How to Set Up a Warehouse Management System (WMS)
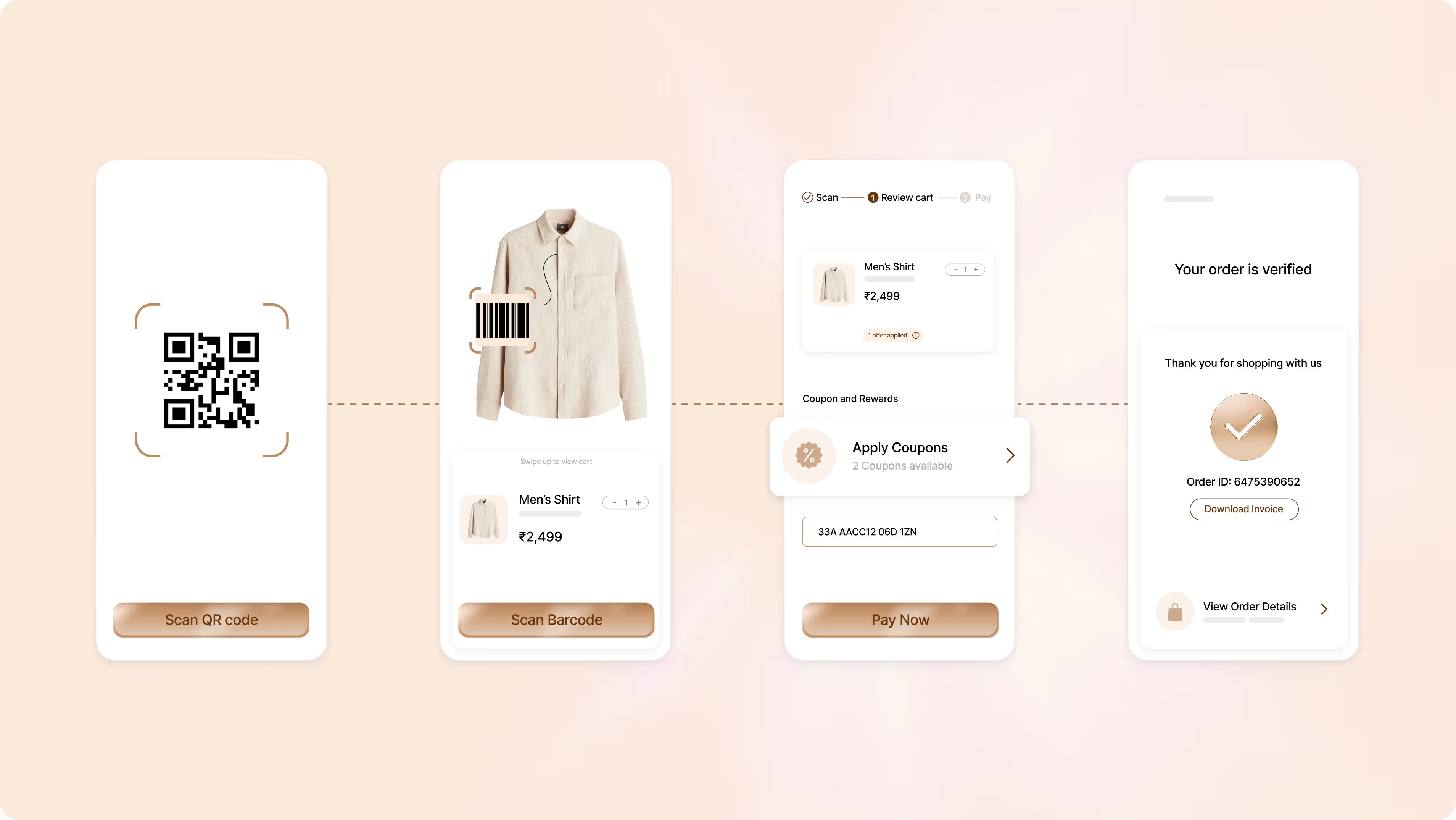
Although considerable advancements in technology have been made, many employees in warehouses still rely on manual processes (e.g., manually tracking inventory for hours through spreadsheets, double-checking orders, and communicating across different systems).
