All About Cloud-Based Warehouse Management System
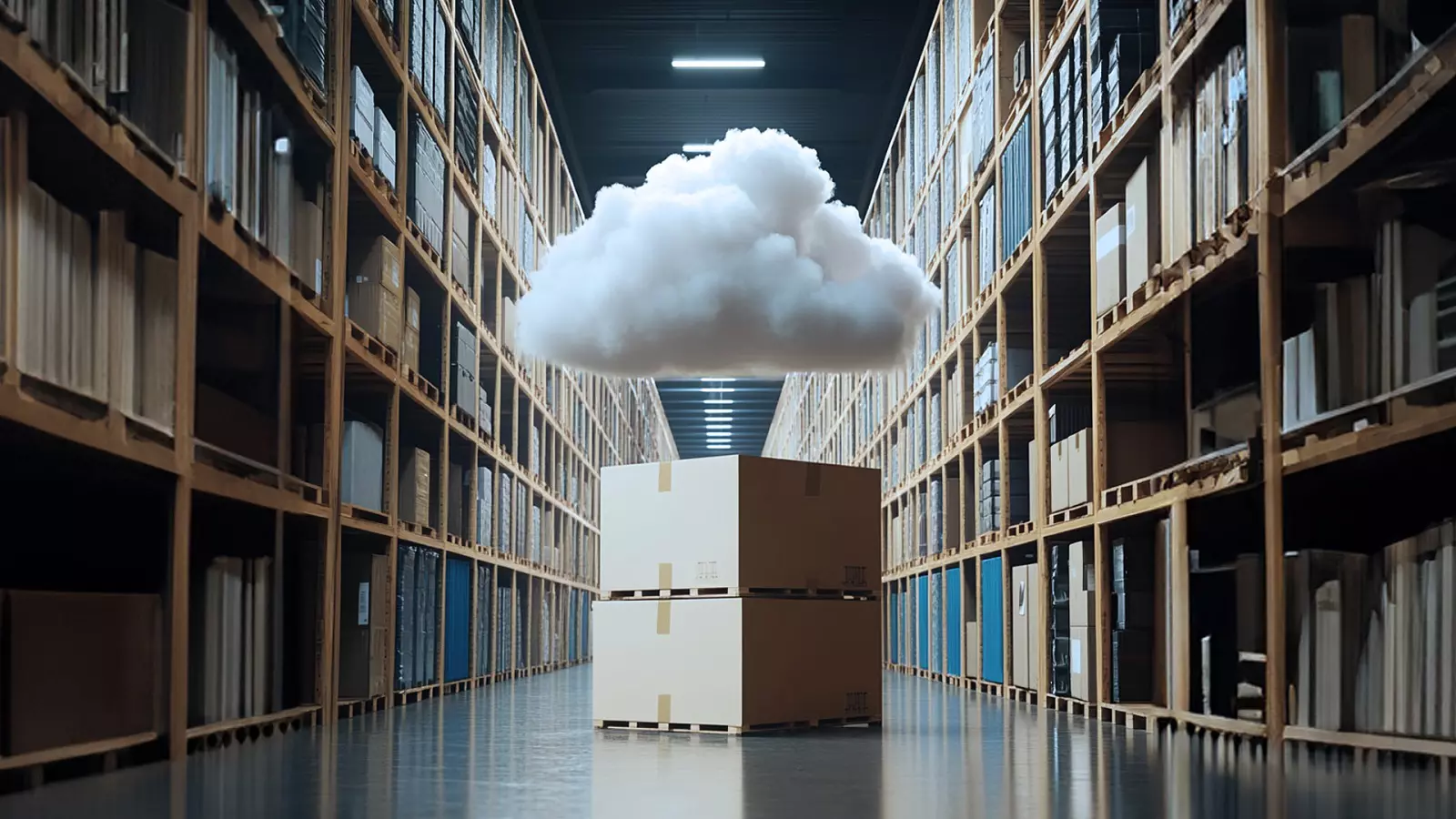
Warehouse management largely influences the results of a supply chain. Proper inventory handling, shipping goods, and real-time tracking can boost the profits of any manufacturer, distributor, or 3PL provider.
That’s when a Warehouse Management System (WMS) becomes important. With a WMS, businesses can oversee and improve warehouse operations, such as input, placement, pickup, and dispatch.
