Fleet Inventory Management: A Complete Guide to Smarter Stock Control
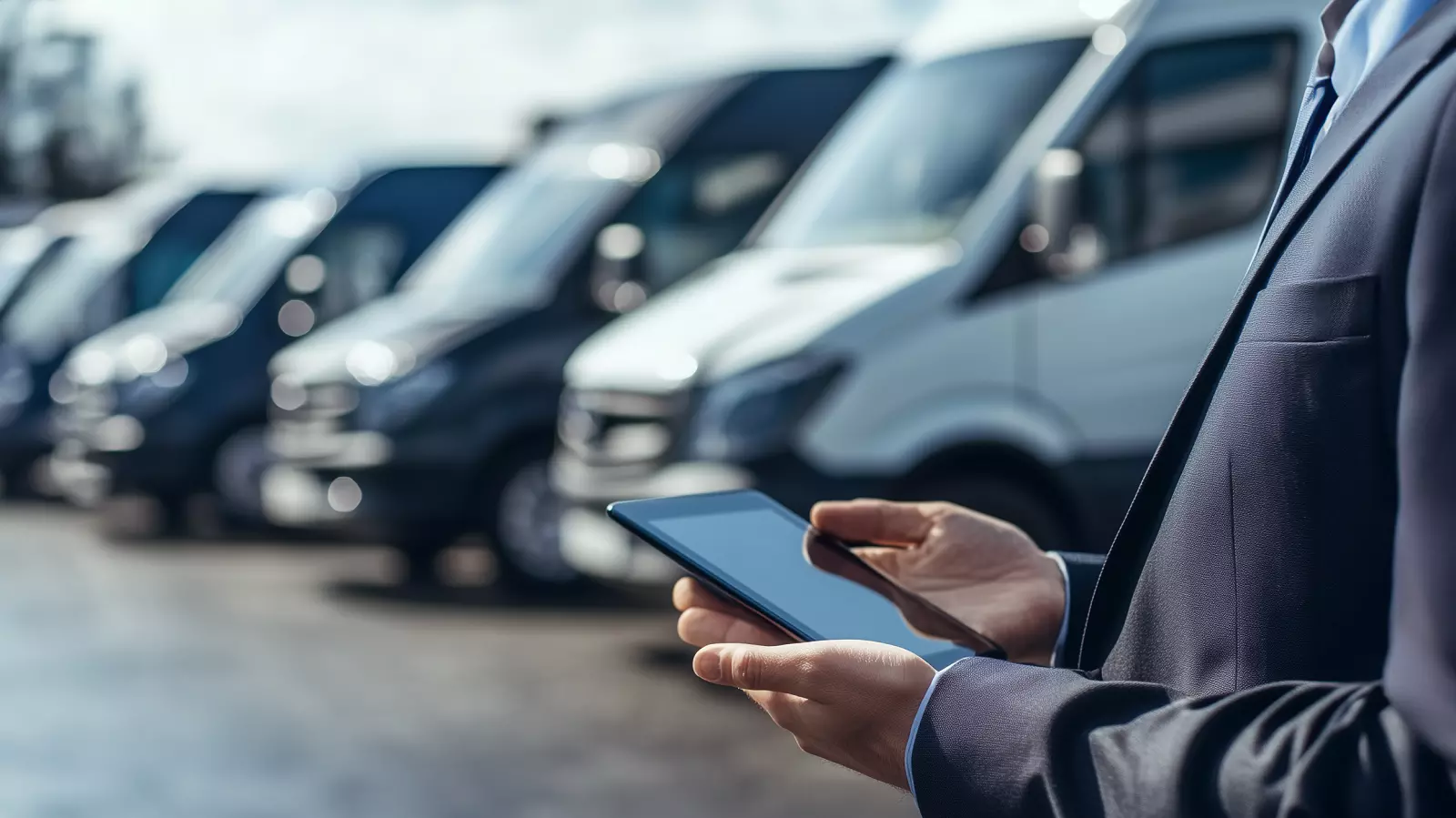
A service van breaks down on the highway. The issue? A simple belt that should’ve been replaced days ago. But the part wasn’t in stock, no one realized it was missing, and now the vehicle, and the job, are both stalled. Meanwhile, another garage across town is sitting on three of the same belt, untouched.
Moments like this aren’t rare. They happen every day in fleets without clear inventory systems. Parts go missing, jobs get delayed, tools disappear, and costs quietly pile up.
This guide breaks down how fleet inventory management actually works, why it matters more than most teams realize, and how to build a system that saves time, money, and chaos, before the next breakdown hits.
What is fleet inventory management?
{{demo_tms="/styles/components"}}
Think of fleet inventory management as keeping tabs on all the gear your vehicles rely on, not just the trucks or vans themselves, but everything from tires and tools to fluids and in-vehicle tech. If it plays a role in keeping the fleet running, it falls under this category.