When customer expectations rise and supply chains become complex, operational inefficiencies quickly become competitive inefficiencies. Organizations must find alternative ways to efficiently operationalize warehouse workflows at the lowest possible costs and meet their commitment to deliver orders on time.
There are ways to simplify warehouse operations, enable centralized and automated processes, and track inventory more efficiently using a warehouse management system (WMS), which can enhance a company's operational excellence by improving accuracy, speed, and inventory management.
This guide will provide a comprehensive understanding of what a WMS is, why automation should be considered, the various systems available, the associated costs, expected timelines, and the potential look of implementing or building a system that complements your business goals.
What is a warehouse management system?
A warehouse management system is primarily software that helps companies operate their warehouses more efficiently. This software tracks the location of products, their movement in and out of the warehouse, and which process or zone they are in at any given time. Instead of spreadsheets and manual logs, a warehouse management system ensures that the correct item is in the correct place and at the correct time while improving the speed and accuracy of warehouse operations.
Imagine a technology that automatically provides you with the amount of inventory available, the location of each item, and what needs to be packed or shipped next. A warehouse management system, or WMS, provides these capabilities and more.
What does a WMS do?
{{demo_wms="/styles/components"}}
A warehouse management system performs many of the daily tasks that happen inside a warehouse. Some of its key functions include:
- Inventory management: Keeps track of the quantity of inventory and its location.
- Receiving and putaway: Helps place incoming items in the correct storage or putaway area for rapid access.
- Order picking and packing: Design the most efficient path for warehouse employees to pick and pack items for delivery.
- Shipping: Performs the labeling, packaging, and shipping part of the process.
- Workforce management: In advanced or integrated WMS platforms, this feature helps allocate tasks to employees and may monitor productivity levels.
- Reporting and analytics: Provides an overview of your warehouse's operation and highlights areas for improvement.
How is a WMS different from other systems?
At this stage, it is easy to integrate a WMS with other business software, such as ERP or basic inventory management systems; each system manages products and information, but more narrowly in different areas.
- Inventory management software is the most basic, allowing someone to track their inventory and notify them when their stock is running low.
- Enterprise resource planning (ERP) systems offer broader functionality by integrating inventory management with accounting, finance, human resources, and sales. However, the inventory features in ERP systems are often more basic compared to those in specialized warehouse management systems (WMS).
- A WMS manages the warehouse operations specifically at the warehouse pace, complexities, and precision of storage, picking, packing, and shipping.
Here’s a quick comparison:
In many cases, a WMS can be used in conjunction with an ERP or integrated into one, depending on the level of sophistication required for the business's logistics needs.
Why is automation needed in a warehouse?
Today’s warehouses are under increased pressure to speed up operations, operate more accurately, and accomplish more with fewer resources. As customer expectations continue to rise, especially in B2B and ecommerce, warehouses simply can’t keep up with customer demands to fulfill orders quickly with manual processes in place.
Common warehouse problems
Many warehouses still rely on paper-based processes, spreadsheets, and legacy software. While paper-based processes and spreadsheets were once adequate, some have serious potential downsides, including:
- Human errors: Relying on manual processes can lead to serious issues, such as human errors in data input, selecting the wrong product, or misstoring inventory.
- Delays in orders: Without automation, locating and shipping products will take longer than necessary, particularly during peak times.
- Accuracy of inventory: Without real-time visibility, inventory can easily be out of stock (losing sales) or overstocked (lost margin).
- Inefficient labor: Workers are often tasked with performing mundane and repetitive tasks that could be automated.
The benefits of warehouse automation
Automation incorporates systems and technologies that reduce labor, facilitate faster operations, and lower costs. The most common systems include barcode scanning, RFID, conveyor systems, robotics, and, most importantly, a warehouse management system (WMS) that integrates warehouse operations and can connect with enterprise systems like ERP to support broader business integration.
