Fleet Management Cost Analysis: A Comprehensive Guide
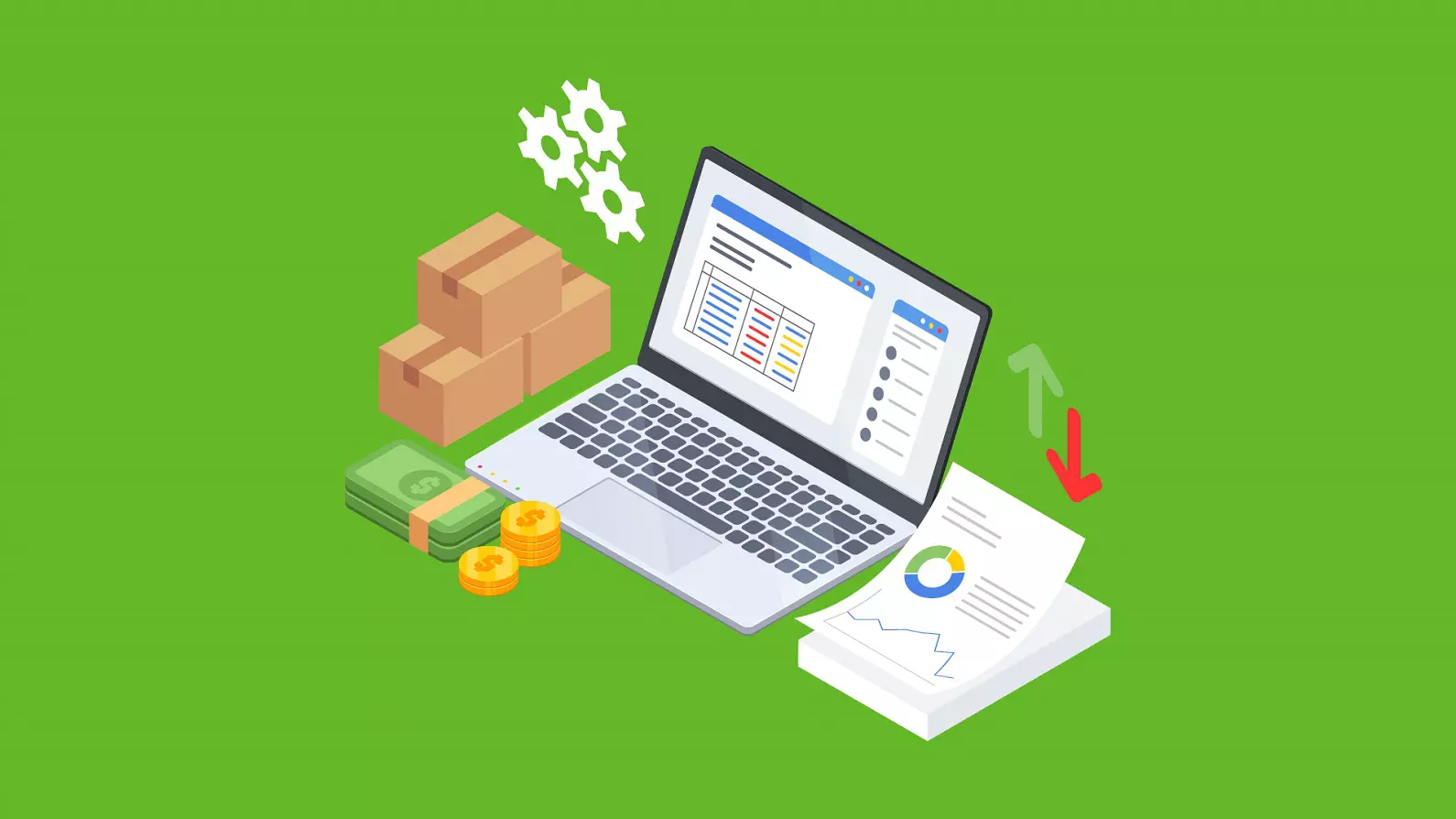
There’s always something pressing—scheduling drivers, handling late deliveries, dealing with a check engine light. The urgent stuff gets handled. But the slow, quiet creep of rising costs? That often flies under the radar.
