How to use WMS: supercharge your warehouse operations
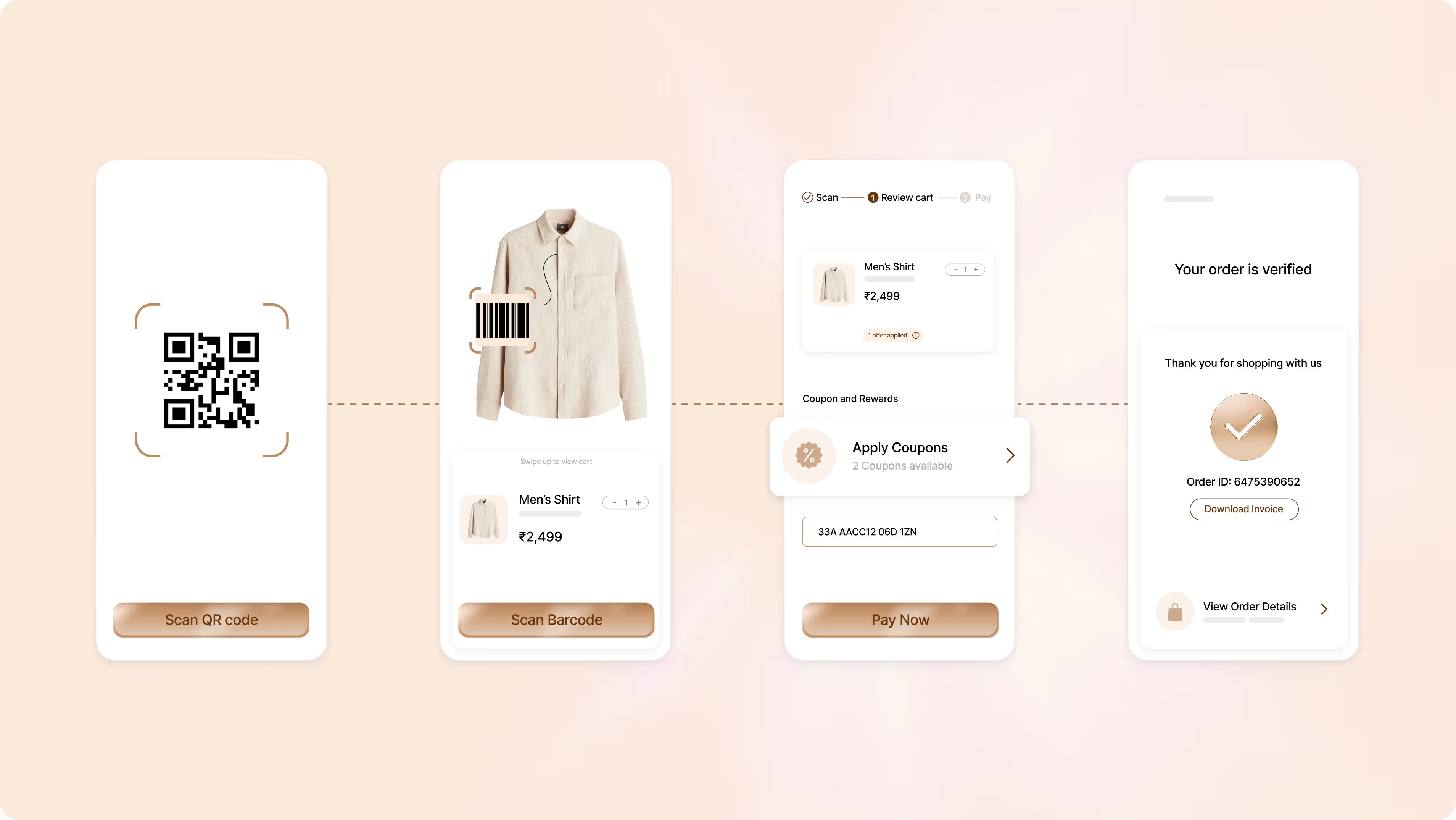
Behind every on-time delivery, accurate inventory count, or hassle-free return is a warehouse functioning in the background. Running your warehouse efficiently is not a simple thing. There is increased customer demand, greater fluctuation in orders, and numerous opportunities for errors in the manual process to occur.