With chains becoming more flexible and customers needing faster deliveries, WMS solutions that run locally are struggling to keep pace. They are often resource-intensive for IT, require manual adjustments, and take a long time to implement.
Thus, Cloud-based WMS is the best solution for warehouses since it is robust, scalable, and cost-effective. Using WMS in the cloud means the system is accessed online, requires a smaller initial cost, and responds swiftly to new business demands.
What’s a cloud-based warehouse management system?
Cloud WMS or cloud-based Warehouse Management System (WMS) is a system designed to support warehouse operations such as inventory control, order fulfillment, and shipping, using the internet. While conventional systems are processed on premises, a Cloud WMS is hosted online and is available anywhere that has a browser and an internet connection.
It’s intended to be flexible, rapidly deployed, and generally easy to maintain, and a great fit for companies looking to modernize their supply chain.
1. How is it different from on-premise WMS
With traditional WMS platforms, you need on-premise servers, manual updating, and an IT staff to keep things in order. That model can be effective, but it’s often costly and not very efficient.
Cloud WMS solutions are changing this approach. They are controlled by the software provider, automatically updated, and typically available on a subscription basis. Small entry-level investment, fast implementation, and scalability as your business grows — all without the typical daunting tech lift.
2. Deployment models at a glance
Cloud WMS can be deployed in a few different ways, depending on your company’s needs:
- SaaS (Software-as-a-Service): The complete package—hosted by the provider (meaning the provider owns the server hardware) and offered via login through a web browser.
- Private cloud - A single tenant, dedicated environment for your organization only. Provides more control and flexibility.
- Public cloud: The infrastructure is shared, but still isolated with appropriate security. Often more cost-effective.
- Hybrid cloud: Hybrid models are rare in WMS unless you are integrating legacy ERPs or need offline functionality.
Key features of a modern cloud WMS
Cloud WMS systems are designed to solve practical problems in warehouse operations — from inventory inefficiencies to delayed fulfillment. What sets them apart is how they combine ease of access with powerful functionality. Here are some of the most important features that make up a modern Cloud WMS and why they’re important for growing businesses.
{{demo_wms="/styles/components"}}
1. Real-time inventory tracking and visibility
One of the major benefits of Cloud WMS is having visibility to what’s going on in your warehouse, in real time — it's not hours or when someone does a report manually.
- Companies can with real-time inventory management.
- Quickly learn what inventory is in stock and where it’s located.
- Control multiple warehouses with one system.
- Receive notifications of low stock or stock imbalances.
2. Efficient order and returns management
It’s in order management where businesses can either win or lose their customers. From getting the order to packing it up, a modern Cloud WMS makes the process easier through the use of various tools.
- Wave picking: Put similar orders together to save time processing them.
- Zone picking: Assign particular workers to designated sections to avoid too much travel back and forth.
- Order verification: Scanning in advance of shipping the product to avoid mistakes.
- Returns workflows: Returns workflows can be partially automated, with triggers for refund processing passed to financial systems.
3. Seamless integration with ERP, TMS, and eCommerce platforms
Warehouse systems do not operate in isolation. Today, warehouse operations are integrally linked to everything from finance to transportation to web storefronts.
A good cloud WMS will be built to tie into pre-existing connectors and/or open APIs to connect with:
- ERP solutions such as SAP, NetSuite, or Microsoft Dynamics — tying warehouse data into financials and procurement.
- Transportation management systems that are capable of communicating with carriers and optimizing shipping efficiency.
- eCommerce sites such as Shopify, Magento, BigCommerce, and marketplaces such as Amazon or eBay, for order auto-syncing.
4. Automation support: barcodes, RFID, and robotics
Manual work is just too prone to human error, especially as the volume of orders increases. Contemporary Cloud WMS can accommodate automation tools to help the warehouse processes go faster, more reliably, and potentially human-free.
Some of the features facilitated by automation include:
- Barcode and QR code scanning: Reduce time spent on picking, receiving, and performing inventory counts.
- RFID tracking: Monitor your inventory with RFID tags that update the system automatically as the products are on the move.
- Mobile device and label printing: Keep workers moving without unnecessary steps.
- Integration with robotics: Certain options include integration with robotics, e.g., AGVs or robot arms for assistive picking operations.