Fuel prices edge up. Tires wear out faster. A truck sits unused for three weeks. Repairs start stacking up. Over time, those hidden costs pile on and eat away at your margins.
That’s where things get tricky. Without a clear system for tracking every dollar that goes into your fleet, it’s nearly impossible to spot what’s draining your budget—or fix it.
This guide digs into that side of fleet management:
- What your fleet is really costing you—down to the vehicle
- Where the money’s going, and why it’s adding up
- How to track, break down, and actually use cost data to make smarter decisions
Let’s begin.
What is fleet management cost analysis?
It’s a way to keep track of what a company spends to run its fleet. That includes fuel, service work, repairs, insurance, and even the drop in value as vehicles age. All of it adds up, and this process helps put those numbers in one place. The goal is to see where the money’s going, not just this month but over the long run.
Businesses use it to stay ahead of problems. A few small costs here and there might not seem like much, but they build up fast. This kind of analysis makes it easier to catch patterns like a truck that breaks down more often than others or routes that burn through too much fuel. Once they see what’s happening, they can decide what needs to change. Major cost factors in fleet management are
1. Fuel costs
Fuel costs aren’t just high they’re unpredictable. A route that made sense last month might be too expensive this month if fuel prices shift. But it’s not just about prices. How the vehicle is driven matters.
Hard braking, idling in traffic, or taking a long way burns more fuel than needed. Some fleets hand out fuel cards to track spending or use GPS tools to keep an eye on habits. It’s not about micromanaging drivers, just understanding where fuel goes and cutting waste where possible.
2. Maintenance & repairs
You can’t run a fleet without expecting something to break. Tires wear out, engines act up, and brakes don’t last forever. Some problems pop up out of nowhere, but a lot of them can be avoided with regular checkups.
Skipping a basic service might seem fine at the moment, but it often leads to a bigger repair later. Many teams now rely on digital logs and alerts to stay on track. It’s not just about keeping the wheels turning—it’s about doing it without surprise bills.
3. Vehicle acquisition & depreciation
Buying a new vehicle? That’s a big decision. But what’s easy to forget is how fast that value drops once the vehicle hits the road. Depreciation can be sneaky—it chips away at a resale value every mile and every year.
Fleets have to figure out when to sell when to hold on, and which vehicles lose value slower. It’s a balance. You don’t want to hang on too long and get stuck with a money pit, but you also don’t want to replace it too soon and waste money.
4. Compliance & insurance
There’s a lot of paperwork behind keeping a fleet legal. Safety checks, registration renewals, permits—it adds up fast. And if you miss something, you’re hit with fines or worse. Then there’s insurance, which is always watching your every move.
One accident or violation can raise rates across the board. Good recordkeeping, proper training, and staying organized can actually bring those costs down. A few missed details can cost more than people expect, so fleets that stay ahead of deadlines tend to spend less in the long run.
5. Labor costs
Drivers are a major part of the budget—and not just their paychecks. Overtime, training, sick days, turnover… it all adds up. If drivers sit in traffic or wait too long at delivery points, the company still pays for that time.
That’s why smarter scheduling and better routing matter. Fleets that plan well often need fewer drivers to do the same amount of work. And keeping good drivers longer means spending less on hiring and onboarding. Labor costs aren’t just wages—they’re everything that happens around the wheel.
Why cost analysis is important
1. Identifies cost-cutting opportunities
Without proper analysis, a lot of hidden expenses go unnoticed. These could be small, recurring repair bills on older vehicles or spikes in fuel use on specific routes. On the surface, they seem like isolated issues. But when seen together through cost analysis, they reveal bigger patterns.
For example, if two vehicles in the same route zone consistently show higher maintenance costs, it may point to road quality, overloading, or driver behavior. Fixing the root cause—rather than repeatedly paying for repairs—saves more in the long run. The goal isn’t to cut costs unthinkingly but to understand where money is quietly leaking.
2. Improves budget forecasting
Budgets don’t work well when they rely on guesses. With cost analysis, managers can look at actual past numbers not just totals, but where and when the money went.