That is when the warehouse management system (WMS) comes in. WMS isn’t just software, it is something that gives structure, automation and real-time control in the complexity of modern logistics. WMS solutions help the businesses to manage its stocks better, optimize its fulfillments, and manage unexpected changes.
This article serves as your guide to utilizing a warehouse management system to its fullest potential, from system implementation and configuration to daily workflows and long-term performance. Whether you are moving from a spreadsheet to a WMS or refining your use of a previous WMS or other solution, this article demonstrates how you can make your warehouse smarter, faster, and more resilient.
{{demo_wms="/styles/components"}}
What is a warehouse management system?
A warehouse management system (WMS) is software that supports and optimizes the function of a warehouse and distribution center. A WMS tracks and controls the movement and storage of materials throughout a warehouse, helping to digitize core functions such as inventory tracking, picking and packing, order fulfillment, and shipping, so that businesses can become more efficient and less prone to errors.
A WMS's main purpose is to create the optimal pathway for the flow of goods and materials through warehouses in a timely and cost-effective manner. WMS technology is an interface between your enterprise resource planning (ERP) system and the physical flow of goods within the warehouse.
Key features of a WMS
A modern warehouse management system, when effectively implemented, can significantly enhance the efficiency of goods receipt, processing, and shipping. However, to truly appreciate a modern WMS, we must break down the essential features that make WMS a great driver of improvement in warehouse operations.
1. Inventory management
The core function of any WMS is inventory management. This functionality allows businesses to have a clear view of stock levels in real-time, providing visibility into what current inventory levels are, which items are on reserve, and what items are due for replenishment.
A WMS uses bar scanning, RFID, and automated data capture devices to eliminate manual data entry errors. A WMS can also provide cycle counts that are accurate, automated replenishment, and better stock rotations (e.g., FIFO, LIFO).
Close to 80% of warehouse associates and decision-makers state that the lack of accurate inventory and out-of-stocks are still major productivity issues. 91% of decision-makers are actively working on this gap, with most of them already planning to invest in technology by 2028 to overcome gaps in visibility throughout the supply chain.
2. Order fulfillment
One of the most significant areas where a WMS adds value is in order fulfillment. The WMS provides automated workflows with time and workload for every function, including picking, packing, and shipping.
Pick lists can be designed in automated workflows with algorithms that minimize travel time throughout the different warehouse zones. Whether using batch picking, wave picking, or zone picking, order volume and timing for all orders can impact the picking stage.
The WMS can even generate shipping labels and order status in the company's ERP or e-commerce platform after a customer order is packed for a shipment, as well as determine the lowest cost carrier.
Having all these functions work seamlessly together allows greater order accuracy, fewer shipping delays, and ultimately happier customers.
3. Labor management
Labor is typically the most expensive recurring expense in a warehouse operation. A WMS can help improve workforce productivity using skill-level-based assignments, availability, and workload balance, which helps you use your labor more effectively and efficiently.
You can track labor on the WMS using any number of labor tracking features, allowing managers to not only see how individuals are performing but also identify bottlenecks and adjust workloads in real-time. There are even WMS solutions offering gamification tools for additional staff motivation and engagement.
Finally, using a data-driven approach to labor helps ensure that your valuable resource, labor, is consistently assigned and utilized during active operations, which is especially valuable during peak or seasonal activity.
4. Integration capabilities
Supply chains of the modern era require unified communication among various systems.
A desirable WMS will be integrated with numerous systems, such as:
- Enterprise resource planning (ERP) systems.
- Transportation management systems (TMS).
- E-commerce platforms.
- Customer relationship management (CRM) tools.
- Third-party logistics (3PL) partners.
Organizations can benefit from and take advantage of open APIs and cloud-based architecture, which enables the implementation of flexible integration, leading to the possibility of real-time synchronizations and faster decision-making in general.
Steps to set up your WMS
Implementation of a warehouse management system is not a single process that involves installation of any software; it is a set of strategic moves that need planning, organization and commitment. Whether you are doing an upgrade of your existing spreadsheets or replacing an old system, going through a structured implementation plan will ensure that you get the most out of your WMS.
Here are some critical steps to effectively implement your WMS:
Step 1: System configuration
The system configuration is the basis for your WMS deployment. The process involves setting up the software to match your warehouse's workflows, facility layout, and operational rules.
You will want to:
- Label storage zones and bins.
- Set up your SKU attribute, barcodes, and unit conversions.
