Top 10 Benefits of a Warehouse Management System in 2025
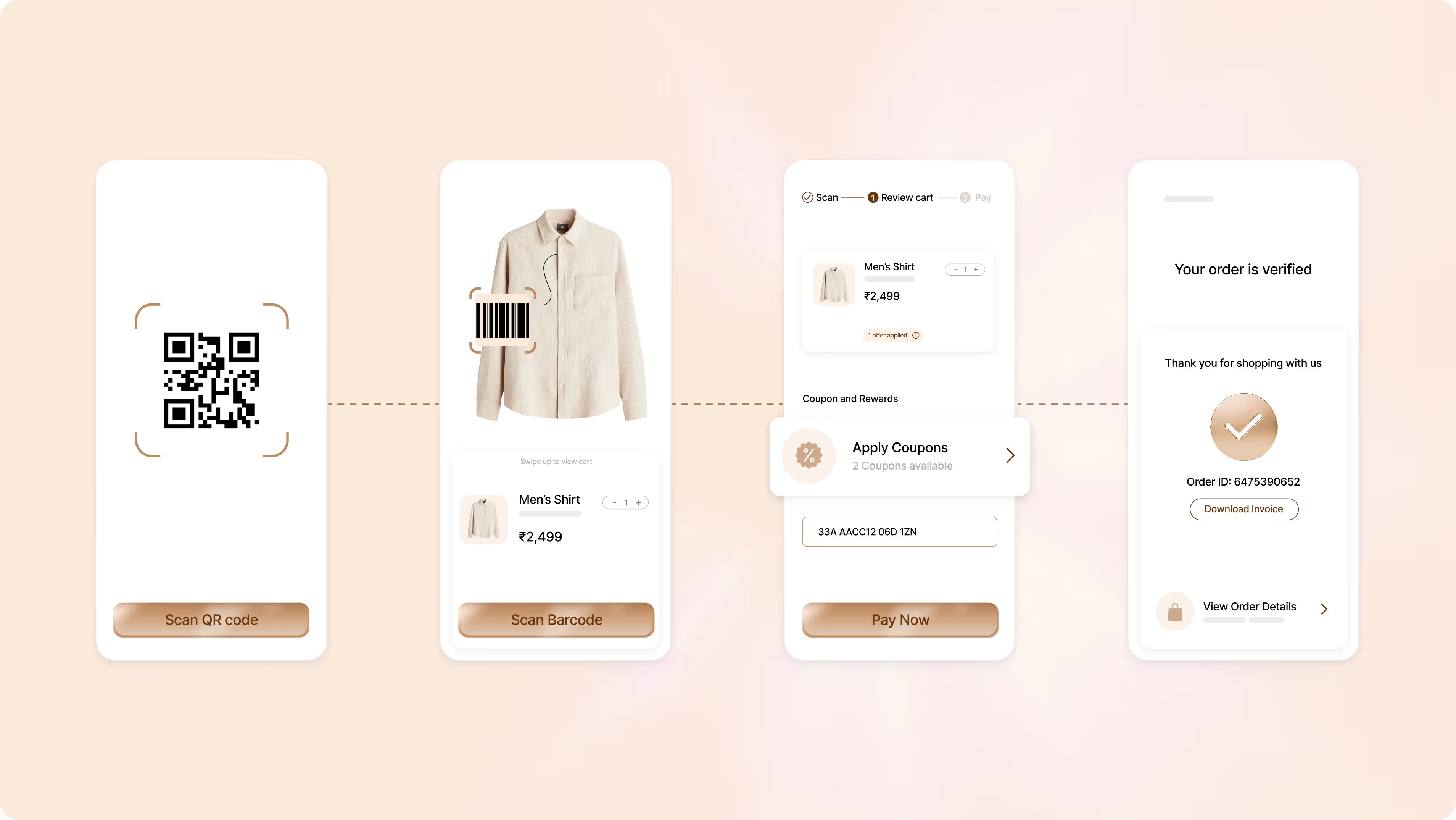
Warehouse Management Systems (WMS) are software solutions that streamline and optimize warehouse operations. A WMS ensures smoother workflows, higher accuracy, and cost efficiency, from inventory tracking to labor management. According to industry research, businesses using WMS solutions report up to a 30% reduction in inventory costs and a 25% improvement in order fulfillment accuracy. Core components of WMS include inventory management systems that track stock in real-time, picking and packing modules that minimize human errors, and analytics dashboards offering actionable insights.
