15 Key features of a warehouse management system
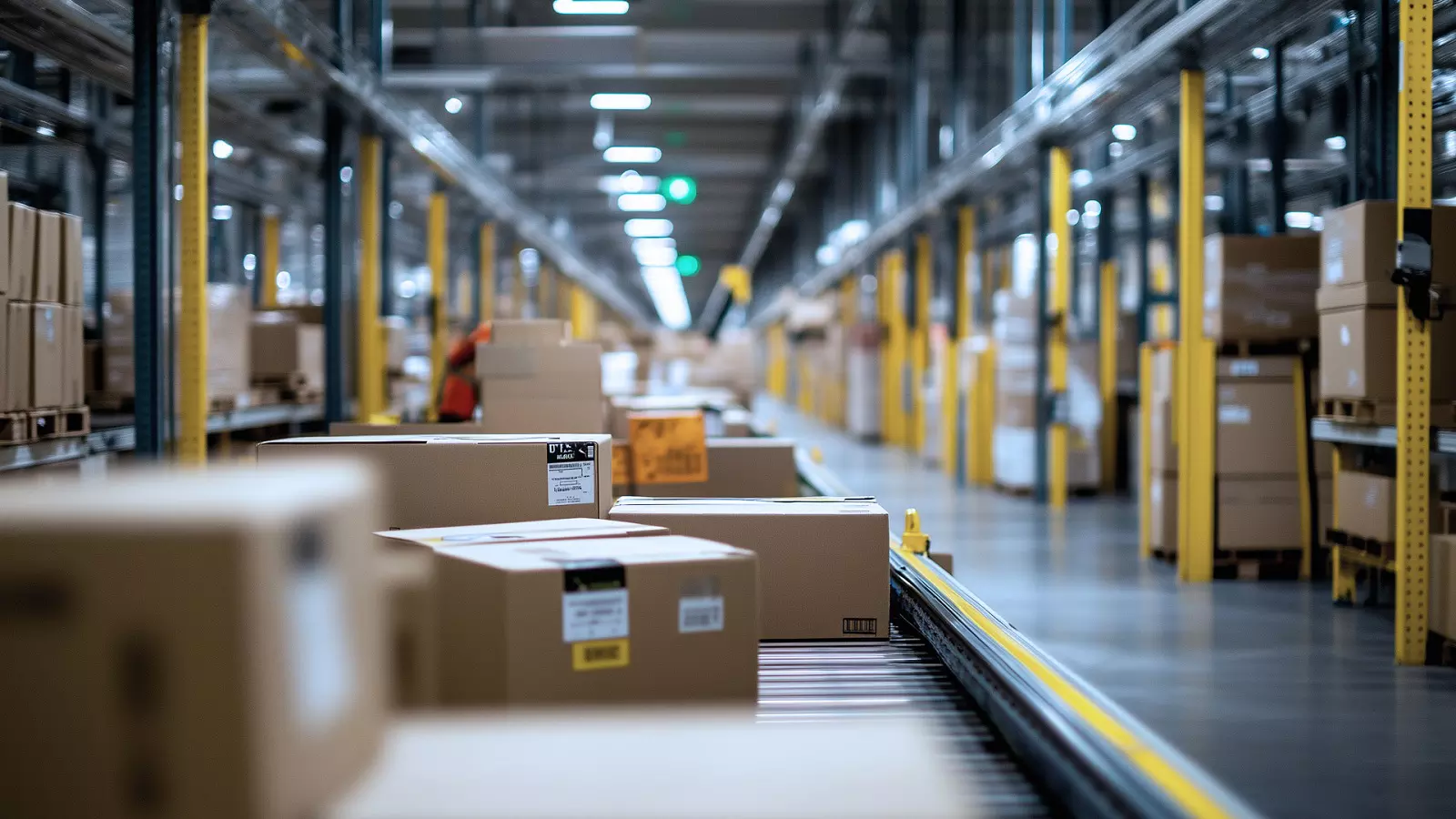
In a world where speed and accuracy in the supply chain can make or break a business, warehouse operations are no longer just a way to manage storage—they are now a key strategic asset. Organizations are under pressure to keep up with customer demand for faster, more accurate services while also dealing with shorter product lifecycles and increased demand for inventory management.