- Design your picking and replenishment plans (e.g, FIFO, LIFO, batch picking).
- Apply your own user roles, permissions, and delegations as needed.
Good configuration translates to a WMS that reflects `real-world` operations, limiting disruption along the way. The system should also be adaptable to support evolving operational requirements that occur on a day-to-day basis and maintain the integrity of the processes.
Step 2: Data migration
Data migration to the new WMS is a very crucial part of the process that should be taken very seriously.
Migrating includes:
- Inventory data.
- Vendor and supplier information.
- Historical ordering information.
- Product details (weights, measurements, serial numbers).
To prevent corrupting your new system, it’s important to clean, validate, and format your data prior to migration. Poor data hygiene at this point could lead to big problems with inventory issues, shipping delays, and inefficiencies in the system.
Step 3: Training and onboarding
The most sophisticated WMS will still fail if your staff are not trained to use it. Training makes sure that your warehouse staff, supervisors, and IT understand how to use the system and how to troubleshoot issues that arise.
Your onboarding process should include:
- Hands-on training for warehouse operators on their handheld devices and scanners.
- Process training for managers and supervisors on how to access dashboards and reports.
- Establishing standard operating procedures (SOPs) that clearly define workflows put in place by the WMS.
This is also a good time to start gaining buy-in and reducing resistance to change. You might want to do a phased rollout, starting with super-users who can support others.
Step 4: Real-time inventory tracking
Once your system goes live, your WMS provides real-time inventory visibility throughout your warehouse.
This includes tracking:
- Live updates of inbound and outbound shipments.
- Immediate notification of inventory movement and/or location changes.
- Real-time notifications of low stock or stock discrepancies.
All item movements will be scanned using RFID or barcode, and every movement will be incorporated and logged into the system, which reduces manual errors and ensures inventory is accurate.
Step 5: Optimizing order fulfillment
Once you have established inventory tracking, it’s time to look for ways to optimize your fulfillment process, specifically how orders are picked, packed, and shipped.
Your WMS should allow for the following strategies to improve operations:
- Dynamic picking paths to reduce travel time.
- Automated packing suggestions based on size and weight.
- Real-time information integration with shipping carriers for rate shopping and label creation.
All of these optimizations will improve processing time, reduce labor costs, and increase accuracy, which results in better customer satisfaction, as well as improved operational efficiency.
Step 6: Utilizing analytics and reporting
After the initial setup of your WMS is completed and goes live, your analytics and reporting tools will be critical to maximizing the performance of your warehouse.
Most modern systems will have dashboards and KPIs that track:
- Picking accuracy.
- Inventory turnover.
- Order cycle time.
- Labor utilization.
- Space utilization.
With this information, warehouse leaders (yourself, your management team, etc.) can better identify bottlenecks, make data-driven decisions, and continuously improve warehouse processes.
When you take these steps in a systematic way, the WMS does not just facilitate your warehouse; it becomes a catalyst for scalable growth, smarter and greater decision-making styles, and enhanced supply chain performance.
How to use WMS for efficient warehouse management
A warehouse management system works best when it is part of daily workflows, not just part of the backend or the tool used to enable workflows. WMS should be the central communication medium that informs every action that takes place on the warehouse floor.
After the WMS is customized to your warehouse function and implementation processes, using the WMS for daily activities means aligning your processes with those included in a WMS, relying on technology to facilitate those processes, and consistently monitoring performance.
Here is how to best utilize the WMS in daily operations:
1. Daily workflows: streamline and standardize
A WMS works best if followed within a consistent and repeatable workflow for the complete warehouse environment. Each operational task related to the activity must follow a standardized process journey, from receiving the product all the way through shipping.
This is where a WMS can provide benefits for the warehouse functions:
- Receiving: Automatically match inbound shipments to purchase orders and flag and report variances, if any, during the putaway assignment process, all in real-time.
- Putaway: Help warehouse personnel assign stored units to storage locations based on size, frequency of product demand, and strategy of product storage.
- Picking: Assign work (selecting orders) using the most efficient picking method, such as wave picking, batch picking, or zone picking, to save both time and distance.
- Packing and shipping: Help confirm items before packing the order, create shipping labels automatically, and connect with carrier platforms for real-time, instant release to ship.
The more consistent your workflows are, the better your WMS will be at spotting inconsistencies, suggesting actions for improvement, and scaling to growth.