If brake repairs tend to go up during winter or tire replacements follow a certain mileage pattern, you can build those expectations right into the forecast. This helps managers walk into budget talks with real numbers instead of just going with what feels right.
3. Enhances operational efficiency
A fleet might look fine on the surface but still waste time and money in ways you don’t catch right away. Maybe drivers are backtracking between stops. Maybe two vehicles are doing the work one could handle alone. These things don’t always show up unless someone looks closely at the numbers.
That’s what cost analysis does. It puts real performance next to actual spending, which makes it easier to see what’s dragging down efficiency. Fixing those issues usually doesn’t take much just a few changes to how things are run day to day.
4. Enables strategic fleet planning
It’s hard to make the big calls—like whether to replace or keep vehicles—without something to back it up. When cost analysis shows how much you're really spending on maintenance, fuel, and downtime, it changes the conversation.
That “free” vehicle might actually be the one eating up the most money behind the scenes.
5. Increases ROI on fleet investments
Not every investment gives back what you put into it. That’s why tracking results matters. If you’ve installed route optimization software or upgraded part of the fleet, it’s important to know if those choices are actually saving time or money.
Cost analysis lets you measure the impact—on fuel, repairs, labor, or downtime. And when you can see which investments paid off and which ones didn’t, it’s easier to make better calls next time.
{{demo_wms="/styles/components"}}
How to perform a fleet cost analysis
Running a cost analysis isn’t about plugging numbers into a spreadsheet and calling it a day. It’s about understanding how much each vehicle is really costing your business and why. Here’s how to break it down in a way that actually makes sense.
1. Calculate total cost of ownership (TCO)
TCO helps you figure out what a vehicle really costs from the time you buy it until the day you retire it. That includes what you paid upfront, what you spent to keep it running, and how much it’s worth at the end.
Say you bought a van for $45,000. Over five years, you spent $25,000 on fuel, repairs, and maintenance. When it was time to sell, you got $10,000 back. Your TCO? That’s $45,000 plus $25,000 minus $10,000. So: $60,000. That’s your real cost.
2. Identify fixed costs
Fixed costs don’t change, no matter how much a vehicle is driven. You’ll pay the same amount whether it’s out on the road every day or parked in the lot. These include:
- The purchase price (or lease)
- Insurance
- Licensing or registration fees
- Depreciation
These are usually easy to track but make up a big chunk of the overall cost, especially if your vehicles aren’t being used as much as planned.
3. Identify variable costs
Variable costs move up and down depending on how much the vehicle is used. Drive more, spend more. That includes:
- Fuel
- Maintenance and repairs
- Tires
- Driver-related expenses (like training, overtime, or tickets)
These costs can sneak up fast. One driver might burn through tires twice as fast as another. A few extra hours of idling every week adds up by the end of the year. Cost analysis helps you spot patterns like that.
4. Calculate cost per mile
This is one of the most useful numbers you can track. It tells you how much you’re spending every time a vehicle drives a single mile.
Here’s the formula:
Cost per mile = (Fixed costs + Variable costs) ÷ Total miles driven
Let’s say your total costs were $232,000, and your fleet covered 100,000 miles. Your cost per mile would be $2.32. No,w you’ve got something to compare across different vehicles, routes, or driver schedules.
TCO to make data-driven decisions
Total Cost of Ownership (TCO) isn’t just a finance metric. It’s a tool that turns day-to-day numbers into a long-term strategy. When fleet managers know the full cost of keeping a vehicle, they can move past gut decisions and start making choices backed by real data.
TCO helps answer some of the toughest questions: When should we replace a vehicle? Should we keep leasing or start buying? Are certain vehicle types consistently more expensive to maintain? Without that insight, it’s easy to pour money into vehicles or operations that just aren’t delivering value.
Once the numbers are clear, patterns emerge. You start to see which decisions are saving money and which ones are quietly burning through the budget. The goal isn’t just to cut costs but to build a fleet that works smarter, lasts longer, and fits the business better.
Here are five areas where understanding TCO leads to more informed, more confident decisions.
1. Vehicle replacement
There’s a point when every vehicle becomes more expensive to keep than to replace. But knowing exactly when that point hits can be tricky. Some fleets wait until a vehicle breaks down repeatedly. Others replace based on mileage alone. TCO gives a better way to decide.
