Components of a Warehouse Management System: Modules and Components
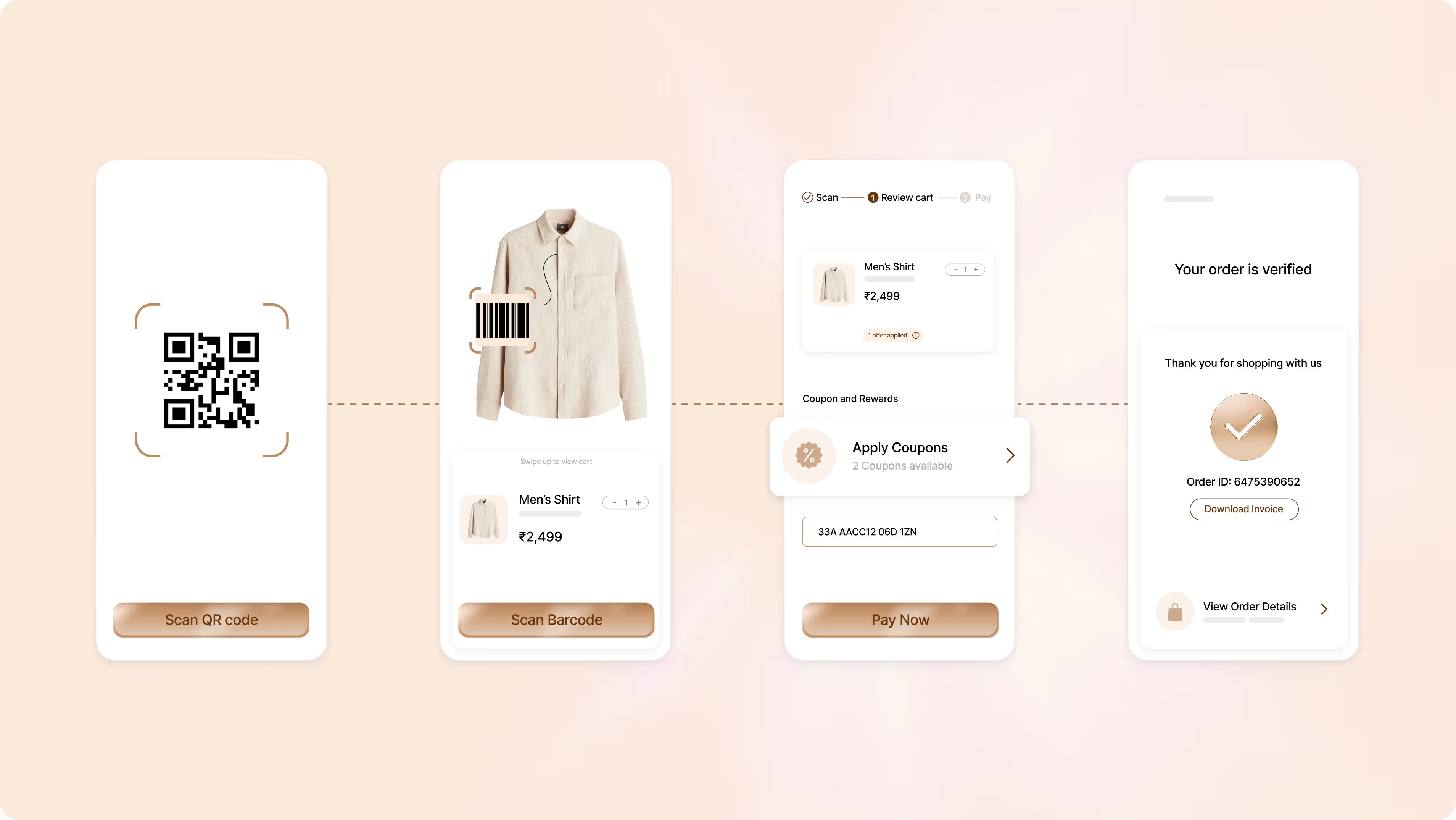
A Warehouse Management System (WMS) is crucial for modern supply chains, enhancing efficiency and accuracy in inventory management. Key components of a WMS include inventory management, which allows businesses to track stock levels in real time and reduce excess inventory by up to 25%. Additionally, the order fulfillment module streamlines processes, with efficient picking and packing techniques improving order accuracy to 99.9%.By integrating technologies such as barcoding and RFID, a WMS can facilitate faster inventory turnover, with warehouses reporting up to a 30% increase in operational productivity.