Warehouse management systems (WMS) have become important in delivering speed, accuracy, and efficiency. With the capability to improve guidelines for day-to-day warehouse operations and give real-time visibility into inventory and order flows, a WMS can be essential in becoming flexible and competitive in the supply chain.
Whether for an e-commerce brand managing 1000+ SKUs or a pharmaceutical company managing temperature-sensitive stock, a WMS can decrease errors, improve accuracy, and improve operational excellence.
This blog looks at what makes a warehouse management system effective, what features to include, what is utilized for that particular industry, and how to pick a warehouse management system for your business.
What is a warehouse management system?
{{demo_wms="/styles/components"}}
A warehouse management system (WMS) is a software application that allows organizations to monitor and control all operational tasks in a warehouse, from delivering goods and materials to a distribution or fulfillment center to their distribution out of the center.
WMS software systems are an important aspect of the supply chain management ecosystem. They provide real-time data visibility on a company's entire inventory, whether inside a warehouse or in transit.
Today's WMS solutions are tailored to help a global supply chain, including distribution, manufacturing, asset-saturated, and service companies. WMS software allows organizations to maximize labor and space utilization and investment in equipment by coordinating and optimizing resource consumption and material flows.
A WMS automates and standardizes processes, reducing human errors, saving time, and ensuring that resources are not wasted. It manages the flow of goods, from when inventory is received to when it is delivered to customers.
In conclusion, a WMS is an essential tool that improves the performance of a warehouse by improving storage and workflow layout. By tracking all inventory types, a WMS obtains locational information about inventory to locate items quickly and effectively manage supply chains by monitoring and scheduling needs.
Key elements of a warehouse management system
A warehouse management system (WMS) has critical components that work together to improve warehouse operations. The main components are software, radio communication devices, and barcode systems.
1. Software
At the center of every WMS is the software that manages and coordinates the activities inside the warehouse. The software provides functions for tracking inventory, order processing, and reporting.
Current WMS computer software can interface with other enterprise systems, like ERP and CRM, to move data seamlessly across the organization. It can also allow for real-time visibility into existing inventory quantities, manage the overall supply chain fulfillment operations, and provide efficient process execution inside the warehouse.
2. Radio communication devices
Radio communication devices, such as portable computers and mobile terminals, enable real-time data transfers in the warehouse. They allow warehouse staff to communicate with the WMS software and electronically decode data regarding inventory movements and tasks assigned to them.
Additionally, radio frequency communication devices allow business transactions occurring in a warehouse atmosphere to be able to be processed electronically, and all data once decoded and transmitted, will flow directly into the ERP.
3. Barcoding system
Barcoding is a baseline technology for warehouse operations and provides a fast and reliable method for tracking inventory. A bar code system includes bar codes, scanners, and printers. Inventory items, locations, and containers can be guaranteed to have unique barcodes assigned, which can then be scanned to obtain the exact information about the inventory item, location, or container.
Barcoding drastically increases transaction speeds and accuracy while decreasing manual entry and data discrepancies related to receiving, picking, and shipping. Implementing a bar code system significantly improves the accuracy of items for inventory and the efficacy of the operations.
15 key features of the warehouse management system
1. Real-time inventory tracking
Real-time inventory tracking is one of the most critical components of any modern warehouse management system. It allows managers to always have a current and accurate view of stock levels, item locations, and movements throughout the warehouse.
With this visibility, preventing costly mistakes like stockouts and excessive inventory is easier, thus preventing disruption to operations or tying up unnecessary working capital.
A WMS can provide this functionality through either barcode scanning or radio frequency identification (RFID). Whenever an inventory item is received, moved, or shipped out, the WMS updates immediately and allows for the following:
- Accurate stock counts at any moment
- Automatic alerts when the stock reaches critical low levels
- Improved order fulfillment speed and accuracy
- Reduced need for manual inventory checks
With real-time inventory tracking, warehouses can adapt to customer requirements sooner, keep waste at a minimum, and utilize the space outlined in their operations plan more effectively, greatly improving the effectiveness of operations in dynamic environments.