2. Mobile devices, barcode scanning, and RFID: power tools for efficiency
Mobile technologies are a key component of a productive WMS. Mobile handheld scanners or mobile devices allow your warehouse workers to capture data in real-time at every touchpoint.
Here's why this matters:
- A barcode scanner will allow your warehouse departments to be fast and accurate when receiving, picking, or cycle counting.
- An RFID (radio frequency identification) reader will allow you to take it even further, enabling your picked items to be tracked without line of sight and allowing you to scan multiple items simultaneously without requiring a barcode scan.
- Mobile apps and tablets allow your management team to monitor the underlying activity on the floor, assign workers to tasks, and address issues without being anchored to a desk.
Simply put, implementing mobile technologies will significantly increase speed, reduce errors, and drive warehouse performance.
3. Monitoring KPIs: data is your advantage
A modern WMS provides good data, but data only contributes to improvement if it's constantly reviewed and incorporated into decision-making. Defining and monitoring key performance indicators (KPIs) specific to your warehouse will provide a clear understanding of what’s going well and where you should focus your efforts.
Here are a few good KPIs to track:
- Picking accuracy: An indication of the percentage of orders that get picked correctly.
- Inventory turnover: An indication of how quickly inventory is sold and replaced.
- Order cycle time: Is an indication of how long it realistically takes from the start of the order until it is finished.
- Dock-to-stock time: An indication of how quickly goods from inbound shipments are put away and put in a position to be used.
- Labor productivity: An indication of the percentage of tasks that were completed by role, or shift.
With the ability to track these metrics, you will be able to notice inefficiencies sooner, recognize your top performers, and ensure you are spending labor in the most efficient way possible.
A WMS is only as effective as its deployment by users. By incorporating it into their workflows, equipping your team with mobile tools, and continually evaluating performance data, you will achieve significant improvements in accuracy, speed, and customer satisfaction.
Benefits of a WMS
When you implement a warehouse management system, one of the most important things to remember is that it's not about digitizing your operation--it's how it fundamentally changes the operation of a warehouse.
A WMS will bring measurable improvements in efficiency, cost, accuracy, and customer experience. Whether you operate a single warehouse or a global distributed network of facilities, a well-supported WMS will create a sustainable competitive advantage for your operation.
Let's talk about some of the benefits that a WMS brings.
1. Increased efficiency
WMS enhances warehouse productivity by automating manual processes, directing the workflows, and eliminating time and effort waste.
- Faster pick and pack: Smart route optimization and task assignments further reduce travel time on the warehouse floor.
- Enhanced automation: Technologies such as barcode scanning, auto-sorting & labeling reduce the number of manual entries, which can be time-consuming.
- Task prioritization: With WMS, the platform assigns work in real-time based on urgency, inventory availability, and order type.
The efficiency gained while using WMS ultimately leads to faster order processing times, increased throughput, and a reduction in friction or dissatisfaction in dispatching orders at peak times of the year.
2. Improved inventory accuracy
Reliance on manual inventory management can lead to stock shortages, overstocking, and lost sales due to unavailable stock.
The WMS improves inventory accuracy by providing real-time tracking and data validation.
- Real-time updates: Inventory levels will continuously adjust after the product is received, moved, picked, or shipped.
- Cycle counting: A continual, smaller inventory count can replace the disruptive periodic physical inventory auditing process.
- Reduced errors: Scanning tools reduce human error in the receiving and picking processes.
With the improvement of inventory accuracy, companies will be able to fill orders faster and avoid costly stockout or overstocking errors.
3. Enhanced customer satisfaction
Order accuracy and delivery time are potentially the largest drivers of customer satisfaction, and a WMS directly impacts both of them.
- Accurate orders: Reduce picking errors and deliver the correct products to customers.
- Faster shipping: Improve efficiencies through real-time data and eliminate delays in fulfillment.
- Order visibility: Customers can receive real-time tracking and updates on their order status.
Customer expectations are only increasing. According to a 2023 PwC report, 73% of customers say a good delivery experience is fundamental to their brand loyalty. A WMS will help you meet that customer expectation and scale your operations effectively.
4. Cost savings
The expenses for a WMS may seem daunting, but the implementation is relatively short-term compared to the savings from reduced operational and labor costs.
- Decreased labor costs: The automation of labor-intensive processes that occur in a warehouse, and the ability to prioritize labor, will lead to fewer overtime hours, and productivity per worker can increase.