5. Customizable dashboards and flexible workflows
Different warehouses have their unique operating models. Speed is important to some, precision is essential to others, and most companies need both. A modern Cloud WMS realizes that generic solutions won’t cover every business’s needs.
That’s why many platforms offer:
- Custom dashboards: Many platforms offer configurable dashboards that display role-specific metrics and KPls.
- Role-based views: Users in each department are shown information that's most relevant to them.
- Workflow customization: Specify and manage workflows such as returns, replenishment, or cycle counting in a way that fits the way your team operates.
6. AI & machine learning for predictive logistics
The most advanced WMS systems help you plan successfully for what’s coming next in addition to organizing your current fulfillments.
With AI and machine learning, Cloud WMS can analyze historical data and current trends to provide insights like:
- Demand forecasting: Identify the products that are expected to see significant increases (or decreases) in sales.
- Labor planning: Help determine the appropriate number of employees needed, given historical data.
- Slotting optimization: Organize inventory to ensure high-demand items are most easily accessible.
- Returns prediction: Advanced cloud WMS platforms with machine learning capabilities may help identify products with unusually high return rates for further investigation.
Benefits of using a cloud WMS
Just a small inefficiency can result in major expenses, such as failed deliveries, inconsistent inventory, or logjams that hamper order completion. A growing number of businesses are replacing legacy and disconnected systems with cloud WMS systems. A Cloud WMS goes far beyond replacing an outdated WMS; It helps businesses shift towards an approach that is more flexible, capable of growth, and relies heavily on real-time data analysis. Here are the key business benefits that come with making that transition.
1. Faster implementation, faster ROI
Building traditional on-premise systems is not an easy process. You should plan for a long setup, as you have to set up hardware, get software ready, add outside software and train your employees. This work requires a lot of IT and can take several months to finish.
You can start using a Cloud WMS more rapidly. Onboarding and deploying cloud infrastructure for most vendors is simple, since they already have everything arranged, so the initial setup is not likely to cause outages.
So, businesses can:
- For small to mid-sized businesses with standard workflows, implementation may take a few weeks. Complex organizations may require several months.
- Straight away, begin to make improvements in the work processes.
- Lower disruptions in the organization will help you achieve ROI more swiftly.
This is particularly helpful for rapidly expanding firms for those experiencing sharp seasonal spikes in demand. In these cases, a quick go-live provides a significant advantage.
2. Lower IT costs and simpler maintenance
Companies must take care of all WMS-related needs on their own when running an on-premise system. Managing your servers, performing software updates, providing IT assistance, and keeping systems secure.
The responsibility of managing on-premise WMS solutions costs both money and precious company resources. Cloud WMS providers take care of those duties for you. You get:
- Automatic updates are typically deployed with minimal or no downtime.
- Automatically reliable with improved security and high availability.
- You don’t have to worry about setting up servers or hiring additional IT personnel.
As a result, you can lower your overall expenses and safeguard your business processes at the same time. You’ll have fewer interruptions to your normal workflow.
3. Effortless scalability
Quick transformations are common in the business world — from launching new facilities to entering new markets to tackling unexpected demand spikes. Growing with older systems often requires pricey updates, necessitates weeks of testing, or simply runs out of space.
A well-designed cloud WMS can scale with your business and support a variety of distribution center needs, depending on your vendor and configuration, from a single location to an increasing number of facilities.
- Increase or restructure your team, facilities, or products swiftly without complexity.
- Meet the challenge of unexpected demand during the busiest times of year.
- Redefine processes to handle increasing needs as your business changes.
Growing and shrinking your resources on demand is a major benefit of cloud computing. It’s easy to adjust capacity and grow as needed without having to replace your entire solution.
4. Anywhere, anytime access
Cloud WMS solutions are accessible across locations with internet access, including offices, warehouse floors, and - with appropriate security measures — in the field.
Multi-location businesses will appreciate being able to manage a dispersed network from one central view.
- Multi-location operations: Monitor your entire enterprise from a distance.
- Remote teams: Give leaders and technologists visibility into operations no matter where they are.
- Disruption planning: Cloud WMS enables centralized oversight, which supports business continuity planning in the event of localized disruptions.
Having transparent insights into your business comes in handy, but is essential to your company’s success when quick action ensures optimal operational outcomes.