Advanced systems also leverage RFID tracking, IoT devices, and automated guided vehicles (AGVs) to further enhance productivity. With a WMS, warehouses can avoid inefficiencies such as mismanaged inventory, high labor costs, and delayed shipments. A robust WMS addresses these issues by optimizing space utilization, reducing picking time by up to 40%, and automating workflows. These systems also integrate seamlessly with other supply chain tools like TMS and ERP, ensuring a connected, agile operation.
Before exploring the benefits of WMS, it’s crucial to understand what a WMS is and how it functions. For businesses seeking a reliable WMS solution, Fynd’s platform provides cutting-edge features that can transform warehouse operations, helping organizations achieve higher efficiency and profitability.
What is a Warehouse Management System?
A Warehouse Management System (WMS) is a software solution designed to manage and streamline warehouse operations efficiently. It helps businesses track inventory, organize storage, and manage tasks like picking, packing, and shipping goods. With real-time data and automation features, WMS ensures better accuracy and faster processes, reducing errors and costs.
Modern WMS platforms often integrate with other systems like ERP and TMS to create a seamless supply chain. By using tools such as barcode scanning, RFID, and analytics dashboards, businesses can improve productivity, optimize space, and enhance customer satisfaction. A WMS is essential for any organization looking to modernize and scale its warehouse operations effectively.
{{demo_wms="/styles/components"}}
Key Benefits of WMS
A Warehouse Management System (WMS) is a vital tool for modern businesses, designed to streamline warehouse operations and boost overall efficiency. It offers features such as real-time inventory tracking, space optimization, and task automation, reducing costs and enhancing accuracy. WMS systems are scalable, making them suitable for both small warehouses and global supply chains.
They deliver measurable improvements, including faster order fulfillment and better resource management, enabling businesses to meet customer demands effectively. Below, the benefits of WMS are explained in detail, showcasing how they address operational challenges and drive success for businesses of all sizes.
Benefit 1: Improved Inventory Accuracy
A Warehouse Management System enhances inventory accuracy by tracking stock levels in real time, offering precise data on every inventory movement. This reduces human errors and eliminates discrepancies, ensuring the right amount of stock is always available at the right time. By providing clear visibility, businesses can avoid costly issues like overstocking or running out of stock.
A WMS ensures streamlined operations, better inventory control, and fewer disruptions, directly contributing to improved customer satisfaction and operational efficiency across the supply chain.
- Tracks inventory in real time using barcodes, RFID, or scanners.
- Prevents errors in stock counts and inventory records.
- Ensures inventory is updated after every transaction automatically.
Benefit 2: Faster Order Fulfillment
WMS speeds up order processing by optimizing picking, packing, and shipping workflows. Using advanced algorithms, it suggests the most efficient routes and methods, reducing fulfillment times and improving overall accuracy.
This not only boosts operational efficiency but also enhances customer loyalty by ensuring that orders are processed faster and with fewer errors. The automation of these tasks leads to timely deliveries and improved service quality, fostering a better relationship between the company and its customers. Minimizing delays helps maintain a seamless flow and guarantees higher satisfaction for both businesses and their clients.
- Reduces picking time by using optimized routes and digital picking lists.
- Ensures accurate packing through automated verification systems.
- Speeds up shipping by integrating with carriers and using automated labeling.
Benefit 3: Optimized Warehouse Space
A WMS maximizes warehouse space by recommending efficient storage strategies tailored to each product's size, weight, and demand. Optimizing vertical and horizontal space usage reduces wasted space and improves product accessibility.