2. Receiving and putaway management
Receiving and putaway are the first and vital stages of warehouse operations, setting the stage for inventory accuracy/efficiency. A WMS automates the process by electronically recording incoming shipments and directing operators to the best locations to store the inventory.
By optimizing putaway decisions by attributes like product size, turnover rate, and the layout of the warehouse, the WMS reduces handling time and increases spatial efficiency. This is important to minimize errors, such as putting products in the wrong location or filling storage bins, which can also delay order fulfillment.
Key benefits include:
- Automated logging of shipment records
- Putaway directions for workers
- Natural optimization of storage based on item specification
- Fast-tracking of receiving items
- Reducing the rate of misplaced items
This functionality will ensure product flow from receiving docks to the warehouse, providing real-time inventory visibility from the moment of receipt.
3. Order picking and packing
The order picking and packing components of the warehouse process flow are paramount because they will either speed up and reduce the errors in fulfilling customer orders, or not. A strategically designed WMS has enhanced functionality to handle these steps, and helps inform the best decisions for the warehouse staff about the layout of the warehouse for order types and business goals.
- Batch picking: involves picking multiple orders in a single run, which significantly reduces travel time and enhances operational efficiency.
- Zone picking: dividing workers into zones in the warehouse to reduce pinch points and increase pace in picking
- Wave picking: using multiple, complex picking waves to provide the picking, packing, and shipping activities, to allow pooling for better throughput.
The WMS helps the pickers toward the right locations with the right quantity to help limit the human error of picking the wrong item or quantity. After items are picked, it will help in the packing process by confirming the items match the order, providing the best packing supplies suggestions, and generating the shipping labels accurately.
Some of the advantages are:
- More accurate orders mean fewer returns and customer complaints, which is costly.
- Faster fulfillment through a more efficient route for the pickers.
- Improved productivity by reducing walking distances and other repetitive movements.
- Better inventory control because stock levels are updated immediately after the items are picked.
In conclusion, the order picking and packing features that are part of a WMS can help warehouses ramp up operations smoothly with proper planning, delivery deadlines, and improved customer satisfaction.
4. Shipping management
Shipping is the last - yet crucial - step in the warehouse order fulfillment cycle. A WMS that integrates all shipping functions seamlessly automates the order shipping process and allows orders to leave the hands of the warehouse quickly, accurately, and with traceability.
When it comes to adding a shipping function to the WMS, it will usually:
- Generate shipping labels automatically by connecting to carriers (FedEx, UPS, DHL, etc.)
- Provide order scheduling or priorities with delivery deadlines or customer priorities
- Provide order or shipment tracking and status in real-time to warehouse staff and customers
- Track shipping paperwork electronically with fewer manual processes, paperwork, and errors.
Such automation mitigates many of the common shipping errors that cause wasted time, costs, and dissatisfaction, such as sending the wrong item or address (which triggers returns)
Effective implementation can even optimize options for packing and shipment, and determine sequenced options that balance the cost with delivery speed. There are a multitude of benefits to shipping management in a WMS. Some of the benefits include:
- Declining manual labor and errors through the automation of labels and documentation
- Greater visibility of shipment for all involved parties, including customers
- Faster turnaround time from packing to shipment
- Better carrier management through multi-carrier inter-connectivity and reporting of cost comparisons
With today's fast-paced logistics ecosystem and e-commerce pack & ship expectations, transportation management in WMS is vital to meet competitive delivery timelines and ensure the customer experience.
5. Returns processing
Returns processing is a critical function in warehouse management; however, it can be a complex process. This complexity arises especially in industries such as retail and e-commerce, which typically have higher return rates.
A capable WMS will be able to address the entire reverse logistics process, starting from the receipt of the return at the warehouse to the final disposition of the item.
In terms of operational efficiencies, as your returns are about to be logged into the system, the WMS will take care of updating your inventory levels in real-time and remind staff of the appropriate steps that need to be taken for each item.