5. Higher accuracy and fewer operational errors
Taking an inventory, typing one list for the pickers and using separate documents for each step usually leads to errors. Even though mobile labels are simple to handle, wrong information due to manual work disappoints customers, creates expensive returns and wastes goods.
Cloud WMS helps improve workflow accuracy by standardizing processes and reducing human error by:
- Creating a set of procedures to be followed for picking, packing and replenishing in one system.
- Supporting employees by using digital ways of work.
- Identifying inconsistencies as the data is being analyzed.
As a result, fewer errors happen when shipping goods, stock is better tracked and the supply chain is kept very tidy.
6. Continual innovation and no manual upgrades
An often underappreciated advantage of cloud systems is this. Your business runs the last available iteration. Vendors release frequent updates and enhancements to their products in response to evolving what users want and what technologies they need.
You get:
- Updates are rolled out whenever they’re released.
- Advanced features are automatically included as soon as they become available.
- Staying ahead of the curve with the most recent developments, no matter your company’s size.
Cloud WMS typically delivers updates with minimal disruption, reducing the need for extensive consulting or system downtime.
7. Better decision-making with live data and analytics
A Cloud WMS gives you instant access to all your warehouse information, so you can track inventory and operations as they happen.
With real-time dashboards and customizable reports, businesses can:
- Monitor key performance indicators such as order accuracy, the approximate time it takes to ship orders, and how quickly stock is moving.
- Beforehand, see if there are any problems, for example, if your returns are increasing or your inventory is not moving swiftly.
- Take the initiative to use strategies that represent the current situation, not just the past.
Improving control and accuracy helps a company make better long-term plans.
8. Stronger collaboration across departments
Using a Cloud WMS allows you to see your entire warehouse’s data in real-time and monitor any changes as they occur.
- They can pull up real-time information and create custom charts at any time.
- Keep an eye on metrics related to shipping speed, the accuracy of your orders, and the rate at which stock is leaving the warehouse.
- Catch potential setbacks as they start to happen, such as higher-than-usual returns or items sitting on the shelves longer than normal.
- Use current information to build plans that work best for the present and future.
Improved understanding of your operations allows you to build more strategic plans for the future.
Why more businesses are switching to cloud WMS
Migrating to the cloud is the best answer for navigating increasing operational requirements, lower profit margins, and the need for greater agility in the supply chain.
Here’s what’s driving the shift.
1. Rising pressure for operational agility
Supply chain operations must be able to respond to changing circumstances with ease. Businesses are facing:
- Fluctuating demand
- Faster shipping expectations
- Shorter product life cycles
- Labor shortages
Legacy solutions are struggling to meet today’s challenges. A Cloud WMS enables organizations to rapidly respond to changes such as opening a temporary facility, adding workforce quickly or switching fulfillment methods in a flash.
2. Lower total cost of ownership (TCO)
Moving to the cloud lets companies avoid expensive initial costs in exchange for payments that adjust with their business needs. Organizations no longer need to purchase servers, manage software updates or pay for tailored connections whenever their business grows or evolves.
Lower, clearer and more predictable expenses make it simpler for small businesses and 3PLs to reduce overhead and remain profitable.
3. Increasing focus on real-time data
Information that is late or incorrect affects every stage in the distribution process, resulting in things like late shipments or items being unavailable. Companies are moving to the cloud in order to have instant access to the latest warehouse information.
By using a cloud WMS, organizations are able to make timely decisions based on accurate data, leading to better planning, faster responses and improved interactions with their customers.
4. Shift toward remote and distributed teams
Since 2020, many organizations have adopted remote management, distributed teams or a combination of the two. Cloud WMS enables control, efficiency and team coordination at scale.
As a result, these changes in how we work now are more about necessity than preference.
5. Growth in multi-channel and e-commerce fulfillment
With increasing numbers of B2B companies selling direct to consumers or launching their own eCommerce operations, warehouse management systems must be able to deliver timely and accurate processing of individual shipments, meet accelerated shipping commitments and efficiently manage higher rates of returns.
Modern Cloud WMS solutions are built to handle the unique needs of many B2B companies that are now processing fewer but larger orders.