- Holding costs for inventories decrease, as more information leads to a reduction in redundant inventory on hand and even a more efficient use of space.
- Fewer errors, therefore, fewer shipping costs: Reducing re-shippings and returns results in decreased logistics and customer service costs.
As these costs are compiled, a WMS can have a significant impact on a warehouse’s cost structure, and of course, allow for scalability and future growth.
A warehouse management system (WMS) can not only improve operations by increasing efficiency, improving accuracy, and enhancing customer satisfaction, but it can also be a strategic asset.
Choosing the right WMS
Not all warehouse management systems are the same. With so many different WMS options, the right WMS for your business depends on your operational model, budget, and long-term growth plan. Selecting the wrong WMS can result in wasted time through expensive delays, failed implementation, and poor adoption.
Selecting the right WMS can help streamline operations, scale with your business, and provide a considerable return on investment. When evaluating WMS options, here's what to consider:
Key decision factors
Before getting into vendor demos or features comparison, you must first identify your business goals and operational needs.
Start by asking some key questions:
- What problems are we trying to solve? (eg. Visibility of inventory, picking mistakes, and labor inefficiencies?)
- How many users will need access?
- What kind of integrations will be needed? (ERP, e-commerce, TMS, etc?)
- How complicated are our operations? (single site versus multi-warehouse, B2B versus B2C fulfilment)
- Will we need mobile or RFID capabilities?
Also consider scalability, will the system be able to handle increased volume, more SKUs, or new warehouses as you grow?
Cloud vs. on-premise
Among the many decisions you'll have to make is whether to go with a cloud-based WMS or an on-premise application.
Cloud-Based WMS:
- Hosted off-premises by the vendor.
- Accessed by a web browser or mobile application.
- Needs little to no in-house IT support.
- Updates and maintenance are handled by the vendor, reducing the need for in-house IT support.
Cloud WMS is typically quicker and more cost-effective to set up and implement, and is generally preferred for organizations that grow or operate remotely.
On-premise WMS:
- Has more control and customization.
- Requires operational IT infrastructure and an in-house IT team.
- Higher fixed cost but potentially lower long-term subscription fees.
On-premise WMS tends to be utilized more by enterprises with highly specialized workflows and rigid data compliance requirements.
Vendor evaluation tips
Once you determine your needs, when comparing vendors, be critical. Not just features, but also documents, reliability, and partnership.
You want to consider:
- Industry experience - have they got excellent industry (e.g. retail, manufacturing, 3PL) experience?
- Implementation assistance - will they assist (at least so that you will get adequate assistance) with data migration, training and/or go-live assistant?
- User interface and experience: Is it easy and intuitive to be built up by the seller warehouse team members?
- Integration - is the WMS open to integrating with current or future ERP, CRM, and/or e-commerce platforms?
- Customer Support - Does it offer 24/7 support, account management, and/or monitoring?
- Customer references - can you get referrals or case studies from similar and current companies?
In summary, do not merely consider the needs that exist today, but examine how the system will be able to assist you and develop during the following 3-5 years.
The selection of WMS is a strategic move. When you match it with your business strategies, when you do your homework to learn what your technical needs are, when you carefully qualify vendors, you will find yourself in good shape to make a good, future-proof investment.
Common challenges and how to overcome them
A warehouse management system can provide significant advantages, but it is not without obstacles. As you expand and upgrade a WMS for the first time or shift away from the WMS you've had too long, there are plenty of things that can go wrong during setup, integration, and usage. The good news is that most problems can be predicted and managed with sufficient preparation.
Below are the most common issues with WMS implementations, and many ways to overcome them:
1. Resistance to change
The challenge: Warehouse staff and even management can exhibit resistance to new systems, especially those that rely on manual processes or a legacy solution. This resistance can slow adoption, decrease productivity, and jeopardize the rollout.
How to address it:
- Start by communicating. Explain why the WMS is being implemented, what issues it will help resolve, and how it will help each specific role.
- Involve your employees early. Relying on frontline workers to help make the decision will help to ultimately gain buy-in.
- Provide training. Make sure that users receive hands-on, role-specific training. This will not only promote user confidence but also reduce the fear of the unknown.
- Assign champions. Identify super users or team leaders who can help guide others through the change process.