It’s about staying ahead of the curve. When you know exactly what parts you have in stock, and what’s running low, you’re less likely to get caught off guard by a missing battery or a back-ordered filter. No one wants to delay a repair because of a forgotten part.
These days, many teams use software to track it all. The right tool can remind you when it’s time to reorder, show what’s being used up fastest, and even help you plan better for the future. It’s all about making smarter decisions and keeping things moving without unnecessary hiccups.
Why fleet inventory management is important
1. Keeps operations running smoothly
You don’t notice inventory problems, until suddenly, you do. A truck’s out of service because a basic part wasn’t available. A job gets pushed. People wait around. It’s avoidable. When inventory is dialed in, repairs happen on time, not “whenever that part comes in.” It’s one of those monotonous systems that quietly keeps everything moving.
2. Avoids unnecessary spending
Ordering extra “just in case” feels safe, but it adds up, fast. Parts sit on shelves, budgets swell, and no one remembers why that fourth alternator was ever ordered. Good inventory management helps control that. You stop overspending not by cutting corners, but by seeing exactly what’s needed and what’s not.
3. Supports accurate maintenance
When a part’s missing, the job gets skipped, or worse, someone makes do with what’s available. That’s how tiny issues turn into full-blown breakdowns. With a proper inventory system, techs don’t have to guess or wait. The right parts are there, the work gets done, and vehicles stay in better shape for longer.
4. Helps plan budgets better
Fleet spending adds up fast, especially when no one’s watching the shelves. Real-time inventory tracking gives you the numbers you need, not just what was spent, but what’s sitting idle. That kind of visibility makes it way easier to plan ahead, set realistic budgets, and avoid surprise costs down the road.
5. Improves accountability
When tools or parts go missing, the blame game starts, and no one wins. But when inventory is tracked properly, you know exactly who used what, when, and for what reason. It cuts out the mystery. People take better care of shared resources when they know there’s a record behind them.
Step-by-step guide to setting up fleet inventory management
1. Define goals and fix what’s slowing you down
Start by asking: what’s breaking down in your current inventory setup? Are parts showing up late? Are you buying more than you need and watching it sit unused? Or is it just unclear where everything is when you need it?
List out the main problems, then attach real numbers to the outcomes you want. For example, maybe you want to cut part-related delays by 30% over the next quarter or stop all last-minute emergency orders. The more specific you get, the easier it is to track what’s working, and what’s not worth your time.
2. Use software that can actually keep up
Most teams start with spreadsheets, and that works for a while, until it doesn’t. As your fleet grows or you start managing parts across locations, things slip. Stock goes missing, orders get delayed, and you’re stuck guessing.
That’s where software like Fynd TMS helps. It tracks inventory live, connects to your service schedules, and gives you a clear view of what’s needed, before it becomes urgent. Having that kind of visibility means fewer surprises, fewer delays, and a lot less scrambling.
3. List and categorize all inventory
Inventory isn’t just parts sitting on a shelf. It includes tires, filters, batteries, oil, tools, and tech like GPS trackers. Basically, anything you rely on to keep your vehicles running.
You need to list each item and label it, barcode, part number, whatever your team uses. Then group things in a way that’s easy to find. Not by some system that looks clean on paper, but by what makes sense to the people actually pulling those items every day.
4. Set up stock locations
Knowing you have a part is good; knowing where it is is better. Organize your inventory by physical location, whether it’s a main garage, a satellite depot, or even mobile repair units. Define minimum stock levels for each item and set reorder points so you’re not reacting to shortages after they happen.
5. Assign user roles and access levels
Not everyone needs full access to your inventory system, and honestly, not everyone should have it. Decide early on who’s allowed to adjust stock levels, move items around, or approve new orders. And if you're not already doing it, start tracking who’s using what and when. That way, if something doesn’t add up, you’ve got a trail to follow.
6. Link inventory to maintenance workflows
No one should have to remember to log every part after a repair, it’s just too easy to miss. The smarter move? Connect your work orders directly to your inventory system. So when a job’s marked done, the parts come off the list automatically. It keeps your counts tight and avoids those “how are we out of that?” moments. Setting up low-stock alerts tied to job schedules helps too, so you're not caught off guard.
7. Audit regularly
Even if you’ve got solid software in place, things can still go off track. Parts get misplaced, bins get mislabeled, and updates get missed, it happens. That’s why it’s smart to do a quick physical count every month or so. Just making sure what’s on the shelf lines up with what’s in the system can save you from bigger problems down the line.
Best practices for fleet inventory management
1. Keep digital records that don’t rely on memory or guesswork
When inventory is tracked on whiteboards or sticky notes, or worse, in someone’s head, mistakes are inevitable. You’ll forget who took what, lose track of when something ran out, and make decisions based on bad info. A digital system creates a reliable source of truth. It records every item in real time, with full history and access control, so nothing gets lost in translation.