Depending on a variety of factors, including but not limited to the reason for the return, the condition of the item, and company policy, the WMS can assist with directing the item toward:
- Immediate restocking if the item is in a sellable condition
- Inspection or repair if the item was damaged or defective
- Disposal or recycling if the item is completely unsellable
When companies automate the returns management system, they are able to reduce errors like mislocating an item or returning it to the wrong section, which negatively affects inventory records and order fulfillment precision.
In maintaining inventory balance, other advantages include:
- Return and refund progress can be processed quickly, which allows for less idle time.
- Due to the higher return and refund process efficiency, customer satisfaction increases.
- Business loss and compliance audit check risk are helped by having better tracking of inventory movements within the framework of return management.
- Confidence in the reflection of company assets improves, thus leading to improved control over inventory.
The burden of managing returns is reduced while maintaining service level, accuracy of cleared returns, and integration of processed returns in a warehouse management system (WMS).
6. Cycle counting and audits
Cycle counting is a planning method for counting inventory in small sections at regular intervals; this is preferable to counting all inventory in a warehouse at one time.
A WMS allows you to automate cycle counting by scheduling counts according to item value or the number of times there has been an error in the past. Workers are given parameters on where to cycle count, and the system monitors physical counts against inventory, easily identifying discrepancies.
Cycle counting provides the following advantages when counting inventory:
- Reduces inventory error.
- Decreases stockouts.
- Maintains accurate data while continuing regular operations.
- Assists with audits by keeping records of counts that show a history of counting in real-time.
Cycle counting provides accurate inventory records and limits disruption of daily practices.
7. Integration with ERP and CRM systems
A warehouse management system (WMS) that integrates easily with your ERP (Enterprise Resource Planning) and CRM (Customer Relationship Management) systems allows for an easy flow of information throughout your business. Order information from sales channels can go directly into your warehouse, and inventory levels will be updated in real-time with the finance and procurement modules.
Having an integrated warehouse management system will reduce the number of manual entry errors, speed up processing time, and improve visibility across departments. For instance, a sales team will be able to see real-time stock levels of products at their disposal to help with customer expectations. The procurement team can forecast customers' demand.
The main benefits of having an integrated WMS are:
- Automated data sync.
- Optimized operations.
- Improved visibility across departments.
- Reduced errors and minimized delays
Integration allows your WMS to operate naturally as part of a business ecosystem.
8. RFID support
RFID (Radio-Frequency Identification) helps warehouses manage their inventory through tags that are read by scanners without a direct line of sight. With a WMS that accepts RFID, receiving, picking, and shipping can be faster because whole pallets or bins can be scanned.
In addition to improving accuracy by reducing scanning errors that can come from people, RFID can increase efficiency, especially for large or high-volume warehouses. RFID can also improve asset security, minimizing theft and misplacement, by tracking, monitoring, and checking inventory more closely.
Benefits:
- Quick inventory processing
- More accuracy and fewer mistakes
- Better asset and inventory security
- Helps with complex inventory control processes.
The only drawback might be that buying and implementing RFID can be more expensive initially, but it does allow warehouses to increase productivity.
9. Mobile compatibility and cloud access
Modern warehouse management systems (WMS) consistently offer mobile apps, as well as cloud options to give warehouse employees and managers visibility anytime and from anywhere. Employees can use handheld scanners or smartphones to capture information in real-time during the picking, receiving, and shipping portions of materials movements.
Using a cloud-based WMS ensures that updates are made in real time, and management can oversee operations remotely.
Benefits:
- Access to in-time updates via mobile.
- The ability for remote management access.
- Scalable and agile implementation.
- Improved and speedier communication.
Mobile and cloud functionalities grant warehouses a greater ability to operate quickly and responsively.
10. Analytics and reporting
An effective WMS has analytics capabilities that turn operational data into actionable insights. Custom dashboards can track relevant KPIs like order accuracy, inventory turns, and labor productivity on a real-time basis.
Managers can generate reports to identify lagging KPIs, trends, bottlenecks, and opportunities to improve. They can use these insights to assist in making operational decisions like whether to stock out an SKU or how to support a peak period of fulfilling orders.
Analytics features:
- Historical and real-time reporting.