This leads to faster operations, as workers can quickly retrieve items from the most logical locations. Additionally, it results in cost savings for the business, reducing the need for excessive space while still increasing storage capacity.
- Suggests optimal slotting and bin locations for inventory.
- Reduces storage costs by optimizing vertical and floor space.
- Improves product accessibility, minimizing worker movement.
Benefit 4: Enhanced Operational Efficiency
WMS automates repetitive tasks, reducing manual labor and allowing employees to focus on higher-value tasks. By improving coordination across different warehouse departments, WMS eliminates delays and boosts productivity. It streamlines operations by offering seamless task assignments and helping businesses manage resources more effectively. This operational cohesion results in time and cost savings, making the entire warehouse more efficient.
- Automates tasks like scanning, labeling, and data entry.
- Ensures smooth coordination between different warehouse teams.
- Reduces operational delays caused by manual errors.
Benefit 5: Cost Reduction
Implementing a WMS can significantly reduce costs by improving inventory management, reducing labor expenses, and minimizing operational errors. Automation and optimized workflows lead to fewer resources needed for operations, making the entire warehouse process more cost-efficient. Businesses can also prevent excess inventory from tying up capital, further driving cost savings across the supply chain. The resulting efficiency helps offset initial system investment, improving long-term profitability.
- Cuts labor costs by automating repetitive tasks.
- Reduces waste and loss by ensuring accurate inventory management.
- Lowers shipping costs with streamlined order processing.
Benefit 6: Real-Time Reporting and Analytics
WMS provides businesses with comprehensive real-time reporting and analytics tools, allowing them to monitor key performance indicators (KPIs) and identify areas for improvement. This data-driven insight enables informed decision-making and promotes ongoing optimization. Real-time visibility into operations helps companies stay on top of performance metrics and ensures that adjustments can be made quickly to address inefficiencies or capitalize on opportunities.
- Tracks key metrics like inventory turnover and order accuracy.
- Provides insights into cost-saving opportunities.
- Enables quick adjustments through real-time data visibility.
Benefit 7: Increased Labor Productivity
WMS improves labor productivity by efficiently assigning tasks based on available workers and their skills. The system eliminates redundant tasks and helps manage workloads more evenly, reducing fatigue and optimizing performance. As a result, employees are more motivated, and warehouse operations experience a boost in productivity, which directly translates to faster order fulfillment and a more efficient warehouse environment.
- Assigns tasks based on availability and skill level.
- Reduces worker fatigue by eliminating redundant tasks.
- Tracks performance to identify and improve weak areas.
Benefit 8: Better Supply Chain Integration
A WMS integrates seamlessly with other systems like Enterprise Resource Planning (ERP) and Transportation Management Systems (TMS), creating a unified supply chain management solution. This integration ensures better coordination between suppliers, warehouses, and customers, enhancing data visibility across the supply chain. With accurate, real-time information, companies can optimize deliveries, reduce lead times, and provide better service to end customers.
- Synchronizes data across multiple systems for better visibility.
- Enhances communication between supply chain partners.
- Simplifies order tracking and inventory updates.
Benefit 9: Support for Scalability
As businesses grow, so do their warehouse operations. A WMS is designed to scale with these growing needs, supporting multi-warehouse operations and handling increased inventory volumes effectively. It ensures that, even during peak periods, operations remain smooth, allowing businesses to maintain their efficiency without the need for significant manual intervention or additional resources.
- Handles increasing inventory volumes with scalable features.
- Supports operations across multiple warehouse locations.
- Ensures seamless operations even during peak demand.
Benefit 10: Improved Customer Satisfaction
WMS ensures faster and more accurate order fulfillment, leading to higher customer satisfaction. By reducing errors and ensuring on-time deliveries, businesses can meet customer expectations consistently. This reliability improves customer retention, enhances brand reputation, and increases repeat business. As a result, a WMS directly contributes to a stronger customer base and long-term business success.
- Ensures on-time deliveries with precise order tracking.