Cost comparison: cloud WMS vs. on-premise WMS
Cloud and On-Premise WMS solutions address similar challenges, but their expense models at once vary considerably. The total expense includes costs for maintaining infrastructure, making upgrades, IT support, and achieving flexibility.
Here’s how they stack up:
Keep in mind that the true benefits come into play as your business grows.
You can more easily plan and manage costs with Cloud WMS and it grows effortlessly as your business expands.
As growth occurs, On-Premise WMS can lead to expensive maintenance charges and additional, sometimes unpredicted, expenses.
Most companies in this size range find Cloud WMS to offer greater value at a lower cost of ownership, even matching or exceeding the functionality of on-premise solutions.
Compliance and regulations in cloud-based WMS
In the world of warehousing, keeping your operations safe and compliant is not just a matter of IT, it’s essential to the success of your business. Compliance with up-to-date standards is essential no matter your industry, data or geographic scope.
Cloud WMS solutions really stand out by making it easier to achieve compliance. The service typically provides the tools and best practices needed to help companies comply with legal, industry and data security regulations.
1. Why compliance matters
Warehousing now involves much more than physically transporting items. They manage sensitive data and regulated products used by banks, hospitals, pharmacies and e-commerce retailers.
Not complying with the necessary regulations and rules may result in:
- Legal penalties and fines
- Loss of contracts or certifications
- Data breaches or operational shutdowns
- Damaged customer trust and reputation
Cloud WMS systems are now sought after for their operational benefits and built-in features that assist with achieving regulatory compliance and minimize risks associated with information and goods transported online.
2. Key regulatory standards to know
Here is a look at some of the key compliance frameworks commonly adopted by companies in various sectors:
- GDPR ensures the proper handling of the personal information of people living in the European Union. Affects organizations processing personal data of individuals living in the European Union.
- HIPAA governs how protected health information (PHI) is used and shared within the U.S. healthcare industry.
- ISO 27001 sets out the requirements and guidance for implementing a stable and effective information security management system (ISMS).
- SOC 2 ensures the security, availability and integrity of systems and information, as well as protecting individuals’ privacy. Cloud computing and software as a service companies are especially affected by SOC 2 requirements.
Compliance with industry or sector-specific regulations such as FDA 21 CFR Part 11 (pharma industry) or PCI DSS (payment data handling companies) may be required depending on your niche.
3. How cloud WMS helps with compliance
Many cloud WMS providers ensure their solutions are compliant right from the start — making life easier for your in-house teams. Here’s how:
Built-in data security features
- Leading cloud WMS providers typically encrypt data in transit and at rest. Businesses should confirm these capabilities with the vendor.
- Two-step verification is required for all users to log in.
- Most cloud WMS platforms offer session timeout controls that can be configured to automatically log out inactive users and every user has a limited set of roles to access different features.
- Hosting is provided by established and certified cloud services such as Amazon Web Services, Microsoft Azure or Google Cloud.
Audit logs and access controls
Cloud systems also monitor user activity — who did what, when, and what were they doing — automatically. These logs are important for:
- Internal audits
- Outside regulatory inspections
- Tracking.potential breaches or misuse
Vendor certifications
Most prominent Cloud WMS providers achieve certifications such as ISO 27001, SOC 2 and FedRAMP to work with government systems. These mean the provider has gone through detailed outside assessments and incorporates top security standards.
- Seek out providers that publicly post their certifications or provide security documentation as part of the initial process. It's an indication that they're serious about compliance.
Data residency and sovereignty options
Some cloud WMS providers offer flexibility in terms of data storage locations so you can meet the requirements of data sovereignty regulations in countries like the EU, Canada or Australia.
Compliance used to keep companies from using cloud solutions — now it frequently motivates them to move to the cloud. Businesses can outsource regulation and security compliance to professional cloud providers, lightening their load while ensuring they remain on top of all the latest regulations.
It allows your logistics and operations teams to excel at making your warehouses top performers in the industry, while leaving them free from having to worry about catching up with new regulations or staying on top of cybersecurity.
Technical infrastructure requirements
Cloud WMS is highly attractive because it significantly simplifies the IT work needed to keep a warehouse up and running. Although you won’t need to maintain your own servers or hire an IT staff, there are some important foundational elements that are essential for the ongoing effectiveness of your Cloud WMS.