- Custom dashboards.
- Exportable data to help with audits and planning.
- Performance tracking.
Accuracy and efficiency are fundamentally important to warehousing and distribution performance, where enhancements can positively impact orders fulfilled and customer service, as well as strategic planning for warehouse space and labor resources.
11. User role permissions
WMS systems allow defining user roles and permissions to protect sensitive data and exercise operational control. Each staff member’s access is limited to the functions they require to complete their job, and this protects against inappropriate actions.
These capabilities mean that the system is more secure, the potential for error is reduced, and it is easier to demonstrate accountability because there is a complete audit history of what users have done and when.
Benefits include:
- Control over access to data and functions
- Reduced potential for errors or security breaches
- A level of end-user accountability
- Easier management of staff
Role-based permissions are one way to keep warehouse systems secure and running smoothly.
12. Labor management
Labor management capabilities help you to optimize workforce scheduling and productivity. The WMS uses skills and workload, assigns tasks, tracks performance, and makes forecasts on staffing requirements as demand for processing orders occurs.
Labor management can help you identify training needs as well as process inefficiencies as a result of labor data analysis.
Benefits can include:
- More optimal task assignment and related efficiencies
- Performance monitoring and reporting
- Better management of labor costs
- Workforce planning based on consumer demand
Labor management can help you have a motivated, efficient team, which can lower your operational costs.
13. Multi-location management
Multi-location management allows businesses with multiple warehouses or distribution centers to have centralized management and visibility. The WMS operates with inventory and operations for each location, allowing for the movement of stock and standardizing processes.
This ultimately allows for consistent service levels and visibility into inventory distribution levels.
Benefits of multi-location management:
- Centralized visibility of multiple locations.
- Streamlined movement of stock.
- Standardized process.
- Easier to scale and accommodate growing operations.
Multi-location management also helps companies manage complex supply chains.
14. Automated replenishment
Automated replenishment uses predefined reorder points and safety stock levels to automatically initiate replenishment. This will maintain appropriate inventory levels without having to manually monitor stock levels.
The system will generate a purchase order or transfer stock between warehouses as needed in order to achieve lower stock-outs and less surplus inventory.
The primary benefits are:
- Continuous availability of products
- Reduced manual intervention with a decrease in error
- Lower carrying costs
- Improved demand response
Automated replenishment keeps operations flowing while positively impacting customer satisfaction.
15. Task interleaving
Task interleaving consolidates multiple warehouse activities (picking, replenishment, and putaway) into one activity. It helps make the most out of labor by minimizing trips and walking distance.
For example, while workers are picking an item, they may be able to restock an item on their way to perform the picking task.
Benefits:
- Higher labor productivity
- Less travel time
- Speedier order fulfillment
- More evenly distributed workload
Task interleaving allows warehouses to do more in less amount of time with fewer resources.
Benefits of a warehouse management system (WMS)
A warehouse management system is not merely a utility to monitor items but also a tactical advantage that fosters efficiency, accuracy, and growth. A WMS can help transform your warehouse management, whether you are managing a few hundred SKUs or developing multi-site fulfillment operations.
These are some of the most important benefits:
1. Higher inventory accuracy
Real-time tracking and barcode scanning allow you to reduce any discrepancies in your inventory. A WMS minimizes your reliance on manual records and ensures your inventory data matches your actual physical stock; therefore, you have a more accurate forecast and a lower likelihood of running out unexpectedly.
2. Quicker and more precise order fulfillment
A WMS speeds up the order fulfillment process by optimizing picking paths, automating packing lists, and eliminating human error. With the speed and accuracy required from e-commerce businesses (and other businesses too), these enhancements are essential wherever customers simply expect packages delivered on time with accuracy.
3. Reduced cost for operations
A WMS can give a business an advantage when it can generate efficiencies in processes like receiving, putaway, and shipping, so labor costs are reduced. By leveraging smarter and more efficient stock rotation and use of space, WMS systems also help reduce excess inventory and storage costs.
4. Enhanced customer satisfaction
Accurate inventory counts and dependable delivery timelines also yield fewer delays, errors, and returns. With improved fulfillment, the customer has better trust in your services, and the likelihood of repeat business increases.