- Reduces customer complaints by eliminating order errors.
- Enhances customer experience through efficient service.
Why is WMS Important for Your Business
A Warehouse Management System (WMS) is crucial for businesses aiming to optimize warehouse operations, improve efficiency, and streamline supply chain management. By automating critical processes like inventory tracking, order fulfillment, and space management, WMS helps businesses meet customer demands more effectively while minimizing operational costs.
Whether you're a small business or part of a larger organization, implementing WMS technology can significantly boost productivity, reduce errors, and ensure the smooth flow of goods, resulting in faster order processing and improved customer satisfaction across the board.
1. Improved Inventory Accuracy
A WMS enhances inventory accuracy by tracking stock levels in real time and providing detailed records of all inventory movements. This minimizes human errors, eliminates discrepancies, and prevents issues such as overstocking or stockouts. With precise and updated inventory data, businesses can make better decisions, streamline operations, and avoid costly mistakes. Accurate inventory ensures the right products are available when needed, improving order fulfillment and customer satisfaction.
2. Faster Order Fulfillment
A WMS optimizes key warehouse functions such as picking, packing, and shipping by automating these processes. This significantly reduces order fulfillment times, allowing businesses to deliver orders faster and more accurately. The system’s use of advanced algorithms helps streamline workflows, ensuring that items are picked in the most efficient order and shipped quickly. As a result, businesses can offer improved customer service and foster customer loyalty through faster delivery times.
3. Cost Reduction
WMS systems drive cost reductions by improving inventory management, space utilization, and labor efficiency. By automating routine tasks and optimizing warehouse processes, businesses can reduce labor costs. Accurate inventory management ensures that businesses avoid costly stockouts and overstocking, while optimized space utilization cuts storage costs. The system also reduces waste by providing clear visibility into inventory levels, helping to prevent overproduction and ensuring a leaner, more cost-effective operation.
4. Enhanced Operational Efficiency
With a WMS, businesses can streamline their operations by automating routine tasks and improving communication across teams. This leads to fewer errors, minimized delays, and increased productivity. WMS helps coordinate activities such as order picking, stock replenishment, and inventory tracking, reducing the need for manual intervention. By improving the flow of goods and information, a WMS enhances overall operational efficiency, allowing businesses to scale their operations without sacrificing performance.
5. Better Space Utilization
WMS optimizes warehouse space by recommending the best storage solutions based on product characteristics such as size, weight, and demand. The system helps businesses make the most efficient use of both vertical and horizontal space, allowing for higher storage density. This optimization not only cuts storage costs but also makes it easier for workers to access products, enhancing workflow efficiency and minimizing time spent searching for items.
6. Real-Time Data and Reporting
A key benefit of WMS is its ability to provide real-time data and comprehensive reporting on key warehouse metrics like inventory turnover, order accuracy, and supply chain performance. These insights allow businesses to make informed decisions, spot inefficiencies, and quickly adjust processes to improve operations. Real-time reporting enables businesses to be more responsive to market demands and customer needs, helping them stay competitive and continually improve their performance.
7. Improved Customer Satisfaction
WMS contributes to improved customer satisfaction by ensuring orders are processed quickly and accurately. The system’s ability to automate order picking and packing reduces errors and shipping delays. As a result, customers receive their orders on time and in good condition. This reliability builds customer trust and loyalty, leading to increased satisfaction and repeat business. Ultimately, faster fulfillment and fewer mistakes contribute to a positive customer experience.
8. Scalability
A WMS is designed to grow your business, making it an ideal solution for companies with plans to scale. Whether your business is expanding inventory, adding new warehouses, or handling seasonal fluctuations, a WMS can manage increased complexity without losing control over warehouse operations. Its scalability ensures that businesses can keep operations running smoothly and efficiently even as demands increase, ensuring a flexible solution that adapts to business growth.