Implementing a WMS provides numerous benefits, including significant cost savings—studies show that companies can reduce labor costs by as much as 20%. Furthermore, WMS analytics enable data-driven decisions that can enhance supply chain performance. This is particularly vital in a competitive marketplace where efficiency translates directly to customer satisfaction and loyalty.
At Fynd, we specialize in providing cutting-edge Warehouse Management System solutions tailored to your business needs. Our platform not only addresses these essential components but also positions you for future growth, ensuring your warehouse operates at peak efficiency. Discover how Fynd can transform your warehouse operations today.
What is a Warehouse Management System (WMS)
A Warehouse Management System (WMS) is a comprehensive software solution designed to optimize warehouse operations by enhancing the management of inventory, order fulfillment, and shipping processes. This technology enables businesses to improve overall efficiency and significantly reduce errors associated with manual handling.
By automating various tasks such as inventory tracking, order processing, and reporting, a WMS helps companies streamline their operations, making them more agile and responsive to evolving market demands. Research indicates that effective implementation of a WMS can lead to inventory accuracy improvements of up to 99% and reductions in operational costs by as much as 20%. The key features of a Warehouse Management System are given below.
- Inventory Tracking: Monitors stock levels in real-time to prevent overstocking and stockouts.
- Order Management: Facilitates the picking, packing, and shipping of orders efficiently.
- Labor Management: Helps track employee productivity and optimize labor allocation.
- Reporting and Analytics: Provide insights into performance metrics, aiding strategic decision-making.
- Integration Capabilities: Connects with other systems like ERP and TMS for seamless operations.
{{demo_wms="/styles/components"}}
Key Components of Warehouse Management System
A Warehouse Management System (WMS) is essential for effectively managing the flow of goods in and out of a warehouse, playing a pivotal role in supply chain management. Understanding its key components is crucial for optimizing operations and improving overall efficiency. These components work together to automate various processes, enhance inventory accuracy, and streamline order fulfillment.
By implementing a WMS, businesses can reduce operational costs and improve customer satisfaction significantly. Below, you will find an overview of the key components of a WMS, along with a brief explanation of each, illustrating how they contribute to a well-functioning warehouse operation.
1. Inventory Management
Inventory management is the backbone of a Warehouse Management System (WMS). It empowers businesses to monitor stock levels in real-time, ensuring that the right products are on hand when required. Techniques like barcode scanning and RFID enhance inventory accuracy, significantly reducing the likelihood of overstocking or stockouts. This precision is vital for maintaining customer satisfaction and optimizing warehouse efficiency.
2. Order Fulfillment
Order fulfillment is a critical component of a WMS that manages the complete order process. This includes receiving orders, picking items, packing them securely, and shipping them to customers. A well-optimized WMS accelerates these processes, ensuring quick and accurate fulfillment, which is essential for enhancing customer satisfaction. Improved order fulfillment leads to faster delivery times and significantly fewer shipment errors.
3. Labor Management
Labor management features within a WMS track employee performance and productivity effectively. This component analyzes workforce data, enabling businesses to optimize labor allocation and improve overall efficiency. It assists in scheduling by ensuring that the appropriate number of staff members is available to meet operational demands. This strategic approach helps reduce labor costs while maximizing productivity in warehouse operations.
4. Reporting and Analytics
A robust WMS offers reporting and analytics tools that provide valuable insights into warehouse operations. By analyzing data on key metrics such as inventory turnover, order accuracy, and labor productivity, businesses can make informed decisions that enhance operational efficiency. These insights are crucial for identifying areas of improvement and ultimately reducing costs within the warehouse environment.
5. Integration Capabilities
Modern WMS solutions are designed to integrate seamlessly with other systems, such as Enterprise Resource Planning (ERP) and Transportation Management Systems (TMS). This integration allows for smooth data flow across various business functions, fostering better coordination and communication between different aspects of the supply chain. Enhanced integration capabilities lead to improved operational efficiency and a more cohesive logistics strategy.