2. Use barcode or QR scanning to build a traceable, accountable workflow
Typing part names or flipping through binders slows everyone down, and invites human error. Barcode or QR systems turn inventory into a scan-and-go process, saving hours of admin work. But more than that, they build traceability.
3. Automate reorders to prevent last-minute scrambles
Running out of critical parts is rarely about negligence, it’s usually about not knowing you were low in the first place. When you set reorder triggers based on real usage data, your system can flag items before they become a problem.
4. Track usage by technician or vehicle to find hidden inefficiencies
It’s not enough to know what’s getting used, you need to know who’s using it, and where. When you track parts by technician or vehicle, patterns start to show up. Maybe one team’s burning through the same component too often, or a certain route keeps leading to repeat fixes. That kind of detail doesn’t just help you restock, it helps you fix what’s actually going wrong.
5. Separate fast-moving and slow-moving parts to manage risk differently
Some parts fly off the shelves, others take weeks to replace. You can’t treat them the same. Stuff like filters or brake pads moves fast, so you need to keep a close eye and reorder often. But specialty parts? You’ve got to plan ahead and maybe keep a backup on hand. If you lump everything into one process, things get missed. A good system helps you stay on top of both, without the guesswork.
6. Use reports to reveal waste, not just count inventory
Counting what you have is basic. Knowing why you're going through certain parts faster than expected? That’s valuable. Usage reports should highlight trends over time, spikes, drop-offs, or inconsistent usage across teams. That data tells you whether it’s a training issue, a mechanical problem, or just poor planning. It’s not just about tracking parts, it’s about spotting the story behind them.
7. Integrate inventory with vendors and maintenance to reduce manual work
Too often, inventory, vendors, and maintenance operate in silos, and that’s where things fall apart. When your system connects all three, reorders can be triggered automatically, parts get linked to specific work orders, and vendor updates sync in real time. The result? Fewer delays, less double-handling, and a smoother flow from order to install.
Challenges in fleet inventory management
Managing fleet inventory isn’t simple, here are some of the biggest challenges fleets face, along with practical ways to solve them.
1. Lack of visibility
Challenge
When inventory is scattered across different garages or locations, it’s hard to keep track. One site might be fully stocked while another’s missing something essential, and nobody realizes until it causes a delay.
Solution
The fix is a shared system that shows what’s in stock, everywhere, in real time. That way, teams aren’t guessing or making calls, they know what’s available and where to find it.
2. Overstocking or understocking
Challenge
If there’s no clear rule on when to reorder, people either overbuy to be safe or don’t restock in time. You end up with shelves full of stuff you don’t need, or nothing when you do.
Solution
Set smart minimums and max limits based on how fast things actually move. And if your system can trigger alerts automatically, that’s even better, less to track, fewer surprises.
3. Manual tracking errors
Challenge
Writing things down or keeping a spreadsheet might seem easy, but it doesn’t take much for it to fall apart. Someone skips an update, miscounts a part, or saves the wrong version, and just like that, your numbers don’t match reality.
Solution
Use a system that updates as things happen. Even basic scanning helps. It takes pressure off the team and cuts down the time you spend fixing mistakes later.
4. Parts mismatch during repairs
Challenge
You’ve got a tech ready to do the work, but the part doesn’t fit, or worse, it’s missing. Now they’re stuck hunting around or trying to make something else work. That’s wasted time and money.
Solution
Make sure every part is labeled clearly, and tie it to specific repairs or vehicles in the system. That way, the right part is ready when the job starts, no guesswork, no delay.
5. Theft or loss of tools and high-cost items
Challenge
When inventory goes missing and there’s no clear record of who used it or when, it’s almost impossible to trace. Over time, these small losses become a major financial drain.
Solution
Implement user-based tracking for high-value items. Assign tools or parts to specific jobs or technicians to create accountability and make missing items easier to investigate.
6. Disconnected systems
Challenge
When inventory isn’t linked to maintenance schedules or vendor orders, service gets delayed. A job is scheduled but parts aren’t ready, or parts arrive, but no one logs them in.
Solution
Choose an integrated platform that connects inventory, maintenance, and purchasing. This keeps workflows in sync and ensures that every scheduled job has the parts it needs, on time.
Frequently asked questions
It’s simply how a fleet keeps track of the parts, tools, and materials it needs to stay operational. Without it, things fall through the cracks.
Spreadsheets work, for a while. But once things scale, they’re easy to mess up. A good digital tool gives you live updates and a lot less room for error.
Start by looking at usage trends. From there, set reorder levels that actually match what your team uses, not just what feels safe.
Yes. Many systems let you link parts directly to jobs, so when work is done, the system updates automatically, no extra steps.
For most teams, once a month is enough. But if your parts move fast, weekly spot checks can save you from bigger headaches later.
Use tags or barcodes, and have team members log check-outs. It creates a clear record of who took what, and when.