9. Better Supply Chain Integration
WMS’s integrate seamlessly with other business systems such as Enterprise Resource Planning (ERP) and Transportation Management Systems (TMS). This integration allows for a unified view of the entire supply chain, improving coordination between suppliers, warehouses, and customers. With synchronized data across systems, businesses can track orders, shipments, and inventory in real time, reducing errors and improving overall supply chain efficiency. Better integration leads to smoother workflows and more reliable service.
10. Increased Labor Productivity
WMS increases labor productivity by automating routine tasks and optimizing workflows within the warehouse. Workers are assigned tasks based on priority and available resources, enabling them to complete orders more quickly. The automation of data entry, scanning, and labeling eliminates the need for manual interventions, allowing staff to focus on more value-added activities. By improving task efficiency and reducing worker fatigue, businesses can increase productivity and ensure faster order processing.
Key Features of WMS
A Warehouse Management System (WMS) is an essential tool for businesses that need to manage warehouse operations efficiently. It helps automate processes, improve inventory accuracy, and optimize warehouse space. With features that enable real-time tracking, streamlined order fulfillment, and labor management, a WMS allows businesses to operate at maximum efficiency.
Whether you're a small business or a large enterprise, understanding the key features of a WMS is crucial for selecting the right solution to enhance your operations, reduce costs, and improve customer satisfaction.
1. Real-Time Inventory Tracking
WMS provides real-time visibility into inventory levels, allowing businesses to track stock movements instantly. This reduces the chances of discrepancies, overstocking, or stockouts by keeping accurate data on product quantities. Real-time updates also enable businesses to quickly adjust to changes in demand and make informed decisions, improving overall inventory management and speeding up order fulfillment, which ultimately leads to better customer service and operational efficiency.
2. Order Management and Fulfillment
A WMS streamlines the order fulfillment process by automating tasks such as picking, packing, and shipping. The system uses optimized workflows to ensure that the right products are selected and packed according to customer specifications. This leads to improved accuracy, reduced errors, and faster delivery times. By eliminating manual processes and human error, WMS makes order fulfillment more efficient and helps maintain a high level of customer satisfaction.
3. Space Optimization
WMS helps businesses maximize the use of warehouse space by recommending optimal storage locations based on various factors such as product size, demand, and weight. By efficiently organizing products, businesses can reduce unnecessary storage costs while improving warehouse workflow. This enables quicker product retrieval and better inventory management, leading to a more organized warehouse environment and better space utilization, which can enhance overall operational efficiency.
4. Barcode Scanning and RFID Integration
Using barcode scanning and RFID technology, WMS facilitates accurate, real-time inventory tracking. Barcodes and RFID tags make it easy to identify and locate products in the warehouse quickly, reducing the risk of human error and keeping inventory data up-to-date. These technologies also speed up the process of stocktaking and order picking, ensuring that products are accurately tracked from arrival to shipment, thus improving operational efficiency and accuracy.
5. Automation of Repetitive Tasks
WMS automates repetitive tasks such as data entry, labeling, stock replenishment, and order picking. By automating these tasks, businesses can reduce the need for manual labor and increase productivity. This also minimizes human error and allows employees to focus on more complex tasks, improving overall warehouse operations. The automation of these tasks leads to faster processes, less downtime, and a more efficient and streamlined warehouse environment.
6. Reporting and Analytics
WMS provides robust reporting and analytics tools that track critical metrics such as order accuracy, stock levels, and worker productivity. These insights help businesses identify bottlenecks and inefficiencies in warehouse operations. By offering detailed, real-time data, WMS enables businesses to make informed decisions that improve operational efficiency. Regularly reviewing these analytics also allows businesses to continuously refine their processes, leading to improved performance and reduced operational costs.
7. Labor Management
A WMS optimizes labor allocation by assigning tasks based on worker availability, skill levels, and workload. This system ensures that tasks are completed efficiently by the right person at the right time, reducing downtime and improving overall warehouse productivity. Automating labor management boosts employee satisfaction by reducing the likelihood of overburdening workers while also ensuring that workers are more focused and productive, leading to smoother operations.