Inventory Management Module
The Inventory Management Module is a crucial component of any Warehouse Management System (WMS). It enables businesses to efficiently track, control, and manage stock levels in real time. By automating inventory processes, this module minimizes human errors and enhances accuracy, which is vital for maintaining a smooth supply chain.
An effective inventory management system allows organizations to respond swiftly to market demands while reducing excess inventory costs and the risk of stockouts, ultimately contributing to improved operational efficiency and customer satisfaction. Here are the key functions of the Inventory Management Module:
1. Real-Time Tracking
This function enables businesses to monitor inventory levels as they fluctuate throughout the day continuously. By offering real-time updates, companies can make informed decisions regarding stock replenishment and order fulfillment. This capability significantly reduces the risk of stockouts or overstocking, leading to more effective inventory management practices. Ultimately, real-time tracking enhances operational efficiency and helps maintain optimal inventory levels across the supply chain.
2. Automated Reordering
The automated reordering feature activates replenishment orders whenever stock levels dip below set thresholds. This function ensures that inventory is consistently available for customer orders, which helps minimize stockouts. Automating the reordering process not only saves time but also reduces the likelihood of human errors in inventory management. This leads to improved stock availability and better overall service for customers.
3. Inventory Optimization
Inventory optimization tools analyze sales data and trends, enabling businesses to identify ideal stock levels for each product. By understanding demand patterns, companies can maintain optimal inventory levels, which reduces holding costs and ensures product availability. This strategic approach to inventory management enhances cash flow and profitability by preventing overstock situations while meeting customer needs effectively.
4. Reporting and Analytics
The reporting and analytics function provides valuable insights into inventory performance, such as turnover rates and current stock levels. By examining this data, businesses can pinpoint slow-moving items and make informed decisions regarding product promotion or discontinuation. Enhanced reporting capabilities support better forecasting and inventory planning, leading to more strategic inventory management and increased operational efficiency.
5. Integration with Other Systems
The Inventory Management Module integrates seamlessly with other WMS modules, including order fulfillment and labor management. This integration ensures that all inventory-related aspects are interconnected, facilitating improved coordination and efficiency across warehouse operations. A holistic view of inventory management enables organizations to streamline processes and enhance overall productivity, making the supply chain more responsive and effective.
Receiving Module
The Receiving Module is a crucial component of a Warehouse Management System (WMS) that focuses on the effective management of incoming goods. It streamlines the entire process from the moment products arrive at the warehouse to their eventual storage. By automating key tasks such as shipment verification and barcode scanning, this module significantly reduces errors, enhances accuracy, and improves inventory visibility.
A well-functioning receiving module ensures that businesses can manage incoming shipments promptly, leading to better inventory control, increased efficiency, and a smoother operation overall. Here are the key functions of the Receiving Module:
1. Shipment Verification
The shipment verification function allows warehouse staff to confirm that the received goods match the purchase order specifications. This involves checking the quantity, quality, and condition of the items against the documentation provided. Ensuring accuracy at this stage minimizes discrepancies and helps prevent issues later in the supply chain, ultimately maintaining high inventory accuracy and reliability.
2. Barcode Scanning
Barcode scanning technology is used in the receiving process to automate data entry and improve accuracy. When items arrive, warehouse staff can quickly scan barcodes to update the system with product information. This speeds up the receiving process and reduces human errors associated with manual data entry. Additionally, it enhances inventory tracking, making it easier to manage stock levels.
3. Damage Reporting
The damage reporting feature allows employees to document any issues with received goods. If items are found to be damaged, staff can quickly record the details and notify relevant departments for resolution. This function helps maintain transparency in inventory management and ensures that only quality products are stored, preventing potential problems down the line.
4. Putaway Management
Putaway management is a critical function that involves directing received items to their designated storage locations within the warehouse. The system assists warehouse staff by guiding the most efficient routes and optimal storage strategies, which helps in maximizing space utilization. Effective management of the putaway process ensures that products are easily accessible when needed, significantly enhancing overall warehouse efficiency and reducing retrieval times for order fulfillment.