2. Data migration errors
The challenge: Inaccurate data from manual records, legacy systems, or spreadsheets can lead to catastrophic errors after the data is fed into the new WMS, resulting in inaccurate on-hand inventory, duplicate SKUs, or unsuccessful order processing.
How to address it:
- Clean your data before migration. Standardize naming conventions, delete outdated records, correct potential editorial errors, and validate key fields.
- Test in stages. It is easier to catch potential issues if you do test migrations using limited data sets.
- Create backups. Always keep your original data (and key fields) and original configuration settings in some form in case retraction is necessary.
- Consult with the vendor. If you are uncertain about data mapping, the vendor often provides data mapping services to eliminate problems later.
3. Integration challenges
The challenge: A WMS typically does not function independently; it must integrate with your ERP, e-commerce platform, CRM, TMS, or accounting system. A lack of integration creates data silos that cause delays in order fulfillment and mismatches in inventory.
How to address it:
- Determine integration points in the planning phase, not in the post-implementation phase.
- Use APIs and/or middleware. Ensure that you use a WMS that simplifies complexity by leveraging modern integration tools.
- Test any connection. Before going live, run full workflows (e.g., order-to-ship) to be able to verify data flows to the different systems.
- Collaboration with experts. Engage consultants who can assist with integrating your systems.
4. Insufficient training and onboarding
The challenge: If employees do not know how to use the WMS, even simple tasks such as receiving product or picking product can be delayed or go wrong completely. An under-trained user can create inconsistencies in data or disrupt workflow.
How to address it:
- Provide training for every establishment role, not just administrators or managers.
- Use real-life examples during training, instead of just theory.
- Have a knowledge base that uses calls/vaults, FAQs, and cheat sheets.
- Schedule refresher training after go-live to reinforce daily habits and address any knowledge gaps.
Training is not a singular activity. Continuous learning ensures that your team grows with the system.
5. Misaligned expectations
The challenge: Leadership may sometimes expect "on day one" ROI or 100% automation. Once those expectations aren’t met, confidence in the system might falter, even if the implementation was done exceptionally well.
How to overcome it:
- Set realistic goals with every implementation phase (e.g., reduce picking error by 20% in 3 months).
- As far as timelines and limitations for stakeholders, it is essential to clearly outline them.
- Celebrate the small wins to build early momentum and internal support.
WMS implementation success is a journey. While some expectations have a time frame, early expectations set for stakeholders are crucial in developing the full value that will be realized over time.
When considering a successful warehouse management system (WMS) implementation, you don't just think about technology; it's also about people, process, and planning to anticipate and avoid potential hurdles down the road.
You should expect challenges, and being proactive about these common obstacles could help you set yourself up for success not only in implementation but also in the outcomes of that implementation.
How do you optimize WMS performance long term?
A WMS implementation is only half the battle. The value from a WMS comes from its ongoing performance. A successful WMS "launch" is just the beginning. Optimizing the ongoing value and return on your WMS investment means having a long-term perspective, which is focused on a culture of relentless improvement, ongoing user engagement, and a more strategic use of system capabilities once the system goes live.
Here are practical considerations to keep your WMS performing well every year:
Revisit KPIs regularly
Why it matters: Your warehouse operations evolve, and so should your metrics. What mattered when you went live may not be your primary driver today.
What to do:
- Establish a cadence to review KPIs (for example, pick accuracy, inventory turns, and dock-to-stock time) at least quarterly.
- Align metrics with business goals (for example, fulfill orders faster, achieve better accuracy, or reduce returns).
- Use the insights to drive operational changes or tech enhancements.
For example, if a company starts by improving its KPIs for order accuracy, but later shifts its focus to reducing cycle time for high-volume SKUs.
Evolve your processes with the system.
Why this is important: As time goes on, it's possible your warehouse design, staffing model, or product mix will change. Leaving the WMS settings unchanged can lead to inefficiencies.
What to do:
- Perform regular process reviews and identify specific areas where workflows or configurations need to be updated.
- Make changes to storage rules, picking logic, and replenishment strategies based on SKU velocity or seasonal trends.
- Include a diverse cross-functional team (ops, IT, supply chain) as part of periodic reviews, at least quarterly.
Use WMS data beyond the warehouse.
Why it matters: The information from your WMS can benefit more than just warehouse personnel. When leveraged across departments, these findings can enhance supply chain decisions.
What to do:
- Share real-time inventory and order flow with sales and customer service.