Here’s what’s typically needed:
1. Reliable internet connectivity
You must have reliable internet to ensure flawless operation of a Cloud WMS. Every aspect of warehouse management depends on consistent access to your system.
What you need:
- High-speed broadband or fiber connection.
- Experience continuity by running an alternative broadband connection as a backup.
- Wireless signals should reach all corners of the warehouse.
Almost any minute of downtime affects your operations, making availability and having backup solutions a priority.
2. Device and browser compatibility
These Cloud WMS solutions now operate primarily through web browsers or dedicated mobile applications, resulting in greater range and convenience for users.
Typical compatible devices:
- Desktop computers (Windows/macOS).
- Tablets and mobile phones (iOS/Android).
- Portable barcode scanners or tough handhelds (frequently running Android).
You should have no trouble using cloud-based WMS if your computers, tablets, smartphones and barcode scanners work with the latest internet browsers.
3. Integration readiness (APIs and data flow)
A WMS works closely with your ERP, TMS, eCommerce platforms, shipping tools and various other systems.
Cloud WMS integrations are usually simple set up with ready-made APIs, but you’ll want to check:
- Do your existing software systems allow for seamless connections?
- Will you be able to call on a technical expert for support should the need arise?
- Do you have reliable, standardized data from which to pull information?
Many vendors provide pre-configured integrations for a number of popular systems such as Shopify, NetSuite, SAP and Salesforce.
4. Data backup and disaster recovery
Being prepared is essential, even if your cloud WMS hosts your data securely.
Data protection and business continuity are integral components of many Cloud WMS systems by default.
- Daily or real-time data backups
- Geographically distributed data centers
- SLA-backed recovery timelines
Still, it’s worth asking vendors:
- How often is data saved?
- How long is data retained?
- How long will it take to get the system up and running again after a disaster?
It guarantees that you’ll be in the know ahead of time in case of any issues that threaten the continuity of your operations.
5. User access and security setup
Prior to activation, companies must define key access management rules.
- Allowing certain users to perform specific activities within the system.
- Authentication requires configuring password policies, switching on multi-factor authentication or setting up single sign-on capability.
- Only specific gadgets and networks are permitted for use.
- Ease-of-use already exists in Cloud WMS systems with admin panels; clear access policies help enforce security and ensure accountability from the start.
- The good news? Cloud WMS solutions are accessible to businesses of all sizes.
- Setting up the necessary infrastructure is simple — it only involves having a reliable internet connection, using newer computers and planning any required integrations.
- Conversely, it's easier to adopt a Cloud WMS than implementing a legacy system. Hosting, updates and security are handled by the provider, leaving your internal technology team with manageable workloads.
- Many companies prefer Cloud WMS as they grow because it's easy to use and flexible.
Challenges and considerations
Cloud WMS offers a host of advantages, though there are also important issues to keep in mind. These are the most frequent problems businesses run into, along with solutions or strategies to address them.
1. Data security and privacy
The concern:
There are concerns about managing confidential data remotely, particularly for customer, purchase or regulated goods data.
The solution:
- Partner with organizations that hold recognized security standards like ISO 27001 or SOC 2.
- Apply role-based access controls, encrypt data at rest and in transit and require additional security keys to log in.
- Know which country hosts your data and what company provides the data center.
2. Internet dependency
The concern:
Your warehouse management system requires a stable internet connection. If this link is lost, your WMS will also be unavailable.
The solution:
- Ensure your internet connections are redundant by using two providers or switching to 4G/5G when the wired network is down.
- Look for suppliers able to work without an internet connection on mobile devices.
- Collaborate with your IT experts on how best to manage any period of system disruption.
3. Vendor lock-in
The concern:
Changing providers after setup could become very complicated and costly.
The solution:
- Ask about data export and API access before signing
- Avoid working with companies that operate on closed or proprietary systems.
- Look for solutions that offer extensive and easy-to-use integration capabilities.
4. Limited customization
The concern:
Simplicity-focused cloud platforms may not adhere to diverse and specialized task requirements properly.
The solution:
- Focus on configurable platforms, not just customizable ones.
- Request walkthroughs of options similar to what you need.
- Ensure which features you can adjust to fit your specific needs.
5. Change management and training
The concern:
Sometimes, strong technology is still not enough for people to embrace it easily. Poor onboarding = poor results.