By tracking a vehicle’s repair costs, fuel use, and depreciation over time, you can see when costs start climbing faster than usual. For example, if a truck’s maintenance costs double between years four and five, that’s a sign it may no longer be worth keeping—even if it still runs.
Looking at resale value also plays a role. A vehicle that still has a decent resale value might be better sold early than held onto for another year of high costs. TCO helps you weigh the short-term savings of keeping a vehicle against the long-term cost of running it into the ground.
This approach keeps the fleet in better shape, avoids unplanned downtime, and helps stretch the budget over time not by guessing but by working with actual numbers.
2. Maintenance strategy
Maintenance doesn’t just keep vehicles running—it’s one of the biggest drivers of long-term cost. A solid TCO analysis shows how much you’re spending on upkeep and whether your current strategy is actually working.
For example, preventive maintenance usually costs less than emergency repairs. But if you’re still seeing high maintenance costs, it may be time to dig deeper. Are vehicles being serviced too late? Are certain models more prone to breakdowns? TCO can help break those costs down per vehicle or vehicle type.
It’s also useful when negotiating service contracts. Suppose you know exactly how much you're spending annually on parts, labor, and downtime. In that case, you're in a better position to evaluate whether a third-party maintenance program is worth the price—or if it makes sense to handle it in-house.
In short, TCO puts a dollar figure on maintenance trends so you can stop guessing what’s going wrong and start fixing it. Over time, this leads to a more stable fleet and fewer surprises.
3. Buy vs. lease vs. rent.
Choosing whether to buy, lease, or rent vehicles isn't just a financial call—it affects operations, risk, and long-term planning. TCO helps compare these options in a meaningful way. Buying usually costs more upfront but can be cheaper in the long run if the vehicle is used for many years.
Leasing reduces upfront costs and may include maintenance, but often comes with restrictions on mileage or customization. Renting is flexible, especially for seasonal or project-based needs, but it’s the most expensive per mile. TCO analysis helps break these options down beyond surface-level costs.
For example, you can compare how depreciation and resale affect a purchased vehicle’s lifetime cost versus the predictable payments and included services in a lease. Rentals might seem expensive until you compare them against the cost of maintaining idle vehicles in your yard.
The best choice depends on how the fleet is used, how often it needs to change, and how long you plan to keep the vehicles. With clear TCO numbers, the decision isn’t just financial it’s strategic.
4. Right-sizing the fleet
It’s easy for a fleet to slowly grow bigger than it needs to be. Vehicles are added for short-term demand, kept “just in case,” or left idle between jobs. But each unused vehicle still racks up fixed costs—insurance, depreciation, and storage even if it’s barely driven.
TCO helps identify which vehicles are truly pulling their weight. If two trucks serve the same area, but one costs more per mile due to repair history and low usage, that’s a red flag. And if you’re leasing vehicles that sit unused, TCO makes it clear how much that downtime is costing.
By comparing cost per mile, cost per hour, or total annual cost against how often a vehicle is actually used, fleet managers can find opportunities to scale back without hurting operations. This also makes it easier to plan around seasonal changes—renting when demand spikes instead of owning year-round.
Right-sizing doesn’t mean cutting aggressively. It means adjusting based on data. TCO helps spot the quiet inefficiencies and gives a clear case for what to keep, what to retire, and where adjustments could save thousands.
5. Choosing the right vehicle types
Not all vehicles cost the same to own and operate even if they serve the same function. Some models may be cheaper upfront but require more repairs. Others may cost more to buy but use less fuel over time. Without TCO, it’s easy to choose based on price tag alone and end up paying more in the long run.
Tracking ownership cost by model or category helps answer questions like: Are light-duty vans better than pickups for urban routes? Do smaller engine trucks actually save money, or do they wear out faster under heavy loads?
This is especially useful when expanding or replacing part of the fleet. Instead of relying on what’s always been used, managers can compare actual performance across vehicles already in use. If one model consistently shows a lower cost per mile over three years, that data makes the case for standardizing future purchases.