Some of the main benefits in automating warehouse functions include:
- Higher accuracy: Automation reduces human mistakes in tracking inventory and order picking.
- Faster process: Automation speeds up receiving, picking, packing, and shipping, fulfilling tight delivery windows.
- Lower labor cost: Many repetitive tasks (such as data entry and label printing) can be handled by systems, allowing staff to focus on more valuable work.
- Real-time visibility: A centralized system can provide real-time updates on inventory, shipments, and the workforce.
- Scalability: Automated warehouses can scale to fulfill even more orders without requiring a greater proportionate increase in headcount or cost.
Automation is not about replacing workers; it’s about helping workers with better tools. For instance, a picker with a mobile device, who a WMS directs, can perform tasks much faster than one who works off paper.
As companies grow, automation is less of a competitive advantage and more of a requirement. If they do not automate, warehouses may fall behind in both cost and customer satisfaction.
Types of Warehouse Management Systems
Choosing the right type of warehouse management system (WMS) is one of the most critical decisions when looking to optimize warehouse operations. Understanding the distinctions can go a long way in selecting the right option for your company and its size, structure, and future goals.
Here are the four most common types of WMS:
1. Standalone warehouse management system
A standalone WMS is a solution specifically designed to manage warehouse operations. In general, it has core functionality in inventory controls, receiving, picking, packing, and shipping. A standalone WMS is commonplace for businesses that need more control over their warehouse workflows but do not require an entire enterprise suite.
Best suited for Mid-sized companies with expanding fulfillment operations, small businesses seeking scalable solutions, and third-party logistics (3PL) providers without an existing enterprise system.
2. Supply chain execution (SCE) modules
Certain businesses operate with WMS supported by a broader supply chain execution system collaboration platform. Such systems operate on a single platform, planning not only the warehouse use but also transportation, order processing, and supply chain visibility.
Best suited for: Enterprises with complex logistics networks and a need for high supply chain coordination.
3. Integrated ERP systems with WMS modules
Today, many enterprise resource planning (ERP) platforms provide functions of a WMS in a module. In this situation, the warehouse operations and activities are now part of a larger ecosystem with other departments like finance, human resources, procurement, and sales.
Best suited for large companies looking for a single system that connects all departments and operational functions.
4. Cloud-based warehouse management systems
Cloud-based WMSs are web-based software systems that are hosted on the web and can be accessed by a web browser, a mobile app, or both. These systems have grown in popularity in recent years due to the flexibility they offer businesses, as well as their affordability and scalability.
Best suited for businesses that need a WMS with quick deployment, scalable functionality, and remote and flexible access.
Each type of WMS system can serve very different operational needs. For example, a small-scale B2B wholesale distributor may only need a simple cloud-based WMS or a standalone WMS. In contrast, a large multinational distributor will require some ERP-level integration with the WMS at an operational level and need visibility across the entire supply chain. Choosing a WMS comes down to first understanding where your current processes are today and what your future growth goals are.
WMS options: ready-made vs custom build
Once a company has opted to utilize a warehouse management system, the next big decision to make is whether to use an off-the-shelf solution or build a custom-designed system from scratch. Both approaches have their benefits and limits, depending on the size, complexity, budget, and roadmap of the company.
1. Off-the-shelf/WMS solutions
Off-the-shelf (also referred to as ready-made) WMS systems are pre-engineered software that are designed to work for a wide variety of companies. These types of applications come with built-in features, practices, user interfaces, and some support interfaces within the software itself, such as carrier and ecommerce integrations.
Best for: Companies looking for implementation in a reasonable time frame, proven results, and a lower up-front investment.
Benefits:
- Speed of implementation: Many commercial systems can be implemented in weeks rather than months.
- Reduced upfront cost: No need to pay for developers or ongoing custom development.
- Reliability: They have been validated across many industries.
- Vendor updates and support: Vendors typically provide new features regularly, along with customer support.
Drawbacks:
- Limited flexibility: Organizations must work within the confines of what is available in the system.
- Limited customization: Organizations may require very niche features that require expensive customization.