5. Real-time visibility into warehouse operations
Dashboards and reporting tools offer managers visibility into inventory levels, order statuses, and team performance, enabling them to make faster, more data-driven decisions.
6. Better utilization of space
Slotting optimization and inventory flow analysis improve the use of available space, making your warehouse more efficient and more productive without expanding your warehouse.
7. Better compliance and traceability
There are many industries that require strict traceability, such as pharmaceuticals or food. A WMS allows you to track lot numbers, expiration dates, and movement history, supporting audits and safety standards.
8. Scalable and system integration
Because a WMS is a professional system, it will grow as your company grows and can accommodate more products, more locations, and more orders. The WMS system is also software that can plug into your ERP, CRM, and more.
Real-world applications of WMS across industries
To effectively illustrate some of the benefits these features provide, let's look at how warehouse management systems are being effectively utilized to produce real results in practice within business cases.
1. Fashion retail: H&M's agile supply chain
Business Overview: H&M is a global fashion retailer with more than 4000 stores in 79 markets around the world, with a variety of customer demographics that operate in a fast fashion business model.
Operational challenges:
- Seasonally shifting and rapidly changing fashions and consumer preferences require a quick turnover of products.
- H&M wants to maintain low inventory levels, thus incurring little if any holding costs.
- H&M also wants real-time visibility of inventory levels across its stores around the world.
WMS implementation:
- Dual Inventory Management: H&M uses both centrally run and decentralized inventory management. Quality inspections are done centrally, while regional warehouses manage inventory directly to meet local demand promptly.
- Data Matrix Barcodes: H&M uses 2D barcodes that can contain up to 2,335 alphanumeric characters of information, including batch numbers and product certifications. This new barcoding technology has helped improve product traceability and quick point-of-sale operations.
- Supply Network: H&M manages a robust network of over 570 commercial product suppliers across more than 1,100 tier 1 factories, allowing for a quick response to consumer demands.
Outcomes:
- Better able to react to market trends and remain competitive in the fast fashion world.
- Better inventory accuracy with fewer stockouts, due to advanced tracking technologies.
- Better supplier relationships- H&M has an average length of 9 years in its supplier relationships.
2. Decathlon: Streamlining global operations with WMS
Summary: Decathlon is one of the world’s biggest sporting goods retailers and has over 2,000 stores in 79 countries. They design, manufacture, distribute, and retail their own products and manage over 21,000 SKUs globally. To effectively handle both their physical and e-commerce operations, Decathlon needed a highly performing WMS.
Key challenges:
- Managing real-time inventory with multiple warehouses and store inventory for accurate inventory count ∙
- Looking for a way to scale its logistics associated with the increasing online demand presented by COVID-19.
- Speed and accuracy of fulfillment of customer orders.
WMS solutions implemented:
- RFID Integration: Decathlon has implemented end-to-end RFID for real-time tracking of products and accurate inventory counts for inventory management for over 21,000 SKUs (by using an RFID portal to track inbound and outbound from the warehouse).
- Warehouse Automation: Decathlon is expanding its distribution center in Shanghai to almost 5,500 square meters and is using 71 Geek+ robots to sort and fulfill a very large number of orders.
- OMS-WMS integration: Decathlon defined improvement for its Order Management System; it integrated its Order Management System with its WMS systems for improved bandwidth and synchronization of order management across channels.
Conclusion:
By evolving its capabilities utilizing the benefits of WMS, Decathlon developed an agile and more responsive supply chain. Collectively, RFID, automation advancements, and system integration helped Decathlon respond to a dynamic retail environment and improved their customer experience by delivering a better, synchronized, consistent experience to both their online and store customers.
Pricing models of warehouse management systems
When assessing a warehouse management system (WMS) the pricing model can be as important as the features. Most WMS solution providers offer either a Subscription-Based pricing model or a Perpetual License pricing model. Both come with benefits depending on your organization's size, structure, and future goals.
1. Subscription-based model (SaaS / cloud-based)
This is the most popular pricing model today, for use especially among small to middle-market businesses. You pay a recurring fee (monthly or annually) for access to the software hosted in the cloud.