Why you should have fleet management software for cost analysis
Manual spreadsheets and disconnected tools can only take a fleet so far. Fleet management software ties everything together, giving teams not just more data—but better visibility and faster decision-making. Here’s why using software makes a real difference in fleet cost analysis:
1. All your cost data in one place
Fuel logs in one system, maintenance records in another, driver reports on paper—it’s messy, and it slows everything down. Fleet management software brings all of that into one platform. Fuel transactions, service history, inspections, parts, labor hours—they’re all connected.
That means you don’t have to pull numbers from five different tools just to understand how much a vehicle is costing you this month. It’s all visible at once, with up-to-date totals and detailed breakdowns per vehicle. You can go from a high-level view of total fleet cost down to a single brake replacement on one truck.
This kind of centralization is the first step toward understanding TCO clearly and acting on it faster.
2. Real-time visibility into trends
Costs don’t spike all at once—they build over time. Without a system that tracks expenses in real-time, you won’t see those slow climbs until they’re already hitting your budget.
Fleet software tracks expenses as they happen. That means you’ll see if fuel costs are creeping up across the fleet or if one vehicle’s maintenance bills are trending higher than the others. You’re not waiting until the end of the month to catch the problem—you’re catching it while it’s still small.
This helps with both day-to-day decisions and long-term planning. Over time, patterns in fuel use, tire replacements, and driver-related costs can be used to adjust routes, rethink training, or flag vehicles for early retirement.
3. Easier and more accurate cost-per-mile tracking
Tracking cost per mile manually is time-consuming—and it’s easy to get wrong if you’re pulling mileage from logs and plugging costs into a spreadsheet. Fleet management software does the math for you.
It pulls mileage automatically from telematics or odometer updates and matches it with real-time fuel, maintenance, and other variable costs. You get up-to-date cost-per-mile data for every vehicle, which means you can actually compare performance, catch underperforming assets, and make faster decisions.
Whether you’re comparing two truck models or reviewing a single vehicle’s lifetime efficiency, this kind of detail makes it easier to figure out what’s working—and what’s not worth keeping.
4. Tracks vehicle lifecycle performance
The software helps you see how a vehicle performs from the day it joins the fleet until the day it’s sold or retired. You can track all service history, repair frequency, downtime, and total spending.
That kind of lifecycle view isn’t just nice to have—it’s essential for making smart replacement decisions. If one model consistently costs more in its third year or downtime climbs after 150,000 miles, you can use that data to plan better replacement cycles.
And when it’s time to sell, having a complete record of care and usage helps support resale value. Buyers trust well-documented vehicles, and you can prove a strong maintenance history with just a few clicks.
5. Fewer errors, less time wasted
Manually entering data leaves room for mistakes—missed entries, wrong numbers, skipped dates. Over time, those small errors mess with your analysis. If the numbers aren’t clean, the decisions won’t be either.
The software reduces those errors by pulling data directly from fuel systems, telematics, inspection apps, and maintenance logs. That means fewer things slip through the cracks, and less time is spent fixing reporting issues.
It also saves teams time. No more chasing down drivers for receipts or trying to rebuild missing logs. Everything is in the system, in real-time, and ready to report. That kind of reliability makes it easier to run monthly reports, forecast costs, or answer leadership questions without scrambling.
6. Helps with driver accountability and cost control
Fleet software doesn’t just track vehicles—it tracks behavior. Harsh braking, speeding, excessive idling, and fuel misuse—all of it affects cost. If you don’t see it, you can’t correct it.
With telematics integration and digital inspection tools, you get a clear picture of how each vehicle is being used and who’s behind the wheel. That allows for better coaching and cost control. You can reward drivers with strong habits and follow up with those causing avoidable wear and fuel waste.
It also gives drivers fewer excuses. When behavior is tied to cost—and it’s visible—accountability improves. That’s not about blame; it’s about visibility. And it’s one of the best ways to reduce avoidable expenses over time.
Reducing fleet costs
Cutting costs in a fleet doesn’t mean compromising safety or performance. It means looking closely at how money is being spent—and finding better ways to run day-to-day operations. Here are five proven ways to reduce fleet costs without sacrificing reliability.
