This reduces human error, speeds up the fulfillment process, and ensures that customers receive the correct products on time.
Yes, WMS can be customized to meet the needs of different warehouse types, whether small or large. It helps businesses of all sizes improve warehouse efficiency, reduce costs, and optimize space utilization.