- Vendor lock-in: If all your data and operations are dependent on a single provider, it may be challenging to switch to a different platform.
2. Custom-built WMS solutions
A custom WMS is developed by either a software development team or from a vendor provided to a company that designs for a company’s specific needs.
A custom WMS is developed from the ground up, so the company has complete control over the features, design, and integrations. That said, this means the company may also assume long-term maintenance responsibilities in addition to potential tech debt.
Best suited for: large enterprises and businesses that have specialized operations, complex workflows, or a long-term growth strategy that cannot be satisfied by standard "out of the box" systems.
Benefits:
- Total customization: Allows you to tailor every element of the system to your business processes.
- Scalable architecture: Designed to accommodate future expansion of the system, future business growth, and future sophisticated automation opportunities.
- Competitive differentiation enables best-in-class innovation and provides the opportunity to create a WMS tailored to unique business models.
Drawbacks:
- Time to develop: Custom WMS typically require design, build, and testing periods from several months to a year.
- Expense: Both development, testing, security, compliance, and maintenance require a planned investment.
- Ongoing technical accountability: In-house or external developers or technical support will need to be involved in the design, future enhancement, and support.
Which one is better?
For the majority of businesses, especially those that conduct standard warehouse processes, a fit-for-purpose WMS is typically the most cost- and time-effective option, as it can be deployed relatively quickly and consists of existing and built-in industry expertise.
However, businesses should also consider whether the system will be able to scale with growth moving forward. These solutions are quicker to implement and come with a lot of industry knowledge built in.
However, organizations that have significant customization requirements, already have specific and unique workflows established, or plan to scale rapidly, may find that a customized system is better in the long term if they are fully resourced with budget and internal resources.
It's all about matching the technology to actual business needs, not just what they need now, but what the organization sees in 5–10 years.
Choosing to implement a warehouse management system is a difficult decision in both a logistical sense and a financial sense. Whether a business decides to go with a packaged solution or a custom one, knowing the anticipated cost and time to develop helps reduce surprises and allows for improved planning.
Why invest in a custom WMS?
Custom WMS may be considered by businesses that have very specific practices in their workflows, multiple warehouses that are part of a network, or a unique business model. Custom WMS has the advantage of greater flexibility and control over how the system operates, how it integrates with other business systems, and how it scales.
But again, a cost is involved in that flexibility.
Building a warehouse management system from the ground up is similar to launching a software product; it requires careful planning, coding, testing, training, and ongoing maintenance. Additionally, it must account for regulatory compliance and risk mitigation, which are critical in warehouse operations.
Custom WMS cost range:
- Simple WMS (basic inventory tracking and warehouse operations): ~$30,000–$100,000, depending on location, features, and vendor.
- Medium complexity (multiple warehouse locations, role-based access, custom integrations): $100,000–$250,000.
- Enterprise-level (automated workflows, multi-language/multi-region support, advanced analytics): $250,000–$500,000+.
These costs typically cover:
- Requirements gathering.
- UI/UX design.
- Software development.
- Testing.
- Deployment.
- Post-launch support.
Development timelines also vary:
- MVP (minimum viable product): 4–6 months.
- Full version: 9–18 months, depending on feature set and integration depth.
Why use an online or ready-made solution?
For organizations that prefer to rapidly and reliably improve their warehouse management, either a cloud-based or an on-premises system is usually most effective. These systems include widespread features already created and maintained by experienced partners in the software world.
Costs for ready-made WMS:
The costs for ready-made WMS for any of these features follow a three-part range of
- Monthly license fees can range from $300 to over $10,000, depending on the number of users, warehouse volume, and feature complexity, particularly for enterprise-grade WMS platforms.
- Set-up fees: The one-time fee can take anywhere from $1,000–$10,000 for onboarding, training, and configuring the system.
Time to Implementation:
Most off-the-shelf WMS will be implemented and running in 2–6 weeks, especially when the integrations are already built around the platform.
These systems are a great fit for small and mid-size organizations that want to modernize quickly and without a large investment.