5. Integration with Inventory Management
The Receiving Module integrates seamlessly with the inventory management system, allowing for real-time updates on stock levels. This connection ensures that as items are received, the inventory is automatically adjusted. This integration provides a holistic view of inventory levels and improves decision-making related to stock replenishment and order fulfillment, leading to a more responsive supply chain.
Order Fulfillment Module
The Order Fulfillment Module is a vital aspect of a Warehouse Management System (WMS) that efficiently manages the entire order processing cycle. This module encompasses all stages, from order receipt to picking, packing, and shipping, ensuring that the right products reach customers promptly and accurately. By automating various stages of order fulfillment, businesses can significantly reduce errors, enhance customer satisfaction, and improve overall operational efficiency.
This streamlined approach not only helps companies respond quickly to market demands but also positions them competitively in their respective industries. With effective order fulfillment, businesses can build stronger customer loyalty and drive revenue growth. Here are the key features of the Order Fulfilment Module:
1. Order Processing
Order processing involves receiving and verifying incoming customer orders to ensure accuracy and efficiency. The Warehouse Management System (WMS) checks product availability and organizes the orders for streamlined processing. This thorough approach is crucial, as it not only enhances customer satisfaction but also significantly reduces the likelihood of order errors. By ensuring that each step is executed correctly, the fulfillment process becomes effective, leading to improved service and operational excellence.
2. Picking Management
Picking management is focused on selecting the correct items from inventory based on specific customer orders. The system provides warehouse staff with detailed instructions on item locations and optimal picking routes to enhance efficiency. This careful management of the picking process results in faster and more accurate order fulfillment, which is vital for maintaining customer trust. Efficient picking also helps reduce labor costs.
3. Packing Process
The packing process entails preparing picked items for shipment, which involves assembling products into boxes and ensuring they are securely packaged. This module aids in selecting the appropriate packing materials, weighing items, and generating shipping labels. Effective packing not only minimizes damage during transit but also ensures compliance with shipping regulations. This proactive approach ultimately reduces return rates and helps maintain customer satisfaction by delivering products in pristine condition.
4. Shipping Management
Shipping management oversees all logistics involved in dispatching customer orders. This function includes generating accurate shipping labels, tracking shipments in real time, and managing communications with various shipping carriers. By coordinating these essential activities, the system ensures timely deliveries, allowing businesses to meet customer expectations. Furthermore, providing customers with tracking information enhances their overall experience, as they can monitor their orders, increasing satisfaction and fostering loyalty.
5. Returns Management
Returns management focuses on efficiently handling returned products to minimize disruptions in operations. The WMS facilitates quick processing of returns by accurately tracking items, updating inventory levels, and managing customer communications. Streamlining this return process not only minimizes losses associated with product returns but also enhances customer service. Ensuring that returned items are promptly accounted for in inventory helps maintain overall warehouse efficiency and keeps stock levels accurate.
Shipping Module
The Shipping Module is a critical component of a Warehouse Management System (WMS) that efficiently manages the entire shipping process for customer orders. This module ensures that products are dispatched accurately and on time, significantly enhancing overall customer satisfaction.
Automating various shipping tasks, such as label generation and tracking, helps streamline logistics, improve tracking capabilities, and reduce errors in the shipping process. A well-implemented shipping module not only leads to significant cost savings but also enhances operational efficiency for businesses, ultimately contributing to a better customer experience and increased loyalty. Here are the features of the Shipping Module:
1. Shipping Label Generation
This function automates the creation of shipping labels for outgoing packages. The system efficiently pulls relevant order information, such as the shipping address, product details, and tracking numbers, to generate accurate labels. By automating this process, businesses significantly reduce the risk of human errors, ensuring that packages are correctly labeled. This streamlining facilitates smooth shipping operations, helping to avoid costly delays and improving overall delivery efficiency.
2. Carrier Management
Carrier management involves selecting and managing relationships with various shipping carriers. The WMS provides comprehensive tools to compare shipping rates, transit times, and service levels for each carrier, allowing businesses to choose the most suitable option for every shipment. Effective carrier management not only ensures cost efficiency and reliability in the shipping process but also improves customer satisfaction by providing timely deliveries and better service.