- Utilize SKU movement reports to inform purchases and demand planning.
- Have the warehouse feed data into business intelligence (BI) dashboards for leadership visibility.
Build a continuous improvement culture.
Why it matters: A WMS is not a piece of static software; rather, it is an active system. A warehouse running on a WMS successfully treats it as a constantly evolving system with ongoing improvement.
What you can do:
- Encourage feedback loops to enable employees to suggest process improvements.
- Host occasional kaizen workshops to identify wasteful activities.
- Offer prizes to teams or individuals for identifying process smart optimizations within the system or workflow.
Plan for upgrades and innovation
Why it matters: Technology is changing rapidly. WMS platforms are continually updated with new features and functionality, including AI-based labor forecasting and robotics capabilities.
What you can do:
- Check in with your vendor regularly to see product updates.
- Continue to learn about emerging technologies (e.g., automation, IoT, RFID advancements) that your WMS can support.
- Pilot new features in controlled testing before going wide-scale.
The key to maintaining a long-term successful WMS is not large enterprise-wide sweeps, but a history of systemic progressive changes that continue to align your WMS to your business needs. Your WMS can continue to create value, flexibility, and efficiency long after the initial implementation if you have the culture and processes in place.
A warehouse management system is more than just a system; it is a powerful competitive advantage that has a very real influence on other customers and the bottom line. Fast, accurate, and low-cost order fulfillment differentiates competitors, and the WMS provides businesses with the right combination of tools to deliver consistently and grow with confidence.
If you are a supply chain executive planning your first WMS deployment, or you are a warehouse operations manager wanting to improve your daily operating efficiencies, the right supply chain WMS and practices will no longer make you a cost center, but a performance engine.
The best time to start smarter warehouse management is yesterday; the next best time is now.
Frequently asked questions
A warehouse management system (WMS) is a dedicated IT tool that manages all warehouse operations, including inventory management, order picking, receiving, put-away, and shipping. In contrast, enterprise resource planning systems (ERPs) provide a wider scope of activity, integrating multiple business functions, including finance, purchasing, and human resources, that also provide some level of inventory and/or supply chain management functionality. ERPS can provide some warehouse management capabilities, but WMSs will deliver greater, real-time management of warehousing functions. Quite frequently, organizations require both systems to take advantage of their dissimilar strengths.
The duration of a WMS implementation can differ dramatically depending on the size of the warehouse, the nature of the operation, and the business’s readiness. For smaller or less complex warehouses, implementation may take two to four months. Bigger facilities with numerous locations may take six months to a year (or longer) to implement. In addition to warehouse size and complexity, the extent of data migration, training, testing, and any integrations with other systems (such as ERP or TMS) can play a significant role in the timeline.
Absolutely. In fact, small and medium-sized businesses can realize significant ROI by implementing a WMS sooner in their business. There are several cloud-based WMS solutions that are affordable, scalable, and require minimal to no IT resources for implementation. Investing in a WMS provides many small businesses with better accuracy, reduces labor costs, and can better manage increasing order volume as the business continues to grow.
Although a WMS can generate substantial ROI in the long run, there are expenses that businesses will overlook in the planning stages. They could include items such as data cleanup and migration to a WMS, employees learning how to use your WMS, a budget for purchasing hardware (barcode scanners, mobile devices, etc.), potentially many hours of custom integration with other systems, and hosting and maintenance fees if you buy a WMS that requires hosting. You'll want to work closely with your vendor to ensure that, while it's likely too early in your planning phase to know, you'll have a clear understanding of the total cost of ownership upfront.
Most cloud WMS providers definitely implement security features such as encryption, access controls, and continuous monitoring of the cloud environment. In fact, they are often more secure than on-premises solutions, as the cloud version automatically implements updates, patches, and enhanced security protocols without requiring any action on your part. It's recommended to engage a vendor that can show they have implemented industry-recognized security standards (such as ISO 27001 or SOC 2) to ensure your data is secure.
WMSs deploy updates usually on some regular cadence, quarterly or semi-annually, depending on the vendor. Updates can be security patches, improvements to performance, or the release of new features. Cloud-based WMS solutions will automatically update for users to use, and thus will always have the latest version. For on-premise systems, updates will need to be scheduled, tested, and pushed. Regular updates are key to continuing to maintain performance, interoperability, and improved function over time.