Key cost drivers to consider
Whether custom or ready-made, several factors influence the final cost of a WMS:
To summarize, although custom WMS development is a big investment with promising returns for large or complex operations, the vast majority of businesses can achieve better results more quickly and with less risk using ready-made systems.
Factors to consider when designing a WMS
Regardless of whether you are developing a custom warehouse management system or a complex, ready-made solution, the design and architecture are crucial to the system's ultimate success over the long term. In fact, a well-designed WMS doesn't just manage inventory; it provides the business with the ability to grow, be nimble, and compete more effectively.
Here are the most important considerations:
1. Scalability
An effective WMS can evolve with the business. It may allow for expansion into multiple warehouses or facilities, increasing inventory and order volumes, or adding automation or robotics, such as conveyors. The WMS should be designed to adapt to your changing business needs, rather than requiring a complete system overhaul.
- Look for a modular design that allows you to add or change functionality without interfering with existing processes.
- Think of multi-warehouse support, role-based permissions, or dynamic storage.
2. Real-time data synchronization
Today's world of supply chain decisions is based on reliable, accurate data, and that data is based on real-time. Your WMS should update data for inventory, order status, and operational performance in real-time.
- Capture live data with barcode scanning, RFID, and IoT sensors; when you define the inbound and outbound movement of goods, it establishes clear record-keeping via your WMS.
- Integrate with your sales, procurement, or transportation systems with APIs or webhooks.
- Don't rely on batch updates or static reports; rather, they create delays and misalignment.
3. User roles and permissions
Employees, supervisors, managers, and IT admins will all engage with the WMS in different ways. Assigning appropriate user roles provides both security and efficiency.
- Establish permissions based on job function.
- Restrict what users see as only the data and tools they will need to complete their work.
- Support audit trails to track usage and limit exposure to unauthorized changes.
4. Integration with ERP, shipping carriers, and ecommerce platforms
A WMS should never function in a silo. The closer your WMS can be to connecting seamlessly with your other systems, the less time you and your team will have to spend on manual processes, and there are no data silos.
Key systems to integrate with:
- ERP systems (NetSuite, SAP, Microsoft Dynamics) to obtain and sync with financial, procurement, and demand averages.
- Shipping carriers (FedEx, UPS, DHL) to calculate real-time rates, generate labels, and track shipments.
- Ecommerce platforms (Shopify, WooCommerce, Magento) to combine order information and inventory levels.
Integrating each of these systems means everyone in the company, from the warehousing staff to the sales staff, is working from one source of information.
5. Security and Compliance
A WMS (warehouse management system) processes operational data that is often sensitive, including elements such as product pricing, supplier information, and customer orders; security should be treated as a critical priority when selecting or developing a WMS.
- Ensure the system features role-based access control, end-to-end encryption, and a built-in data backup mechanism. When evaluating cloud-based systems, verify that the company is compliant with industry standards such as SOC 2, ISO 27001, and GDPR.
- Also, include details for data loss prevention measures in the application to protect peak volumes during busy times of the season.
The design considerations are not just technical or operational comforts; they influence the effectiveness of the warehouse on a day-to-day basis, the scalability of the organization, and its adaptability and resilience under change, uncertainty, and disruption.
Top 5 warehouse management systems
The warehouse management system space is crowded with options for organizations of all sizes, complexities, and industries. Some offerings of systems were specifically for small businesses, providing a simple WMS, while others offered solutions for large companies with multiple sites and complex logistics. Here are five solid WMS offerings that are receiving recognition among vendors for credibility, usability, and market share.
1. Fynd WMS
Fynd WMS is primarily a cloud-based Warehouse Management System for fast-growing ecommerce and retail brands. The features include real-time inventory visibility, barcode scanning, and linking order sync across multiple sales channels, including Amazon, Shopify, and Flipkart. The WMS is particularly suitable for brands that utilize either a D2C or omnichannel fulfillment model.
The Fynd WMS enables efficiency in operations and accuracy in orders, with setup and scaling streamlined, which is ideal, especially for businesses with fluctuating inventory and order volumes.