3. Tracking Shipments
The tracking shipments function enables businesses and customers to monitor the status of orders in real-time. The WMS generates tracking numbers and integrates seamlessly with carrier systems to deliver up-to-date information on shipment locations and estimated delivery times. This transparency enhances the overall customer experience by allowing customers to stay informed about their orders, which fosters trust and increases satisfaction with the service.
4. Shipping Notifications
Shipping notifications are automated messages sent to customers regarding the status of their orders. This feature keeps customers updated on key milestones in the shipping process, such as when their order has been shipped and when it is expected to arrive. Timely notifications improve communication and enhance customer satisfaction by reducing anxiety and uncertainty about order status, allowing for a more positive shopping experience.
5. Returns Processing
Returns processing within the shipping module manages the logistics of handling returned items efficiently. The WMS tracks return shipments, updates inventory levels in real-time, and facilitates clear communication with customers regarding their return status. Efficient return processing minimizes financial losses associated with returns and enhances customer service by ensuring a smooth, hassle-free return experience, which can lead to improved customer loyalty and retention.
Role of Advanced Technology in Modern Warehouse Management Systems
Advanced technology is essential in modern warehouse management systems (WMS), significantly improving efficiency, accuracy, and productivity. By integrating advanced technologies, warehouses can optimize operations and adapt to customer demands while maintaining a competitive edge. Key roles include automation of tasks to reduce labor costs, real-time data analytics for informed decision-making, and enhanced inventory management through RFID and barcode systems.
Additionally, robotics and artificial intelligence streamline processes and predict demand, while cloud computing facilitates access to data from anywhere. These innovations transform how warehouses operate, ensuring faster, more reliable service for customers.
- Automation: Automation streamlines various processes, including order picking and packing, reducing manual labor and increasing speed.
- Real-Time Data Analytics: Technologies provide real-time data that helps managers make informed decisions, improve inventory accuracy, and track performance metrics.
- Inventory Management: Advanced tracking systems, like RFID and barcodes, enhance inventory visibility, minimizing errors and preventing stockouts.
- Artificial Intelligence: AI algorithms predict demand trends, optimize stock levels, and enhance route planning for faster deliveries.
- Robotics: Automated guided vehicles (AGVs) and robots assist in moving goods, reducing the risk of injury for human workers and speeding up operations.
- Cloud Computing: Cloud-based solutions enable easy access to data and applications from anywhere, facilitating better collaboration and flexibility in warehouse operations.
- IoT Integration: Internet of Things (IoT) devices monitor equipment conditions and track shipments in real-time, leading to improved maintenance and reduced downtime.
Conclusion
The integration of advanced technology in modern warehouse management systems (WMS) is transforming how businesses operate. By enhancing efficiency, accuracy, and productivity, these technologies enable warehouses to meet customer demands effectively and maintain a competitive advantage.
As companies look to optimize their operations, adopting innovative solutions like those offered by Fynd can lead to significant improvements in inventory management and order fulfillment processes. Investing in the right technology not only streamlines operations but also enhances overall customer satisfaction, driving business success in today’s fast-paced market.
Frequently asked questions
A Warehouse Management System (WMS) is a software solution that helps manage and optimize warehouse operations, including inventory management, order fulfillment, and shipping. It enhances efficiency by automating various processes.
A WMS improves inventory accuracy by utilizing technologies such as barcode scanning and RFID, which minimize human errors in tracking stock. Real-time updates allow businesses to identify discrepancies and maintain optimal inventory levels quickly.
Advanced technology in WMS enhances efficiency, reduces errors, and improves productivity. It allows for better tracking, streamlined operations, and effective order fulfillment, which ultimately leads to higher customer satisfaction and reduced operational costs.
Yes, most modern WMS solutions can integrate seamlessly with other systems, such as Enterprise Resource Planning (ERP) and Transportation Management Systems (TMS). This integration ensures smooth data flow across different functions of the supply chain.
A WMS significantly enhances order fulfillment by automating processes such as order processing, picking, packing, and shipping. This leads to faster turnaround times, fewer errors, and improved customer satisfaction.
When choosing a WMS, businesses should consider factors like scalability, ease of integration with existing systems, user-friendliness, and the specific needs of their operations. It’s essential to select a solution that can grow with the business and adapt to changing demands.