1. Improve route planning
When drivers take the long way around—or sit in traffic or retrace their steps—costs pile up. More fuel burned, more hours on the clock, and more wear on the vehicles. It all adds up fast.
Even a small change in a daily route can make a noticeable difference. If someone’s covering 180 miles a day across 10 stops, trimming just 15 miles a day saves over 3,000 miles a year. Multiply that by 20 drivers, and now it’s a big deal.
But this isn’t just about saving miles. Better routes mean less fuel, fewer breakdowns, and fewer surprises that lead to delays or overtime. Planning with real traffic, driver schedules, and actual stop times—not just what looks good on paper—helps everything run smoother and cheaper.
2. Reduce idling and aggressive driving
Idling burns fuel without moving the vehicle an inch. Aggressive driving—harsh braking, speeding, rapid acceleration—puts extra stress on the engine, tires, and brakes. These habits quietly push up both fuel and maintenance costs.
With telematics data, fleets can monitor driver behavior in real-time. If one truck idles 45 minutes more per day than others in the same role, that’s a red flag. Over a month, that could mean 20–30 extra gallons of fuel burned for no reason.
Training drivers on better habits is one part of the fix. The other is visibility. When drivers know behavior is being tracked and tied to cost, most adjust without needing constant reminders. That reduces fuel waste, lowers maintenance bills, and extends vehicle life—all without changing your routes or fleet size.
3. Use preventive maintenance, not reactive fixes
Waiting for a breakdown always costs more than staying ahead of it. Emergency repairs come with towing, downtime, missed schedules, and sometimes higher labor costs. Preventive maintenance avoids all of that.
By sticking to a regular maintenance schedule, you catch issues early—before they cause major damage. For instance, catching worn brake pads in time might cost a few hundred dollars. If you miss them and the rotors get damaged, that turns into a $1,500 job, plus lost driving time.
Fleet software makes it easier to schedule, track, and follow up on preventive tasks. It also ensures that no vehicle slips through the cracks. Over time, this approach builds reliability into the fleet and reduces the “surprise” costs that throw off monthly budgets.
4. Track cost-per-vehicle to find weak links
Not every vehicle in the fleet is pulling its weight. Some cost more than others to keep on the road, and without tracking cost-per-vehicle data, it’s hard to know which ones.
One vehicle might have a history of frequent repairs. Another could be assigned to routes with poor mileage performance. Cost-per-vehicle analysis brings all of that to light. You get a clear view of which assets are consistently reliable and which ones are quietly draining money.
This doesn’t always mean removing vehicles right away. Sometimes, it means changing how they’re used, assigning them to different routes, or even swapping drivers. The point is to use data to fix problems early. When you know exactly where your money is going, you can make faster decisions that actually stick.
5. Replace underperforming assets sooner
Holding on to older vehicles can feel like the frugal choice—until the repair bills start piling up, fuel costs climb, and downtime starts affecting operations. Eventually, keeping a worn-out vehicle becomes more expensive than just replacing it.
That’s where the total cost of ownership (TCO) comes in. It’s a simple way to spot when a vehicle’s no longer pulling its weight. Maybe repairs have doubled in the past year, or it’s burning more fuel than similar models. Either way, that’s a sign it’s time to move on.
The longer the delay, the more likely unexpected breakdowns start to creep in. Swapping out aging vehicles doesn’t always mean buying brand-new ones. It could be as simple as replacing a few of the worst performers, moving high-mileage units into lighter roles, or trading in for something more fuel-efficient.
The idea is to stop sinking money into assets that aren’t paying off anymore. This isn’t about cutting corners. It’s about using data to make calls that actually save money. A few smart moves around maintenance, fuel, and how vehicles are used can add up to real savings over time.
Frequently asked questions
It depends on your setup, but many fleets spend several thousand dollars per vehicle each year.
You add up everything—fuel, maintenance, insurance, wages—and see what it’s costing you to run.
It’s a way to figure out what a vehicle really costs from purchase to resale, including all the stuff in between.
Stay ahead on maintenance, avoid fuel waste, plan better routes, and keep an eye on how vehicles are used.
It shows you where money’s going and helps you make decisions that actually save it.
Most teams use fleet software—it tracks all the moving parts without needing five different spreadsheets.