2. NetSuite WMS
NetSuite’s WMS is part of Oracle’s larger ERP solution family and is best suited for medium to large companies that require sophisticated integration between warehousing, finance, procurement, and supply chains.
It has sophisticated features like wave picking, zone picking, cycle counting, mobile RF barcode scanning, and cartonization logic, but cartonization may not apply to all NetSuite ERP editions (or it may require a third-party integration provider).
For companies utilizing NetSuite ERP, the WMS module is a powerful solution that provides a seamless extension, connecting all warehouse activities to backend systems. This helps reduce manual work in the warehouse and speeds up the order fulfillment rate.
3. Fishbowl
Fishbowl is a popular WMS and inventory solution primarily for manufacturing and wholesale distribution companies, but it also covers some common gaps for businesses using QuickBooks with advanced features for inventory control, order management, and production tracking capabilities. It offers the ability to work order creation, tracking raw materials, and multiple locations.
Fishbowl is suitable for organizations that want good inventory controls but are not yet ready for an enterprise-level ERP solution, as it can be run on-premise or cloud deployment (your business choice).
4. Odoo Inventory
Odoo Inventory is part of the larger Odoo ERP package, which emphasizes a more modular approach to managing your business. The warehouse management module is well-positioned for small- to medium-sized businesses looking for a relatively inexpensive, flexible, and customizable software solution.
Odoo offers a comprehensive range of appealing features in the Odoo Inventory/WMS module, including barcode scanning, intelligent put-away, intelligent demand forecasting, and picking route optimization within the warehouse.
Odoo is flexible enough for businesses to start with the inventory management software alone and then expand into areas such as accounting, sales, and maybe even HR as required. Thus, small- and medium-sized businesses can benefit from good ERP-level coverage without needing to commit to expensive and rigid enterprise systems.
5. Zoho Inventory
Zoho Inventory provides software and services aimed at small businesses and start-ups looking for a simple and budget-friendly stock, sales, and order management tool. Zoho Inventory has many fundamental warehouse functions, such as inventory tracking, multiple channel order processing/management, automated purchasing, as well as shipping integration with leading carriers.
Even though it lacks the more advanced automation functionality of enterprise-class tools available, Zoho still hits its mark in simplicity, user-friendly interface, and integration with other Zoho tools. Zoho Inventory is likely to be particularly valuable to companies that have just begun their digitization journey and would benefit from a system that does not need dedicated IT support.
These five systems cover a variety of use cases, ranging from high-velocity e-commerce to manufacturing and lean startups. Each system offers a different pricing model, deployment style, set of features, etc. The best option depends on the unique operational challenges and long-term outcomes of the business.
How to build a warehouse management system
When workflows, legacy systems, or operational needs are so unique that even a commercially available, off-the-shelf WMS cannot meet their needs, companies may pursue developing a warehouse management system from scratch. A specific development project will provide you with full control, deep integrations, and an optimized system for automation, but a successful development will require planning and input from across the organization, as well as extensive commitment.
Here’s a step-by-step outline of how a custom WMS is generally built:
1. Business requirements gathering
A deep understanding of what problem a system is solving is the basis of a successful system. In this phase, you need to understand how a warehouse currently operates and look for gaps in the process, inefficiencies in the process, and/or areas for automation of manual work.
Key activities include:
- Conducting interviews with warehouse managers, supervisors, and staff,
- Documenting what's taking place currently (receiving, picking, packing, shipping, and inventory adjustments),
- Identifying pain points (stock-outs, misspeaks, orders that are delayed),
- Setting goals (reduce picking time by 30%, reduce items in inventory from 25% down to 2%).
This step is to make sure that the WMS is set up based on business needs (not just technical needs).
2. Workflow design
Once you have defined the requirements, you now need to design how the system will operate. The design will require you to describe the user flows the logic of the various processes, and optimize your warehouse layout.
During the design phase, it is important to consider the following:
- What happens when new stock is received?
- How is an item found, picked, placed in a box, and packed?