8. Scalability and Flexibility
WMS systems are designed to scale with your business. Whether you're increasing your inventory, expanding to new warehouse locations, or dealing with seasonal fluctuations in demand, a WMS can easily adapt to meet your needs. This scalability ensures that businesses can grow without worrying about losing control over warehouse operations. A flexible WMS is an ideal solution for businesses of any size, providing continuous support as your operations expand.
9. Integration with Other Systems
A WMS can integrate with other enterprise systems, such as Enterprise Resource Planning (ERP) and Transportation Management Systems (TMS). This integration provides businesses with a unified view of their entire supply chain, improving data visibility and coordination. By synchronizing inventory, orders, and shipments, businesses can streamline operations across departments, reducing delays and improving decision-making. This holistic approach results in more efficient processes and better overall performance.
10. Enhanced Customer Satisfaction
With WMS ensuring accurate order fulfillment and on-time deliveries, businesses can significantly improve customer satisfaction. By reducing errors and processing orders more quickly, businesses can meet customer expectations and build stronger relationships. Faster shipping, accurate order tracking, and reliable delivery help businesses foster customer loyalty, increase retention rates, and enhance their reputation in a competitive market, ultimately driving long-term growth.
Challenges to Consider before Implementing WMS
Implementing a Warehouse Management System (WMS) can greatly enhance operational efficiency, reduce errors, and streamline supply chain processes. However, before committing to this solution, businesses must carefully evaluate several challenges.
These include the upfront financial investment, the potential complexity of integrating the WMS with existing systems, and the disruption it may cause to day-to-day operations. Addressing these challenges early on will ensure a smoother implementation process and allow businesses to maximize the long-term benefits of the WMS, ultimately improving their warehouse and inventory management practices.
- Initial Costs: WMS implementation involves significant costs for software, hardware, and training. Budgeting for both initial and ongoing expenses is essential for a positive ROI.
- Integration with Existing Systems: Integrating WMS with ERP, TMS, and other systems can be complex and time-consuming, requiring expert resources.
- Employee Training: Proper training is essential for effective WMS use, requiring time and resources to ensure employees are proficient with the system.
- Disruption of Operations: WMS implementation can temporarily disrupt warehouse operations, potentially slowing productivity during the transition period.
- Customization Needs: Customizing WMS to meet specific business needs can increase both costs and the time required for full implementation.
- Resistance to Change: Employees may resist new technology, especially when moving away from manual processes. Managing this resistance is key to a smooth transition.
- Data Migration: Migrating existing data into a new WMS can be challenging, and errors during this process can lead to operational inefficiencies.
- Ongoing Maintenance and Support: Continuous maintenance, updates, and troubleshooting are required, with businesses needing to plan for long-term support.
Conclusion
Implementing a Warehouse Management System (WMS) can greatly enhance operational efficiency, reduce costs, and improve customer satisfaction. However, businesses must consider challenges like initial costs, system integration complexities, employee training, and potential disruptions during implementation.
By addressing these challenges early on, companies can maximize the benefits of a WMS, ensuring smoother operations, more accurate inventory management, and the ability to scale efficiently. With proper planning, ongoing support, and the right solution like Fynd WMS, businesses can achieve long-term success and enhanced warehouse performance.
Frequently asked questions
A Warehouse Management System (WMS) is software that helps manage and control warehouse operations, including inventory tracking, order fulfillment, and space optimization.
WMS improves accuracy, speeds up order fulfillment, and optimizes inventory management. It helps reduce errors, lower operational costs, and boost customer satisfaction.
Key features include real-time inventory tracking, order management, space optimization, barcode scanning, automation of tasks, and comprehensive reporting tools.
The cost of implementing a WMS depends on factors like software, hardware, integration, and training. Businesses should budget for both upfront and ongoing expenses.
WMS can be integrated with ERP, TMS, and other systems, allowing seamless data flow and improving coordination across the supply chain.
Challenges include high initial costs, system integration complexity, employee training needs, temporary disruptions in operations, and data migration issues.