How it works
Pricing is typically based on the number of users, warehouse locations, number of SKUs that are being managed, or order capacity. Some vendors offer plans that are more tiered based on growing needs (Basic, Standard, Enterprise, etc.).
The key benefits:
- Low upfront cost - great for businesses that do not have or want to spend capital.
- Automatic updates and maintenance - the vendor manages system upgrades, bug fixes, and backups.
- High potential for scalability - depending on the level of activity from the warehouse or the growth of the business, it's easy to scale up or down.
- Remote access - with cloud access, warehouse activity can be monitored from anywhere via mobile devices or desktops.
Good fit for:
- E-commerce/d2c businesses
- Growing retailers
- Businesses with minimal IT support
2. Perpetual license model (on-premise)
In this model, the business buys a lifetime license to use the software, which is typically housed on their servers. There is generally a separate annual fee charged for technical support, updates, and maintenance.
How it works:
You pay a one-time license fee for the software, which gives you a perpetual right to use the software version purchased. After that, any additional enhancements or support are charged separately, often at a percentage of the original license cost.
Advantages:
- Greater customization and control - Organizations can adapt the system to match their way of operating.
- Owning and defending data - All data resides in your infrastructure and you are responsible for protecting it, a must in broad compliance-based industries.
- Big picture, lower costing over the longer term - Conversely, if the system is stable, or a mature business, the total price may be less than subscribing over time.
Good fit for:
- Large enterprises.
- Pharmaceutical or regulated industries.
- Companies with strong internal IT capability.
In conclusion, on one hand, there are various SaaS flexible features and lower upfront costs; while on the other hand, there are benefits from perpetual license use to greater control and potentially long-term savings for businesses that can manage their own infrastructure.
The decision may ultimately rest on a combination of operational complexity, in-house IT strength, and future growth needs.
Top warehouse management systems in 2025
With a solid grasp of WMS features and pricing, businesses will naturally look towards available solutions. Here are some of the top warehouse management systems currently on the market.
1. Fynd WMS
Best for: Scaling and growing retail businesses, D2C brands, and omnichannel retailers.
Fynd WMS has an easy plug-and-play architecture and fast setup capability, good omnichannel integrations, live view of inventory, automated order routing, smart picking systems, and B2B and B2C. Its flexible workflows and intuitive UI make it easy to utilize for teams.
Features:
- Cloud-based.
- Mobile initiatives/capabilities.
- Integrates with Shopify, Amazon, Flipkart, and ERP tools.
- Returns, Bundling, and multi-location fulfillment.
Why it’s a top pick: Fast setup, scalability in design
Focus on user experience and e-commerce integrations, and design orientation (e.g., user-centric interface, visually intuitive dashboards).
2. Manhattan associates WMS
Best for: Large organizations with complex supply chains.
Manhattan Associates develops a powerful and scalable WMS that integrates easily with automation. Manhattan Associates' WMS uses artificial intelligence and machine learning to enhance warehouse operations in a variety of ways, including demand predictions and cost reduction.
Features:
- Ability to leverage advanced AI capabilities and demand forecasts
- Labor management and slotting
- Adaptive fulfillment
3. SAP extended warehouse management (SAP EWM)
Best for: Organizations using SAP ERP
SAP EWM is designed to be integrated directly into the SAP ERP ecosystem, which will allow for real-time synchronization between warehouse & business operations. It offers advanced resource management, inbound and outbound logistics optimization, and full analytics.
SAP EWM Features:
- Robust, real-time analytics and automated replenishment.
- Seamless integration with numerous Warehouse Automation systems.
- Scalable to fit into complex supply chains.
4. Blue yonder
Best suited for: Retail and e-commerce
Blue Yonder offers a cloud WMS with end-to-end visibility, real-time inventory tracking, and AI-powered decision-making. The system has the flexibility to integrate with different automation systems.