- What are the approval workflows for stock adjustments or returns?
- What happens when there is an error or an exception occurs?
You will also have tools such as process maps, wireframes, and warehouse layout simulations to help you visualize the system before you write any code.
3. Choosing the right tech stack
The technology stack will help determine how closely the WMS meets performance, scalability, and integration with existing systems.
For example:
- Backend: Node.js, Java, Python.
- Frontend: React, Angular, Vue.js.
- Database: PostgreSQL, MongoDB, MySQL.
- Cloud infrastructure: AWS, Azure, Google Cloud.
- APIs: RESTful or GraphQL for integration with ERP, ecommerce, or shipping platforms.
- Mobile support: For handheld scanner interfaces (Android/iOS apps or PWAs).
Ultimately, the technology stack is based on project scope, budgets, and the existing tech ecosystem.
4. Development phases (from MVP to full version)
To minimize risk and optimize value-added speed, custom WMS projects tend to roll out increments. Many projects will start with a minimum viable product (MVP) that will typically include only the most crucial features. The typical MVP features are:
- Inventory management with SKU, lot, or serial number tracking.
- Basic inbound and outbound workflows.
- Barcode tracking with handheld devices.
- Real-time inventory visibility.
- Basic reporting dashboards.
Once the MVP has been tested and validated we can phase multiple other modules including order routing, warehouse slotting, time & labor tracking, and predictive analytics.
The incremental approach provides opportunities for faster roll out, continuous feedback, and alignment with business.
5. Testing and rollout
Prior to going live, a comprehensive test of the system under realistic conditions needs to be performed. This includes the following:
- Unit tests: Testing to make sure the individual features are working correctly.
- Integration test: Testing to make sure that the modules and any external systems can communicate with one another.
- User Acceptance testing (UAT): Real users pretend to do their day-to-day tasks to test how usable and effective the WMS is.
It's also important to do a pilot run, often in one warehouse or department, to identify any problems before deploying the system across the organization. You don't want to disrupt operations across the business.
Finally, staff training or onboarding is needed. Even a well-designed WMS will fail if users are unsure how to use it effectively.
A warehouse management system is vital to the improvement of accuracy and the reduction of delays associated with warehouse operations. Whether a business is automating repetitive tasks or adding end-to-end visibility of inventory while in transit, a rational WMS can greatly advance operational efficiency and productivity, ultimately leading to better customer satisfaction.
Whether to use a pre-built or custom-built warehouse management system depends on the size, complexity, available in-house technical capabilities, and future scalability of your business. Prebuilt warehouse management platforms are generally quicker to implement and lower in cost to set up.
Custom-built WMS may allow for greater flexibility and features tailored to your business needs. In either case, investing in the right warehouse management system will help facilitate a more agile, scalable, and efficient supply chain.
Frequently asked questions
A WMS boosts inventory accuracy, increases the speed of order processing, reduces manual errors, and lets you see your warehouse operations in real-time. It can help businesses reduce operational costs and improve efficiency and customer satisfaction.
In most cases, a packaged WMS will be the best solution because it typically takes less time to deploy and requires less capital upfront. Custom WMS will be better suited for companies with very specific workflows or those with very specific integration needs that packaged solutions cannot provide.
Most modern WMS solutions are designed to integrate with an ERP system, as well as with carriers and e-commerce platforms like Shopify, WooCommerce, and Amazon. Like ERP solutions, WMS integrations enable data to flow seamlessly throughout the supply chain.
Typical challenges include high up-front costs, considerable resistance to change from warehouse workers, integration issues with legacy or a combination of legacy systems, and sometimes incorrectly estimating the expected training required for a smooth transition.
Cloud-based WMS platforms provide more flexibility, can be simpler to stay up to date, and generally require less effort to maintain than on-premise systems. They can also be easier to scale as the organization grows, which is one of the main reasons so many companies are using them today.
To help with your WMS scaling, your chosen WMS should support multi-warehouse operations, support high order volumes, and have easy integration with other business tools. Systems that have a modular design or an API are generally more suitable for the future.