The solution:
- Choose a provider that has resources to show you how to use it and can help with any questions.
- Choose members within your organization to spearhead the implementation.
- Introduce the new tools to a single area or department at first.
The best cloud warehouse management system
Fynd WMS is arguably one of the best solutions for flexible and scalable warehouse management due to its cloud-native architecture customized to ease warehouse management for businesses across various industries. It is capable of evolving alongside the business and supports operational diversification.
Key features
- Customizable workflows – You can customize each workflow in your warehouse such as reviewing quality, stocking locations, picking from shelves and loading trucks, according to how your company operates.
- Universal scan & search - Review information about products, racks, bins or the entire warehouse instantly using barcode scanning.
- Mobile-first interface – These features are available on mobile devices ensuring no install is required.
- Real-time inventory visibility – Provides real-time updates of stock levels of multiple warehouses ensuring accurate recording.
- Integrated returns handling – Without any human input involved, cancellation and return processes have been made simple.
- Plug-and-play integrations – E-commerce applications, ERPs, as well as third-party applications are easily linked with the system.
Fynd WMS is designed to provide enterprise-grade functionality while avoiding the complexities associated with older systems.
Cloud WMS: real-world use cases from leading industries
Cloud WMS isn’t simply a passing fad; it’s successful in helping organizations tackle their warehouse management needs. A wide variety of businesses — such as retailers, manufacturers and third-party logistics companies — are leveraging cloud WMS to overcome various warehouse issues and boost their efficiency.
1. Retail & e-commerce
SharkNinja (USA)
SharkNinja was struggling with problems regarding inventory accuracy and fulfillment efficiency. They unlocked significant improvements with NetSuite’s Cloud WMS in place.
- NetSuite reports that companies using its WMS have seen up to 30% gains in fulfillment speed. While specific SharkNinja results are not publicly published, similar manufacturers report notable improvements.
- Customers were even more pleased as orders were shipped out quicker.
2. Third-Party logistics (3PL)
Ransa
Ransa has a network of 46 distribution centers and 171 warehouses spanning 7 nations as its core logistics business operations. Ransa successfully deployed Infor's cloud-based WMS on AWS as it navigated the COVID-19 challenges.
- Operational growth during challenging times
- Enhanced efficiency across multiple locations
3. Manufacturing
Huhtamaki (UK)
As a result of implementing SnapFulfil's cloud-based WMS, Huhtamaki achieved the following results at its Gosport location:
- ~30% increase in productivity
- Removing the need for a night shift resulted in a reduction of 20% in the number of staff required.
- Warehouse lateness and shortage issues were reduced by 10%.
- SnapFulfil reported that Huhtamaki achieved up to 98% warehouse space utilization with improved layout and slotting.
- According to SnapFulfil's case study, Huhtamaki reported a 99% reduction in stock losses after implementing their cloud WMS.
4. The future of cloud WMS
As supply chains change, Cloud WMS will become more important for maintaining flexibility, scalability and data-driven processes. Here’s what’s on the horizon:
- AI & Predictive Analytics: Uncovering hidden trends, making smarter route choices and sending inventory alerts ahead of time.
- IoT & Real Time Monitoring: Tracking of pallets, temperatures, and equipment with sensor supervision.
- Deeper Automation: Effortless automation integrations with robotics, drone systems, and automated picking.
- More Plug and Play Integrations: Faster ERP, CRM, and eCommerce platform cross-links which will minimize setup time.
The evolution of the industry goes beyond better storage solutions — it’s about transforming the warehouse into a sophisticated, tactical asset.
A Cloud WMS is more than an update; it requires a shift in approach. The cost savings, real-time monitoring, quick scaling and compliance ease make these benefits hard to overlook. Whether you are involved in retail, 3PL or manufacturing, a cloud solution allows you to stay flexible and competitive.
Frequently asked questions
Many industries depend on NetSuite, Oracle Cloud WMS and Fynd WMS as popular cloud-based systems.
Very. The flexibility of cloud WMS systems lets you handle growth by simply adding users, warehouses or new connections.
You can find standalone WMS, WMS with ERP integration, cloud-based WMS and Supply Chain Modules equipped with WMS.
Yes. There are many services that provide options and features suitable for SMBs as they grow.