Key Features:
- Predictive analytics and AI for more accurate inventory
- Adaptive logistics solutions
- A strong focus on automation and cloud technology
5. Oracle warehouse management cloud
Best Suited For: Organizations that require extensive analytics capabilities and global scalability
Oracle’s WMS is a deep cloud-based system that supports cutting-edge warehouse automation technology and includes a comprehensive suite of standard features including mobile management, order picking, and Internet of Things (IoT) and robotics integrations.
Features:
- Multi-channel order fulfillment
- Automated task management
- Mobile-friendly operation
What to consider when choosing a warehouse management system (WMS)
Similar to selecting the right WMS can positively impact your warehousing operations, selecting the wrong software can also negatively impact your operations and be wasteful in terms of money and resources.
Here are some considerations:
1. Business requirements and scalability
Consider the dimensions of your current warehouse and the total volume and complexity of your order. Select a system that can easily be scaled when you expand and/or diversify your business.
For example, a small retail business may only need to start with the cloud-based set of SaaS services, but a multinational operation would need a sophisticated on-premise system to track multiple locations.
2. Integration capabilities
Your WMS should easily connect with existing systems such as ERP, CRM, and e-commerce. Good integration keeps the data from becoming siloed and your real-time visibility improved throughout the supply chain.
For example, while SAP EWM integrates deeply into SAP ERP, it is also possible to have Fynd WMS integrate easily into Shopify or Amazon.
3. User experience and training
A well-designed user interface will minimize onboarding time and errors. Keep in mind whether the system can be used effectively on mobile devices and handheld scanners.
Training and vendor support are crucial to a seamless transition, as a warehouse environment can be labor-intensive.
4. Features and flexibility
Identify the features that are core to your needs including live inventory tracking, pick order optimization, returns handling, and analytics. Look into whether the WMS allows customization to meet your needs and workflow, without copious amounts of coding.
5. Deployment model and price
Select between a cloud subscription-hosted WMS or an on-premise perpetual licensed solution. Think about your IT environment, cost and security implications. Consider any and all costs associated with implementation, training, and post-implementation support.
6. Vendor reputation and support
Examine vendor portfolios with strong positive customer references. From the 24/7 support to ongoing updates of your vendor's tool, you get reliability and expertise on your solution.
7. Compliance and security
Depending on your industry, this may be the most important factor to consider. Ensure that the WMS adheres to your relevant standards and that it can ensure proper data security. With these considerations, you can select a WMS that meets your application needs to improve your operational efficiencies and growth going forward.
Warehouse Management Systems have become integral features of modern supply chains that facilitate complex operations at speed, accuracy, and efficiency. WMS supports a range of different activities from real-time inventory management to labor management, and working with multiple locations.
WMS creates optimized workflows across multiple warehouses to improve accuracy and reduce operational errors, ultimately offering a higher level of customer satisfaction.
The right WMS for your company will depend on your company's size, industry requirements, and longer-term goals for growth. Regardless of whether you want a flexible subscription model with cloud-based accessibility or prefer the control of an on-premise license, having a clear understanding of the criteria and features, as well as the pricing, will help you to the WMS provider that offers what your organization requires.
While taking time to select and implement a WMS might seem to be costly in a fast-paced market where demand is often changing, doing so might be one of the most strategic and advantageous ways for your warehouse infrastructure to be positioned to meet the ever-growing and changing demands of customers.
Frequently asked questions
Key capabilities of a WMS include real-time inventory management, receiving and putaway processes, order picking and packing, shipping management, returns processing, cycle counting, analytics, and integration with other systems like ERP and CRM.
A WMS reduces human error and achieves inventory accuracy through automation of data capture with barcode or RFID scanning, minimizes data entry time, and provides real-time visibility of inventory.
Yes, many modern WMS systems can integrate with any number of systems, including ERP, CRM, e-commerce systems, and even automation hardware to help the user stay synchronized across multiple processes.
WMS will enable optimized picking, packing, and shipping operations, leading to faster and more accurate fulfillment to ensure customers receive their orders as expected.
WMS tools have features to report on employee productivity, such as assigning work tasks efficiently and balancing workloads to optimize labor utilization.
Yes. Cloud-based WMS solutions can be easily scaled for business growth, while on-premise systems can be configured to scale for growth.